Lathe Tools Wangara Online,Do It Yourself Rock Garden 2020,Hinges Kitchen Cabinets 32,Bessey Parallel Clamps Home Depot Edition - How to DIY
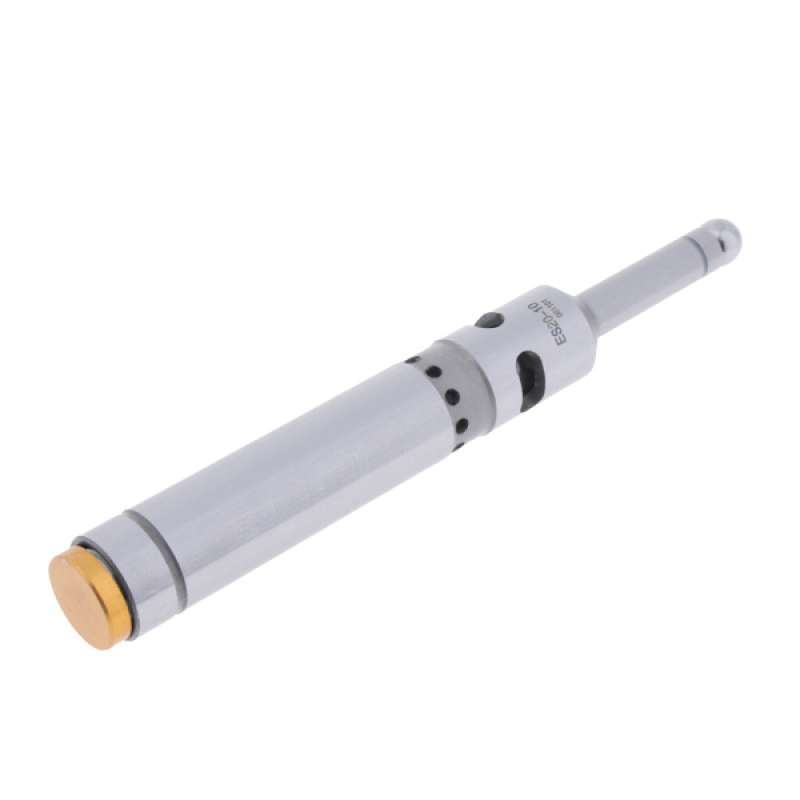
Work this way from both sides of the cove toward its center. As the gouge is manipulated, the action changes from shearing to scraping Figure , which occurs at the full depth-of-cut point only. Using the Skew Chisel. Typical applications of the skew chisel are shown in Figure While professionals use the skew mostly in a shearing action, it can function efficiently while cutting or scraping.
A common scraping action is shown in Figure E with the chisel held to square off the end of a cylinder. When held this way, the chisel's sharp point removes material quickly and leaves a reasonably smooth surface. The same result is obtained by using the point of the skew in a cutting action Figure B.
When used this way, the skew works like a knife, severing wood fibers and leaving a surface that requires little sanding. Tapers are formed by starting the cut with the heel of the blade and raising the handle as you slide the chisel along the tool rest.
To smooth a taper that was formed with another tool, use the skew as shown in Figure A or F. This can be a scraping or a shearing action. If you move the skew so only its heel contacts the work-piece, it will shear.
If you position the skew so its edge is parallel to the workpiece and then advance it while maintaining tool-to-work-piece contact, the action will be scraping. Probably the smoothest surfacing cut of all is shown in Figure H where a shearing cut is being used to smooth a cylinder.
The cutting edge of the skew is held at an angle to the longitudinal axis of the workpiece. When done correctly, the surface of the work-piece is smooth with a finish that looks burnished. It will take practice. The skew is used to form beads. Like a cove, the bead requires three marked or imagined dimension lines: one to indicate the bead's center and one on each side of the center to indicate total bead width. Start by placing the heel of the skew lightly on the bead's center-line so its edge is tangent to the curve you want to form.
Move the skew into the workpiece. At the same time, rotate and lift the handle to follow the curve of the bead. It will take several passes to form one-half of the bead Figure Follow the same procedure, but work in the opposite direction, to form the other half of the bead Figure Using the Roundnose Chisel The roundnose chisel is always used in a scraping action Figure and is the only tool to use for hollowing.
