Small Cabinet Lock Parts Names,Woodworking Plans Outdoor Table Number,Do It Yourself Wood Shutters - Good Point

There are two main styles of latch or bolt —a spring bolt and a deadbolt. It is designed to hold the bolt securely in the doorframe when the lock is engaged. The metal plate, which attaches to the frame of the door, is the strike plate. The purpose of the strike plate is to guide the bolt from the cylinder into the box of the frame and give added reinforcement to the locking mechanism.
Technology has brought vast improvements to home and commercial security. In particular, businesses are increasingly interested safeguarding their property by upgrading locks and installing security systems. Electronic locks are just one of the great new options on the market. Electronic locks are very different from traditional spring or deadbolt style locks. They rely on a series of magnets and small, electric-powered motors that are activated to open and close. Electronic locks are programmed to require the correct keypad combination , key fob , access card or biometric data , such as fingerprints, in order to unlock.
Smart Electronic Locks are electronic locks with the added capability of being controlled remotely through a smartphone application. A business owner can monitor traffic, restrict access through certain doors, lock doors and activate the security system without being anywhere near the building.
Usually, smart electronic locks also have a mechanical key cylinder to allow access with a traditional key. An experienced locksmith should also be able to answer any questions you have. Call us at or fill out our online request form to get in touch with Great Valley Lockshop.
This blog was originally published on June 10, and has since been modified and updated to reflect the most accurate information. Chris is a volunteer firefighter and "Life Member" for East Whiteland Township Volunteer Fire Company and a huge Nascar fan who loves to go camping and enjoys the outdoors. Chris Strauss frequently blogs for Read other articles written by Chris Strauss.
Discover what thousands of our customers already know: When you hire Great Valley Lockshop you can expect us to be prompt, passionate and genuinely enthusiastic about your project! When a kitchen sink needs to be exactly centered under a window, for example, a 2" or 3" offset can make a very big difference. Custom cabinets easily accommodate such differences and offer more flexibility in cabinet placement. They also allow you to add compatible new cabinets to an existing set. H ere are the names of the parts of a typical kitchen or bath cabinet.
These are the common names here in the Midwest. Almost every one of these has at least one other common name, and there are lots of regional and local variations.
A "panel" to one cabinetmaker may be a "pane" to another. But these, we think, are the most widely-used terms, understood by most cabinet folk even if they usually use another term. In cabinets with bottom drawers or slide-outs, it is never seen but it is very important to the structural integrity of the cabinet. A weak bottom panel allows the cabinet to twist out of square during handling and installation.
You will find them in base cabinets, more rarely in wall and full-height cabinets that have a solid top and bottom panel. They are primary structural elements and need to be very strong. This is one area where cabinetmakers rarely skimp. Most are adjustable. European style cabinets are built without a separate face frame See"Cabinet Case Basics" below. Because it is constantly being opened and closed, it needs to be tough with strong joints.
The strong drawer joints are dovetail, dowel-pegged and slip joints. All of these will stand up to year after year of use. This permits the part you see to be adjusted independently of the drawer itself so it aligns correctly with the other elements of the cabinet. In less expensive drawers, the front of the drawer box see above is also the front you see.
There is no separate false front. Most of what you can actually see of a cabinet is its doors. They determine the style of the cabinet. These have a number of advantages, the most useful is that they can be adjusted to precisely align the door. Older visible hinges require more skill to install but on heritage cabinets these are often the best choice. Better cabinets include separate toe kick platforms that span several cabinets. These are easier to level so the cabinets that sit on them are also precisely level.
For more information on how cabinets are made, see Comparative Cabinet Construction. The trick to buying custom cabinets at an affordable price is not to go overboard with the customization. Most cabinet shops that have been in business a few years have a standard catalog of hundreds, if not thousands of cabinet door styles.
Sticking with these standard doors usually reduces the cost of cabinets. If you truly have your heart set on an exclusive custom design, your local shop can make it but expect to pay a premium. Costs for custom cabinets range from low mid-range to "holy cow — you must be kidding", depending on the material, detail, accessories, and degree of hand-work involved.
