Build Your Own Metal Frame 900,Table Saw Projects Free Plans Zone,Woodworkers Journal Premium Content Kit,Mini Cyclone Bucket Dust Collector - PDF 2021

The following sizes automatically include a mat with the following opening sizes. Mats do not come standard with Poster or Certificate frames. If interested in purchasing additional mats or colors they can be done so via Mat Designers. Chat Support. Metal Frames. U-Frame Kit I. Select a size. Shell Only? Foam Core? I started with a solid concrete foundation.
Perhaps it was overkill, but I brought each truss pad to precise grade with thinset grout. Anchor bolts need to be precisely placed, so I did not set conventional J-bolts into the wet cement. Instead I drilled and epoxied Allthread after the concrete was set. Pilot holes were drilled in scrap plywood at the exact anchor points to guide and support the rotary hammer bit, then that same plywood template was used to hold the anchor bolts in place as the epoxy was setting.
When it was time to erect the steel, I had help from a friend. The columns were a bit heavy and bulky to set by hand, so we used a tractor. Initially, we were unable to find the wind bracing rods in the material pile, so we used nylon cargo straps as a temporary solution.
Shortly thereafter we found the wind bracing rods nested inside the roof trusses. I set up temporary scaffolding on a tandem axle trailer. Erecting the trusses was definitely not a solo operation. While the trusses were only a few hundred pounds, it would have been very difficult to erect them without additional help and equipment.
My friend and I used a Gradall, and all six trusses were bolted in place in less than three hours. While the Gradall was on site, I also used it to place a row of temporary purlins near the peak. This would have been difficult to accomplish without the equipment.
Using a Gradeall to hold truss while bolting in place. Next I placed the permanent purlins. The moveable scaffolding was handy during this step of the metal building construction. The only quality control issue that I found in this steel building package was with the wind bracing rods. The threads were poorly cut poorly leaving gaps on the rods.
However, the way the rods are installed allowed me to position the nuts on the good portion of the threads. It would be nice to have clean threads and minimum torque specs.
Constructing this steel building solo, most purlins were not a problem because they sat on the trusses and the anchor plates and were held in place by gravity while being bolted down.
However, the bottom outboard purlin has nothing to sit on while it is being bolted in place. So I temporarily screwed notched 2x4s on the ends to hook on the anchor plates while bolting the bottom purlin. After the girts and purlins were in place, it became apparent that our hot Idaho sun during a record heat wave was not being nice to the exposed wood. A downside to constructing my steel building solo is that it took longer, giving the wood more time to twist and bow in the heat.
It was so bad that gang drilling the panels would have been impractical. So I ended up placing blocking at the midpoint of all girts and purlins to straighten them out. Blocking in place on the girts and purlins. The end columns were too heavy for me to lift into place, so I used a forklift and chain hoist. Instead, I should have used a plumb bob. Forks and chain hoist used to lift door headers. Once the overhead door headers and the overhead doors were installed, I was ready to install the siding.
As recommended in the construction plans, it is best to pre-drill the panels. For this project, I made a jig to hold the bit. That prevented me from having to mark each line while also holding the bit nice and straight. Limit gang drilling to six sheets, but doing so is a major time saver.
I framed the windows and man doors to match the spacing of the 3-foot wide panels. That made cutting the panels around those openings easier and saved a significant amount of panel material that I will repurpose later on another project. Inspect each and every aspect of your ideal steel structure and see your building take shape before your eyes:.
Elephant Structures began our business with the goal of providing a no-hassle solution for creating and ordering custom metal buildings online. We are an industry leader for not only prefab steel structures but DIY building kits too, so any customer is covered. Want a custom colored building? Looking to design the interior? You can do it all with Elephant Structures.
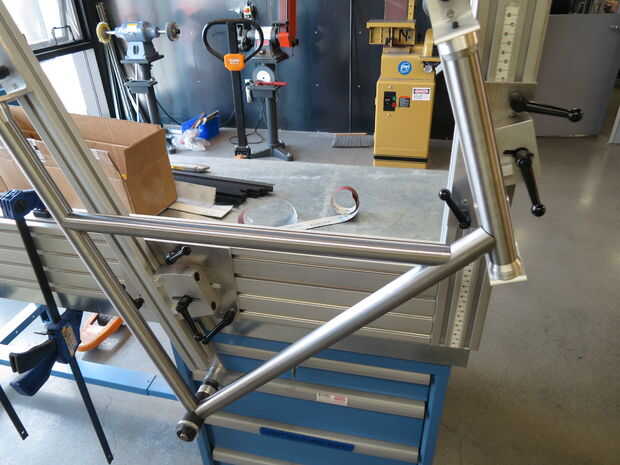
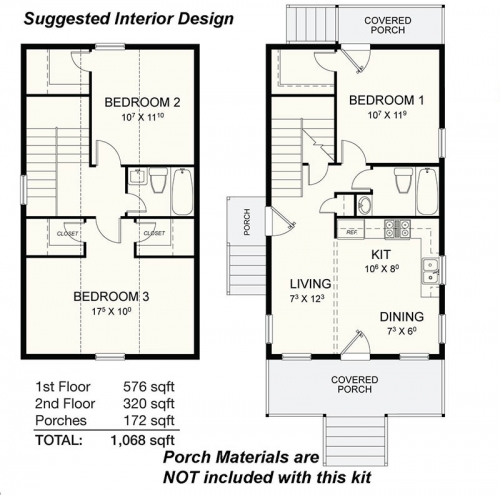

Maple Wood For Turning Glory Wood Shop Air Filter Reviews Data Trap Door Hinges Hardware Pocket Hole Jig Greece Net |
mikrob
18.05.2021 at 16:54:43
TM_087
18.05.2021 at 15:32:45
shirin
18.05.2021 at 10:53:59
Bad_Boy
18.05.2021 at 14:22:35
Dj_SkypeGirl
18.05.2021 at 23:50:13