Workshop Layout Tool Js,Wood Floor Sanding Machine Rental Us,1600 Woodworking Plans Key,Woodworking Files Home Depot 03 - Plans On 2021

The plastic flexible hose is connected to a small 6 in. A router table with integral dust collection, tubing and blast gate can be seen in the fourth photo. Dust collection is critical in a woodworking environment.
The process of preparing and dimensioning lumber using machines produces copious amounts of dust and shavings. If the dust is not removed at the source, it will become airborne and infiltrate the air you breathe. Fine wood dust causes health problems and should be avoided, especially if you are woodworking for long periods of time. Thickness planers typically produce a large amount of shavings.
Low velocity and high volume dust collectors excel at quickly removing the chips from the planer. Alternatively, routers, tablesaws and bandsaws generate large amounts of fine dust which is also handled efficiently by large capacity DC systems.
The first two photos are of 1. This dust collector is attached to a cyclone lid setup. Blast gates controlling the input to the dust collector can also be seen. The blast gates are located a short distance from the dust port of each machine. Typically, only one blast gate is open when dust collectors under 2 HP are used.
This creates the maximum velocity and volume to effectively evacuate the dust from a stationary machine. The photos also demonstrate how flexible 4 inch piping is connected to common woodworking machines, in this case a 13 in. The machines each have a blast gate to control dust collection.
Capturing dust at the source will create a healthier environment for your woodworking. If not captured, the dust will become airborne and begin to settle on all horizontal surfaces. In a very short time, your woodworking workshop will begin to collect a layer of dust. There are several reasons why this is not advisable, notably health, fire safety and your insurance premiums. You will likely find that effective dust collection helps to create a clean, safe workshop environment and will also result in lower insurance premiums.
Bandsaws often pose a challenge to dust collection. Fine dust is created and follows the blade and bandsaw wheel motion. Factory dust ports located under the bandsaw table only succeed in capturing a portion of the fine dust generated. The need for another dust port at the apex of the lower wheel becomes critical to capture all the fine dust before it exits the lower wheel cover housing.
In this photo I have designed and adapted a dust port flange to the lower wheel cover of a standard 14 inch bandsaw. The removal of dust is greatly improved with this additional dust port.
Shown is a photo of a vacuum fitting, hose and blast gate attached to a bandsaw. Also, another photo of vacuum fittings, hoses and a blast gate attached to a bandsaw. A magnetic dust chute which clips on to the bandsaw casting is at the front. If the shop is to be used primarily for woodworking, the minimum recommended area for the workshop is 75 square feet. An ideal shop would measure square feet, to this area would be added a lumber storage area.
The size of the shop is determined by the number of stationary power tools that it will hold. The main workbench in the shop should be designed for both sitting with access to a stool, and for standing.
The workbench should be located approximately 4 feet from stationary machines. The machines should be spaced a minimum of 3 feet apart. If space is limited, install rolling bases on the equipment.
Machines should be placed as to not impede traffic flow. Material, both raw lumber and finished goods, needs to be moved into and out of the shop.
Provide a large door or a window for this. Machines used in a sequence should be placed close together. Allow ample clearance for doorways. Tools can be placed on pegboards mounted to walls, or in separate freestanding tool cabinets.
Proper lighting in a workshop is very important, and natural ambient light or sunlight is ideal. Place machines or workbenches so that bright sunlight will not shine directly into your eyes. Reflected light can be an asset in any shop. Paint the ceiling and walls white or off-white as to reflect maximum light. Shown is a typical workshop floor plan. A general floor plan for your workshop should be drawn up. All equipment should be positioned to provide maximum flexibility and with the ability for you to manoeuvre around the machines and your workbench or workbenches.
If you have a large space available to you, plan for future additional equipment. A lumber storage area is important, and can be either situated in the workshop or outside. Photo shows a recent view of my current woodworking workshop. Make sure the workshop has adequate electrical service and plenty of lighting. Ideally, a medium sized workshop will have its own electrical sub-panel also known as a pony panel.
This panel serves the receptacles and lighting for the workshop and can be readily turned off if necessary. The sub-panel should be wired for the maximum amperage drawn in the workshop and this includes lighting. It is prudent to consider that 2 machines will be operating simultaneously as is the case when a machine and dust collector are running at the same time. In this case the amperage drawn will increase considerably. Shown is an electrical sub-panel for the workshop.