But the myth that custom cabinets are always high-cost items is just that — a myth. Many local cabinet shops are very price-competitive with large factory manufacturers because of their lower overhead and much-reduced shipping expense. While many large cabinet factories offer what they term "semi-custom" cabinets, their product is actually a semi-stock cabinet — their usual product made in a custom size.
The true semi-custom cabinet is typically crafted by a local or regional cabinet shop that farms out some of its work to a factory that specializes in components. For example, the local maker may sub-contract the cabinet boxes to a specialist in "cases" the technical cabinetmaking term for the cabinet box , the doors to another specialist in cabinet doors, drawers to yet a third specialist, and so on. What the local shop then does is assemble these components into a cabinet and apply the finish specified by the customer.
It is often possible to get components from a large-scale component maker for less than the local shop pays for raw wood.
The advantage to the customer is "custom" cabinets at a substantially reduced cost. The disadvantage is that the materials, designs, and details, while often extensive, are still somewhat limited by what the component makers can provide as opposed to a true custom cabinet that has no such limitations. Most custom cabinetmakers use out-sourced components to some extent but almost all still retain the ability to make the components in-house if necessary to achieve that special look.
In many instances, true custom cabinets are combined with semi-custom cabinets in the same kitchen to keep the cost down while still getting the look and feel of custom work. If a cabinet is merely a custom size of a factory's stock cabinets, it is semi-stock, not, as the factories usually advertise "semi-custom". These can be an economical way to round out a factory stock kitchen.
The components are factory-made but manufactured to fit a specific kitchen. More economical stock cabinet sizes are used to fill most of the space, while a few cabinets are custom sized to fill in the rest of the space without filler strips. In most cases, all components are factory-built, though some are customized. In some instances, the installer builds some details or components to finish out the cabinetry.
Factory Stock Cabinets Factory stock cabinets consist of mix-and-match components starting at 9" in width and graduating in 3" increments to about 60". Because the sizes and details are standardized, and the cabinets built on an assembly-line, stock cabinets are often very affordable. And, because they are made in fixed sizes, a minimally trained employee with a computer program can place the cabinets to form a kitchen.
This means they can be sold in great quantities by lumber yards, and home stores without the expense of a trained and experienced kitchen designer. Fine Homebuilding magazine is the almost universally recognized "bible" of quality building and remodeling in the U. The editors have come up with typical cabinet costs in the U. The cost is stated as a linear foot average and includes both upper and base cabinets, installed unless otherwise noted but does not include countertops.
Factory stock cabinets are sold everywhere, from the finest cabinet design studios to lumber yards and home centers. Prices vary with the type of material and construction methods used, and the number, type, and quality of storage features. Drawer boxes, for example, cost more than the same cabinet fitted with doors and shelves. Drawers are more costly to build. Keep in mind that these are typical prices for typical homes.
The good news for homeowners is that competition at this level is truly fierce. What's more, dealers and home centers make shopping easier by providing display kitchens in a variety of styles and prices. These side-by-side comparisons help focus the selection process. It was not very long ago that RTA cabinets were considered, and in fact were, the very bottom of the heap. Particleboard with very low-quality hardware, the low price for these cabinets was usually the result of very low-quality.
Things may be changing. While there are still dozens if not hundreds of manufacturers of low-quality RTA cabinets, we have started seeing some cabinets coming out of Asia that are the quality-equal of a typical factory stock cabinet, and for quite a bit less cost.
The lower cost is certainly due to the much lower labor costs in Asia but also because they are shipped broken-down in flat-packs, which greatly reduces shipping costs. Cabinets, shelving, furniture all claiming to have a melamine finish.
What is this stuff and where did it come from? Chemically, it's a resin produced from urea and formaldehyde that results in a low-temperature plastic that is very durable and stain resistant. Today it is used to manufacture scads of products from white erasable boards to countertops; flooring to paint to chemical cleansers such as Magic Eraser.