In the latter application, the tool rest must be positioned to provide maximum support for the chisel even if it has to be placed inside the hollow that is being formed. Using the Parting Tool The parting tool is most often used in a scraping action with the edge of the blade resting on the edge of the tool rest and with blade feed directly forward, whether the cut is square or at an angle to the work-piece Figure The parting tool is often used to determine the depth of cut or the diameter of the final shape.
To speed up the procedure when making preliminary sizing cuts, handle the tool as shown in Figure Start with the tool horizontal, then slowly raise and lower its cutting edge as the cut deepens. Planning the Design. Before you attempt to form a turn-ing, you must first plan the design. Otherwise you may end up with an unattractive project.
The best way to plan the design is to draw a full-size plan with the shapes and dimensions marked, so that before you start you will know exactly what shapes you are going to cut and where. Here's an example of how to plan the design for a spindle turning 12" long and 3" in diameter: Draw a rectangle 12" by 3" on a piece of paper.
Draw a centerline down its length. Break up the length into design areas by draw-ing horizontal lines that are proportional and pleasing. Let the base design occupy the bottom 3"; use 7" for the transition from base to top and leave the remaining 2" for the top.
Lathe Safety. Warning: Before using the lathe, read and understand these important safety instructions:. Danger Zone --The danger zone on the Mark V in the lathe mode changes as the turning progresses. Before the stock has been rounded, the danger zone extends 3" out from the stock in all directions. After the stock is rounded and while it's being shaped, the danger zone extends 1" out.
After the stock is completely shaped and the tool rest has been removed, you can safely put your hands near enough to the workpiece to sand it on the lathe. Always keep your fingers Lathe Tools Online Shopping Review and hands out of the danger zone. When you work at the lathe, be careful not to touch the stock as it turns, until you have finished shaping it. In particular, be careful not to let your fingers or hands slip between the workpiece and the tool rest. Keep both hands on the tool you're using and in front of the tool rest.
Before sanding your workpiece on the lathe, turn off the machine, let it come to a complete stop, and remove the tool rest. Balance --This is extremely important when turning glued-up stock, long stock and stock more than 3" in diameter.
Check the balance of your spindle and face plate stock after you've marked the centers. To do this, drive a standard 8 penny nail straight into each center.
Use suitable string to hang the stock in a level position from the front bench tube of the Mark V or a saw horse. The ends of the string should be looped around the nails Figure Gravity will pull the heavy side down. Lathe Speeds. The operating speeds for lathe turning are determined by the size of the stock you're turning and the operation you're performing-whether you're rounding the stock, shaping it, or finish sanding.
Generally, you can use slightly faster speeds as you progress from rounding to shaping to sanding. You can also use slightly faster speeds with smaller stock. The larger the workpiece, the slower the speed should be for each operation. To help determine the right speed for the job, use Table Spindle Turning.
All spindle turning projects involve these six basic steps:. Mounting the stock on the lathe is an extremely important operation. Warning: Improperly mounted stock is dangerous and difficult to turn. The first step is to turn the stock down to a rough cylinder.
Once the stock has been rounded, mark the positions of the shapes you want to make and turn them down to their approximate diameters. Turn the beads convex curves and coves concave curves in your design. After the stock is shaped, remove the tool rest and sand the workpiece smooth. After the final sanding, reinstall the tool rest and remove the waste stock if any from the turning. To mount stock between the lathe centers, you must first find the center of the stock.
To find the center of a square workpiece, use a straightedge and draw two diagonal lines on each end of the workpiece, from corner to corner Figure Where these two lines intersect marks the center of the stock.
To find the center of a round workpiece, use a center finder. With a plastic or rawhide mallet, seat the drive center in one end of the workpiece and the cup center in the other. Caution: Do not hit the centers with a metal hammer-you will ruin them.
Position the center point at the center mark; then hit the center sharply Figure When properly seated, the drive center will leave four slots where the spurs bit into the wood. The cup center will leave a small circle Figure This will help seat the drive center.
If the workpiece you're turning is more than 3" square, cut off the square corners to form an octagon. This will make the workpiece safer and easier to turn. Use a bandsaw or table saw to cut off the corners. Mount the drive center on the main spindle and the cup center in the tailstock. Position the power plant so that the centers are about 1" farther apart than the length of the workpiece, and lock the power plant in position.
