Jet Air Filtration Manual 20,Cabinet Drawer Slide Release Free,16mm Indexable Lathe Tools Datasheet - PDF Books
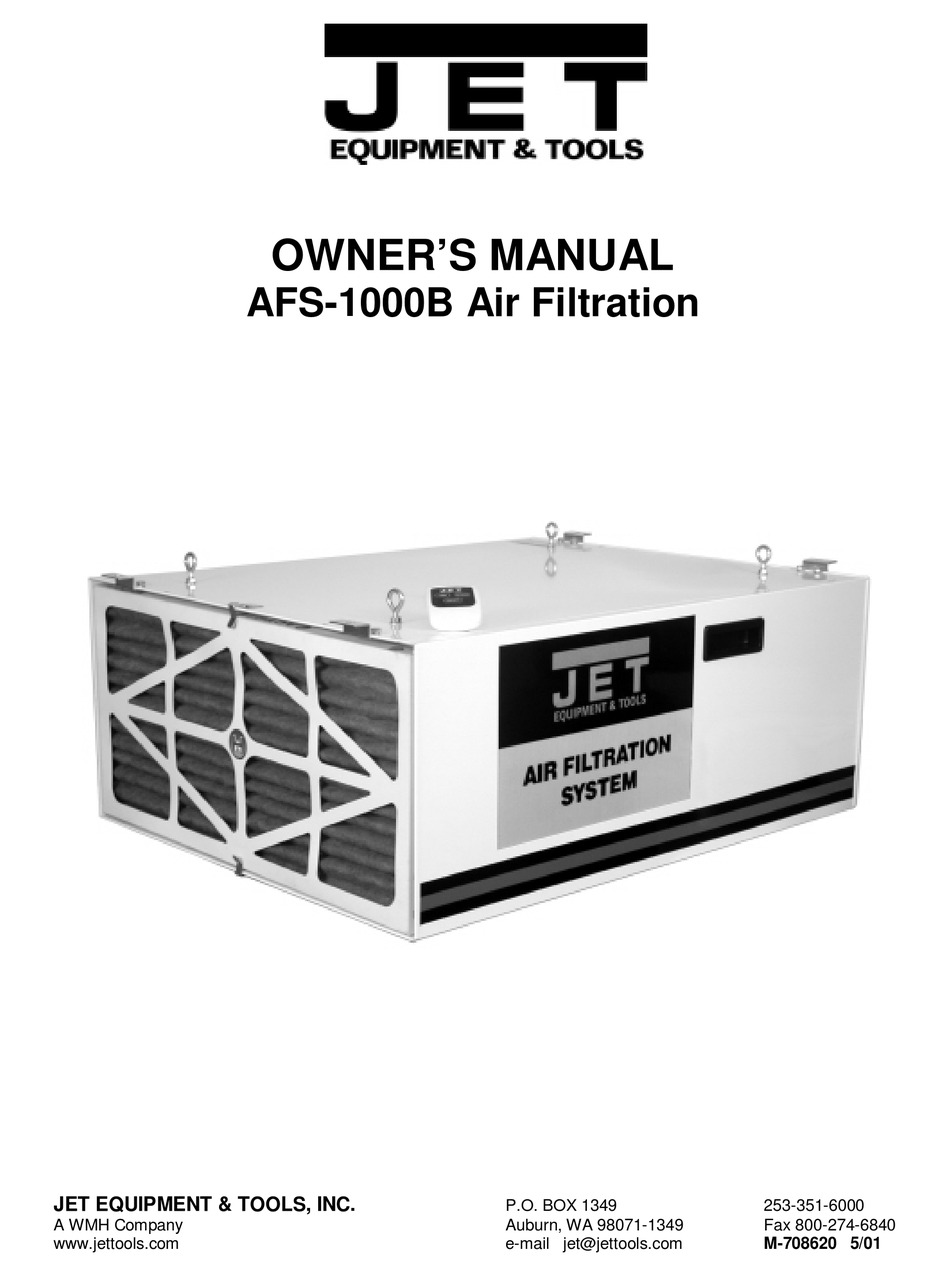
Complete the carbonization process at a temperature of degrees C, with a yield of approximately 80 percent primary carbon. The carbonized intermediate product is then treated with an activating agent such as steam or carbon dioxide steam is most widely used. Steam, at temperatures of degrees C, burns off the decomposition products exposing pore openings for subsequent enlargement.
All pores are not plugged with amorphous carbon, therefore some pores are exposed to the activating agent for longer periods of time. Exposure to the activating agent results in the widening of existing pores, and development of the macroporous structure. Adsorption is a process in which matter is extracted from one phase and concentrated at the surface of another, and is therefore termed a surface phenomenon. Adsorption from wastewater onto activated carbon can occur as a result of two separate properties of the wastewater-activated carbon system, or some combination of the two: 1 the low solubility of a particular solute in the wastewater; and 2 a high affinity of a particular solute in the wastewater for the activated carbon.
According to the most generally accepted concepts of adsorption, this latter surface phenomenon may be predominantly one of electrical attraction of the solute to the carbon, of van der Wads attraction, or of a chemical nature.
There are essentially three consecutive steps in the adsorption of dissolved materials in wastewater by granular activated carbon. The first step is the transport of the solute through a surface film to the exterior of the carbon. The second step is the diffusion of the solute within the pores of the activated carbon. The third and final step is adsorption of the solute on the interior surfaces bounding the pore and capillary spaces of the activated carbon.