Melamine dishware was first produced for use in hospitals, mess halls, and restaurants during World War II. The dishware was very "institutional" — possibly the ugliest brown ever seen — but designed to be easily stacked and not easily broken.
The dishware was a resounding success. It remained in use by the military at least until the s. Melamine was a new plastic in the s. Unlike other plastics of the era, it could be given virtually almost any color under the sun, and these colors could be mottled and mixed.
Lightweight and strong, this new plastic was often used in automotive parts of the time. However, melamine really made its mark in the dinnerware world. As soon as World War II was over, manufacturers took a new look at the institutional plastic.
One such company, The American Cyanamid Corporation , produced melamine dishes with their own special material blend called "Melmac," which soon entered the vernacular as the common household name for melamine dishware. The Branchell Manufacturing Company of St. Louis, also produced several household lines including Royale and Color-Flyte. Nor was melamine a stranger to high fashion.
Housewares designer Russel Wright produced his very own high-end lines. His melamine finishes were unique: featuring layered colors to create a mottled effect. Some of the recognized names he produced were black velvet, sea mist, lemon ice, and copper penny — all prized collectibles today.
Young post-war parents loved it. It was virtually kid-proof. It could be dropped, thrown, stabbed and molested in just about any manner a kid could dream up without serious damage. So, just how popular was melamine dishware? The numbers say it all You can almost guarantee that your mother and grandmother both had at least one set of Melmac.
Two reasons. First, inexpensive and very beautiful ceramic dishes from China began flooding into the market in the mids, much of it nearly unbrekable "stoneware". Priced to compete with melamine, many homeowners switched back to porcelain and china. Melamine manufacturers tried to keep up with the new imports by making their dishware less costly. But the only way to do that was to reduce quality.
Melamine dishes became thinner, less durable, lightweight, cheaper, and more "plastiky". Second, Amana invented the microwave. The rise of microwave cooking was the end of melamine dishware in the American home.
But it is still going strong elsewhere, particularly in the Orient where manufacturers are reaching new heights in color and decoration. So, where does melamine stand today? It's rarely used in dishware in America but commonly found as the coating for the cabinets that dishware is stored in and the countertops they sit on.
Formica is mar-resistant, heat-tolerant although it will scorch at high heat , easy to clean and durable. Best of all, compared to other laminate finishes, it's cheap. And ubiquitous — even very-high-end cabinets boast interiors finished in melamine. Quite a journey from ugly brown Army dishware. As for vintage melamine dishware — if you have some in good shape, hold on to it. It is becoming a collectible.
Complete sets of rare patterns and colors are selling at astounding prices, and even everyday pieces from name manufacturers are attracting collector attention. Who would'a guessed? The trade-off is that they must be assembled, which takes an hour or more per cabinet and they are not as strong as factory-built cabinets.
The mechanical fasteners used to hold RTA cabinets together cannot equal the durability of well-joined cabinets put together with strong mechanical joints and modern glues. The additional labor involved in assembling these cabinets usually offsets any savings resulting from the lower cost of RTA cabinets. But, if you intend to assemble and install them yourself, and you know how to install cabinets, then these may be a viable, low cost, option for your new kitchen. If you intend to assemble the units yourself, there are a few considerations to take into account.
Cabinet cases are constructed on one or two basic formats: framed American and frameless European. In American-format cabinets, the front edge of the cabinet box is joined to a face frame usually made from hardwood. When fitting to an irregular wall, the frame around the perimeter can be shaved to fit and the frame makes it possible to use affordable, low-quality materials for cabinet sides.
It slightly narrows opening sizes for doors and drawers — but except in very narrow cabinets, this is not usually a hindrance. Generally, framed cases are considered stronger and more resistant to deformation. The normal factory door type is half-overlay, although all styles are available, some at an extra cost. Go to Cabinet Basics, Part 2: Door and Door Construction for Small Cabinet Lock Parts Size an explanation of door overlay, then click your browser's [back] button to return Small Cabinet Lock Parts 13 here.
European-format cabinets have no face frame. The design is particularly well suited to mass production, and was, in fact, developed after WWII with the express aim of quickly manufacturing a lot of quality casework from panel stock to rebuild war-torn European cities.