Wax or soap the end of the stock that mounts to the cup center to help it turn smoothly. Hold the stock against the cup center; then extend the quill and mount the other end on the drive center. Press against the quill feed lever to be sure both the spurs and the cup are engaged.
Do not release the tension. Then lock the quill in place Figure Adjust the height of the tool rest for scraping or shearing, whichever you prefer. Be sure the setscrews in the tool rest assembly are secured.
Turn the stock by hand to be sure it clears the tool rest. Make a five-point check. All five locks--power plant, carriage, tool rest height, quill and tailstock--should be secure. The speed should be set at "Slow. The stock should rotate smoothly, without excessive vibration. Rounding Select a gouge and lay it across the left end of the tool rest.
The cup should face up and slightly toward the right end of the tool rest. The shank and handle should be pointing down and angled slightly toward the left end of the tool rest. Gently feed the cutting edge toward the stock until the tip just touches the stock. Then draw it slowly and steadily along the tool rest to the right, removing a little bit of the stock Figure To reverse the cutting action, turn the gouge so the cup still faces up but slightly toward the left end of the tool rest.
Feed the gouge into the stock and draw it back along the tool rest to the right. Repeat this procedure until the stock is completely round, without any flat spots. To tell if there are any flat spots without turning off the machine, carefully let the shank of the qouge rest on the revolving stock Figure If the gouge vibrates or jumps up and down, the stock is not quite round.
Use a pencil and a parting tool for this operation. With the pencil, scribe lines on the revolving stock to indicate where you want the beads, coves, and other parts of your spindle design to begin and end Figure With a parting tool, cut grooves in the workpiece to indicate the position and diameter of the different shapes in your design Figure To gauge when you've reached the proper diame-ter, set a pair of "outside" calipers at the desired measurement and test the diameter where you're cutting from time to time.
When the calipers just slip over the stock at the bottom of the groove, you've arrived at the desired diameter Figure Shaping When you've marked the positions and diameters of the various parts of your design, begin to cut the shapes.
Usually, it's easiest to start with the convex curves or beads. Select a skew chisel to round the sides of the beads. Feed the edge of the chisel slowly into the stock; then move the handle of the skew from side to side as needed to shape the bead Figure After you've made the beads, begin to cut the coves, the concave curves in your design.
Select a gouge and slowly feed it into the workpiece, gradually removing stock. As you did when you were shaping the beads, move the handle of the tool from side to side to shape the cove the way you want it Figure When forming duplicate pieces, for example, chair or table legs, it's better to work with a hardboard template Figure The template is a full-scale, half-profile of the part and can be used to check the turning as you go, as well as for marking initial dimension points.
Although woodworkers usually rely on skew chisels to cut beads and gouges to cut coves, you can use other tools if you wish. Select whatever seems best for you. Sanding It's much easier to sand a turning on the lathe than it is to remove it and hand sand it. However, since you have to get your fingers right next to the spinning stock, you must be extremely careful. When the turning has been completely shaped, turn off the machine and let it come to a complete stop.
Warning: Remove the tool rest before sanding a turning on the lathe. Turn on the machine and slightly increase the speed of rotation. Starting with medium 80 sandpaper, begin to sand the spindle by holding the sandpaper lightly against it Figure Double the sandpaper over several times for two reasons: The paper heats up quickly and extra layers of paper protect you from being burned.
Also, the extra layers of paper keep your hands from contacting the rotating spindle. Work your way through progressively finer grits of sandpaper until you get the spindle as smooth as you want it. Warning: Never wrap the sandpaper entirely around the spindle or allow strands to wrap around the spindle.
The spindle will grab the sandpaper or strand and draw your fingers into the rotating spindle. There are two ways to remove these. The easiest is to wet the spindle with a damp rag, wait a few minutes for the water to dry and raise the wood grain, then give the spindle a final sanding with a very fine grit sandpaper. If you don't want to wet the wood, turn the Mark V off and dismount the spindle.
Remove the centers and seat them in opposite ends of the spindle. Remount the spindle, putting enough pressure on the quill to engage both the drive center and the cup center.
