Table Router Joint Jig Zoom,Next Wave Shark Sd120 Cnc Machine Ltd,6500 Woodworking Projects Pdf 90 - Try Out

Review this product Average Customer Rating: 1 reviews Add your own review for this product. I purchased profile B and am now looking to add the others. This bit has worked superbly! It provides quick and clean cuts while producing a very attractive edge. I've also varied the bit depth in the router to create different profiles making the bit more versatile besides its intended profile. Great bit!!! Great price!!! Without help, people will struggle to get good images.
Understanding what's possible and what's not possible makes the task much easier. Air Rifle Links and Demos :. If you're interested in air rifles, this site will introduce you to the types of rifles available and many of the things you'll Make Finger Joint Jig Router Table Value need to know to shoot accurately. It also touches on field target competition. There are links to some of the better sites and forums as well as a collection of interactive demos.
Basic Computer Operation :. This site helps anyone new to computers and anyone with a basic understanding of computers with a desire to learn more about the internal components of a computer. If you have a computer that you'd like to upgrade but don't know where to start, this is a good site for you. Basic Go-Kart Mechanics :. This site is for those who want to begin racing karts but don't fully understand how the various parts work.
It's mostly interactive demos that show how the various parts of the kart work. Email Home Page. Use F11 to go to full screen viewing if using Google Translate. From this point on, I'll refer to it simply as acrylic. Before we begin Do not remove the film or paper protector from the acrylic until you absolutely have to. The material can be scratched relatively easily. If the application requires that the surface is scratch free for a show vehicle, etc When cleaning the acrylic material, only use cleaners that are approved by the manufacturer.
Unlike glass, glass cleaners like those with ammonia can damage some acrylic. When cutting acrylic for applications where the edge will be visible and will need to be either polished or at least very smooth, it's absolutely imperative that you get the cut right the first time.
It may seem that you could easily fix any roughness in the edge with a bit of sandpaper. It's VERY time consuming to have to fix the results of a bad cut. Sanding, filing and scraping go very slowly, especially on rough surfaces. Cutting Acrylic: There are a couple of different ways to cut acrylic. You'll see standard blades with teeth simply cut from the material that makes up the rest of Finger Joint Jig Router Table Title the blade.
These are budget blades and are rarely used. The better blades have carbide teeth welded or brazed onto the steel. These are much more durable and can last for many years if not abused. Blades come in different configurations. The teeth on the following blade are in the most common configuration. The second blade is a more specialized blade. The teeth alternate from straight to beveled.
The beveled tooth is beveled on both sides and flat on top. Another characteristic is the rake angle. The first image below shows a blade with a moderate rake angle. For rough cutting acrylic, you can use a table saw or a circular saw with a fine blade. Blades with fine closely spaced teeth like those used for plywood will work relatively well.
Blades with widely spaced teeth and a significant rake angle like those preferred for cutting MDF will cause significant chipping. For the casual DIYer, the finish with these may be good enough not requiring a more expensive blade. When using a hand held circular saw, use a guide to make sure you get a straight cut with minimal chipping.
The Irwin is a TCG blade and does a very good job on a table saw. There are blades made specifically for cutting acrylic. If you're going to be cutting a lot of acrylic or are using very expensive thick material, you need to invest in a blade specifically designed for cutting plastics and laminates. Blades with a triple chip grind like the Irwin blade mentioned are well suited for acrylic so if you can't find a blade that is specifically made for acrylics, the general purpose TCG blades may work well enough.
When you get a blade that cuts the acrylic well, you can make about light passes with a scraper and then do a bit of light sanding and the edge is good enough for most any purpose polishing or joining, to be covered a bit later. Chipping was mentioned above. If you need to have a perfect, good looking joint, you cannot have any chipping. The first image below shows significant chipping. The second image is a much cleaner cut. A note about price Used properly, they will last a very long time and are well worth the up-front cost but the cost can be a bit of a surprise.
Many of us have table saws that were made for general purpose cutting and do a good job for building speaker enclosures from MDF. Acrylic is expensive, when someone buys an acrylic enclosure, they expect it to be perfect.
