Best Ca Glue For Wood Rings 200,Pumpkin Carving Kit Menards Usa,Makita Plate Joiner Cordless 35,Makita Rp2301fcxk Review List - And More

In the past, if a project was going to get wet, I would use Titebond III to glue the joints together. All PVA glues, including the Titebond series, did very poorly in the exterior conditions. Several of the blocks from Titebond II and Titebond III did not even make it to the test as they fell off when being carried to the testing rig.
The evidence was more than enough to convince me that from now on, in exterior conditions, I will be using epoxy or even CA Glue instead of the PVA glues. One expectation I had was that the PVA glues would be vastly blown away by the superiority of epoxies and other high tech glues. The strength for most of the PVA glues was far more than would be needed for any joint.
This test was designed to find out the strength of the glues regardless of the strength of the wood. Almost all of the glues tested would cause the average wood to fail long before the glue would fail. While some of the numbers are very impressive the glues tend to be far stronger than they need to be.
Many of the assumptions going into the test were destroyed, several were upheld and reaffirmed. For most wood glue joints, PVA is a fantastic glue that will serve the user very well. Hide glues are a very respectable glue with several benefits other than their strength. For exterior conditions, epoxies really are worth the expense and time needed to complete the project.
Although in the past I have laughed at the idea of using a CA glue, I will now be adding them to my normal use as legitimate wood glues. For detailed information on how the test was conducted, you can watch this video. Here are some supplies and tools we find essential in our everyday work around the shop. We may receive a commission from sales referred by our links; however, we have carefully selected these products for their usefulness and quality.
By Popular Woodworking. Too little glue will leave gaps in your ring. If you're adding another layer of wood veneer to your ring, you can now fish the second piece out of the pot of boiling water. Wrap it around the base of the ring and secure it with tape. Wait a few minutes, then glue it to the base layer in the same manner described above. If you're using two thin strips of veneer on the outer layers of the ring to create a channel for an inlay, you can wrap and glue them separately from each other.
I prefer to leave the very outside end of the veneer unglued at this point. Cyanoacrylate likes to turn white when it's exposed to water. If I glue it now, it'll likely leave a white residue when I go to sand the ring and finish it. The residue will be impossible to remove because it impregnates the wood fibers. When the ring is glued, slide it off the tube and let it sit out to dry.
It has to be completely dry before you begin sanding. This can take several hours. This is when I glue down the outer edge of veneer.
Sand it down, slip a little glue under the edge, and press firmly. Because the outer edge is thin, tapered veneer, I use an implement to hold it in place instead of my finger. I'm really sick of superglue on my fingers. The glue will take longer to set this time because the wood is no longer wet.
Some woods show the seam more than others. The pearwood veneer I have gets darker edges in places coated with superglue, even if the ring is finished with that same superglue. The lighter and darker woods I've used like maple and walnut don't seem to have that problem. The seam doesn't bother me, but you might not want a visible seam, so you might want to experiment with which types of wood hide seams the best. You could always do some creative cutting and sanding for the outer seam to really blend it with a wood that shows seams.
I don't bother to do much seam shaping; I usually can't even find the seam on my maple or walnut rings once they're finished. I use the dremel to smooth the edges of the ring. Even when I wrap the wood carefully, the edges aren't perfectly aligned. I'm not a perfectly precise type of person. I don't use the dremel for sanding the rest of the ring. I'm probably just uncoordinated, but I end up with a lumpy ring if I use the dremel on the rest of it. Use sandpaper to smooth down any sharp corners at the edges of the ring.
If you have trouble getting sandpaper inside the ring, you can use a small file. Sand and smooth the edges of the groove if you're doing an inlay. Proper sanding will make a huge difference in the finished ring.
Use a full range of sandpaper grits and don't skip any. I use sanding blocks from 60 grit to , then switch to my micro mesh sanding sheets. The micro mesh really matters if you want a smooth, glossy finish. You only need to sand up to the grit in the micro mesh before finishing.
Sanding beyond that isn't necessary. The finish needs a small amount of roughness to grip onto, and you'll be using the higher grits to sand the finish, anyway. If you don't want to bother with a stone inlay, skip to step 5. If you want spots of crushed stone in your ring, take a grinding bit on a drill or dremel and drill holes into your ring. Don't drill all the way through; just make cavities that you can fill with the crushed stone.
We bought some cheap rocks in various colors from the local rock shop. None of them cost more than a dollar. Use a hammer and anvil or whatever else to smash your chosen rock into powder. Josh bought some plumbing fittings at the hardware store to smash the rock. The larger metal cap contains the Best Ca Glue For Wood Rings 300 bits of rock so they don't fly all over the place when I'm smashing them. Fold a piece of paper in half lengthwise.
Unfold and fold crosswise. This will create valleys that make it easier to keep your powdered stone where you want it.
Dump your crushed stone in the center of the paper where the lines intersect. On a separate small piece of paper, squirt equal portions of both parts of the epoxy. Mix them thoroughly with your toothpick, trying to avoid adding a lot of air. Pour on a little of the crushed stone and mix. Add enough stone that you won't have empty clear spots in your epoxy when it's in the ring, but not so much that the epoxy can't hold everything together.
Press the stone mixture into the recesses of your ring with your toothpick. Squash it in carefully and thoroughly. After I used the toothpick, I put a little petrolatum on my fingertips to squash it in further. Scrape off as much excess as you can while still keeping the stone mixture slightly above the surface wood in the ring. You'll save a little time if you also scrape the epoxy off the surface wood as much as you can while it's wet.
My container of epoxy said 5 minutes. It was misleading, in my mind. I had 5 minutes of work time, but it wasn't hard enough for me to sand after that time. The small print on the package stated that it took 8 hours before it was usable and 24 hours for the full cure. I'm impatient. I waited an hour or two. You should probably wait longer It would take forever to sand down the excess stone mixture with sandpaper, especially if you use the types with a less durable grit.
I used a large metal file to get most of it, then refined it with sandpaper. Work your way back up the grits of sandpaper. Make sure the stone portion and the wood are now flush with each other.
There are lots of different types of finishes. I won't talk about most of them. I've heard good things about layer upon layer of a drying oil, such as tung oil. I've never tried it.
Josh is fond of shellac. So am I; it's hard to go wrong with edible bug excretions. You don't believe me?
Check your candy labels for shellac, resinous glaze, or confectioner's glaze. Shellac doesn't leave a very durable finish on a ring, though. Some people prefer to finish their wood rings with beeswax and olive oil.
The oil and wax should be reapplied regularly and won't be as glossy as other finishes. They leave a really nice, "natural" feel to the wood, though. I love using olive oil and beeswax to finish a ring made of solid olivewood.
Olive oil and beeswax do not fill the pores in wood. Some wood has bigger pores than other wood. When choosing a finish, consider the effect you want, including whether or not you want to fill all the pores to make the surface completely smooth.
My own personal opinion is that cyanoacrylate is the best finish for bent wood rings. It's durable, water resistant, and it's already used throughout the ring. It's sometimes a pain to work with. Before you add any finish, look closely at your ring. You might see some pale or dark streaks, depending on the color of your wood. These are pores in the wood, and they're likely filled with fine sawdust from sanding your ring. If you don't get rid of the dust, it'll get stuck in the finish and leave your ring dull and dirty looking.
These wood glues excel when joining wood grain end-to-end—for example, if you need to connect two pieces of crown molding—forming flexible, durable joints. This toxic chemical needs to be handled with care. Always work in a room with good ventilation, and wear a face mask and goggles to avoid inhaling glue fumes. If you intend to stain your wood, know that polyurethane goes on more easily than PVA.
Still, remove any excess glue with mineral spirits—water is not strong enough. Once cured, these bonds are very hard and rigid, which is helpful if you only need to create a temporary bond—a couple taps of a hammer or mallet will break it. It also comes in handy for filling cracks when mixed with sawdust. Unlike other wood glues, CA glue will not bond to a dry wood surface and requires the wood be slightly damp before application. It does, however, bond almost instantly at room temperatures, so it should be handled with care and precision.
Wear a mask and protective gloves when working with the runny, water-like glue; if any glue touches your skin, remove the superglue with acetone nail polish remover.
Acetone can also be used to remove excess super glue from your work surface, but this chemical solvent can also damage your wood finish if not used carefully. Its short shelf life means that CA glue will only work on near-term projects, good for about a year when sealed but as little as a month after opening. Basically boiled animal collagen, hide glue comes in two forms: liquid and solid crystals that are melted in a hot water bath and applied with a brush. The liquid room-temperature hide glue utilizes urea crystal additives to keep it fluid and allow more time to work.
Hot glue, in contrast, will cure as it cools soon after application. Today, woodworkers choose both forms of hide glue primarily for the leeway i. It creates lasting, yet flexible joints—which is why many antiques are still repaired with hide glue. Using this adhesive preserves the quality of antiques and honors traditional craftsmanship. In liquid form, hide glue gives you more time to perfectly fit two pieces of wood. When fully set and dried, it is an excellent choice for furniture construction and other tight, lasting bonds.
Both types of hide glue are often used in guitar and stringed instrument construction. Unlike the liquid texture of other wood glues, epoxies thicken to a putty-like consistency.

