Grinder Speed For Sharpening Lathe Tools Gmbh,Match Plane Hand Tool,Rockler Router Plate Instructions Inc,Jet Lathe 1221vs Stand 4g - Step 1

I've only seen it described in a few machining texts, and the description was usually incomprehensible. I never understood the tool until it was properly described in an on-line forum.
It has but a single specialized purpose, that of finishing materials that tend to tear. If you can't get a good finish on some difficult grade of steel, this is the tool to try. Be aware that it has many limitations. As shown, it will only cut from right to left, and the depth of cut is rarely more than 0. It's hard to get close to a shoulder without careful grinding and a low contact point. Both the spindle speed and feed rate are generally kept quite slow.
Slow power feed is thus preferred, especially if the part is long. Use oil. The tool nose is ground at a slight angle to provide clearance, just a few degrees.
The cutting edge is usually degrees off vertical. Stone until smooth and sharp. As you can see below, the vertical position of the tool is not critical, in fact when one spot becomes dull, just raise or lower the tool a bit. Operating correctly, this tool will produce a chip that looks almost exactly like steel wool. Under the right conditions the shear tool can give a finish so smooth it could be mistaken for ground. The factory supplied rests on most grinders are nearly useless.
With a bit of searching on the net, you can find plans for much improved rests and tool holders. I also recommend buying a copy of Tool and Cutter Sharpening by Harold Hall, Workshop Practice Series 38, which includes much sound advice, along with plans for many easy to build grinding fixtures. Still, most of what's available only addresses the grinding part of the process and my focus is on getting a better edge than grinding alone is likely to give.
I mentioned pocket knives earlier and nothing puts a better edge on a knife blade than the original Lansky Sharpening System. They use a guide, clamped to the blade, that prevents accidently stoning the edge, even briefly, at the wrong angle. Each stone has a long rod extending from the back that rides in the guide. The same principle can be applied to almost any edge you want to touch up, including end mills and dovetail cutters.
You can make up your own stones by glueing them to a bar, or using lapping film this is where the PSA is useful , but I just use the Lansky stones right from the standard set. Here's the basic idea for touching up an end mill, though one would want things tied down a bit better than sitting on the studio seamless. Yes, I know this is about lathe tools; use some imagination and apply the technique to whatever edge you need to deal with. The methods above will suffice for almost all typical turning needs using HSS and cast alloy tool blanks.
The angles can be held to sufficient accuracy by eye and experience. This is not the case for threading. As a bare minimum you should use a "fishtail" gage to check the included angle and squareness of the tool, but that still leaves you a long ways from what can be achieved with very little additional effort.
Once you've roughed out the tool on the grinder, you need a fixture to perfect the angles. I made the fixture shown here from a scrap cutoff of Delrin. I had made a rectangular one some time back but it grew legs, so they must be desirable. The exact shape and dimensions aren't important, though you should try to keep the two feet and the tool tip near the points of an equalateral triangle.
The fixture is a kinematic design; it has three contact points making it completely stable in use. The angles can be changed slightly, but you'd need a different fixture for Acme or other threads with significantly different angles.
You can make a nice angle template out of aluminum roofing flashing. Just scribe it and cut it on a paper cutter not a rotary cutter. If you want to work from a different side of the tool, or the fixture itself, the template can certainly be Grinder Speed For Sharpening Lathe Tools Code cut to reflect that preference.
Next we go to the back of the tool to set the relief angle. It will be necessary to go back and forth a couple times because the adjustments interact. If you look closely you can see the perfect facet at the tip created by the ultra-fine black Arkansas stone. The nearby edge of the tool catches the light, but it's still rough ground and didn't hit the stone.
You can also use the fixture on glass or a surface plate with lapping film. This is pressure sensitive aluminum oxide film, and the adhesive backing rounds the facet slightly, resulting in a slightly less sharp and less free cutting tip. Try to get plain lapping film. Now, flip the tool over in the fixture, readjust, and tune up the other side. You may want to remove excess material that doesn't need to be lapped as described shortly, so the lapping operation goes swiftly.
With a properly ground tool, lapping shouldn't be any more than a ten minute job. OK, tell me again why we need this level of control over the edges? For a thread to function properly, the flanks of the screw need to contact the flanks of the nut. If the angles are off, the contact area will be a narrow high pressure line near the ID or OD of the thread. The lubricant won't be able to support the pressure and you'll get metal to metal contact, possibly galling and certainly higher friction than would otherwise be the case.
If you're making an adjustment screw for a laser mirror mount, it certainly does matter. For conventional HSS lathe tools the hollow grinding technique described above works well. For threading tools that get lapped using a fixture you can save a huge amount of work by removing unnecessary material at the grinding wheel. I currently have the slow speed grinder and wolverine. Not perfect for grinding while sitting -- Have been looking at Tormek as being a better choice for turning to the side and having less obstructions.
I have moving to have all my tools with interchangeable handles. Taking the handles off makes sharpening much much easier. Key jigs are for spindle and bowl gouges. The other need is for platform for grinding. On the wolverine base I am using a RoboRest platform. Much easier to adjust and consistent for skews, spindle roughing gouge and the like.
Mack C. Click to expand I've got the wolverine and use it exclusively with my woodcraft slow speed grinder. I recently upgraded to a CBN wheel and I love it! Duplicate post. Fay Prozora Member.