This particular sub-panel or pony panel is located next to an alarm system control box with attached motion sensor. Another consideration in a workshop is the location of electrical outlets.
The normal height of an electrical outlet in a home is about one foot from the floor. In a workshop, it is preferred to have the outlets approximately 4 feet off the ground. This is well above the height of workbench surfaces and it will be much easier to plug small tools in. Consider the location of electrical outlets if designing your own workshop. The quantity and horizontal spacing of electrical outlets in a dedicated workshop should also be greater than in a home space. It is best to have no more than outlets per circuit breaker since power tools typically draw much startup and operating current.
It is also wise to install dedicated V circuits as heavy duty machinery will inevitably need this as a power requirement. Many types of machinery also have an option to be wired for V or V power. In my own workshop, I have at least 4 dedicated V circuits.
Each of these electrical circuits has a dedicated circuit breaker in the electrical panel, sub-panel or pony panel. It is also recommended to label each of the electrical outlets to determine which circuit they are on.
This will help eliminate overloading an individual circuit and breaker. Shop lighting should be set up on its own circuit breaker. This prevents the lighting from turning off in the event a tool triggers a circuit breaker. More dedicated circuits and circuit breakers also allow a problem to be isolated in the event a circuit breaker trips. Another consideration is the ease or difficulty in transporting materials into and out of the workshop.
Large doors or windows can facilitate the movement of lumber and finished goods into and out of the workshop. When designing a workshop, it is important to consider the dimensions of doors and windows of the workshop. Ventilation is also important, and sometimes a common household fan placed in a window of the shop or in the vicinity can satisfy the ventilation requirement. Safety considerations include a non-slip floor, adequate lighting, and room to manoeuvre around equipment.
Fluorescent lighting provides more light than incandescent lighting and is less expensive to operate. Some fixtures come with wires to plug into a receptacle, other fixtures need to be permanently wired.
Grounded receptacles are of primary importance and guard against shock. If the workshop is located in the basement, receptacles should be considered. GFCI receptacles sense small changes in current flow, similar to a short circuit, and disable the power instantly. Portable clip-on spot lamps can be used in proximity of the workbench or stationary machines, to serve as task lighting.
The photos show how banks of fluorescent lighting are used in a typical woodworking workshop, my current workshop. The banks can be switched on and off separately and the concentration of light creates a bright environment. The incidence of injuries is greatly reduced if the work are has large amounts of light.
You are also less apt to make mistakes since the work pieces are easily seen. When finishing a project, a bright, well-lit environment shows any surface flaws better. In my workshop design, the amount of windows was increased to bring in more ambient light. On bright days, I hardly ever turn on any of the fluorescent banks of light. Task lighting is important when doing hand work such as sawing and laying out dovetail joinery. I have a portable lamp attached to each of my four workbenches.
Storage is an essential requirement in a workshop. Without storage, tools would need to be left on workbenches and other work surfaces. Compartmentalizing and arranging your tools for quick access is a excellent strategy for a workshop design. Tool cabinets can be located along the surfaces of walls. Tool cabinets are typically designed with a low profile so they do not extend out into the workshop excessively.
Workshop cabinets also serve to keep dust away from metal tools. Dust on tools can stick to the metal if the air moisture in a workshop environment is high. Dust attracts moisture and causes rust and tarnishing to occur. For this reason, I keep most of my tools in enclosed cabinets.
Each tool has its own place within a cabinet to keep me from searching for the tool. The first photo shows one half of a matching pair of wall mounted cabinets for hand planes. These are not difficult to build and have mitered frame and panel doors with a hardboard panel. The cabinet itself has rabbet joints reinforced with biscuits. The shelves are dadoed into the sides of the cabinet.
The partitions are custom sized for the individual hand planes. Second photo shows a typical wall mounted cabinet for chisels and marking tools, the door has a shatterproof lexan polycarbonate panel. The cabinet is made of oak, the door is a mitered frame and panel construction reinforced with biscuits.
