Jet Plane Diesel Limited,Woodworking Plans Table Lamps Difference,Pocket Hole Jig Without Clamp Evo - New On 2021
Their engine has flown in test aircraft and airship installations. Unlike the Junkers, it is made for horizontal installation with a central output shaft for the geared cranks, the overall installed shape thereby approximately resembling a four-stroke flat-four engine.
However, the Gemini is an engine. They have recently announced that Tecnam will test a prototype with the Gemini engine.
Wisconsin-based Engineered Propulsion Systems develops its Graflight liquid-cooled V-8 engine with steel pistons and compacted graphite iron crankcase for better strength and durability than aluminum at similar weight, increasing time between overhauls to 3, h. It is managed by a Bosch ECU and consumes Jet A, JP-8 or straight diesel for general aviation aircraft and small helicopters , military drones , small boats or troop carriers, and its low vibration allows the use of composite or aluminum airscrews.
It is a four-stroke inline turbo charged engine. Formerly Vulcan Aircraft Engines until September The FlyEco diesel is a three-cylinder, 0. From Wikipedia, the free encyclopedia. This article needs additional citations for verification. Please help improve this article by adding citations to reliable sources.
Unsourced material may be challenged and removed. General Aviation News. Retrieved 20 April Flying Magazine. Int J Occup Environ Health. PMID S2CID December Journal of Environmental Health.
Environmental Research. Bibcode : ER Popular Mechanics. September Retrieved Accessed: 28 December Cranfield University, 20 October Slide Rule. London: Heinemann. London: Stratus Books. ISBN Archived from the original PDF on 10 September Retrieved 9 August Safran SMA.
March December 19, Archived from the original PDF on August 9, Retrieved August 9, RED aircraft. Jul Archived from the original PDF on DieselAir Research, Inc.
Archived from the original on Archived from the original on 14 December August 10, Nov 22, Oct 14, Advanced Component Engineering.
Gemini Jet2holidays Planes Limited Diesel. August April Engineered Propulsion Systems. Raptor Aircraft. Experimental Aircraft Info. European Commission. Airbus Helicopter. November 10, Teos Powertrain Engineering. Categories : Aircraft engines Diesel engines Aircraft diesel engines. Hidden categories: CS1 maint: DOI inactive as of January Webarchive template wayback links Articles needing additional references from August All articles needing additional references All articles with failed verification Articles with failed verification from August All articles with unsourced statements Articles with unsourced statements from August Wikipedia articles needing clarification from September Commons category link is on Wikidata.
Namespaces Article Talk. Views Read Edit View history. As a result the broader turbine engine world has standardized around this type of fuel. Piston engines are the second category of aviation engine in common use, and depending on their design may use ignition or compression fuels.
Piston engines may burn automotive or aviation gasoline ignition fuels, though few can use automotive fuel… more on that later , or for aviation diesel engines, Jet-A compression fuel. The standard fuel used in aviation piston engines is aviation gasoline, or AvGas. The approved engines typically are approved for the use of lower octane fuels that are no longer produced specifically for aviation engines.
These STCs are popular with the owners of older light aircraft and with homebuilders and it offers a potentially lower cost source of fuel. The rarest piston fuel is by far Jet-A. Aviation diesel engines are an abnormality in the piston aircraft fleet, as the technical challenges associated with building lightweight aircraft diesel engines are substantial.
Kerosene is a generic name for a wide range of fuel products, of which Jet-A is a tightly standardized version. As a fuel product, Kerosene uses a wider range of quality and chemical property standards, which is acceptable for most terrestrial and marine applications.
Because aviation requires consistent fuel performance across multiple engines and airframes and in rapidly changing environments, Jet-A is more precisely refined to remove impurities and ensure consistent performance. It is apparent from the table above that Jet-A is refined to much tighter tolerances. This is necessary to ensure the fuel meets the necessary performance across the operating envelope of turbine aircraft.
The slightly lower autoignition temperature allows for more reliable performance within the combustion chamber of the turbine engine itself. Finally, the thermodynamic output of the fuel must also be consistent in order to ensure that flight planning manuals provide accurate data, as lower heating values produce lower thrust output, and reduced cruise performance.
The criticality of consistent performance drives these tighter tolerances. While a typical aircraft turbine would burn generic kerosene, engine performance would be reduced and unpredictable. The difference between diesel fuel and Jet-A is similar to that between Jet-A and kerosene, but of an even greater magnitude. Diesel fuel is designed and refined for use in diesel piston engines; it contains higher concentrations of impurities, and does not tolerate the wide temperature extremes needed in aviation.
Reviewing the data in Error! Reference source not found. These differences are tied to the chemical makeup of the two fuels, with Jet-A being refined at higher temperatures, thus removing the sulfur compounds and providing a more uniform set of carbon molecules.
Jet-A is essentially an extremely high-quality diesel fuel, and indeed running a typical automotive diesel engine on Jet-A is likely possible. However, the chemical compounds within diesel fuel have lubricating properties that ensure proper operating of fuel injectors, pumps and other mechanical components; the higher chemical purity of Jet-A strips away these lubricating compounds, resulting in more consistent performance, and a wider useful temperature envelope, but poorer mechanical properties.
Additionally the higher vapor pressure of diesel fuel may interfere with proper atomization of the fuel within the combustion chamber leading to a host of other issues.