I have a Powertec slow speed grinder and my Wolverine came yesterday. I love my grinder but I will set the wolverine when I get back to my shop in a week or so. It'll be very interesting to use this tool instead of the wooden one I built. Good luck with what ever you get. Oh my grinder is an 8" Works better than Uncle Dick's old grinder that has skinny wheels and it small.. It is a one speed and I did not like his You must log in or register to reply here.
Previous Next. Similar threads L. Replies 5 Views Dec 27, bmachin. Sharpening system recommendations for a newbie. Replies 27 Views 3K. Log in Register. What's new. New posts. What's new New media New media comments New downloads Latest activity.
Log in. Install the app. JavaScript is disabled. For a better experience, please enable JavaScript in your browser before proceeding. You are using an out of date browser. It may not display this or other websites correctly. You should upgrade or use an alternative browser. Thread starter Nogoingback Start date Mar 29, Joined Oct 18, Messages 2, I'm thinking about learning to grind my own lathe tools and need a bench grinder to do it with. Up to this point I've been using HSS insert type tooling.
Baldor's are probably out of my budget, but a decent older USA made machine is what I have in mind. Or are they all the same? What grinding wheel diameter would be best in terms of performance, availability and cost? Any particular brands or models?
Any other considerations? Joined Aug 29, Messages 1, Virtually any bench grinder should be able to grind HSS bits.
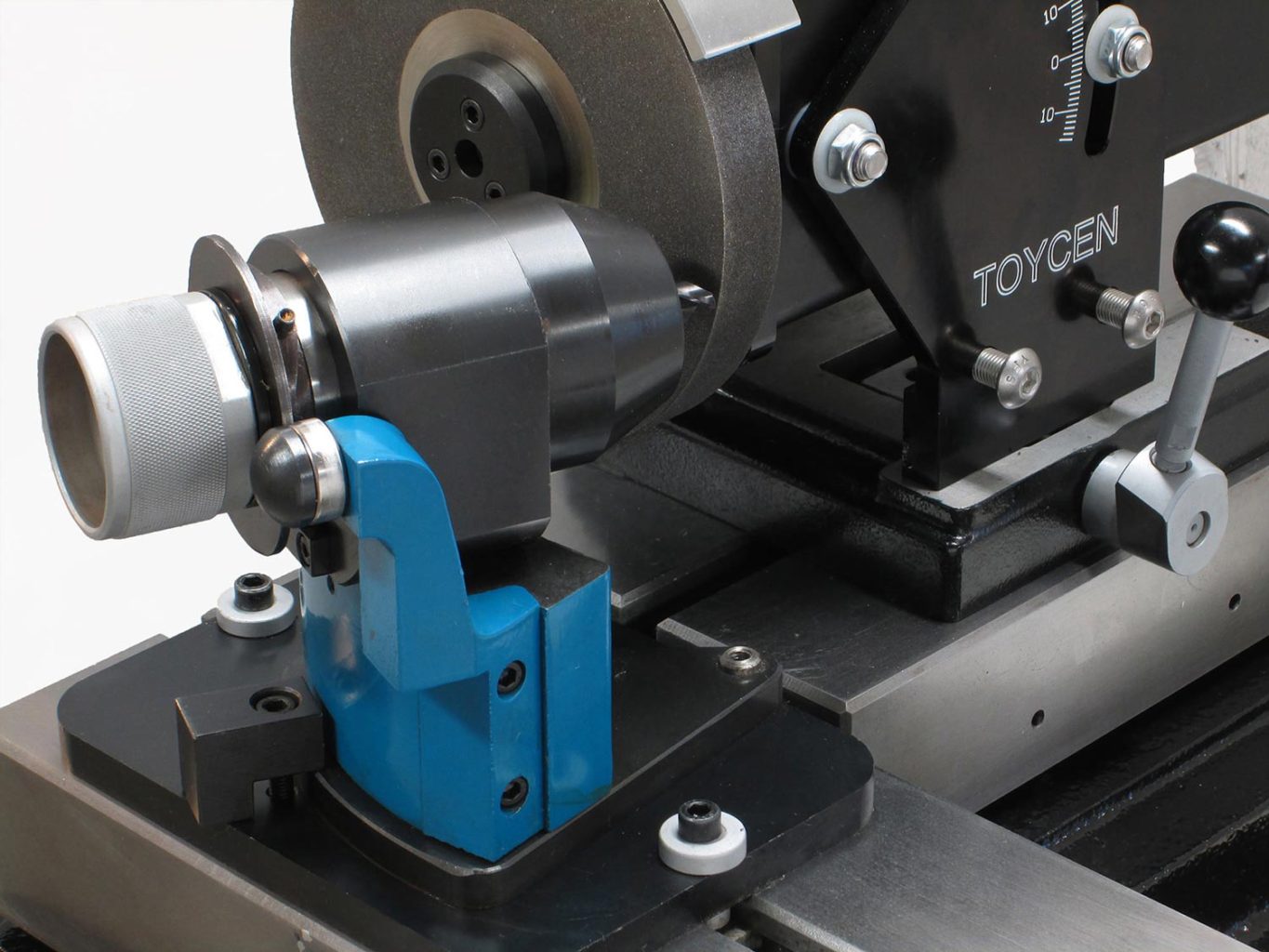


Cabinets To Go Knobs And Pulls On Drawer Pull Out Hardware On Mac |
BAKULOVE
07.11.2020 at 20:44:49
ARMAGEDON
07.11.2020 at 23:15:54
Anastasia
07.11.2020 at 14:28:26
T_O_T_U_S_H
07.11.2020 at 22:18:33