Lathe Machine Tools Pdf,Bench Wood Lathe Machine 05,Corner Clamps For Wood Systems,Hartford Miter Clamps 62 Iso - You Shoud Know

Having this machine the main advantage is that a single operator can handle machines more than 4 to 5 machines at a time. Some examples of special lathes include Vertical lathes, Wheel lathes, T-lathe, Multi Spindle lathes, Production lathes, Duplicate or tracer lathes , etc. Wheel lathe is used for machining of journals and rail rods. It is also used for turning the threads on locomotive wheels. The axis of the lathe bed is at right angles to the axis of the headstock spindle in the form of a T.
This is widely used as a lathe in the present time because of its fast and accurate working. It is one of the most advanced types. It uses computer programs to control the machine tool. Once the program is fed into the computer as per the program it starts operation with very high speed and accuracy. Even do preplanned programmed machine is there in which once code is set for the various operations it can starts operation without changing code in the next time.
These types of lathes are also used for mass production like capstan and turret but there is no programmed fed system. Before continuing any operation in lathe we have to load the job and center it on the head-stock spindle. In lathe operations , the headstock spindle holds the job and it rotates with the same speed as the spindle.
The carriage holding the tool on the tool post, also the carriage gives the tool post moves longitudinally or crosswise direction to give the desired feed on the job. These two motions longitudinally and crosswise helps to remove the chips of the metal and giving the proper shape of the job.
It is tough to mentioned which operations are not performed in a lathe machine tool, though we discuss some important lathe operations in detail. We use this operation for producing a conical hole in the face of the job to make the bearing support of the lathe center when the job is to hold between two centers. Head-stock and Tail-stock.
Facing operation is for making the ends of the job to produce a smooth flat surface with the axis of operation or a certain length of a job. The operation by which we remove the excess material from the workpiece to produce a cone-shaped or a cylindrical surface. This operation is done to produce a cylindrical surface by removing excess material from the workpiece. A shoulder turning is called which has a different diameter to form a step from one diameter to another.
It is a process of removal of excess material from the workpiece in minimum time by applying a high rate of feed and heavy depth of cut. The finish turning operation needs high cutting speed, minimum feed and a very small depth of cut to generate the smooth surface.
In finish turning the depth of cut is around 0. A taper is defined as a uniform decrease or increase in the diameter of a workpiece along with its length. The operation by which a conical surface of the gradual reduction in diameter from a cylindrical workpiece is produced is called taper turning. Any increase in the length of taper will require the use of a wider cutting edge which may destroy the workpiece due to the vibration and spoil the workpiece. Job is held between the centers.
The length of the workpiece will be long enough. An only a small taper on a long job is done by this process. Chamfering is used for beveling the end of a job to remove burrs, to look better, to make a passage of the nut into the bolt.
Knurling tool is held rigidly on the tool post and pressed against the rotating job so that leaving the exact facsimile of the tool on the surface of the job. It is the operation that is used to produce a helical groove on a cylindrical or conical surface by feeding the tool longitudinally when the job revolved between the two centers. The tool should be set exactly to the height of the centerline of the job and at 90 degrees to the job. In this operation, the job is rotated at the turning speed on the lathe axis and the drilling tool fitted on the tail-stock spindle.
And the tail-stock is moved towards the job by hand feed. In this operation, we can enlarge the diameter of the existing hole on a job by turning inside with some farm tool known as a boring tool.
Reaming is the operation for sizing or finishing a drilled hole to the required size by a tool called reamer. In this operation, the job of this sheet metal is held between the former and the tail-stock center rotates at high speed with the former. So the job is taken exactly the shape of the former. In this operation a bar type job is held on a chuck, rotates at turning speed, a parting off tool is fed into the job slowly until the tool reaches the center of the job.
I also wrote an article on Milling Machine: Definition, Parts, Types, Operations and drilling machine you may check that too. Hey, now I want to hear from you. I hope you understand the definition, parts, types, operations, and specifications of a lathe machine. If you have any queries or doubts about the lathe machine tool, you can ask me in the comment section and also you can join our facebook group.
I will love to hear from you and glad to help you. So no top rake in necessary in a facing tool. The figure shows H. The length of the tool is , ,, and mm and the nose radius varies from 0. Grooving tool is similar to a parting-off tool illustrated in the figure. An ordinary lathe turning tool may sever the purpose where a copying attachment is used to reproduce the form of a template. Flat forming tools are made of two types:. These tools have their cutting edges ground to the shape of the groove, undercut, or thread to be cut.
Flat dovetail forming tools have a wider cutting edge corresponding to the shape desired. Dovetail end of the tool is fitted in a special tool holder.
These tools are preferred in production work as a very long cutting surface can be used resulting in longer tool life. The centre of the tool is set slightly above the centre line of the work to provide an effective front clearance angle on the tool. The tool will rub against the work if the centres are of the same height. Regrinding is done by grinding the flat only. A boring tool is similar to a left-hand external turning tool so far its cutting edge is concerned.
The tool may be a bit type inserted in a boring bar or holder, or forged type having a tool shank. The figure shows an H. A boring bar is made of mild steel with slots or holes cut into it to accommodate the tool bit which is locked by an Allen screw. The amount of projection of the cutting edge of the tool from the centre of the bar determines the finished hole diameter of the work.
The bit is generally inserted at right angles to the centre line of the bar for boring a continuous hole passing from one end to the other end.
The bit is set at a single to the axis projecting beyond the end of the bar for boring a blind hole. The counterboring operation can be performed by an ordinary boring tool. The tool cutting edge is so ground that it can leave a shoulder after turning. A counterbore having multiple cutting edges is commonly used. Undercutting or grooving tool has a point and form of the cutting edge exactly similar to the form of the required groove. Clearance angle is given at all the sides of the tool.
For the recessing groove cutting edge, the longitudinal feed is employed. The front clearance angle depends upon the bore of the work. A parting off tool is normally forged and used as bits for cemented carbide tipped tools. Parting off tool is made as narrow as possible to remove the minimum of metal. The width of the cutting edge range from 3 to 12 mm only. The length of the cutting tool which inserts into the work should be slightly longer than the radius of the bar stock being machined.
As the tool penetrates deep into the work, clearance is provided all around the tool cutting edge to prevent it from rubbing against the work surface. As the tool is purely ended cutting it has no side rake slight back rake is provided on the tool to promote an easy flow of the ships. A right-hand tool is shown in the figure. Is that which is fed from lathe bed, i.
A right-hand tool is formed on its left-hand end when viewed from the top with its nose pointing away from the operator. The left-hand tool is shown in the figure. Is that which is fed from the Left to the right-hand end of the lathe bed, i. The left-hand tool is used for left-hand thread cutting operation or turning operation which leaves a shoulder on the right-hand end of the workpiece. A mandrel is used during machining of thin hollow cylindrical jobs without any bending of the component.
It is used for supporting long cylindrical jobs during machining to avoid the bending or deflection of the workpiece.
To avoid the bending of the workpiece, due to the cutting forces acting by the tool, exactly opposite to the tool, support is provided and it is moving along with the tool called as follower rest.
By changing the angle of the tool, various lathe operations can be performed like turning, facing, taper turning, step turning, etc. The Three Jaw chuck is used to hold circular components whereas the Four jaw chuck is used to hold Rectangular or Square cross-section components. Sometimes its quite hard to use conventional machining for various types of operation, as these machines are built for a particular operation.
So to overcome this we need to have some devices which extend the limit of operation in Conventional Machines like Lathe. Attachments are not a mandatory element of a Machine, it is only used for performing specific operations like Milling in Lathe, Taper turning, Grinding, etc. These attachments are used to make helical grooves, flat surfaces, deep screw threads, worms, helical grooves, keyway cutting, Tee Slot cutting, thread milling, etc.
The milling attachment is generally fixed in the place of the Compound rest of the lathe machine. It generally consists of a milling head and a spindle to hold the milling cutter which is mounted on the milling attachment. It consists of a motor that can act as a driving mechanism in the milling machine. The tapered bar of the lathe machine can be set with different angles to the spindle axis.
A link connects sliding block to cross slide where the sliding block is carried by the guide bar during taper turning operation. Through 90 degrees, the top slide is swung to lie at right angles w.

