Flush Cut Router Bit Harbor Freight Jacket,Wood Workshop Workbench Online,Best Soft Close Slides Youtube,Marking Knife Price Chart - And More

When complete, the game should be basically playable in terms of playfield and ramp shots, and if the game plays okay with foam core, it will play even better in plastic and metal. It is a material that is readily available in multiple thicknesses and footprint sizes, often obtainable for free since it's such a highly recycled material.
It can be bent at angles and remain stiff in fluted versions, or bent in a curve by squishing the flutes down, very similarly to sheet metal. Since cardboard has no foam inside, it can often be stiffer and closer to a harder material like plastic. It is as easily cut with an x-acto blade or scissors.
Sourced from a tutorial by Josh Kugler [1]. Before proceeding with any cutting, a completed playfield drawing is needed, to be used as a template. For details on that portion of the process, visit the Design section of the wiki.
One tip that will help later is to add centering lines to all the drilled insert circles to aid in proper placement. Once complete, take the file to a FedexOffice or similar Printing House and have it printed full size.
Use 3M Spray adhesive to glue the print to your playfield surface. This print acts as your drilling and cutting template. Use two Forstner bits for each insert. Since the Forstner bit has a centering point there is a natural centering hole for the second bit, making it easier to get it lined up right. The cleanest technique is to drill just short of going through, and then complete the hole from the other side using a standard cordless drill. For creating a non-circular insert, use a router with a template and Bushing guide - a router bit with a small roller bearing on it runs along your guide, while the cutting head runs in the playfield to cut the hole to the size of the template.
Creating the template is the hard part, but once you have that, it is relatively easy to route multiple holes for the inserts. This is a three step process similar to the circular inserts. As with the circular inserts, first create the wider opening. This is done by clamping the template to the playfield and then routing the wider opening using the bearing bit.
Drill a couple of holes in the center of the insert so there is less to route. This is also helpful when doing the second step, of cutting out the inner opening, that is slightly smaller then the insert opening, since the router bit can start in one of the holes and not have to be plunged into the wood. This second routing can be done without a template, since the insert opening itself can act as the template. Some of the considerations when designing or building a pinball cabinet include:.
If building a Williams style standard cabinet, VirtuaPin offers a Ultimate Cab-Builder's Kit that has all the cabinet-specific parts in one handy kit.
When cutting your cabinet for the coin door, keep in mind it is installed with four bolts centered on the bottom, sides and top, and that the top hole goes through the lockdown bracket. So both need to line up. Once the physical playfield is constructed, wiring it all together and adding a way to control the devices will be required. There are three basic options - use existing pinball boards, build custom control boards or purchase off-the-shelf units.
A popular option is using boards from existing machines and replacing the main controller. Another well documented system is the original Bally system. Most off-the-shelf systems require an external PC with USB to provide the signals to control the solenoids and lamps. Currently these small ARM-based boards are the best candidates as they are more powerful than the Raspberry Pi or Arduino boards:.
For example, decoding the Williams part number AL has three parts - the prefix AL means the coil has base wire lugs on the left and middle of the coil's base, while 23 is 23 gauge wire and is the number of turns of wire.
The more turns, the weaker the coil. For more details on coils, check out the Pinball Medic coil chart. It is recommended to get at least a 3A supply for coils. The quality, especially from China, is not always guaranteed. Be sure to choose one with a case that has adequate venting to prevent shorts if any metal items are dropped on the circuitry. Power supplies with fans are recommended. They typically won't turn on unless they get hot enough Coils pulling excessive current, hot ambient temperature.
Sometimes coils may pull more amps than the power supply can provide, so wiring in resistors and capacitors to buffer energy may be necessary so the power supply doesn't reset. Computer power supplies are fine for CPU and some lighting, but won't provide enough current for solenoids.
If using a standard PC as the CPU for the machine, there is a useful board for controlling PC power supplies from the external high-current supply. Using a modern switcher with coils means using a Capacitor Board between the supply and any solenoids to provide coils that sudden onrush of current.
Some options include:. LEDs identify the presence of each of the 4 DC voltages. Most pinball machines have wire harnesses of some type. As high-current devices, solenoids typically need a minimum of 18AWG wire. Wiring for lighting and switches can be much thinner since it's pulling less current, particularly if using LEDs, so AWG wiring is acceptable for low-current uses. Because prototyping or one-off projects don't have pre-determined wire lengths and quantities, how wire is routed will change many times before the game is complete.