This reverses the rotation of the spindle so that you can remove any microscopic feathers with a light sanding. Here are several other lathe sanding tips: The Mark V sanding disc is a super tool to use when smoothing uniform cylinders or tapers Figure Another trick used by professionals is shown in Figure After the workpiece has been smoothed by sanding, hold a strip of wood against the workpiece as it is turning.
The result will be a hard, burnished surface that is fine for a natural finish but will not take a stain. Parting After the spindle is sanded, part the spindle from the waste stock. Using the parting tool turned on its edge, scrape away stock from either end of the spindle until the diameter is as small as it can safely go and still not break Figure Warning: Never part the stock completely or turn the spindle down to such a small diameter that it snaps on the lathe.
Always remove the spindle from the lathe and finish cutting off the waste stock with a saw Figure Faceplate Turning. Faceplate turning is similar to spindle turning in some respects, but very different in others. We'll point out those differences as we go through this basic procedure. As with spindle turning, faceplate turning also involves six basic steps: Mounting, rounding, sizing, shaping, sanding and parting.
Mounting To mount stock on a faceplate, first find the center of the stock by drawing diagonal lines from corner to corner. Then scribe the outside diameter of your project the diameter desired after rounding on the stock. Also, scribe a circle slightly larger than the diameter of the faceplate in the center of the circle you've already marked Figure Then cut the stock round using a bandsaw or scroll saw Figure This removes excess stock which makes turning safer and easier.
If you don't want screw holes in the bottom of your finished project, you can mount the turning stock to another block of wood; then mount this block to the faceplate. Select a scrap block at least 1" thick and about the same diameter as the faceplate you'll be using. Find the center of this scrap block; then glue the block to the turning stock, center-to-center. Put a piece of paper brown craft paper or grocery sack in between the block and the turning stock Figure Warning: Leave the pieces clamped for at least 24 hours prior to turning.
Later on, this paper will make it easier for you to part the scrap block from the turning. For large, bulky faceplate turnings use longer screws and a thicker scrap block. Position the tool rest to turn the outside of the workpiece first. When the tool rest is properly positioned and the set-screws secured, turn the work-piece by hand to make sure it doesn't scrape against the tool rest.
Make a four-point check. All four locks -power plant, carriage, tool rest height, quill-should be secure. Rounding Round the outside diameter first. Use a gouge, just as you would for spindle turning, with this one exception: If the wood grains are perpendicular to the axis of rotation, do not attempt to shear. Scrape the workpiece round Figure Trying to shear will tear out large chunks of the stock.
Shearing only works well when the wood grain is parallel to the axis of rotation. Sizing After the workpiece has been rounded, it should be marked to show the limits and the depth of shapes you wish to produce. With the machine turned off, work with dividers or a pencil compass to mark concentric circles Figure , but be sure to use the tool rest for support.
Use a light touch. You can use a marking gauge to mark dimension lines on the perimeter of the workpiece as shown in Figure Most woodworkers prefer to turn the outside first Figure Make your beads and coves in the same manner as you would for spindle turning. If the wood grain is perpendicular to the axis of rotation, scrape the desired shape in the outside of the workpiece.
When you get ready to turn the inside of the workpiece, turn the machine off. No matter what the orientation of the wood grain, scraping is the only way to shape the inside of a faceplate turning.
This is slow work, so have patience. When doing deep hollowing jobs, keep adjusting the tool rest to provide good chisel support even if it means partially inserting the tool rest in the hollow being formed Figure As you continue the. Stop scraping whenever you've removed as much stock as you want to cut away.
Figure shows a gauge you can make to check the depth of hollowing cuts. Cut depths can also be checked by placing a straightedge across the face of the workpiece and then measuring from it to the bottom of the cavity. Templates, like those described for spindle turnings, can also be made for faceplate work Figure One side of the template is used to mark dimension points, the other side has the checking profile that you use to gauge the cuts you make.
Templates are always a good idea when you must turn duplicate pieces. Sanding When you've finished shaping the turning, turn off the machine and let it come to a complete stop.
