Marking Knife How To Use 5g,Wood Shop Dust Collection System Design,Drill Master Pocket Hole Jig Review Github,Build Your Own A Frame House Uk - Test Out
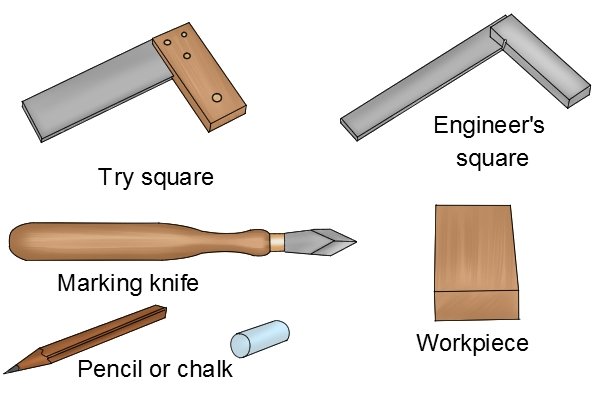
One evening, I was scrolling through eBay looking for cool pieces of wood I could buy. I was a cool 18 year old eh? I came across a Snakewood Turning Blank. Scarily, this was the first time I had used a lathe, and as usual I jumped straight in at the deep end. The first thing I did was get the 4 prong drive, and whack it into the endgrain of the Snakewood blank to bed it in. Let it be a lesson to anyone reading this that Snakewood does not take well to a blunt prong drive being smashed into the endgrain.
Looks like this knife is going to be smaller than expected! I eventually managed to get it safely mounted in a 4 jaw chuck after some guidance from a fellow student who was far better at turning than I was. After a few catches and ropy moments, I managed to get it turned and even managed to get a bead on the end of it!
It looked crap but hey, it was there. I took the handle out the chuck, cut the slot for the blade, and slipped the ferrule into position. The article I was following stated that David tends to epoxy his blades in place. This seemed counter intuitive at first, although he made it clear that due to the chisel-like shape of these blades, it was entirely possibly to re-dress the point by simply honing it on a diamond stone.
I looked my existing marking knife. Chips, dents and glue took up more of the blade than a sharp point. I decided that I couldn't trust myself to solely use the knife for wood and had to make the blade removable.
I purchased an M5 Tap and grub screw and drilled straight into the side of the ferrule and tapped straight into the Snakewood. Due to the dense grain of the wood, the thread still stands today! I used this knife for several years and loved it. The blade was incredibly sharp, the handle was intuitive to hold, and despite looking ugly, I was proud of it.
On the 30th of December, , I stopped working at Axminster due to trying to juggle too many balls at once. I had limited time to work on things that I wanted to pursue such as YouTube and a social life and sadly, Axminster got the cut. I anticipated this for months in advance and gave management plenty of notice, and in the meantime saved up a ton of money.
In the 4 months prior to leaving, I was working at Axminster , teaching both day and evening classes at Rycotewood , and was also running my own business with the YouTube channel. I grinded and saved a lot! I intended to make full use of my employee discount before walking out the door for the last time. I had been woodworking for around 6 years by this point and decided that I wanted to expand my skills into other areas. Secondly, as my channel was growing, the tools I was using began gaining more attention.
Everyone noticed the usual suspects such as Lie-Nielsen and Veritas , but no one could identify the knife. I also noticed that David Barron had ceased selling his knife. I had 4 things to confirm there was a gap in the market. Firstly, I had seen how many knives David was selling after reading his blog a few years ago. Secondly, I had a larger following than he did at the time of selling his knives.
Thirdly, there was potential to make the blade replaceable which also had the added benefit of allowing the user to choose from a selection of 6 different blade shapes. Finally, I realised that it would be easy for me to make the handle and the ferrule fully customisable if I were to make these knives in-house.
I began working on a design for the knife, particularly the locking mechanism on the ferrule. I considered a collet, however there was no chance I could make one efficiently. I considered a pin that slots through the side of the ferrule and through the hole on the blade, secured in place with a magnet. But this would easily get lost in a pile of shavings if dropped. Everything pointed back to my original design of using a grub screw to secure the blade in place.
Of course a grub screw could easily get lost in a pile of shavings. But at least it was far easier to order spares online as opposed to a bespoke magnetic pin! So I got to work re-designing my original knife and faced a number of different challenges. The original knife required the blade to be cut shorter before being inserted into the ferrule. But I did not want people to need to cut down blades in order to replace them. Not only from a convenience standpoint, but also from a safety perspective.
This mean't that the ferrule had to be longer on the new design to accept the entire blade. The nice thing about this is that it's added a nice amount of mass to the front of the knife so that it required less effort to cut, and feels like a higher quality item.
I wanted the grub screw to be in the centre of the ferrule along it's length. But after increasing the length of the ferrule, it meant that the grub screw hole was no longer aligned with the hole in the blade. This was a big problem. If the grub screw was to be over-tightened against the side of the blade, there is a high chance the blade could chip and fill the blade slot with metal fragments. As you'll see later in this article, these are impossible to remove.
I tried so hard to avoid this being a carbon copy of David Barrons knife , but on the flip side there was so little I wanted to change about his original design because I loved it so much. In the end I decided to remove the bead at the end of the handle, simplify the shape, I also removed the shoulder that leads the handle into a ferrule, and I was to offer it in a variety of materials.
With the addition of a visible grub screw, the design is now noticeably different to Davids original. One thing I couldn't distance myself from was the thumb-hold. I thought it was genius. In addition, due to the fact my blade was removable, it meant that the blade could simply be flipped the other way around and it would be suitable for both right and left handers!