Cases are made up of panels finished on both sides and edged with a simple laminate banding or narrow strip of veneer. Doors on frameless cabinets usually conceal most if not all of the cabinet box with only a slight reveal between them, offering an unbroken appearance, and making it unnecessary to be real fussy about the finish of the front edge of the cabinet.
Frameless cabinets are found at all price ranges but seem to cluster at both ends of the price spectrum. Inexpensive "ready-to-assemble" cabinets composed of particleboard and veneer are usually frameless. But so are many of the top-line designer studio cabinets — especially from European studios. Because they tend to be more common in inexpensive cabinets, the frameless format has gotten a bad rap for durability. The problem is not with the format, however, but with the construction of the cabinets.
Often the cabinet sides are veneered in nothing more than paper, printed to look sort of like wood grain. Commonly, front edges are also banded in paper, which does not withstand much abuse. But, frameless cabinets made correctly are very durable.
We veneer the insides in melamine laminate. It provides a very sanitary, washable surface. On the outside, where the ends are exposed, we use actual wood veneer, applied at a factory under great pressure.
It will not delaminate and will stand up to abuse much better than paper. The hardwood protects the front edge from damage just as well as a hardwood frame, while still giving the cabinet a more contemporary, frameless appearance. Whether framed or frameless, most manufactured cabinets and, indeed, most custom work these days use the European standard "32mm mounting system.
European hinges, drawer slides, shelf supports, and other cabinet hardware are designed or "indexed" to exactly fit these holes. The system has had a pronounced effect on how cabinets are made, the most significant of which is drawer and accessory sizing. Drawers must be made in increments of 32mm to fit correctly. So, typically factory-made drawers are now designed in multiples of 32mm rather than in inches with adjustments for the small gap between drawers, so they don't rub on each other.
A lot of the hype surrounding kitchen and bath cabinets centers around particleboard and medium density fiberboard. Both are engineered composite wood panels. These are made by combining cellulose filler material and a binder — typically a resin to form a sheet or panel. Both are usually considered "green" materials since they are made out of what would otherwise be trash.
The filler material in both is the leftovers from wood milling: sawdust, chips, bark; agricultural waste such as bagasse sugar cane stalks and corn stalks and post-consumer waste that otherwise would end up in the landfill.
Anything containing cellulose fibers will do. To make particleboard, these are all ground into small particles the "particle" in particle board. To make MDF, they are steam heated until they literally fall apart into their constituent cellulose fibers the "fiber" in fiber board. Both materials are then mixed with a resin and bonded into sheets under pressure and heat. MDF is made under much higher pressure than particleboard, is denser, heavier and less likely to contain voids.
Each of the primary grades can be divided into sub-grades. M grade, for example, comes in M1, M2, and M3, representing variations in density. Particleboard got a bad rap when it became the preferred material for inexpensive ready-to-assemble furniture, and it has never lived it down.
It is indeed not a good choice for furniture because furniture gets moved around and is exposed to bashing and dinging in the process. Kitchen cabinets are not. Once a cabinet is installed, you cannot get to the case except from the inside.
The back and sides are usually against the wall or another cabinet. The bottom of a base cabinet is on the floor, its top is covered by a countertop.
The front is covered by a hardwood frame and the door. So, a case does not need to be especially ding- and bash-resistant, it only needs to be moisture resistant and strong enough to hold the weight of the stuff you put in the cabinet. Laminated particleboard meets these criteria easily. So, it's generally is not the particleboard itself that is the issue with lower-end cabinets, it's the fact that a manufacturer that selects particleboard because of its lower cost is also most likely to use the least expensive hardware and construction techniques, including bottom-of-the-line drawer glides and hinges, and lots of staples and hot glue rather than stronger pocket screws, biscuits or mortises.
It's a good basic rule of quality cabinet selection to avoid all staples, period. Particleboard requires special fasteners — regular screws don't work well, and many makers of economy cabinets do not use the necessary special hardware. If a particleboard cabinet is constructed using the proper fasteners, with top quality glides and hinges, there is no reason it could not give excellent service for year and years.