Third photo shows a wall-mounted plane rack. This particular plane rack is directly located above a workbench in order to quickly access the different hand planes available. Small wall-mounted cabinet designed to hold router bits, drill bits, sandpaper and assorted hardware.
Next or fourth photo shows another version of the wall mounted cabinet shown earlier, but for drill bits, router bits and layout tools. Construction is very similar to the previous wall cabinets. The front door is necessary to keep dust out of the cabinet. This cabinet is made from extra pine pieces lying around the workshop. A wall mounted pegboard is shown last. The pegboard is for clamps, small tools, measuring tools, levels and accessories.
Quick access is an important feature of the wall-mounted pegboard. A basement workshop is ideal because heat is already provided from the home through existing ducting; as opposed to a garage or detached workshop building. Headroom of the basement workshop should be at a minimum of 80 inches of vertical clearance which is beneath pipes and heating ducts. Verify that the basement is structurally sound, and there is not a leaking foundation in the home.
Any moisture problems must be solved before setting up a workshop. Moisture can create problems such as rust on machinery or lumber which will never be at the correct EMC.
Installing a dehumidifier can solve some moisture problems and keep it within an acceptable range. Power tools should always be used in a dry location. Damp floors greatly increase the risk of electric shock because damp concrete provides excellent electrical conduction from the tool right into the ground.
It was mentioned earlier to install GFCI receptacles which sense if there is a dangerous ground path created and trips a breaker within the receptacle. Windows can be enlarged and replaced to provide more light to the workshop, otherwise adequate artificial lighting will need to be installed in the workshop area. Most building codes mandate that a basement have secondary stairs to the upper floor. A stairwell with minimum steepness, and which is turned or split in the middle with a landing, is much safer than a steep, narrow, straight stairwell.
A door that allows access to the basement directly from outside is preferable but not necessary. Central heating will provide more than enough heat for the basement workshop, and additional heating ducts can be installed if necessary. Double-tube fluorescent lamps provide the best, brightest lighting, and are the most economical to operate continuously. A wood floor could be laid over the concrete floor to provide more comfort. Shown is an illustration of a wider, split stairwell.
Although this stairwell includes a turn, it is much safer than the straight, narrow type. The landing serves to break a fall and to rest heavier pieces as they are being brought in or removed from the basement workshop. I added the series of four photos to demonstrate how an area of a basement can be converted into a workshop space for woodworking.
This is vintage digital photography of one of my early workshops over 20 years ago. The workshop was enclosed with walls and a door to contain any dust generated and isolate it from the rest of the basement.
A window was added later to allow ambient light from the rest of the basement to enter the workshop area. The workbench is essentially a structurally rigid table to work on. It must be extremely reliable, both strong and rigid. The top should be very flat, and deep enough from front to back to accommodate your work. The overall height of the workbench should be emphasized, as it should be convenient for you to work on comfortably.
Workbenches can be purchased, but if you design and build one, it is best to follow an existing plan as many sensible details have already been incorporated into the design. Common features of a workbench are a tool recess at the rear of the top running lengthwise along the tabletop. The tool recess is to ensure that tools do not protrude into the workpiece above the level of the table top.
Other common features of the typical woodworking workbench are drawers or shelves under the work area, and two vises. Vises are very important because holding the workpiece firmly is essential to a good job. Often there is a vise face vise at the front of the bench and Machine Tools Workshop Layout another at the end of the bench tail vise or shoulder vise.
These vises work in conjunction with bench dogs to hold long or wide material firmly to the work surface. The bench dog, shown in the second photo, is basically a square or round, wood or metal peg which is inserted at predefined holes in the surface of the workbench. Despite all this, ripping sawing lumber along the grain and working large boards is usually awkward on the workbench. A pair of sawhorses is invaluable in the shop, on which you can rest the workpiece with plenty of overhang.
A sawhorse is also handy in cross-cutting sawing across the grain. Storage is another essential requirement of the workshop. Storage is used for hand tools, portable power tools, finishing materials, and small hardware.
The third photo illustrates a typical woodworking bench with a front vise and storage underneath in a workshop setting. The height of the workbench should be adjusted for your individual comfort, because it is most often used by yourself. Stand straight and rest the palms of your hands on a surface just high enough so that your elbows are slightly bent.