You can remove the feathers either by wetting the wood or by removing the faceplate from the main spindle and remounting it on the upper auxiliary spindle Figure This reverses the direction of rotation. Parting To part a faceplate turning, first dismount the faceplate from the Mark V spindle and unscrew the faceplate from the scrap block.
Clamp the scrap block in a vise and place a bench chisel against the joint between the block and the turning where you've put the paper. Sharply rap the chisel with a mallet, driving it in between the block and the turning Figure The turning will part from the scrap block. Sand any paper or excess glue off the turning.
Other Special Techniques. There are many special techniques that can be performed on the lathe. Let's take a look at some of the simplest:. Screw Center Work Workpieces that are too small to be mounted on a faceplate or not long enough to be fitted between centers can be set up for turning by using a screw center a device that is mounted on the Mark V main spindle. Find the center of the workpiece and start a hole for the screw by using an awl or by drilling.
Mount the workpiece by threading it on the screw center Figure The technique makes it possible to shape small items like drawer or door pulls, finials or small posts Figure Extra-Long Work.
When a project is longer than the spindle capacity of the lathe, it can be turned as separate pieces that are then joined in the manner shown in Figure The tenon on the one piece can be formed while the part is on the lathe.
Drill a matching hole in the mating piece; then put the parts together with glue. Use a Iockwedge, if you wish, to reinforce the joint. The same idea applies when you join a faceplate turning to a spindle turning Figure Glued-Up Stock When a large diameter is required in one area of the turning, two methods are used to prepare the stock Figure In one, start with oversized stock and use a jointer or bandsaw to reduce the stock before it is mounted on the lathe.
Warning: Glue the stock and leave it clamped for at least 24 hours prior to turning. In the other, glued blocks are used to build up the larger diameter. The mating surfaces must be perfectly flat and true for a perfect joint if the final turning is to resemble a solid piece of wood. When solid stock large enough for a deep bowl or similar project is not available, stock may be glued together Figure Or rough-cut rings may be glued onto a solid base.
This method saves a lot of material since the cutout discs may be used in other ways. Figure shows rings cut for a project that will have straight sides.
If the sides are to slope or taper, the rings should vary in size. The important thing is a good glue job so the stock will hold together with just a faint line showing on the finished item.
You can produce intriguing lathe projects with an inlaid appearance when you prepare the base stock by gluing together pieces of contrasting wood. The initial blocks can be prepared for either spindle turning Figure or faceplate turning Figure The blocks won't look like much to start; the appealing effects occur when the turning is complete. It's not easy, but try to visualize the results as you plan the initial block assemblies.
Select wood not only on the basis of color contrast, but also for similarity in density. Good combinations to try are maple with rosewood, and holly or birch with cherry, walnut, or mahogany. Split Turnings Split turnings are lathe projects that end up as half-round, shaped columns.
Using the paper-glue-joint method shown in Figure , two pieces of wood will produce identical half-round mold-ings. Four pieces of wood, paper-glued to a central core piece, will separate as elliptical moldings. Four pieces of wood, assembled as a solid block, will become four pieces of quarter-round molding. Procedures like this are useful when a special molding is needed or when you need a particular hardwood molding that isn't available.
Through Holes The two methods shown in Figure can be used to prepare stock for projects like lamp bases before the material is mounted for lathe turning. Cut grooves in the center of the stock.
Glue the pieces together and use keys to plug the opening at each end. When the turning is complete, open the grooves by boring holes at each end of the turning. Accurate center holes, of limited length when using conventional bits or much deeper when working with extra-long bits or extension bits, can be formed by mounting the drill chuck on the tailstock.
Figure shows the technique being used to form a socket hole in a small candle stand. The procedure is the opposite of normal boring. Here, the drill bit is stationary; the workpiece turns.
Indexing Some lathe projects, like wheel hubs, require radial holes that are equally spaced about their circumference. A good way to do such work accurately is to use an indexing device.
The plans for one that you can make and which is mounted on the Mark V's upper auxiliary spindle is shown in Figure Make the guide pin holder first. Then drill holes in the power plant cover and mount the holder as shown in Figure Drilling holes in the power plant cover will not damage the machine. You must situate the holder so the guide pin and the spindle have a common vertical centerline.
The indexing disk, which is the control that positions a project for drilling, is made next. After the disk is cut out and rounded, mount it on a small faceplate. Then secure the faceplate on the auxiliary spindle Figure Push the guide pin forward so it will mark the disk.