There are turbine engines designed to use diesel fuel, but these engine have distinct design requirements from aviation turbines. The base chemical components of these fuels are virtually identical, as both are fundamentally gasoline and are extracted from the refining process at the same point. AvGas contains tetraethyl lead TEL , to improve engine component lubrication, and boost the octane rating of the fuel. This type of octane boosting was common in automotive engines until , when environmental concerns surrounding lead contamination resulted in the phase-out of lead in automotive gas.
Detonation is an operating condition in which the fuel ignites spontaneously under compression prior to normal firing of the spark plug. This results in severe pressure and temperature spikes within the engine, and quickly leads to severe engine damage. Tetraethyl Lead reduces wear in valve assemblies with the engine. The build-up of lead on valve guides and seats helps to lengthen the service life of these components. A wide range of aviation engines are compatible with unleaded fuels such as MoGas, presuming the engine manufacturer has approved the use of unleaded fuel and the associated octane rating is met.
Typically, these engines have fairly low horsepower outputs and low compression ratios, as such the aircraft they are installed in are typically small, lightweight aircraft.
The greatest hazard for aircraft engines using unleaded fuel is typically engine knock during climb at high altitudes, where the fuel air mixture is generally leaned to maximize engine performance, and where engine temperatures are highest.
The tighter quality control processes required for aviation fuels ensures that greater uniformity is present within AvGas. One example of this is the use of ethanol as a fuel additive. Ethanol is increasingly mixed with automotive fuel to raise the octane rating and improve fuel economy at reduced cost to fuel refiners, but the precise mixture ratio is rarely placarded sufficiently to ensure safe aviation use.
Unfortunately, ethanol is incompatible with nearly all aviation piston engines and their fuel systems. The rubberized components used in aircraft fuel systems, from tanks, to hoses to seals are not compatible with ethanol and quickly deteriorate when ethanol laced fuel is used.
Automotive engines have been designed to utilize a wide range of fuel qualities and tolerate a wide variety of additives to improve engine life and durability. The effect of these additives is numerous, but in particular, these additional chemicals raise the vapor pressure of MoGas, meaning that it evaporates from liquid to gaseous at a higher rate relative to AvGas.
This higher evaporation rate makes MoGas susceptible to vapor lock at high altitudes and at high temperatures, making engine starts more difficult and engine failures at low power settings more likely.
Check it out here. Piston engine powered aircraft continue to rely on AvGas as a fuel source because the design requirements of diesel engines incur an inherent weight penalty, and new engine development is expensive and prolonged.
Diesel engines are typically heavier than their gasoline equivalents to meet the strength requirements associated with compression engine cycles. Automotive and aviation diesels alike nearly exclusively require turbocharging to be effective power plants as throttle response is a primary design consideration in both industries. Additionally, aviation diesels are, primarily, derived from automotive diesels and thus must be geared down to drive a propeller.
These gearboxes are failure prone, and often result in expensive replacement costs over dramatically shorter time intervals than is typical for gasoline engines. These additional mechanical systems drive up the weight and complexity of the engine, a serious detriment to the implementation of diesel engines as a primary powerplant for piston powered aircraft. This resultant increase in weight generally results in an engine that develops less power for the same basic engine size and weight, resulting in lower aircraft performance.
Lower performance is not a detriment for certain segments of the aviation industry, particularly in the training sector and Asian and African markets, but sufficient sales have not yet materialized to justify the development costs and timelines necessary to certify new piston aircraft under current regulatory burdens.
The automotive roots of these engines do provide some benefits however, much of the research and development costs of the engine itself have been amortized by the automotive industry, and the engine control systems are typically electronic i.
FADEC controlled just like many turbine engines. Electronic controls simplify engine operation and allow for extremely efficient operations.
However, there is not yet sufficient net operating cost benefit for these engines to make significant sales gains within the piston aircraft fleet, either with OEMs or as aftermarket STCs. When you drive you spend little time with the throttle wide open developing maximum power.
It is apparent that if typical automotive engines were operated similarly to aviation piston engines, higher octane values would be required to maintain reliability. The high octane rating requirements of aviation piston engines stem from the pinnacle of piston engine development in the s into the s.
Supercharging and turbocharging drove the outputs of piston engines to extreme heights in order to maximize engine performance for military and transport aircraft. The extreme operating pressures and temperatures required fuel that would resist detonation under high engine loads for hours at a time.
The requirement for aviation piston engines to maximize power output under continuous high load is the driving design requirement for Jet Plane Diesel Engines the use of high octane rating fuels. Turbine powered aircraft operate at environmental extremes that necessitate extremely stable, pure fuels that produce consistent, predictable thermodynamic performance.
As discussed previously, the chemical properties and ease of storage of Jet-A and its equivalents make it ideally suited to turbine engine operations. AvGas in contrast to Jet-A is contaminated with lead and has a dramatically higher vapor pressure; both of these factors make it difficult to use in high temperature environments.
During combustion, lead is deposited on combustion liners and expansion turbine blades, reducing efficiency aerodynamic efficiency of the turbine and increasing the engine temperatures, resulting in decreased engine life. The vapor pressure issue results in cavitation and vapor locking of fuel pumps.

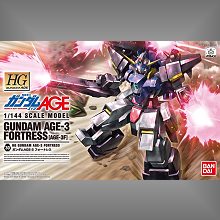

Chest Lid Hinge Cabinet Drawer Slide Bumpers Model |
NUHANTE
01.06.2021 at 17:17:48
EDEN
01.06.2021 at 22:32:10