When cutting acrylic, where the tolerances may need to be within a few thousandths of an inch to make the pieces fit together perfectly. This means that any runout play, slack, wear When the blade is working hard to make a cut through the middle of a sheet of acrylic, the runout may be more of an issue than when just trimming a few thousandths off of the edge.
Then move the fence to where it needs to be and trim the last few thousandths of an inch off of the edge. Jigsaw: Jigsaws can be used to cut acrylic when you need something other than a straight cut.
If a jigsaw is all you have and you need to keep costs down, the right blade and a bit of preparation can produce good results. To reduce the work of cleaning up the cut, use the finest blade that you can find. Blades with reduced depth like those used for scroll work - shown below will work best due to less friction and less resistance when turning the blade.
You'll have to experiment with cutting speed to see what works best. Too much pressure can cause excessive chipping. Going too slow may cause the acrylic to melt. If the acrylic melts when cutting, use a light lubricating oil. Have someone apply the oil to the blade as you're making the cut.
DON'T use an aerosol dispensed oil. The propellant may be flammable and may be ignited by the jigsaw motor. This blade is made for cutting laminated flooring. Below, you can see the blade profiles for the blade above first image and a standard jigsaw blade. As you can see, the tips of the teeth on the laminate blade are directly in front of the body of the blade.
On the scroll blade, the teeth cut a kerf wider than the body of the blade. Between these two blades, it would seem that the scroll blade would cut faster but the laminate blade cuts much more quickly. You should also experiment with the various setting on your particular jigsaw.
With some blades, for example, the cut will be very bad so bad that the material melts back together when the blade is set to a normal, straight up and down stroke but when the jigsaw is set to the maximum orbital setting, that same blade will make a clean cut.
Router: A router can be used to cut acrylic for either straight or curved cuts. Trying to cut too much acrylic can lead to melting of the material unless you have a bit well suited to cut plastic.
To prevent chipping, make sure the bit is not allowed to break contact with the cut edge. If it does break contact with the material and you push the router bit back into the edge too quickly, the cutter may chip the acrylic. Spiral bits are generally better than straight-cut bits and slow-spiral bits tend to be a bit better than standard spiral bits.
You also must make sure you have a sharp bit carbide tipped or solid carbide recommended to prevent melting of the material. Again, you'll have to experiment to see what works best for you. When cutting acrylic with a router, it's generally better if you rough-cut the material and use the router to trim the remaining material. You can use the router or any other saw for the rough-cut. If you are cutting through a large panel and want a fine finish on the cut, you need to support both pieces of the panel.
If you don't support both pieces, the piece that falls away as the cut it finished could cause the corner of either piece to chip. This is a minor problem for rough cuts but for cuts where you don't want to do any finishing of the cut edge, it's important. The bits below are solid carbide spiral bits. The top is a standard spiral Whiteside RU The bottom is a slow spiral Amana Both do a good job but the slow spiral produces cuts that are a bit cleaner.
When you buy router bits, there are up-cut and down-cut bits. If you are cutting slots or have a vacuum connected to your router to remove shavings, you'll likely want the up-cut bit. Otherwise, I'd recommend the downcut bit. The downcut bit will throw the shavings down and away from you. When making a cut along a fence with a router, its face has to be very smooth and it has to be very rigid, especially for long cuts. To make it rigid, it needs to be relatively deep. Oak, ash or birch will work better than pine plywood.
To make the face of the fence smooth enough to prevent any flaws from showing up in the cut, you will likely need to face it with metal stock. Aluminum angle stock works well. You can use iron stock but it's generally too rough. If you cut along a straight edge that's not stiff enough, you will make a bowed cut. This is because most people push hard against the straight edge to make sure that the router doesn't veer away from it.
This can cause a weak straight edge to flex slightly. For some applications, this won't be a problem but if you're going to bond the cut edge to the face of another piece of acrylic, it can make getting a perfect bond nearly impossible.