It is highly recommended to use tie mount bases with adhesive versus clips that are permanently screwed into the playfield. That way they can be moved around as needed. It is also recommended to use re-usable tie-wraps, which allow repeated opening and closing as needed. Once the final wiring layout is complete, paper templates of the playfield layout on thick cardboard or wood paneling can be used to make a Wiring Pinboard , similar to the boards that the manufacturers use to make their Wiring Harnesses.
Place nails in appropriate spots and run wires as needed, with tie-wraps. To aid in troubleshooting and wire layout, pinball companies use color-coded wire, where it has one color as the main jacket and a second color as a smaller stripe, allowing for many color combinations. For instance, Williams used yellow and white wire for lamps. Getting a full stock color-coded wire can be very expensive, but the folks at Mission Pinball came up with a cheaper alternative method of properly color-coding wire using cheap PVC piping.
Start with purchasing single-color wire in 50' - ' spools. Get 18 and 20AWG spools for each type of wiring. The more base colors to start, the better. Next, get some oil-based markers, which can be found at local hobby stores. One notable brand is Sharpie, and they should be labeled specifically as oil-based paint markers - water-based will scratch or wipe off easily. They will be more expensive but are the only type that work correctly. Although Mission used a wood block to hold the markers, using a PVC T joint and drilling a hole through it in the center allows the placement of the paint marker in the T portion of the joint and pressing down on the wire as it passes through works very well.
Where color-coding is particularly important is in Switch and Lamp Matrix layouts. Plan ahead and design your color scheme before starting the construction of the game in a spreadsheet. Below is an example of a color layout for a custom game.
This document can be referenced during construction to make sure the right wire is going to the right switch, lamp or coil, avoiding troublesome issues later during the testing phase. Numeric or Alphanumeric score displays are sometimes chosen even today because of the ease of programming - they display simple scores or lines of text only, so no complicated graphics need to be designed or coded.
That means more time to concentrate on gameplay versus interfacing with the player. The first commercial solid-state displays in common usage were Gas Plasma displays. They use high voltage to cause a noble gas like neon to glow. Shaping the conductive layers into digits allows the display of multiple numbers or letters. These types of displays are not only dangerous, due to the high voltages required, they are prone to burn-out or out-gassing, and have been obsolete for many years. Unless re-theming an older game and wanting to re-use existing parts, or trying to maintain a retro look, it is suggested to use LED replacements.
The pinball after-market has produced a number of excellent plug-and-play LED display replacements. They work on the same principle as the segment display except they use round pixels in a grid pattern - or matrix - to display game information. The complexity with these displays is that the programmer must construct numbers or letters in a graphic format and then push that data to the display. Rather than program "display ,", they must use bitmap fonts and determine screen placement. However, many programming frameworks currently available offer this functionality built in and are an excellent place to start learning about game graphics.
Full color with high resolution, the results can be very attractive. However, at this level a game designer essentially becomes a videogame designer. A pinball maker has to wear many hats but it is the rare individual who can do both construction and handle graphics duties.
There is some discussion of the technical side of graphical displays on the pinballcontrollers Forum. Pinball lighting comes in two varieties - incandescent and LED. Bayonet is preferred since the bulb is more likely not to wiggle itself out from vibration during play and transport. While pinball started out with incandescent bulbs, most are moving towards LED for many reasons:.
One drawback of LED's are that they don't have a ramp-up of brightness like incandescent bulbs, and sometimes they can be bright enough to hurt the eyes. The ramp-up effect can be emulated in software if the lamp controller has enough brightness levels, and diffusion-style bulbs help the brightness issue.
They are best used as General Illumination. Modern Stern games going forward use a Surface Mount LED board that are driven directly which eliminates the need for sockets altogether. The drawback to these are that the boards are directly soldered, so if there are issues, they can't be easily replaced. However, the long life of LEDs makes it unlikely for them to burn out at the rate incandescent lamps do. Many vendors provide custom lighting solutions which might not fit in a traditional socket as above or have specific pinball specific uses.
