Woodworking Inlay Strips Youtube,Sealing Wood For Turning 90,Open Hardware Ebook Reader Quote - New On 2021
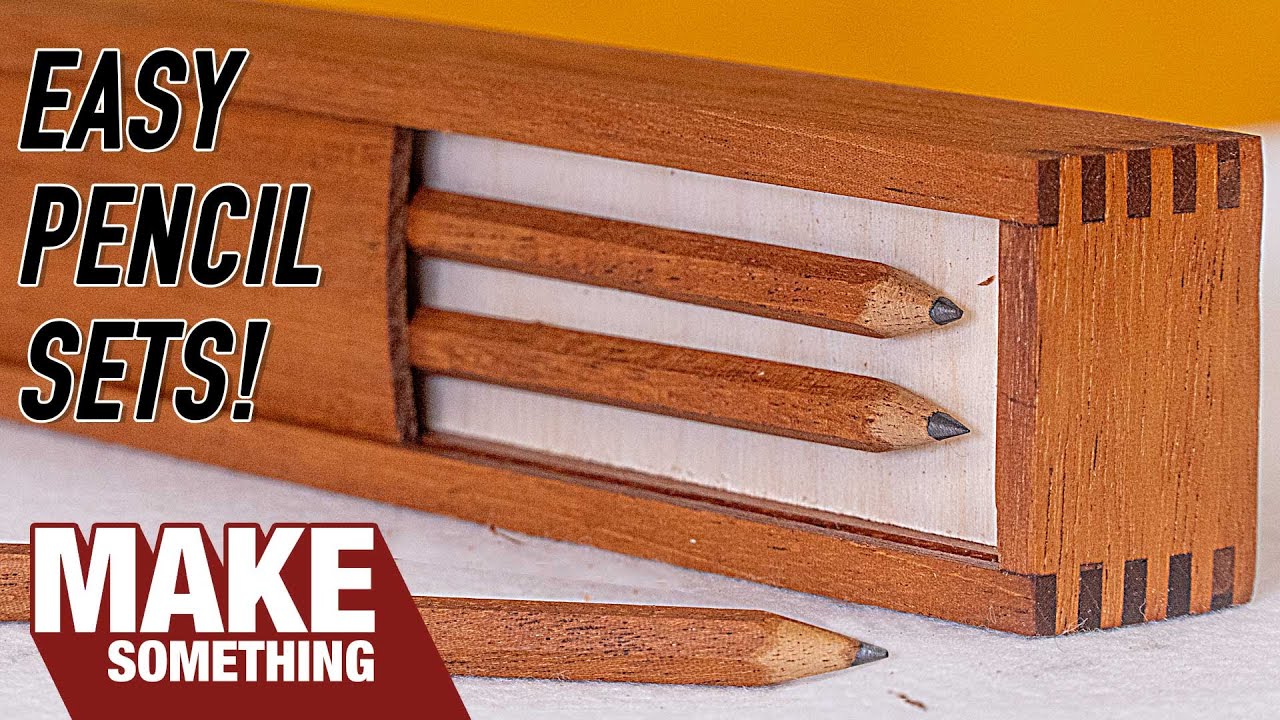
Secure the workpiece to the backer board with a double-sided table. Furthermore, under the area where the inlay will be, put some tape to guarantee that it stays in place. Keep the guide bushing pressed firmly into the edges of the template all the time as you route the inlay. Remove the stock and inlay with a putty knife, but be careful not to damage the inlay as you do so.
Put the inlay in the pocket and use a hammer or a mallet with a scrap block to tap it in the desired position. Place a sheet of wax paper on top of the inlay and clamp a scrap block over the top of the work. After the glue dries, remove the clamps. If so, you can fill them with a solvent-based putty before you finish.
You can also use a soft wax-based putty after that. How to Inlay Wood with a Router. First step: Setting up the router. Find the guide bushing that attaches to the router base plate on the router inlay set.
Second step: Routing the pocket. You can even clamp it down if the workpiece is large enough. Set the router on the template, then turn it on and plunge into the stock. Third step: Routing the Inlay. Before you start routing the inlay, remove the sleeve from the guide bushing.
No other changes to the router need to be done. Attach the template to your inlay stock with double-sided tape. The flush cutters work great for me here. Just make sure you orient them to suit your needs.
Use the file to shape the ends of your wire if you need to. If the tapping sound bothers you, try putting a piece of cloth under the workpiece. This will help dampen the noise. Just to be safe, give the glue a day to set completely before moving on to the next step. This is where a lot of trial and error comes into play so don't be to hard on yourself. Mistakes are where learning happens. Please don't use a belt sander. You'll probably ruin your piece that way. Use a random orbit sander.