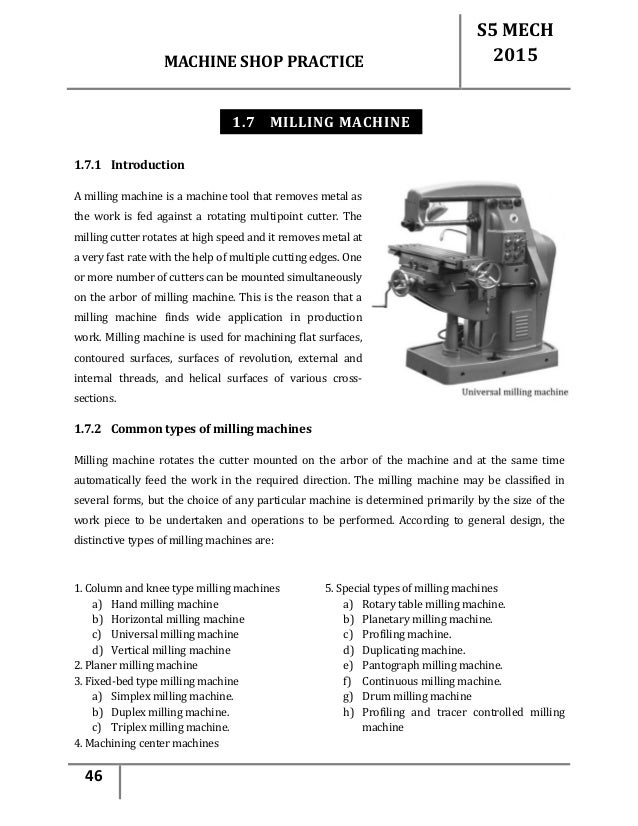

Craftsman 12 Band Saw Blade Size Guide Free Woodworking Plans Uk 10 Hardwood Floor Renewal Products Github |
O1O
25.10.2020 at 14:54:22
RENKA
25.10.2020 at 20:15:45