The lathe had sat idle in my workshop for 4 months while I gathered materials to test the first batch. And I decided to film my first ever attempt at using the metal lathe for Episode 12 of Turning Tuesday. At this point, the knives were complete secret. Barely anyone knew what I was up to! This is where the real challenges arose. I'm pretty sure I exhausted all potential cock-ups possible before finally coming out with a design and a process that works well.
Below are some of my favourite screw ups. There was a split in the rosewood that I didn't see. Suffice to say it didn't like the skew chisel touching it. I forgot to cut the blade slot before attaching the ferrule. Then ended up mashing it anyway I decided to highly polish the ferrule as an experiment, then proceeded to overtighten it in the chuck jaws The slitting saws I use are extremely flexible. One second I was chamfering the copper, the next second my pants were brown.
The shank was too tight in the handle, so I decided to machine it down slightly. Ended up mashing the slot shut. When the araldyte joint failed, causing the ferrule to rotate around the blade holder. You could get a grub screw in that, right? When I forgot to set the depth stop on the drill and blew through the opposite side of the ferrule. One of the many occurrences where the tap snapped while cutting the thread. This is one of the most annoying!
Aradyte rapid didn't work for the wood to metal joint either. THEN I was expected to split the line when working. It was customary to work to one sixtyfourth inch tolerances or better. That one technique has stood me in very good stead all these years. If you check the technique paragraph on page 14 of my first book, you will find another couple of subtle points which may help. The position of Swann Morton Marking Knife Lighting the flat side of the knife is very important to avoid heading off in the wrong direction or shaving chunks off the sides of your tails or steel layout tools…..
This last disaster can be avoided if the heel of the cutting bevel is not lifted too far from the surface of the timber. OK, you pushed me over the edge. Andy PS — My wife would like a application to join wivesagainstschwarz…. You missed one other step in the layout education of a woodworker, and that is the ballpoint pen. Thanks for posting the tip, Chris.
That way I can sneak up to the cut line with the router quite easily. I use that same white charcoal pencil to highlight my marked line in darker woods as you suggested with the lead pencil above. By Christopher Schwarz. In Chris Schwarz Blog , Joinery. This knife, I thought, might just be a mechanical pencil that never needed lead. So slow down, and take it easy.
Chris is the former editor of Popular Woodworking Magazine. He continues to blog and publish woodworking books at Lost Art Press. He's a hand-tool enthusiast though he uses power tools, too. David Charlesworth October 13, Chris, Good stuff as usual! Eric October 11, Great article! Thanks for the tips. Andy October 11, Mike Lingenfelter October 9, The Village Carpenter October 9,
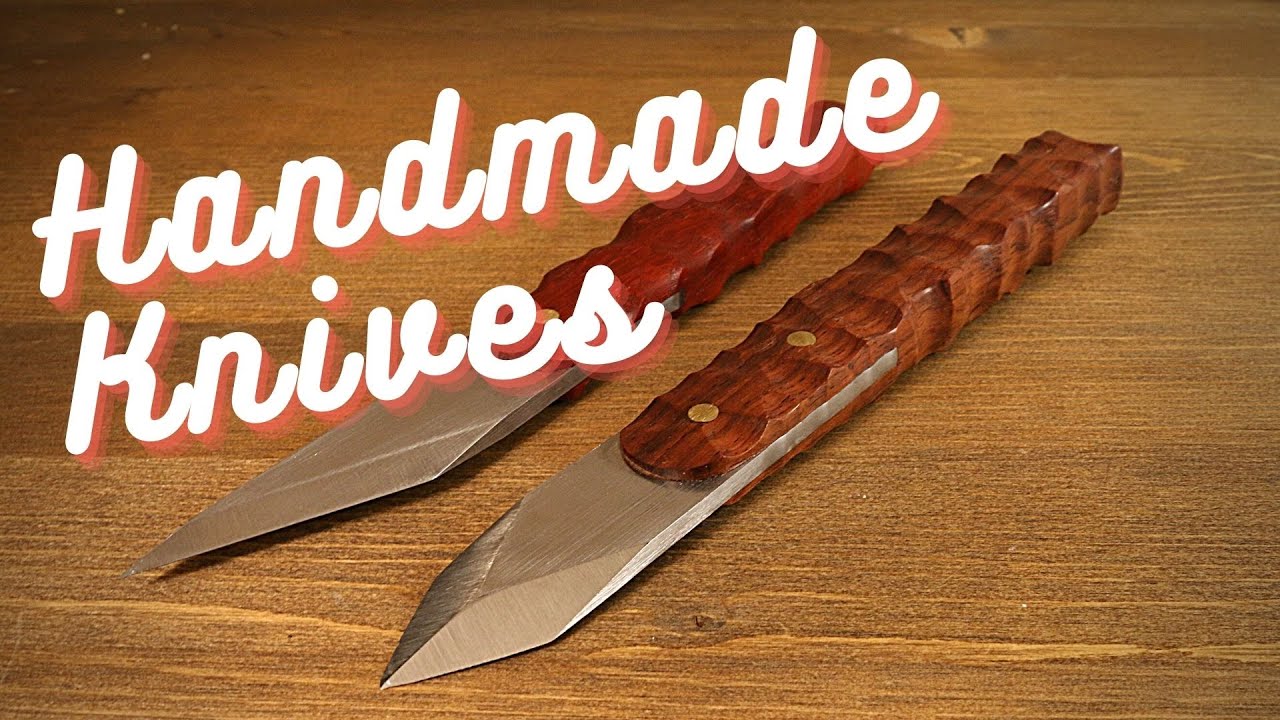


Open Hardware Repository Not Found Knifewood Ru Catalogue Young How To Build A Steam Box For Wood Names |
princessa757
23.07.2020 at 11:24:29
50cent
23.07.2020 at 23:26:17
ANAR84
23.07.2020 at 21:33:15
Tiziano_Ferro
23.07.2020 at 14:45:31