There are several factors which can influence adsorption by activated carbon, including: 1 the nature of the carbon itself; 2 the nature of the material to be adsorbed, including its molecular size and polarity; 3 the nature of the solution, including its pH; and 4 the contacting system and its mode of operation.
This topic is considered in more detail elsewhere [1, 2, 3, 4]. The distribution of this area into pores of different diameters is measured by determining the amount of nitrogen desorbed at intermediate pressures. Another method for determining the area of pores above a lower size limit for a given carbon is by measuring the amount of adsorbate of a given molecular size that is removed from solution. For example, the amount of iodine adsorbed from solution has been found to be proportional to the surface area contributed by pores having diameters greater than 10 angstroms.
Similarly, the adsorption of methylene blue and molasses can be correlated with surface area in pores with diameters greater than 15 and 28 angstroms, respectively. Particle size is generally considered to affect adsorption rate, but not adsorptive capacity. The external surface constitutes a small percent of the total surface area of an activated carbon particle. Since adsorption capacity is related to surface area, a given weight of carbon gains little adsorptive capacity upon being crushed to smaller size.
Granular carbons are those which are larger than approximately U. S Sieve Series No. Properties of several commercially available granular carbons are presented in Table Headloss in the carbon contactor is an important design consideration and is affected by tne carbon particle size.
The suspended solids concentration in the wastewater to be treated by the carbon will also affect the headloss and will thereby be a factor in selection of carbon particle size. The particle size headloss design considerations are discussed in detail in Chapter 3.
Simpler adsorption capacity tests such as the Iodine Number or the Molasses Number may also be appropriate. Pilot tests are also considered important. These tests are described in detail in the chapter on laboratory and pilot tests Chapter 4. Abrasion No. Weber, W. John Wiley and Sons, Inc. Hassler, J. Chemical Publishing Co. DeBoer, J. The Dynamic Character of Adsorption. Oxford University Press, Mantell, C.
McGraw-Hill Book Co. In the last ten years, granular activated carbon treatment of wastewater has been demonstrated for both municipal and industrial applications. The process has become much more attractive for widespread use due to the development of economical regeneration methods and equipment.
There are currently two approaches for the use of granular activated carbon in wastewater treatment. One approach is to use activated carbon in a "tertiary" treatment sequence following conventional primary and biological secondary treatment.
Tertiary treatment processes involving carbon range from treatment of the secondary effluent with only activated carbon to systems with chemical clarification , nutrient removal, filtration, carbon adsorption and disinfection. Another approach utilizes activated carbon in a "physical-chemical" treatment PCT process in which raw wastewater is treated in a primary clarifer with chemicals prior to carbon adsorption. Filtration and disinfection may also be included in PCT, but biological processes are not used.
Flow diagrams for some alternate treatment schemes for tertiary and PCT systems are shown in Figures and A detailed description of tertiary and PCT systems currently under design, construction, or in operation is included in Chapter 6. If biological treatment and efficient filtration precede carbon treatment, there are several benefits: 1 the applied loads of BOD, COD, and other organics are reduced allowing either the production of a higher quality carbon column effluent at a given contact time, or the production of equal water quality at a shorter contact period, 2 the applied loads of suspended and colloidal solids are less, thus reducing headless through the bed of carbon, which may aid in solving problems of physical plugging, ash buildup, and progressive loss of adsorptive capacity in the carbon particles after several cycles of regeneration, and 3 the problems of biological growth, septicity, and hydrogen sulfide production may be decreased Jet Afs 1000b Air Filtration System Manual 5g by reducing the supply of bacterial food and oxygen demanding substances applied to the carbon.
The PCT approach seeks to make maximum use of granular activated carbon by extending its function of removing refractory dissolved organics to adsorption of biodegradable organics as well, and, in some cases, by using the granular bed of carbon as a filter to remove suspended and colloidal materials.
With this approach the carbon is loaded as heavily as possible within the limits of effluent water quality criteria. However, it has been shown in several cases that only when biological oxidation, chemical coagulation, filtration, and adsorption are operated in series as separate processes can the effluent quality be optimized. The capabilities of PCX must be evaluated in light of specific effluent quality requirements to determine its applicability to a given problem.
Carbon adsorption and carbon regeneration are basically simple processes, and are therefore quite reliable. Carbon is versatile and may be used in a variety of locations in wastewater treatment plants. There is no single method of contacting or contactor design which is best for all conditions because of the placement of carbon adsorption at different points in the wastewater treatment unit operation sequence, and the varying qualities of wastewater which may be applied to the carbon.
Design, equipment, and material selection may also be influenced by the total capacity of the plant under consideration. There are fewer design variables in carbon regeneration systems, and facilities are therefore more uniform in their concept and design. Also, somewhat more standardized are carbon transport, monitoring, and control systems.
With the requirement for more complete wastewater treatment Jet Air Filtration Manual Youtube there also is a need for greater reliability of unit processes and overall treatment systems. The ability of carbon to continue functioning satisfactorily under certain shock hydraulic and organic loads contributes to its reliability. The need for standby facilities to assure continuous plant operation at full capacity under various service and emergency conditions should not be overlooked.
This chapter presents information intended to assist engineers in the detailed design of granular carbon contacting and regeneration systems and auxiliaries. This information is drawn from theory and the experience gained from the design and operation of laboratory, pilot, and full-scale carbon treatment systems.
Useful operating life of the plant a. Interest rates and the rate of inflation during the life of the plant. Expected population changes in the plant service area. Changes in domestic living habits and consumer patterns i. Changes in levels and types of industrial activity in the plant's service area. Recycle flows within the plant which may amount to 5 to 25 percent of the plant raw flow.