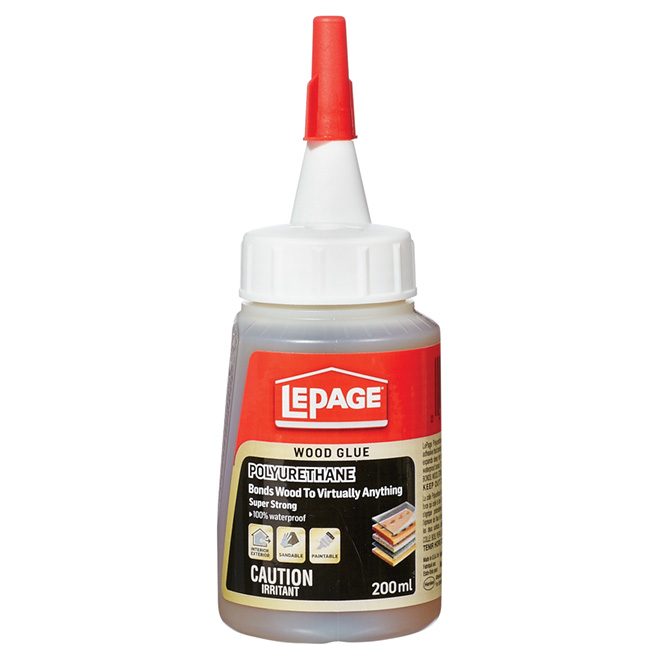

Woodwork Craft Shop Line 28 Euro Drawer Slides Github Make A Frame Teepee In |
Jenifer
06.04.2021 at 20:13:33
Ilqar_10_LT_755
06.04.2021 at 18:28:59