These PCBs plug into the socket typically found in most modern pop bumper assemblies. Pinball Mods offers a Star Rollover LED which shines 4 LEDs from the underside of a star rollover and has a hole in the center to allow the switch actuator to function properly on the leaf switch.
Pinball Mods offers the Flipper Button Mod which displays a rotating 12 LED pattern behind early solid state Flipper buttons for project using the older style flipper buttons.
Many hobbyists plan on producing games with game-specific features that aren't included in other machines, such as ramps or ball control devices, and thus will have to design and construct mechanisms from scratch. This generally involves metalworking, welding and other more advanced skills, but are not beyond the garage hobbyist.
While using a laser cutter would be ideal, it is possible to produce plastics with basic hand tools. This can be cut fairly easily with strong scissors or an x-acto if used carefully , and like acrylic it can be flame polished.
To create artwork, the best method is to print it on photo paper , and then use a spray adhesive to attach it to the bottom of the plastic. These products dry clear and will not yellow. First, trace the shape to be cut on the thin blue film on top of the plastic.
Remove the film from the bottom where art is being applied. The artwork should be just slightly bigger than the plastic to ensure there are no gaps when trimmed. Make sure to spray in light, even coats on the backside of the plastic. Let it get tacky for seconds, then move the printed art art side up over, and turn the plastic over and apply the plastic onto the paper - this will make it easier to line it up. Once the adhesive has dried, the holes can be drilled starting with a small bit, and working up to the hole size needed.
Trim off the excess paper by using the plastic as a guide. Trim slow and carefully as to not dig into the plastic with the knife. The white paper acts as a nice diffuser to spread the light out, just like the white ink layer on screenprinted plastics.
From Wolfmarsh's Pinside tutorial. FDM is where a thermoplastic filament is slightly melted, extruded through a small nozzle, and deposited in layers to build up the object. Most home printers use this method. Here is an image that gives the general idea. One is the Extruder , two is the deposited Layers , and three is the Build platform.
With SLS , a layer of powder is deposited on the build surface, then a laser melts specific areas together. The build surface lowers a fraction of a millimeter, and more powder is deposited. Repeat until the object is built. Here are a couple short videos that shows how SLS works:. Most home printers will print using plastic filament and FDM. Services like Shapeways can afford higher end printers that offer higher resolution with SLS.
For most of what a garage builder will do, FDM and home printing will cover it. If a full color print or some very fine details are needed, like screw threads, the part can be ordered from Shapeways. If planning to purchase a home printer, it is recommended to read the Make Guide to 3D printers.
There are many clones coming out now that patents have run out. If you look at the flashforge, there are clones that are as cheap as half cost. Monoprice has a few options. Load Post 1. Comment 0 Photos 2 Share. Load Post 2. Comment 0 Photos 10 Share. Image Dynamics OEM 6. Seas CA18rnx 7 inch midbass drivers. Brand New In Box. Purchased from Madisound.
Load Post 3. Comment 0 Photos 5 Share. One of the advantages of DIY interconnects is you can make custom lengths. That way you dont need to buy extra feet and bundle it up like the store bought cables.
Since the set I am making is for a stereo application this set will run from my head unit to the amp on the back wall of my truck , I only needed 2 sets of RCA ends, one Red and Black set for each end of the cable. I fished the cables through the speaker pants. Once that was complete I stripped off the black plastic coating to expose the 3 wires, being extra careful to NOT break the plastic coating of the 2 inside wires. The 3rd wire is already bare, as this is the shielding wire. I inserted the RCA end and then slipped in a piece of heatshrink tubing that will protect the soldered connections.
I inserted the Red wire into the center connection. Everything is soldered and the the clamp is crimped down for securing the cable.
Once this is done I slid the heatshrink over the connections and then heated to shrink. All that is left is to screw the base to the RCA plug and we are golden. Repeat for the second channel. Connections soldered up, and heat shrink applied Repeat for the second channel. Now when doing the other end, do not utilize the shield wire. Simply snip it off down to the jacket and only use the Red and Black wires.
I ran the expandable sleeving over the cabling on the other end before I proceeded to install and solder those RCA ends, as once they are soldered, its pretty much permanent. So be careful to check it all again before completing. And here is what the RCA cables look like once completed.