Changes in requirements for treated water quality. One approach is to design the facility for a relatively short term, taking into account only those future events and trends which can be foreseen with some certainty. At the same time, the plant should be constructed so that its capacity can be increased as needed without abandoning or greatly changing the original equipment.
A good way to accomplish this is by using the modular approach to plant design which provides for plant expansion by building new plant units or modules. Physical-chemical treatment plants, and the carbon facilities in particular, are well-suited to the modular design approach. Additional capacity for removal of organics can be provided by adding extra spent carbon storage capacity and by oversizing the regeneration facilities.
In the original design, it is often relatively inexpensive to oversize the regeneration equipment and to operate it initially on a part-time schedule. Application of more organics to the carbon will increase the quantity of carbon to be regenerated; however, there are some savings resulting from continuous rather than intermittent operation of the furnace.
Thus, nonproductive operating costs, such as that associated with startup and shutdown, will be reduced but will be offset by productive operating costs. Since carbon adsorbers readily conform to modular design concepts, treatment plant capacity may be increased by merely adding additional contactor vessels, as required.
The initial facility layout should anticipate future installation of additional contactors and associated apparatus in order to minimize construction costs and disruption of plant operations. Streams of wastewater vary in their volume and chemical composition because of changes in the processes or in the events which generate these streams.
These variations frequently exhibit clearly defined cycles. Municipal wastewater exhibits diurnal cycles corresponding to the life patterns of the population, length of sewer, and size of the town.
Infiltration of ground water or storm water connections may have a marked effect on these cycles. Industrial wastes may be influenced by the working hours of the plants, shift changes, weekend shutdowns, summer holidays, or fluctuations in production rates caused by seasonal marketing patterns.
It is important to recognize that fluctuations occur in the chemical character of the wastewater as well as in its volume.
In the past, the major elements in a conventional plant usually have been designed on the basis of the average dry weather flow expected at the end of the design period, although plant hydraulics may have been designed on the basis of peak hourly flows. In cases of greater-than-average flow, wastewater has often been permitted to pass through the treatment plant as usual.
The increased flow often results in poorer treatment, and an effluent of poor quality may be discharged for a time during the high flow period. One method of avoiding inferior effluent quality is to construct a flow equalization basin preceding the plant. Excess flows or highly concentrated wastes can then be accumulated during surges and later be allowed to enter the plant gradually without impairing treatment efficiency.
Some form of flow equalization may be advisable in any situation where the processes themselves cannot readily accommodate the flow variations, or where it is not economical to provide larger or standby units for the greater capacity requirement.
A detailed discussion of flow equalization facilities is presented in the U. Equalization of the wastewater flow has the following advantages: 1.
The head and flow capacity of pump systems can be reduced with savings in capital investment and the cost of electric power for operation.
The total head for operation of gravity flow units can be reduced for the lower flow rate, thus decreasing construction costs. Lower flow rates will allow the use of smaller pipelines, valves, and meters; and the reduced span of instrument operating ranges may increase their sensitivity and control capability. Carbon contactors may be smaller or fewer in number without exceeding safe design criteria.
If there are effluent requirements for any or all of these parameters, then much of the design criteria must be established by laboratory and bench scale tests as described in Chapter 4. Downflow or upflow of the wastewater through the carbon bed. Series or parallel operation single or multi-stage. Pressure or gravity operation in downflow contactors. Packed or expanded bed operation in upflow contactors.
Materials of construction and configuration of carbon vessel. Steel or concrete. Circular or rectangular cross-section. Countercurrent operation results in the minimum use of carbon, or the lowest carbon dosage rate. Upflow beds may be designed to allow addition of fresh carbon and withdrawal of spent carbon while the column remains in operation. When these operations are conducted almost continuously, the bed may be referred to as a pulsed bed.
A pulsed bed may be either an upflow packed bed or an upflow expanded bed. Upflow packed beds require a high clarity influent usually a turbidity less than about 2. Upflow expanded beds have the advantages of being able to treat wastewater relatively high in suspended solids, and of being able to use finer carbon which reduces the required contact time without excessive headlosses.
Where upflow packed beds typically use 8 x 30 mesh carbon, upflow expanded beds typically use 12 x 40 mesh. The principal reason for using a downflow contactor is to use the carbon for two purposes: 1 adsorption of organics and 2 filtration of suspended materials.
The principle advantage to the dual use of granular carbon is some reduction in capital cost. This economic gain is offset, to an extent not now fully predictable, by loss of efficiency in both filtration and adsorption, and perhaps also by higher operating costs.
The sacrifice in finished water quality which results from combined adsorption-filtration by carbon may or may not be a factor depending upon the effluent quality required. Valves and piping are provided in series installations to permit each bed to be operated in any position in the series sequence, thus giving a pseudo-countercurrent operation. More than two beds in series are seldom used because of the cost of required valves and piping.
Provision must be made to periodically and thoroughly backwash downflow beds to relieve the pressure drop associated with the accumulation of suspended solids. Continued operation of a downflow bed for several days without backwashing may compact or foul the bed sufficiently to make it more difficult to expand the bed during backwash without the use of an excessive quantity of backwash water, i.
Upflow beds may be flushed through a simple well screen inlet-outlet system. Downflow beds require a false bottom support system, backwash facilities, and controls similar to those used in waterworks practice for sand filters. Equipment available for automatic operation of filters is highly developed, reliable, and offers a satisfactory method of process control.
Operation and control of upflow countercurrent carbon columns, following efficient filters, are best accomplished by simple, manual controls. Except for occasional flow reversal, valves serving separate carbon columns are usually operated only during withdrawal and replacement of carbon for regeneration, perhaps once every weeks.