If you do get a good bond, the piece that you bond it to will be bowed and under constant stress. Again, if you're bonding two pieces together, use a saw with a fence like a table saw.
Previously, runout was mentioned. This can be a problem with routers also. A poor quality or old router with excessive runout will make it impossible to get a good, smooth cut. If your router isn't producing good cuts and you need a good router, do some research google, forums, reviews If you use the various woodworking forums, tell them that you're cutting acrylic and need to have a router with little or no runout. I'd suggest small, trim routers. The Bosch pr20evsk does a good job.
Larger routers often have a collet that holds the bit. That adds one more piece that could add runout. Of course, you know to wear safety glasses when doing any cutting or grinding but it's even more critical when using solid carbide bits. Carbide is extremely hard which makes it a good material for cutters but it's also very brittle. When they break and they're not difficult to break they can shatter and cause significant injury.
When they shatter, they will have the ability to penetrate skin. This means that it's important that you protect yourself well. A full face shield and a heavy apron aren't excessive. If your router has shields, keep them in place. The cost of router bits like specialized saw blades can be a bit of a shock.
These are typically specialized bits but sometimes that's what you need to do the job properly. Router Safety Respect the router. Too many people don't give a router the respect it deserves. Set up is pretty straightforward if you take your time. The perspex router base mounting plate is solid, but it doesn't quite fit flush with the aluminum supports. The manual suggests adding shims in the form of tape to allow the two edges to marry up. It required about ten strips of masking tape to achieve a flush surface, so I would suggest that either the perspex base needs to be slightly thicker, or the rebates on the aluminum extrusions need to be re-machined made less deep , to prevent this happening.
Otherwise, it works very well. The fence and router assembly sit perfectly square to the base. The pre-drilled holes align perfectly. Everything bar two very tiny screws was included. A six inch piece of the plastic edge banding on the table had come loose, and broke off during assembly, but this won't affect the way the table works. Just a few other design issues: You cannot easily attach feather-boards to the fence.
There is no track provided, and the knobs holding the router assembly plate get in the way, preventing you from running stock that's more than about 5 inches high over the blade. So this horizontal table isn't a worthy substitute for a regular router table. And finally I would suggest finding a suitable perhaps 2nd hand router to leave in this table if you are going to be using the set-up frequently, as it's a pain to keep having to remove and reinstall the router whenever it's required.
I am using a w Makita BR circa about and I intend to leave it mounted in the table. There are not many of these horizontal tables available commercially not in Australia, anyway. I would recommend this product.
It does what it promises to do pretty well. BTW, Australia is not on the pull down list of countries provided, but I can assure you, we are still around! Before purchasing the unit I did review all the previous reviews and found them to be helpfull in making my decision to purchase the table. In fact I purchased all 3 units. The order came within a reasonable time. Since it was shipped to Canada. I was disapointed in the way it was packaged. The units are quite heavy and all three corners, the same corner on each of the three units was damaged.
Better protection should be used. Molded heavy plastic outside corners would help. It was easily put together, but be carefull not to turn the screws to tight, the threaded insert might come loose as what happened to me.
It was an easy fix though. I've only given it 4 stars but it wouldn't take much to get it to a 5. I think you will be amazed how little you need to really turn this unit into something special. Thank you MLCS. The table was easy to assemble and the assembly directions were among the most accurate I have used.
The table itself is well made and well machined. I used the machine to construct a sliding dovetail in a table leg and skirt board with excellent results. The only downside was a need for some shims to bring the router plate flush with uprights and fence.
Masking tape works but shims would be much more professional. This was one of the best tools I have ever aquired. It performed flawlessly for some moulding I needed to make. I recommend it highly to any woodworker. I have to agree with the previous reviews to some degree, but it was obvious to me that MLCS had made an effort to correct some of the previous shortcomings the table had.
First of all the wooden block that attaches to the plexiglas router plate is now pre-drilled even though the instructions to drill it yourself are still included. Unfortunately, this does not improve the smoothness of operation when raising or lowering the router. Don't misunderstand me, it works, but not with the smoothness you'd like to have. I believe both wooden pieces should be replaced with metal, providing more precise alignment.