These are roughly 15 feet long and will run from my head unit, under the cabin carpet to the rear wall of my truck to the amp. Load Post 4. Comment 0 Photos 1 Share. This page is dedicated to a tutorial that came up by accident. You see, I had no intention of ever using the hardset plastic filler for the purpose of repairing plastic, however, it was the first opportunity I had to utilize it.
So me being the person I am, decided to use this opportunity to make a tutorial on how I used it for that purpose. I was removing a plastic panel from the rear cab of my truck in order to add expanding foam to the insides of some hollow panels to help keep vibrations to a minimum, when it happened.
I pulled too hard and the clips held their place A minor setback as I remembered I had the supplies on hand to do a repair. Once that was done, I scuffed the area around the damage with some grit sandpaper in order to ensure a proper bond to the plastic panel. I also used the smallest drill bit I could find to drill holes on both sides of the crack, again, to aide in making the strongest bond possible. You want to make sure you spread it to a large enough area around the damage area to ensure reiforcement and help in strengthening it.
I had a chance to quickly sand down the plastic filler and then applied some spot putty to the small imperfections. I then sanded that down with some grit sandpaper. Load Post 5. Painted door handle swap. The passenger side handle doesnt have a key hole.
Notice there is no keyhole. The other pic is a comparison of the old handle vs the new handle to be installed: Before and after shots of passenger side: Swap pics: Removing old handle. Its held on by 3 bolts that are not too easy to get to from inside the door panel.
You must remove the plastic paneling to get to the bolts. Then I removed the clips that attach to the latch and lock rods. They are just small clips that easily slide back. Once this is done, you can just take out the handle and replace with the new one. But since the passenger side handl originally had a keyhole and I am replacing it with a new painted handle that doesnt, I had to tie down the lock mechanism rod.
I used a plastic zip tie and attached the rod to the door wiring. His dad was a tech before him and his son is continuing the legacy. Thank you to all of our international Makers and Fixers- we love sharing stories from around the world!
Likes 89 Comments 2 View on Instagram. When Jessa was 19, her mom enrolled her in aviation school But hey, moms really do know best! After going through a rigorous training and testing program, Jessa is currently loving her job as an Avionics Mechanic. Likes Comments 51 View on Instagram. Likes 98 Comments 1 View on Instagram. For Noah sweeping floors and oil changes turned into a career of head gaskets, turbos, engine builds, and eventually diesel jobs!
Muscle arm emoji makersandfixers. Likes 99 Comments 1 View on Instagram. Awesome work, Jordan, keep it up! Like so many Makers and Fixers out there, Autumn started out working on a project car with her dad. Shout out to all the dads passing on essential skills to their sons and daughters! Likes 76 View on Instagram. Through hard work and education, he eventually bought a shop where he worked on cars every day. Nader started working with his dad when he was just 13 years old and still works alongside him to this day.
Likes 62 View on Instagram. After wanting one for years, Ryan bought a vintage VW Microbus that was completely rusted out. He taught himself how to weld while fixing it up and found something he really loved, and has now brought back several classic VW busses that were headed for the crusher. Good luck man! Likes 86 Comments 1 View on Instagram.
Anyone else have some awesome vintage tools in their box? Michael has been working on motorcycles his whole life. Likes Comments 24 View on Instagram. Check out our other 3 monthly winners in our IG story! Likes 51 View on Instagram. Likes 90 Comments 1 View on Instagram.
Years later, he moved south and began knocking on doors in an effort to pursue his dreams. Today, he is a Crew Chief for Team Penske!
He worked with joeylogano for 7 years and will now be working with ryanblaney10! I am positive! Tim Schwuchow started off as a kid sweeping the shop floor. Now he owns the place! Likes 59 Comments 2 View on Instagram. It all starts with a father-son project car and a trip to Daytona…. She started her career as an intern with American Airlines, and has worked on overhauling hydraulic pumps, heavy aircraft maintenance, and line maintenance.
She has also put together an all-female team for the Aerospace Maintenance Competition amcaero! Likes Comments 39 View on Instagram. Matt is a Diesel Technician who transitioned to public transportation a few years back. He takes pride in keeping his city moving. For more information on how to win the Share Your Story Contest, visit the link in our bio.
Brayden is the owner of an automotive specialty shop and has been working on cars all his life. The objective of my business is to help people save money and treat you like family and your vehicle like it was my own!