Valve operation for this purpose is best done manually with operator attendance and observation, and is not amenable to reliable automatic control. The use of downflow carbon contactors for the dual purposes of adsorption and filtration provides capital cost savings.
However, the carbon filter-contactor is basically a surface-type filter, and, as such, is subject to the shortcomings of surface filters in processing sewage. Upsets in pretreatment which produce sudden increases in suspended solids or turbidity can completely blind the surface of a single media bed which requires backwashing before it can be restored to service. If the upset in applied water quality continues for an hour or two, then the supply of high-quality water necessary for backwashing carbon filter-contactors may be exhausted.
Separate filters can be backwashed and placed back on line in 20 minutes or less. Backwashing a carbon filter-contactor may require longer and a proportionally larger volume of water of higher quality to avoid plugging the bottom of a deep bed and saturating it with adsorbed organics. Whether using upflow or downflow contactors, filters protect carbon columns from pretreatment upsets and increase the overall plant reliability.
The underdrain system used for downflow carbon beds is similar to that used for conventional water filters and will not be discussed in detail here. Figure illustrates a two-bed series downflow system for carbon contact. As indicated, water is first passed down through Column A and then down through Column B. When the carbon in Column A is exhausted, the carbon in Column B is only partially spent.
At this time, all carbon in Column A is removed for regeneration, and is replaced with fresh carbon. A COL. When the carbon in Column B is exhausted, the carbon is removed for regeneration and is replaced with fresh carbon. With up flow columns, no spare contactors are needed, because carbon can be withdrawn for regeneration while the column remains in service. Gravity versus Pressure Contacting Systems The use of pressure vessels for carbon contactors will increase the flexibility of operation since it will allow the system to be operated at higher pressure losses.
This may allow the carbon contact system to operate during upsets or variations in the wastewater flow. Gravity contactors may be more economical since concrete and common wall construction may be utilized. Examples for the design of both types of systems are given later in this chapter.
With good design of the flow distribution and collection systems, the aspect ratio is not a crucial factor, and ratios of even less than are satisfactory. However, if the granular bed itself is to be used as a means of flow distribution, then high aspect ratios greater than are desirable to minimize short-circuiting and dead spots in the bed. The current trend in design is to provide inlet and outlet arrangements which distribute and collect the influent and effluent water very uniformly across the entire cross-section of the bed, in which case the aspect ratio is not important.
In large plants, this is not a constraint since the physical limitations on individual contactor's size dictate a large number of columns. Shop-assembled pressure vessels cannot be greater than 12 feet in diameter and 60 feet overall length and still be transportable.
At 30 minutes contact, the maximum capacity per shop fabricated vessel is about 2 mgd with more typical designs see Figure corresponding to about 1 mgd per column. Most open concrete contactors will have a maximum capacity of mgd per contactor at 30 minutes contact, as the maximum area consistent with good flow distribution is about 1, square feet.
Thus, for plants of 5 mgd and above, provision of enough contactors to insure plant reliability does not cause any added costs. For small plants, it may be necessary to use two or more columns to provide flexibility of operation even though one larger column capable of handling the entire flow may be technically feasible.
Some operating cost savings may result from the slight additional carbon loading permitted by blending effluents from parallel columns if it is elected to operate the columns in the manner suggested above. The relative economics for various number of contactors for a given situation is discussed in the literature [ 1 ] and this lengthy discussion will not be repeated here.
The first is to provide contact between the water and the carbon grains for the proper length of time. This requires good distribution and collection of the water at the inlet and outlet of the carbon column, which is not too difficult, as any granular bed is, in itself, a good flow equalizer. The shape of the contacting portion of the vessel is not crucial if the water is properly distributed and collected. Of importance in pulsed upflow beds is the function of uniform withdrawal of spent carbon without mixing of partially spent carbon and without "rat-holing" the center portion of the carbon in the column.
A 45 degree cone bottom with strategically located water jets is ideal for this function. In small tanks, a 60 degree cone bottom is preferable. Another function is placement of the makeup and regenerated carbon on the carbon in the column in a layer of uniform depth.
In closed contactors, an inverted 45 degree cone serves the purpose very well. A dished top is cheaper, but the fresh carbon is deposited only in the center of the bed, and thus some carbon efficiency is lost. Another function is the separation of water and carbon at the inlet and outlet of the column. A stainless steel well screen serves this purpose very well in a closed contactor.
For 8 x 30 mesh carbon, a screen opening of 0. In open contactors of a design similar to gravity filters, the backwash collection troughs should be covered with a screen to prevent loss of carbon during backwash. Thus, the diffusional resistance across the film is controlling.
As the velocity is increased, the point will be reached where the controlling effect will be the inability of the adsorbent material to remove the solute from solution as rapidly as it is transported to the surface from the main body of the stream.
Hydraulic loading has an additional effect on carbon column operation. Increasing flow rates through the carbon will cause increasing headlosses AP. Headless is dependent on the flow rate and carbon particle size. Figure illustrates the increasing pressure drop with increasing hydraulic loading for different sized carbons from different manufacturers, operated in a downflow mode. Because of the more favorable headloss characteristics, 8 x 30 mesh carbon is often preferred for downflow beds while 12 x 40 mesh carbon may be preferable for upflow beds because a lower upflow velocity is required for expansion.
The headloss for a given hydraulic loading with wastewater feed must be determined by pilot testing. Since headloss development is such an important consideration in the design of a carbon bed, hydraulic loading cannot be discussed in isolation from several other design factors.