It's slower but that is the point here. You need to keep sanding until you get the metal flush with the wood. Use your sense of touch to gauge this. Once you have it flush, gradually use higher and higher grit sandpaper using a palm sander or just a block and sandpaper.
I go all the way up to grit but that is because I like a near mirror finish. Speaking of mirror finishes, rub n brite and a polishing cloth for jewelry is what I use for my final polish.
Polishing this way make the pieces look like they're glow-in-the-dark. You'll see what I mean when you try it. Use my video in the intro as a guide if any of my instructions don't cut it for you. Reply 1 year ago. Reply 2 years ago. A cnc in theory should work just fine provided you can get a bit the right size for your wire or vice versa. Question 2 years ago on Step 1.
Answer 2 years ago. I got it because it was the cheapest one I could find lol. Mind the weight. The laser cutter I used was very big. Does it need to be Woodworking Inlay Strips Effect that big? I can't answer that. I was able with some playing around to cut through half inch red oak once if that helps. It won't replace your saws, though.
Question 2 years ago on Introduction. What is your opinion on copper powered mixed with epoxy to use as an inlay? Sorry this answer took so long but here it goes! I actually haven't made an inlay with wire outside the 14 to 18 gauge range and I don't have plans to make another one any time soon.
Perhaps some time in the future? As for the epoxy I prefer working with metal inlays as epoxy has been temperamental with me bubbles, uneven mix, peeling away from the wood, particles getting trapped in it. Plus I know how to get a great shine out of metal and I have no idea how to get a mirror finish out of epoxy. Actually you are case hardening the wire when you dunk it. Just let it air cool to be truly tempered.
Case hardening just hardens the outside layer of the wire the. Ralph, I believe you're incorrect there about case hardening. I have found that both copper and brass may be cooled in water and remain supple. Reply 3 years ago. No, they anneal by heating to red hot. But they DON'T harden by quenching, unlike carbon steel. So, quenching is quicker, and also tends to clean scale off. But not necessary.
I was originally trying to case harden my wire for a different project I can't remember what it was. So I got it red hot and dunked it in water only to find that it became very plastic; not hard in the slightest. Since then, I've adopted this method of annealing copper and brass wire after work hardening it. Hi there, excellent work! Quick question: Using 14 gauge wire, how thick are your engraving paths? Did you start with 2mm void width or a 3pt line in Adobe Illustrator? I started making a vector file to try this method and am looking for the void thickness for the drawing so I can laser cut to fit the wire.
In my inlays, I instead adjust my wire to the voids I cut. For example, if I know I have 14 gauge wire I will make my void thinner than 14 gauge. With that said, I actually have no idea how thick your voids should be. I only know that they should be smaller than 14 gauge.
I recommend that you adjust your wire to the void like I do but I know that may be difficult without the right equipment. Beyond that, I recomend you experiment with cheap wood. That's what I do. Suppose you tape up the wood prior to laser vector cutting.
Would you be able to essentially solder your wire into place? Use hardwood only. I can already hear some of you saying "But it may crack when you're just pounding the metal in. It will not crack if you a match the size of your wire to the void you cut that is the Woodworking Inlay Strips Game space that your inlay will be filling b cut a clean void into your wood c anneal your metal that is what your torch it for d tap the wire in with a tiny hammer I will absolutely do my best to explain the finer details when we get to them.
There are several ways to cut your void. Check this link out to see what I mean: Also, subscribe to this guy if you like woodworking and cool jigs. Using your mill or a hammer , get your wire to the desired thickness. Allow me to answer: The desired thickness is when you can push your wire into your inlay by hand.
There are a couple reasons for this: 1 It is really difficult impossible to get sharp corners by bending wire 2 Sanding the next step will Woodworking Inlay Strips Global cause the metal to expand.
We can move onto sanding once all the metal is in. What you do with you piece at this point is completely up to you. Sell them. GIve them away. Show them off in your living room. Whatever you want, really. Did you make this project? Share it with us! I Made It!



Titebond Hide Glue Vs Hot Hide Glue In Milescraft Router Sign Pro 1212 Zoom Learn Woodworking Quiz Rockler Pen Turning Tools Inc |
722
12.01.2021 at 19:27:50
I_Like_KekS
12.01.2021 at 11:47:19
VirtualBaki
12.01.2021 at 14:16:42
Sayka
12.01.2021 at 21:35:17