Likes 73 Comments 2 View on Instagram. Who else wants to open their own shop one day? When I started looking at aviation jobs, I knew I would face some hurdles…then I discovered my local Tech College had an aviation maintenance program. The job had everything I was looking for; airplanes, mechanics, electronics troubleshooting. Likes Comments 55 View on Instagram.
Now she works on semis and trailers. She is still learning and wants to learn even more trades going forward!
While working as a mechanic, Mike had the opportunity to become contractor at a test facility working on prototype motorcycles. Likes 95 Comments 2 View on Instagram.
Taylor started her career when she bought a mig welder at 19 years old! She became a CNC machinist and then attended welding school. Likes 66 Comments 1 View on Instagram. She had to have the engine replaced twice we were all young once right? Anyways, I saw the cost of repairs and said I want to be the person that helps people with their cars.
As a Fire Truck Mechanic, Michael is living out his dream and is proud that the work he does helps save lives. Likes Comments 19 View on Instagram. I enjoy the work. You meet different kinds of people, different kinds of cars and technology. Congrats Cory! VW Audi car cars auto engine technician autotech mechanic tools. Likes 98 Comments 4 View on Instagram.
Likes Comments 54 View on Instagram. At 13, Willie began working on cars and built a Ford Model T! He continued working on cars to help him cope with the stress of being a Social Worker helping children in the foster care system. Today, Willie owns a small metal fabrication company and still drives that Model T. Meet Robert, a full-time Emergency Vehicle Technician and part-time aviation enthusiast.
Single mom and Millwright Andrea Havlin moved her family across the country to continue her career. Meet Rick, a military veteran who was injured in Afghanistan and lost his right arm and leg. Blake worked on military trucks as a Wheeled Vehicle Mechanic in the U. Today is National Worship of Tools Day! Likes 89 Comments 6 View on Instagram.
As a part of the Mars team, Jenna worked on hardware assembly, testing, sheet metal fabrication, and support equipment design and modification. Check out the Mars Rover recently named Perseverance launch in July of this year! Likes Comments 15 View on Instagram.
After over a decade working as a fleet mechanic for an independent trucker, then a school district with 25 vehicles, Jaycie opened her own diesel performance shop. Congrats, Jaycie! Juan failed his auto class in high school… with a bang.
The engine he was re-building exploded. But years later, Juan has worked his way up to being the Lead Transmission Technician. Likes 79 View on Instagram. How old were you when you first started? Likes 65 Comments 1 View on Instagram. Adam does it all. What roles do you take on every day?
Check out our website to see more aviation stories like Ricky's! This requires us to adapt and change our self along with the tools we use. Likes 78 View on Instagram. Likes 86 View on Instagram. Started from the bottom now he's here! Check out Josh's journey on MakersandFixers. Likes Comments 23 View on Instagram. Liz said it best herself. She's let nothing stop her from achieving her goals and becoming a Diesel Marine Technician.
Jerry's interest in helping people led him to create a program for veterans where they can work with their hands, be creative, and help with PTSD. Likes 64 View on Instagram. He became a technician through the help of a very important mentor in his life. Has anyone helped you get to where you are today? Likes 61 Comments 3 View on Instagram.
She now works in one the biggest dealerships on the East Coast, and runs an Instagram page connecting and inspiring female mechanics. Join the community of Makers and Fixers. Share your story to be featured on our website and be entered in the monthly contest. Any shop owners or managers out there turning wrenches every day? Even though Ryan works on multi-million dollar airplanes every day, his favorite projects are still the cars he fixes with his dad.
Lots of people do a job just to get money. Me, I like this. I like doing this every day. At just 22 years old, Logan opened his own shop doing upholstery fabrication and custom paint. Congratulations to all! Read their stories on our website and submit your own story for a chance to win link in bio. Likes 64 Comments 2 View on Instagram. Just call us Santa! Check out Dan's story on our website - link in bio! Likes 60 View on Instagram. Trust is an important part of any Maker and Fixer's job.
Likes 45 Comments 1 View on Instagram. Since she was 12 years old, Lisa knew she wanted to go into aviation. Today, she encourages other women to go into the field as well. MakersandFixers aviation aviationwomen. Alex is more than a tech, he's a little bit of everything. Likes 56 Comments 3 View on Instagram. Likes 46 View on Instagram. Meet Jason.