If an excessive rate of headloss development due to a high hydraulic loading is anticipated, an upflow bed should be given consideration. Very high hydraulic loadings are practical only in pressurized systems.
Upflow expanded beds should be considered when high headloss is expected. At low flow rates, the particles are undisturbed and the bed remains fixed. As the flow rate is increased, however, a point is reached where all particles no longer remain in contact with one another, and the carbon bed is expanded in depth. The flow rate required for initial expansion of the bed is accompanied by a sizable increase in headloss.
As the flow rate is increased, there is further expansion of the bed. Flow rates required for further expansion of the bed are accompanied by lesser increases in headlosses.
Figure illustrates the sharp increase in AP for initial bed expansion and the lower rate of increase for further expansion.
Figure shows expansion of 8 x 30 and 12 x 40 mesh carbon beds at various flow rates. It has been found that at about a 10 percent expansion of an upflow bed, suspended solids will pass through the bed.
The rate and frequency of backwash is dependent upon the hydraulic loading, the nature and concentration of the suspended solids in the wastewater, the carbon particle size, and the method of contacting upflow, downflow. The same contactor operated at 3. Backwash frequency may be determined by any of several criteria: buildup of headloss, deterioration of effluent turbidity, or at regular predetermined intervals of time.
It may be convenient for operational reasons to arbitrarily backwash beds at one-day intervals, for example, without regard for headloss or turbidity. The other criteria may only be of interest during periods of shock solids loading when backwash frequency exceeds once per day. The removal of solids trapped in a packed upflow bed may require two steps: first, the bottom surface plugging may have to be relieved by temporarily operating the bed in a downflow mode, and second, the suspended solids entrapped in the middle of the bed may have to be flushed out by bed expansion.
Backwashing a downflow contactor normally requires a bed expansion of percent. Effective removal of the solids accumulated on the carbon surface in downflow contactors requires: a surface wash equipment utilizing rotating or stationary nozzles for directing high pressure streams of water at the surface of the bed, b an air wash, or c a combination air-water wash.
A surface wash or air wash system is normally operated only during the first few minutes of a backwash of minutes. When backwashing is supplemented by this scouring type of wash, the total amount of water to achieve a given degree of bed cleaning may be reduced. Also, surface wash or air wash overcomes bed plugging that may not be alleviated by normal backwash velocities. As a general rule, the total amount of backwash water required should not exceed 5 percent of the average plant flow.
Backwash water may be effectively disposed of by recirculating it into the primary sedimentation basin or elsewhere near the inlet of the wastewater treatment plant. A return flow equalization tank may be advisable in order to reduce shock hydraulic loads on the plant from waste washwater.
This is particularly true for small plants. Air scouring has been used successfully in test programs and appears to be suitable for large-scale use.
It is being used at Colorado Springs [ 2] and it is an accepted technique in water filter operation. For breaking biological slimes from the carbon particles, 5 minutes of air scour should be sufficient. Air must be released when filling the column and the vacuum must be broken when draining a column to avoid structural damage to the vessel.
A detail of a typical air-vacuum release valve installation is shown in Figure The hydrogen sulfide is produced by sulfate-reducing bacteria under anaerobic conditions. Conditions promoting or accelerating the production of hydrogen sulfide in carbon contactors include: 1. Low concentrations or absence of dissolved oxygen and nitrate in the carbon contactor influent.
High concentrations of BOD and sulfates. Long detention times. Low flow-through velocities. It may be possible to prevent or correct problems of hydrogen sulfide generation by eliminating one or more of the conditions necessary to sustain growth of the sulfate-reducing bacteria.
Most of the preventive measures must be provided in the design of the carbon contacting system, but there are also some corrective measures which can be taken in plant operation.
The amount of actual plant operation experience in this regard is limited. In plant design, the following measures may be taken to provide flexibility for dealing with problems of hydrogen sulfide production: 1.
Satisfy as much of the oxygen demand of the wastewater as possible by providing biological treatment prior to carbon treatment. Provide biological treatment and efficient filtration to reduce the load of suspended and dissolved organics thus permitting the use of higher flow-through velocities and reduced detention times in the carbon columns.
In packed beds of carbon, provide facilities for application of chlorine to the influent. In addition, in upflow expanded beds it may be desirable to provide for introduction of air, oxygen, or sodium nitrate as a source of oxygen. Because of the mass of cell growth produced, it may be less desirable to introduce air or oxygen ahead of packed beds because of potential physical plugging of the beds.
These growths are flushed through expanded upflow beds, but may be removed in sections of the plant which follow such as filters or clarifiers. Some remedial measures available in the operation of carbon facilities are: 1. Columns may be backwashed at more frequent intervals or backwashed more violently by use of air scour or surface wash.
Detention time may be reduced by taking some carbon contactor units off the line, provided that the reduced carbon contact time is still sufficient to obtain the desired removal of organics and that headlosses in the carbon columns remaining on the line do not become excessive. Chlorination or oxygen addition may be initiated.
As an example of correction in actual plant scale operation in a tertiary process sequence, an incident at the South Tahoe plant is reviewed. The carbon facilities at this location are provided with all of the design features recommended above. In eight years of carbon column operation, there has been only one occasion in of about three days duration of hydrogen sulfide production.
When the odor was detected in the carbon column effluent, it was observed that plant flow was less than half the design flow, and 7 of the 8 carbon columns were in service. This meant that the contact time was more than 40 minutes rather than the normal 17 minutes. Three of the columns were backwashed with water containing DO and taken off the line.