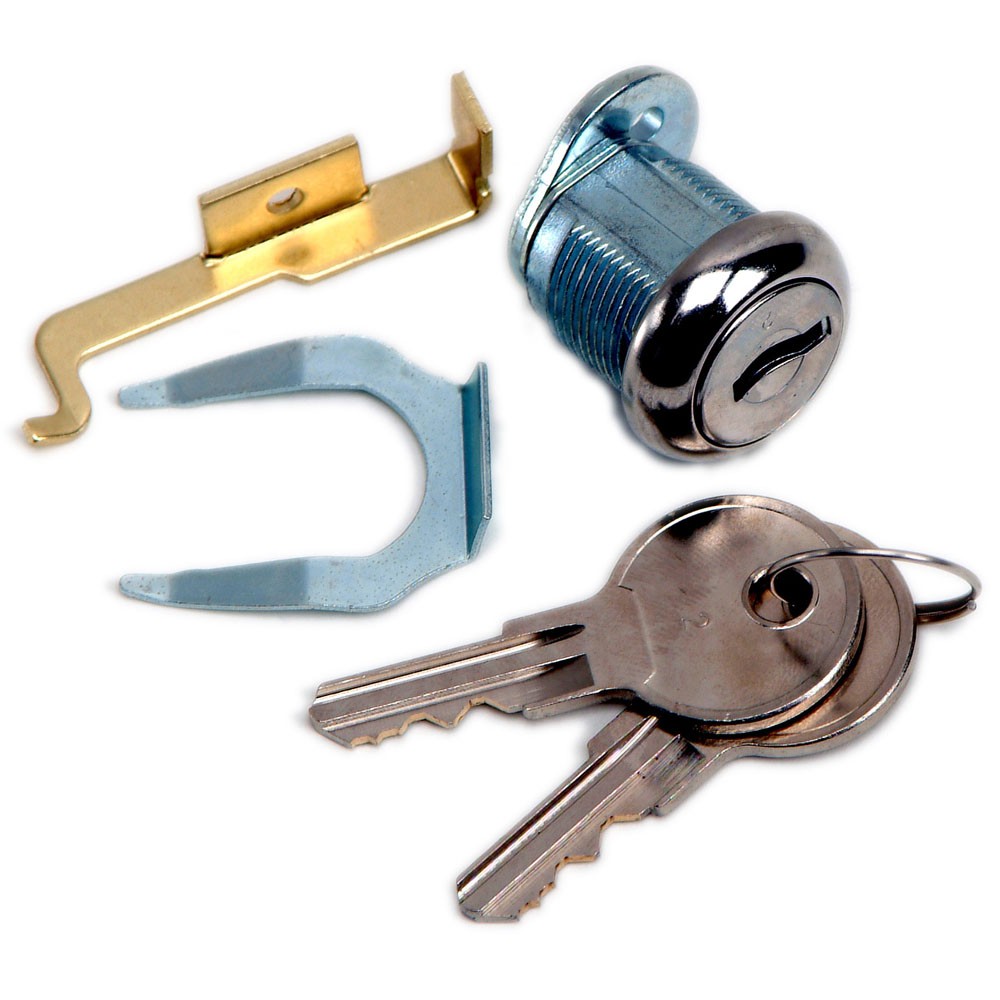
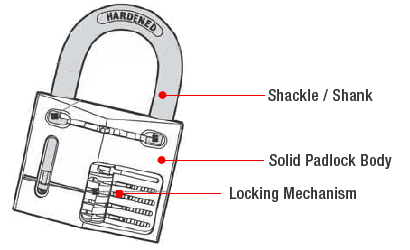

Makita 23ga Pin Nailer Object Best Rap Playlist Names Zip |
666_SaTaNa_666
12.02.2021 at 19:24:36
ASKA_SURGUN
12.02.2021 at 18:34:57
LOREAL_GOZELI
12.02.2021 at 14:50:33