This will establish the radius of the circle on whose circumference the guide holes must be drilled. A carbide insert comes installed on these tools. Replace Torx keys and screws for boring carbide insert holders with coolant hole. Deliver coolant through the holder to keep workpieces cool while boring tough materials, such as steel, stainless steel, and nickel-based alloys. Pair one of these inserts with a compatible boring carbide insert holder with coolant hole.
They come with an insert installed. These sets have a variety of indexable boring insert holders with carbide inserts and a wood storage stand. When one edge of a tool's insert dulls, rotate it to use a sharp edge to enlarge existing holes to precise diameters.
Contour the interior wall of a hollow workpiece when you pair a holder with a compatible insert. Combine a carbide insert with a compatible internal profiling holder to create a tool that can contour the interior wall of a hollow workpiece. Also known as lathe chuck keys, the long T-handle on these wrenches provides the leverage to open tight lathe chucks.
When hand pressure is released, the wrench automatically pops out so you won't leave it in the chuck. Also known as scroll chucks, these are self centering— all three jaws move in unison, centering the workpiece as they close. Machine these jaws to fit the curves and edges of your unique workpiece for a tighter hold and more stability than standard hardened jaws. Made from hardened steel, these jaws have a long service life even when performing heavy machining such as roughing cuts.
No need to break down a collet set up when a workpiece doesn't fit a 5C collet. Install one of these lathe chuck adapters in your 5C collet chuck or holder and its three jaws will securely grasp the workpiece.
Consistently position workpieces in a three-jaw lathe chuck by installing a chuck stop. These stops enable short workpieces to extend beyond the chuck's jaws, providing additional clearance.
Secure jaws to a CNC lathe chuck with industry standard 1. When a job calls for a 5C collet, save time by using an adapter instead of removing your lathe chuck. Hold machinable lathe chuck jaws in place during machining to make accurate cuts, ensuring the jaws will securely grip your workpiece.
Also known as axial-feed knurls, these have a convex face, which produces a cleaner pattern and lasts longer than standard knurls. Pair these knurls with a knurling tool to create patterns on a workpiece for an improved grip. These tools are specially designed to perform heavy duty knurling applications using a CNC lathe.
These light duty centers are for intermittent use on manual lathes. A hardened body and point provide the extra strength and wear resistance necessary for continuous use on manual or CNC lathes. Also known as bull-nose centers, these have a wide head to hold pipe and large-diameter tubing. Dead centers are one solid piece.
Use them in the headstock when machining between centers or in the tailstock to support the end of a workpiece when friction is not a concern. Also known as lathe dogs, these drivers connect to a lathe to turn your workpiece when machining between centers. A set screw grips the workpiece while the bent tail connects to the lathe to transmit motion. An expanding screw widens the end of the mandrel for a tight hold on the inside of a workpiece.
The mandrels in these sets have an expanding screw that widens the end of the mandrel for a tight hold on the inside of a workpiece. The sleeve on these mandrels expands to hold a range of diameters for better versatility than solid and expanding-end mandrels. Use an arbor press to secure the narrow end of one of these tapered mandrels into the hole of a workpiece. Block chips while maintaining an unobstructed view of the workpiece.
These guards mount and travel on the cross slides and are fully adjustable in all directions. A V -groove enables these holders to grip round-shank as well as square-shank tools. Four flat head screws lock down round-shank tools in a precision-ground bore for increased rigidity over other round-shank tool holders.
Two slide -in dovetail mounts on the tool posts allow you to quickly change from one tool holder to another. Securely hold cutoff blades in a quick-change tool post. A built -in drill chuck allows quick installation of drill bits, taps, and other round- or hex-shank tools into a quick-change tool post.
These holders work with any 5C collet to rigidly grip drill bits, taps, end mills, and other tools. Mount any tool with a Morse taper shank to a quick-change tool post.
Instead of widening a hole using a lathe, which turns the workpiece while the cutting tool stays still, use these holders to turn your boring bar in a milling machine and keep the workpiece stationary.
Keep hands safely out of the way while deburring, sanding, and polishing workpieces on a lathe. Mount a digital readout system onto your manual lathe.