After two days of operation on this basis, hydrogen sulfide odors were no longer detected in the carbon column effluent. Sulfides in the carbon column effluent can be removed by precipitation with iron or by the addition of chlorine. For applied BOD values substantially higher than this, it appears that use of upflow, aerobic expanded contactors followed by sedimentation or filtration is preferable.
These are the last treatment units except those for breakpoint chlorination in a 15 mgd plant employing chemical clarification, nitrogen removal and multi-media filtration. Reclaimed water from this plant will be blended with desalted seawater for ground water recharge.
Similar carbon columns are being designed for the Similar type contactors have been in service for eight years at the 7. Applied turbidities will range from 0. At the OCWD plant, there are 17 carbon columns each 12 feet in diameter with a 24 feet long straight sidewall. At a plant flow of 15 mgd, 16 of these columns will provide 30 minutes nominal contact with the carbon.
The 17th column is a spare, also to be used for carbon storage. Each of the columns contains 2, cubic feet of 8 x 30 mesh carbon and the hydraulic loading at design flow is 5. Exterior views of these columns are shown in Figure ; details of the inlet and outlet screens are shown in Figure ; Figures and show the top screen system and the carbon filling chamber.
Filtered water enters the bottom of the column through the screen manifold, flows upward through the carbon, and leaves through the upper screen manifold. The hydraulic gradient lies at a level between the top of the column and the carbon filling bucket. This makes it possible to add fresh carbon regenerated and makeup at the top and to withdraw spent carbon from the bottom while the column is in service.
Therefore, carbon can be withdrawn slowly and more or less continuously and replaced with fresh carbon. If carbon withdrawal is intermittent, the usual practice is to withdraw and replace 5 to 10 percent of the total contents of one column at a time. Figure shows the upflow-to-waste cycle of operation which is used after a major transfer of carbon it if is necessary to clear the effluent of excessive carbon fines.
Figure shows the method of reversing flow downward through the column in order to clear the top screens of carbon particles lodged in screen openings. Reverse flow also removes any accumulated trapped particles in the bottom of the bed. Figure merely shows the valve positions for bypassing a column for inspection, maintenance, or repair.
As shown on Figure , a void space of about 10 percent of the total carbon column volume is provided at the top of the columns. Occasionally, the flow to the column can be increased from the normal rate of 6.
By placing the elevation of the point of spent carbon discharge below the top of the carbon filling chamber on the column, it is possible to withdraw spent carbon by gravity flow from the column while it is in normal service. If more rapid transfer is desired, the wafer valve at the top of the column below the filling chamber may be closed and the entire column pressurized with high pressure water supply for carbon removal.
Note that a pressure supply of dilution water is provided through a pipe cross at the bottom of the column. This allows water to be added as necessary to obtain the desired carbon slurry consistency for hydraulic transfer.
The contactor is also equipped with a transfer jet header which furnishes pressure water through eight tangential nozzles at the top of the bottom cone. Royal Thai Air Force. Archived from the original PDF on 15 August Retrieved 28 October Reed Business Information.
Retrieved 23 February Dagens Nyheter in Swedish. Archived from the original on 8 October Archived from the original on 19 October Archived from the original on 17 January Retrieved 6 May Seven air forces operate or are committed to operating Gripens, along with one British Gripen D test aircraft.
Archived from the original on 20 October Folha de S. Paulo in Portuguese. Archived from the original on 24 May Economia in Portuguese.
Retrieved 19 March Reuters in Portuguese. Le Parisien in French. Archived from the original on 28 December India Today. Rio de Janeiro. Archived from the original on 30 November Retrieved 30 November Washington, DC. Archived from the original on 2 December The Aviationist. Airway in Portuguese. Air recognition. March Sydsvenskan in Swedish. Strategic Intelligence Service. Intelligence briefs. Archived from the original on 5 August Defence Web report.
Archived from the original on 31 January CBC News. Retrieved 30 August Archived from the original on 26 February — via Jane's Ottawa Citizen. Info defensa in Spanish. Retrieved 12 June Archived from the original on 3 April — via Jane's Finland: Ministry of Defence. Archived from the original on 23 July Retrieved 14 June The Finland Times.
Archived from the original on 20 July Retrieved 13 May Archived from the original on 16 February Retrieved 16 February Jane's Defence Weekly. Tampere-Pirkkala Airbase. Archived from the original on 6 April — via Jane's.
Archived from the original on 13 March Retrieved 15 March Archived from the original on 28 March Archived from the original on 6 February Free Press Release. Archived from the original on 9 October The Times of India. Business Standard. The Voice of America. Archived from the original on 19 April India Times Economic Times.
New Delhi. Archived from the original on 23 November SPS Aviation. Philippine Air Force. Retrieved 21 December Archived from the original on 14 June — via Jane's Manila Standard. Philippines News Agency. They are Botswana, Namibia and Kenya]. Archived from the original on 6 January Archived from the original on 29 April Sofia, BG. Archived from the original on 18 December Sofia: Reuters. Archived from the original on 22 December Retrieved 10 July The Copenhagen Post.
Archived from the original on 23 October Retrieved 23 October The Economic Times. Archived from the original on 11 April Archived from the original on 18 January Retrieved 5 February The free library Press release. Archived from the original on 24 January Nederlandse Omroep Stichting in Dutch. Archived from the original on 22 January Retrieved 22 January NRC Handelsblad in Dutch. Archived from the original on 6 August NO : Prime Minister's Office.
Archived from the original on 5 January Retrieved 9 June Archived from the original on 12 June E24 in Norwegian. Archived from the original on 22 August Retrieved 27 July PL : Ministertwo Obrony Narodowej. Archived from the original on 1 September Bankier in Polish.
