Best Wood For Turning Finials Zip,Carpenter Plane Wood Kitchen,Wood Workshop Insurance Quote - How to DIY
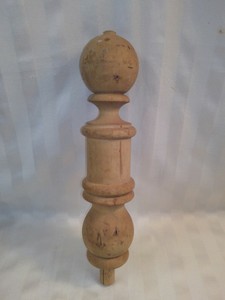
Typically, there are multiple tips that fit in the live center bearing head. Most manufacturers tailstock centers are just a single point and I would suggest upgrading to a cup center of some form. This increases the surface area on the tailstock side and is less prone to tearing away.
I turn on a Nova DVR and as such I stayed with the manufacturers upgraded line of tail stock attachments. If I recall correctly I upgraded the tailstock center after the stock live center bearing went bad. Most manufacturers make similar product for their lathes. The vast majority of things I turn I use the cup center in the tailstock.
The idea is to drill a pilot hole whos diameter is slightly less than the treads of the screw chuck. The screw chuck screws into the pilot hole. There are two main types of screw chucks.
One being, and the one that I prefer, is an all in one attachment that screws onto the headstock. The other is a screw attachment that fits in a 4 jaw chuck. Both basically operate the same way. To attach a blank, I put the screw chuck on the headstock and turn the Best Wood For Turning Finials Journal lathe to the lowest rpm setting.
I then take the bowl blank with the pilot hole and press it against the threaded end of the screw chuck. Let the blank go when it threads all the way up. Also use the tailstock in conjunction with the screw chuck as its not uncommon for the blank to become wobbly when the treads strip.
This is a lot more common on softer woods. I turn bowl bottoms with a tenon for 4 jaw chuck mountings using this method of mounting as it is quick and secure. It has better holding strength than a drive spur and is quicker than mounting a faceplate for larger diameter and heavy bowl blanks. Wood Lathe Faceplate Mounting Faceplates are the most secure method for mounting wood on a lathe.
As the name suggests is a hunk of metal roughly in the shape of a plate that screws onto the headstock. There are number of holes in the faceplate that allow you to screw the faceplate to the wooden blank. In my opinion, faceplate mounting is best for very large projects or ones that are extremely out of balance. Additionally, the screws used are very important. You want to use a screw that bites well, are not brittle, and whos heads are not prone to stripping.
Drywall screws are not a good screw to use for mounting with a faceplate. Faceplate screws also tend to be short as they will occupy a portion of wood that is not usable. Faceplate mounting offers the least amount of flexibility to control the shape of a vessel and as such I never use a faceplate. It is true that it allows you to make small openings.
However, mounting on a drive spur or in the manner I describe below allows some latitude to reposition blanks while turning between centers. You can slide the blank around in my method or alter the tailstock position to turn out less desirable sections in the wood. Once a faceplate is attached or the blank is mounted in a chuck that flexibility no longer exsists.
This is just my experience. The one faceplate I own is actually attached to an early vacuum chuck coupling that I made which I use as a jamb chuck now. At that point saftey becomes the Best Wood For Turning Duck Calls 35 primary concern and I advocate using a faceplate for large or very off balance work. Mounting Wood on a Lathe with 4 Jaw Lathe Chucks A chuck is a device that screws onto the headstock and is designed to hold a piece of wood by either compression on a tenon or expanding to fill a recess. Any finish will stick to shellac and vice versa.
It also dries incredibly quickly and is food safe. While you can buy premixed liquid shellac at a hardware store, I prefer to use dry shellac flakes that have to be dissolved in denatured alcohol.
I mix a small amount of dewaxed shellac flakes with enough denatured alcohol to cover them. I cap the container and let the flakes dissolve over a period of 12 to 24 hours.
You can accelerate the process slightly by placing the bottle in a sunny window or outside on warm summer days. A full-strength solution like this is far too viscous for our needs and must be diluted by mixing one part full-strength shellac to three parts alcohol. This reduces it to a 2-lb. With the turning mounted in the lathe and stationary, I brush on the shellac. When the wood is completely saturated, start the lathe and burnish the finish with either shavings from the floor or a small piece of paper towel.
You need quite a bit of speed for this process to work. Let common sense be your guide here. The friction of the shavings or paper causes the alcohol to evaporate, and the shellac melts into a smooth finish.
A second coat followed by burnishing and even a third is good measure. Much depends on the strength of the shellac and the wood you are finishing. Open-grain woods will take more coats than close-grained varieties. Be sure to insulate your hands with sufficient shavings or paper towel to prevent burns, and remove the toolrest to avoid pinches.
If you are getting streaks with chips sticking to the work, the solution is too thick. Add more alcohol. Pure carnauba wax is a fine finish in its own right. Carnauba is the hardest of waxes and comes from the leaves of a Brazilian palm tree. It is so hard that it cannot be applied in its natural form. These all have various forms of mineral spirits as a vehicle to apply the polish. Once the spirits evaporate, the wax can be buffed out.
At the lathe, pure carnauba in solid form is a friction polish par excellence, but you must use sufficient speed per the speeds for shellac, above to apply it. Hold the wax against the turning to coat the wood, then use chips or paper towel to melt it into a smooth, glossy coating.
Like shellac, traditional oil finishes have been around for a long time. You can make your own by mixing equal parts of an oil-based varnish, a drying oil such as tung or boiled linseed and mineral spirits.

Wood Frame Construction Condo Japanese Hand Saw Types In China Sjobergs Workbench Accessories Review Best Small Workshop Air Filter 40 |
POLITOLOQ
22.08.2020 at 23:39:59
Rahul
22.08.2020 at 14:46:52
SHEMKIREC_057
22.08.2020 at 23:31:20
FRIEND_DRONQO
22.08.2020 at 20:51:55
bakililar
22.08.2020 at 21:39:32