I had no problems with the directions, probably because they were written in this country and not China. Let's talk about dust collection for a minute. In the on-line video the entire table is dropped into a recess built into the bench and this recess contains the dust collection system.
Not feasible for those of us who don't want to build a new bench or seriously rebuild an existing one. Sealing up the rear of the table looked like a difficult proposition to me, so I chose to build a fixture that slides into the front opening under the table with a 4" hose connection.

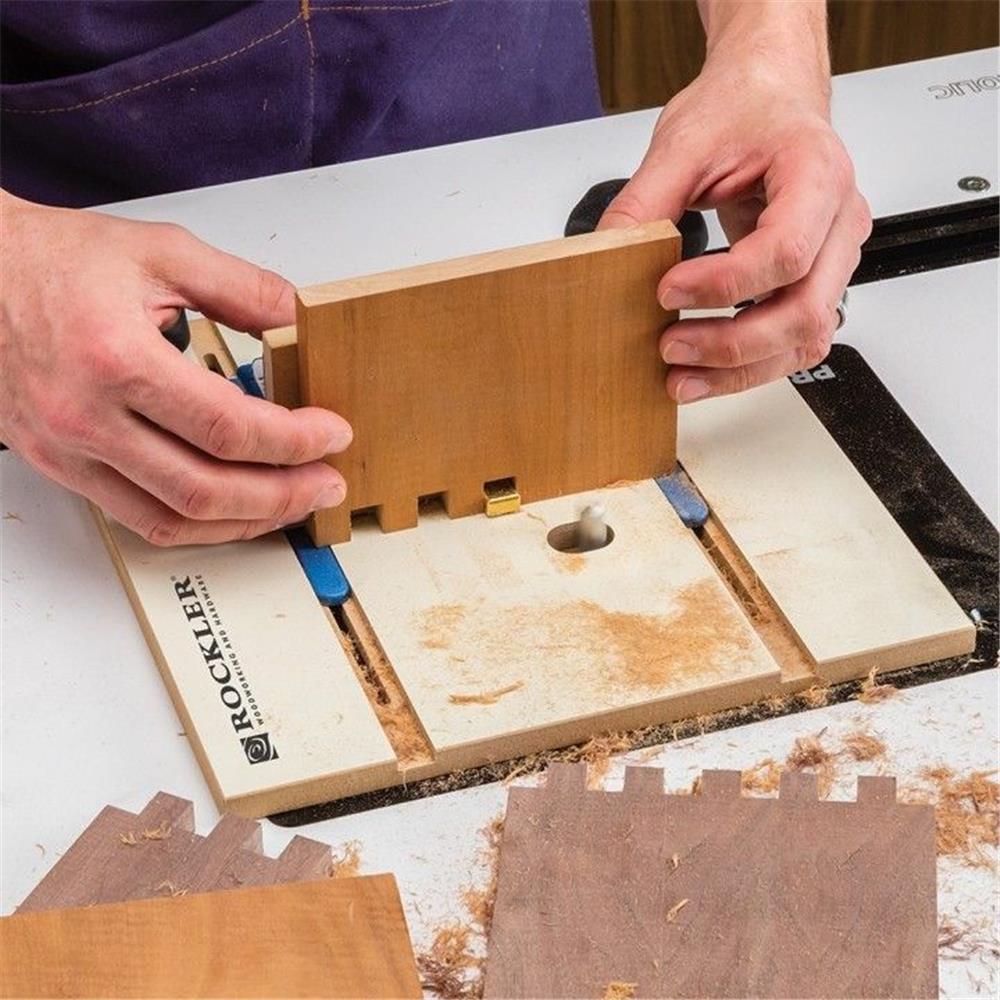

Best Rap Us Album Wallpaper Open Media Vault Recommended Hardware 1 By 3 Wood Projects 600 |
SimPle
07.03.2021 at 10:52:10
melek
07.03.2021 at 21:27:51
2OO8
07.03.2021 at 22:25:42
Roni_013
07.03.2021 at 17:46:26