Konflikty in Polish. PL : WP. Archived from the original video on 12 January F zamiast F" [Boeing interested in the Polish market. F instead of F]. Defence 24 in Polish. Archived from the original on 14 November Retrieved 5 June Archived from the original on 7 February — via Jane's Archived from the original on 11 July Retrieved 11 July Retrieved 13 July — via Petit Press.
SE: Sveriges Television. Archived from the original on 1 December Switzerland: SAF. Le Matin in French. Space War. Archived from the original on 11 September Archived from the original on 21 January Retrieved 22 August Gripen news. February — via Twitter. Tages-Anzeiger in German. Switzerland: Schweizer Radio und Fernsehen.
Switzerland: RTS Info. NZZ in German. The Financial Times. SRF in German. Anyway, it is the first model in M. Cologne, DE. Swiss Info. Archived from the original on 28 January Retrieved 2 February — via Jane's Archived from the original on 13 June — via Jane's Washington, DC: Sight line.
Archived from the original on 22 October Retrieved 22 October Last summer saw the successful conclusion of a deal with Oman for 12 Typhoons.
After canvassing the Israelis, the Dutch, and even the Americans for offers, Romania finally settled on Fs from Portugal in September E24 in Swedish.
Archived from the original on 29 September Business Insider. Archived from the original on 9 March For the combat role, this version will be optimised to enable air battle management from the back seat, including jamming, information warfare and network attack capabilities.
Retrieved 21 December — via Jane's The Gripen Aggressor is essentially a newbuild Gripen C that has had its offensive weapons capability including the internal cannon removed. While it is currently modelled on the single-seat Gripen C, Smith noted that a twin-seat Gripen D version could be offered if a customer requested it. Archived PDF from the original on 18 March Saab has launched a new derivative of its Gripen C, which it believes is ideally suited to meeting the future adversary training needs of the UK and USA.
April Archived from the original PDF on 26 July Retrieved 26 July Archived from the original on 26 July Retrieved 26 July — via Jane's Archived from the original on 22 July Archived from the original on 15 November Retrieved 15 November Bangkok Post.
Photos of the week. Retrieved 29 August Aviation Safety Network. Flight safety foundation. Retrieved 24 July Note page has two entries for 31 May accident with the same serial number. Minnen [Memories] in Swedish. SE: Sveriges Radio. Retrieved 6 October Minnen [Memories] in Thai.
Retrieved 8 July Swedish Armed Forces. Oil Change Oil Filter Removal Oil Filter Jet Air Filtration System Afs 1000b Manual Spec Installation Oil Filter Replacement Page T8: 5. Pump shaft bearing inside Before starting the engine for the first time, add oil: The engine is shipped dry. Page Pressurized Lubrication System Apply silicone sealant to the threads of the pressure switch and tighten it, or tighten the oil passage plug. If there is any damage or uneven wear, replace them with new ones.
If the diameter is less than the service limit, replace the pump shaft with a new one. If necessary, put the ball in position and lightly tap the ball with a suitable tool to form a perfect seat. Page Crankcase Cover Removal Crankcase Cover Installation G: Apply grease. O: Apply engine oil.
S: Follow the specific tightening sequence. Screw 2. Page Specifications 1. Crankshaft Journal Bearing Sealant - Kawasaki Bond Silicone Sealant : FHV, V Page Cleaning Replace the crankcase with a new one if the inside diameter is greater than the service limit.
A sealed-type crankcase emis- sion control system is used to eliminate blow-by gases. The blow-by gases are led to the breather chamber through the crankcase and the camshaft. If the journal diameter is less than the service limit, re- place the camshaft with a new one. Starter System Starter Motor Removal Starter Motor Installation Starter Motor Disassembly Starter Motor Assembly Starter Motor Brush Inspection Brush Spring Inspection Armature Inspection Yoke Assembly Inspection Pinion Clutch Inspection Commutator Groove Depth approx.
Replace it with a new one. If the grooves are shallower than the specified limit, re- place the armature with a new one. If the grooves are only dirty, clean them carefully. Commutator Groove Depth Limit 0. Bad [A] Charging System Learn and observe all the rules below. This will burn out the diodes in the electrical parts. A tester other than the Kawasaki Hand Tester should show different readings.