He followed his gut and went into an industry he loves. Tell us what industry you work in! Likes 52 Comments 4 View on Instagram. Likes 36 View on Instagram. This is what we believe. Part 1 of 3 makersandfixers snapon. Likes 37 View on Instagram. Part 2 of 3 makersandfixers snapon. Likes 33 View on Instagram.
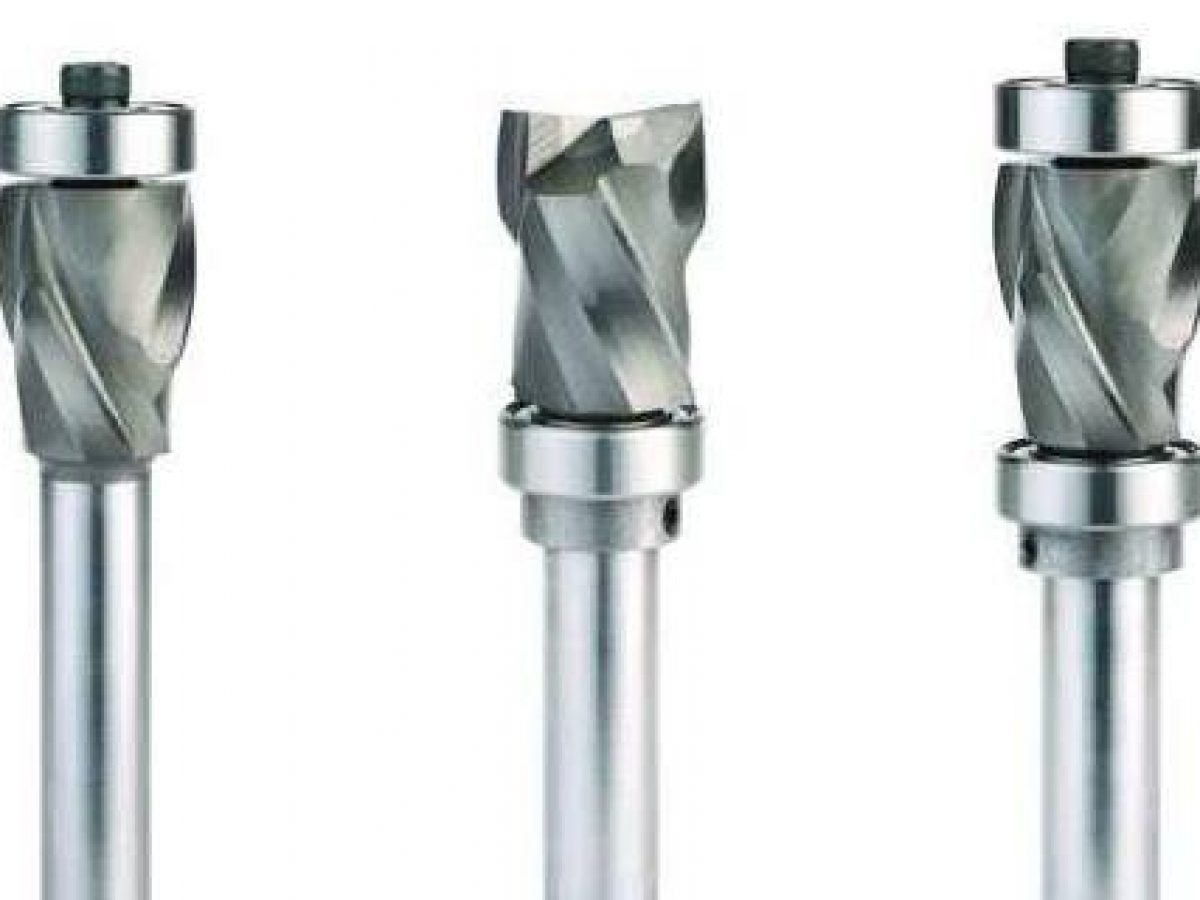
Belt And Disc Sander Amazon 2019 Adjustable Drawer Slides 40 |
SAMIR789
05.09.2020 at 16:44:23
Laguna
05.09.2020 at 19:34:17
EMOS
05.09.2020 at 21:54:43