This is your proper upper work height, and the bench should measure this distance from the floor. Bench heights range from 30 to 36 inches high. Tools should be in close proximity to the bench, ideally the wall behind the bench. A workbench should be comfortable and highly functional. The workbench can be placed in the middle of the shop; you can then work on four sides of the bench. This arrangement leaves plenty of space for manoeuvring large workpieces around the bench. The workbench can also be placed against a wall or on the two sides of a corner.
This arrangement leaves less room to manoeuvre large workpieces, but it offers accessible wall space for storing tools. Brad Frost. Ship components with confidence Storybook makes it easy to keep track of edge cases and as a result you get tests for free.
Ensure consistent user experiences. Whenever you write a story you get a handy visual spec. Quickly browse stories to make sure your UI looks right.
Auto-detect code regressions. Get code snapshot tests out of the box with Storyshots, an official addon. Unit test components. Reuse stories in your unit tests to confirm nuanced functionality.
Catch UI changes down to the pixel every commit. Taurie Davis. Share and reuse everything Stop reinventing the wheel. Get a birds-eye view of your UI library to find components to reuse in your project. Find any component in your app. Storybook is a searchable, single source of truth for your UI components. Of course one organizes the tools on how they work and of course it evolves, but I am the type that wants a plan and not just to throw a , Plus, I have to have a starting point for my electrics, etc!
I know where most tools where go and how my flow works, I am not a hobbyist that purchased my first tools. What I dont know is the exact layout of the air, water and electric in relation to those or exactly where to place the outlets to satisfy an inspector I know every feet etc at 18", every 72"- 48" off floor, etc, some in the floor , but I must have it on paper in software. I can't just do that on the fly, the county wants plans and I want to play with it on paper computer screens and document my work flow in several configurations and be able to change them around easily, for that software is the way to go.
Heck, I am not sure where to put the bathroom or what side the Cyclone add on goes or where I want my spray booth! I do not set up a shop in real life trying to move around lb plus tools on the fly and then try to get in the electrics lighting and everything else after the fact. Anyone starting a brand new shop should a starting plan IMHO.
I just wanted a suggestion on software to get my ideas down where I could see them. So though I think many are trying to help, some of the things being suggested are not realistic. I think trying a variety of configurations in the software, finally choosing the best and then after a month or two of actual work tweaking it is the way to go. To just do everything with no plan is not for me at all.
I just decided to use Sketch Up and everything is in 3D.

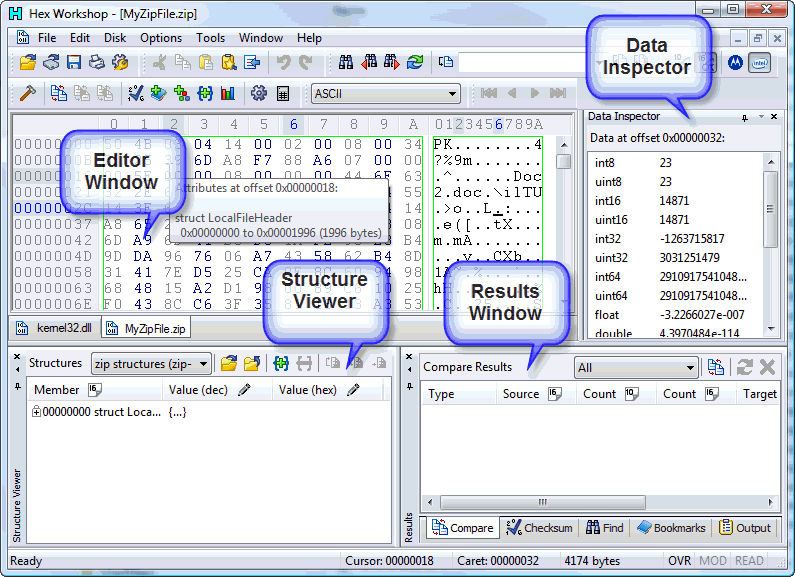

Free Woodworking Patterns Research Diy Workbench Plans Free 71 |
M3ayp
19.01.2021 at 15:34:34
xan001
19.01.2021 at 12:48:56
ZLOY_PAREN
19.01.2021 at 14:14:18
LesTaD
19.01.2021 at 20:39:58