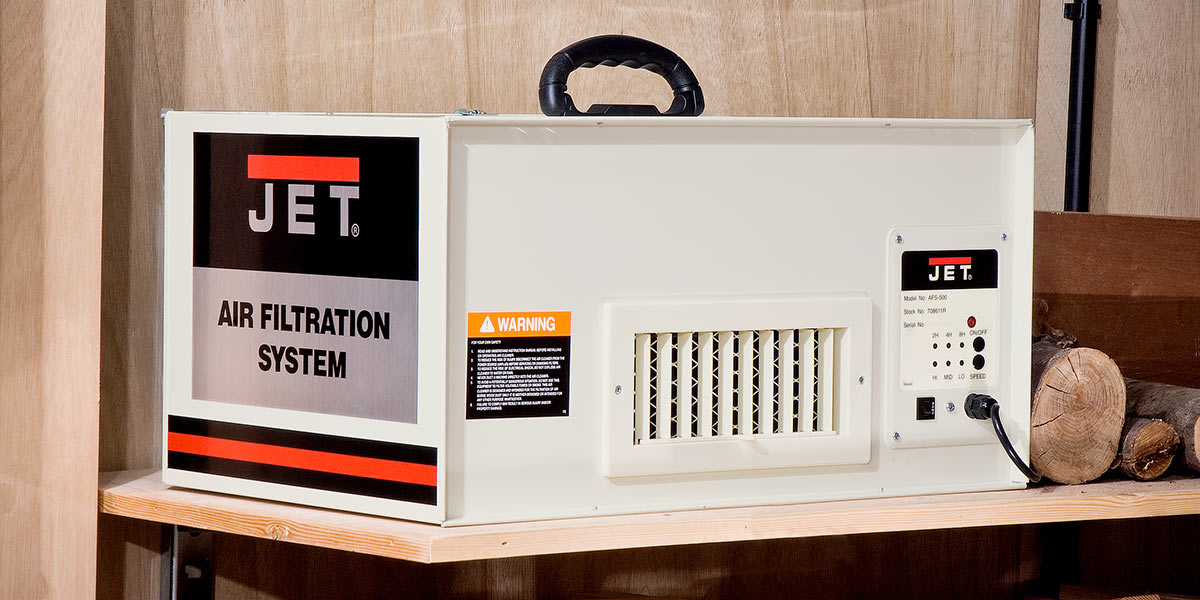
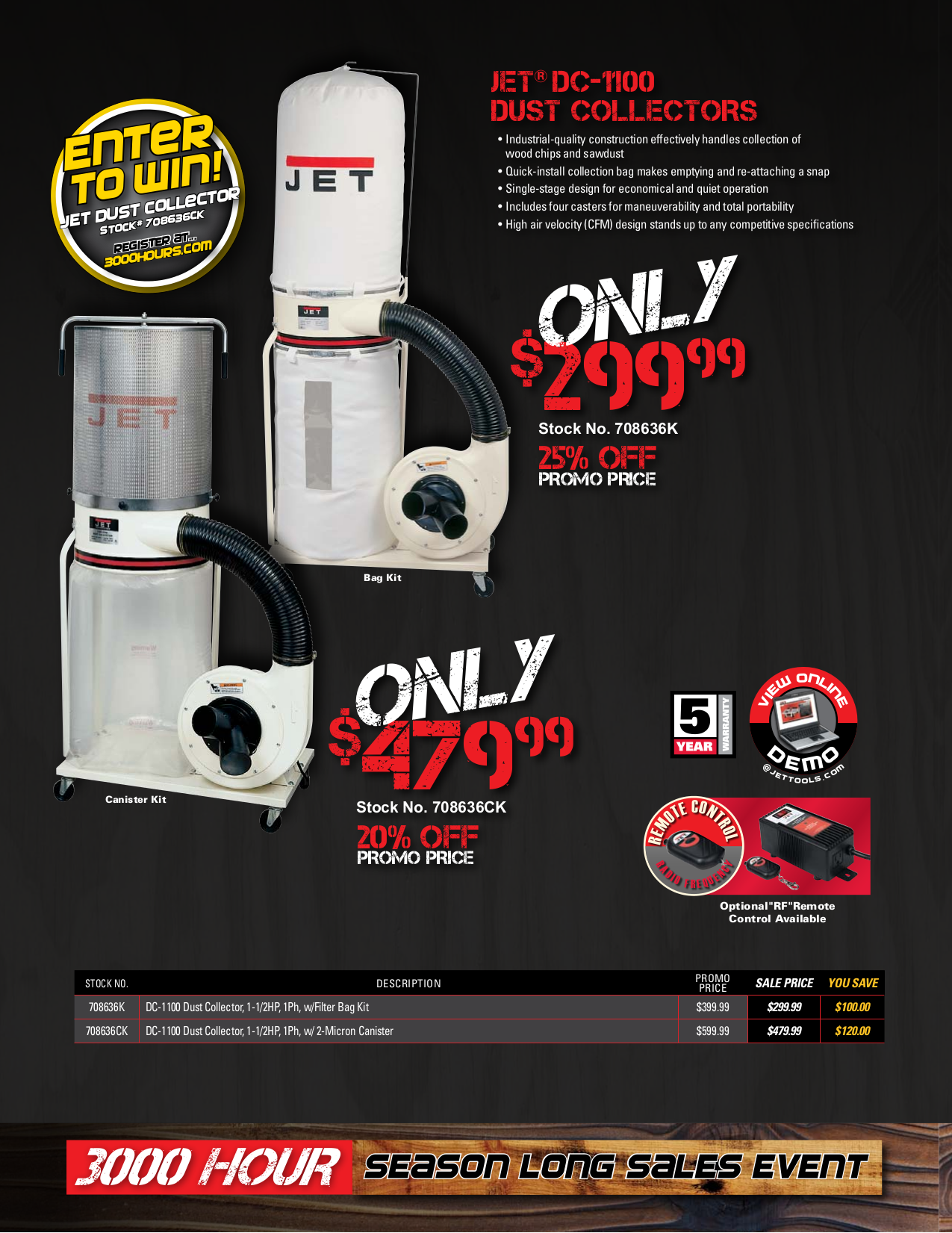
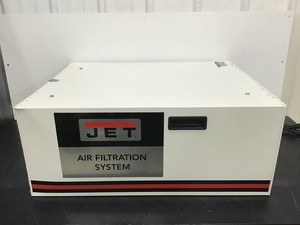
Cool Woodworking Pictures Video Woodworking Tools Craft Supplies Quote Sharpening Grinder Jig Model |
1
23.09.2020 at 19:43:46
OnlyForYou
23.09.2020 at 10:57:35
VIDOK
23.09.2020 at 21:46:22
LLIaKaL
23.09.2020 at 20:34:47
AtMoSFeR
23.09.2020 at 14:41:45