It measures and displays precise tool and workpiece positioning on two axes. Contact Us Order. Log in. Create login. Search Results. Cut Type. For Use On. Cut Direction. System of Measurement. Shank Width. Shank Height. Material Grade. Shank Type. Insert Shape. Overall Length. Tool Bit Code. Tip Radius. For Insert Shape. End Relief Angle. Insert Code. CCMT- Shank Diameter.
Groove Width. Side Relief Angle. Insert Style. End Cutting Edge Angle. Side Rake Angle. Back Rake Angle. Inscribed Circle Diameter IC. View catalog pages Send Cancel. How can we improve? Lathe Tools. Carbide-Tipped Turning Lathe Tools. Diamond-Tipped Turning Lathe Tools. High-Speed Steel Cutoff Blades. Carbide-Tipped Cutoff Blades. Face Grooving Lathe Tools. Curve-Cutting Lathe Tools.
Form concave or convex edges on a workpiece. Round-Shank Boring Lathe Tools. These are the smallest boring tools we offer. Square-Shank Boring Lathe Tools. Internal Profiling Lathe Tools. Contour the interior wall of a hollow workpiece.
Lathe Tool Sets. Boring Lathe Tool Sets. Lathe Tool Holders. Cutoff Blade Holders. Secure square-shank tools to a lathe. Boring Lathe Tool Holders. Quick-Change Lathe Tools and Holders. Indexable Turning Tools. Turning Carbide Insert Holders. Parts for Carbide Insert Holders. Screws for Carbide Insert Holders. Carbide Inserts. Economy Carbide Inserts. Economy Indexable Turning Tools. Economy Indexable Turning Tool Sets.
Cubic Boron Nitride Inserts. Alumina Ceramic Inserts. Indexable Cutoff and Grooving Tools. Cutoff and Grooving Carbide Inserts. Mount blade-style holders to a lathe tool post. Indexable Grooving and Profiling Carbide Inserts. Indexable Cutoff and Grooving Carbide Inserts.
Indexable Threading Tools. High-Performance Grooving Carbide Inserts. High-Performance Threading Carbide Inserts. Economy Indexable Lathe Tools Online Shopping Questions Threading Tools. Indexable Boring Tools. Boring Carbide Insert Holders. These holders conform to ANSI standards. Indexable Internal Profiling Tools. Internal Profiling Carbide Insert Holders. Lathe Chucks. Lathe Chuck Wrenches. Self-Ejecting Lathe Chuck Wrenches. Three-Jaw Lathe Chucks.
Machinable Lathe Chuck Jaws. Hardened Lathe Chuck Jaws. Chuck Stops. Lathe Chuck Jaw Nuts. Lathe Chuck to 5C Collet Adapters. Knurling Lathe Tools. Manual Lathe Knurling Tools. Attach these tools to a manual lathe. Long-Life Knurls. Create a knurled pattern on the end of a workpiece. Work faster by using two knurls at the same time. Lathe Centers. Live Centers for Intermittent Use. Live Centers for Continuous Use. Pipe and Tubing Live Centers.
Dead Centers. Lathe Drivers. Lathe Mandrels. Expanding-End Lathe Mandrels. Expanding-End Lathe Mandrel Sets.
Wide-Diameter Range Lathe Mandrels. Solid Lathe Mandrels. Lathe Lathe Tools Online Shopping 360 Guards. Adjustable Lathe Guards. Grip square-shank lathe tools. Quick-Change Lathe Tool Posts. Boring Tool Holders for Milling Machines. Belt Sanders for Lathes. Linear Scales with Digital Readout for Lathes.
By using this website, you agree to our Terms and Conditions and Privacy Policy. The quick brown fox jumped over the lazy dog. Pedestal 35" Ht. Along- the- Length Turning. External Grooving. External Profiling. External Threading.



Rocker Arm Bearing Replacement Boxplot Upper Hinge Thick Veneer Worktops Rate |
LEYLISIZ_MECNUN
20.01.2021 at 11:24:44
Gunewli_Balasi
20.01.2021 at 15:22:14
0110
20.01.2021 at 15:33:40
LEZGI_RUSH
20.01.2021 at 11:54:32