Slot Cutting Router Bit Harbor Freight Up,Great Wood Projects Pdf,Wood Employee Share Plan Rate - 2021 Feature
Using your ratcheting crimpers, crimp on a wire disconnect and connect it to the NO terminal on the switch, then route your wire to an imput on the ipac.
THis needs done for each microswitch. Once that is done, you need to connect a ground wire to every GRND terminal on every switch. These do not need to be discrete wires, you can chain them together. You will be crimping a ton of connectors. Take your time to route the wires nicely, you will thank yourself later.
Mount your trackball into the mounting plate and connect it to your usb mouse interface. The one i used also has LED lighting that needs to be connected to a 5v and ground.
The Optiwiz that came with my trackball provides this. There is planty of space inside the base of the cabinet to store a PC. I don't plan on going into great detail on setting up the PC, there are many other sources for this info.
This instructable was for building the cabinet. If you need more inspiration or assistance, check out the forums at arcadecontrols. If you followed the instructions, you should end up with an awesome 4 player pedestal cabinet.
Here you can see the final product, with the original sketchup render. Thank you for the excellent write-up! My son and I are in the process of building a similar cabinet and have all the parts and tools, but I was unsure how to best drill the button holes in the plexiglas. I am going to use your method as it's brilliant. Yours looks great! Reply 5 months ago. Reply 4 months ago. It went very well. Here is a picture of the finished product.
There is a trackball, a spinner, and controls for two players. Looks awesome! No regrets :. Thank you for this! My son and I both built one—his cabinet according to your plans and mine on a sit-and-stand desk frame. Thank you! Tip 5 months ago. Just found out this cabinet is not deep enough for ultimarc J ball joysticks with Led upgrade. Hello, How do you figure out the angles for the game stick panel? How about if I am making a smaller version; a two player instead?
Thank you. Reply 11 months ago. I didn't do anything complex, i just looked at it and decided how i thought it should be. Reply 10 months ago. Question 1 year ago. Question 1 year ago on Introduction. Hello do you have any measurements of your button layout I have the same measurements as your panel I like your lay out. Question 1 year ago on Step What is the alignment from the top and how far in are your Sticks, Buttons, Trackball?
Do you have a psd template or cad file of the CP template? Answer 1 year ago. I do not have a template for control locations. I did it the hard way with a ruler and a compass. What thickness did you go with for the t-molding? I am curious how thick you did it for the top so that the t-molding held in the plexie glass.
Instead of cutting the slot in the center of the mdf, I offset it towards the top by the thickness of the plexi. That way the molding lines up with the top surface of the plexi. I used a round over router bit on the bottom side of the mdf so that you don't have any sticking out below the molding. The same principal can also be adapted to hold pipe clamps.
Router planes are amazing tools, but they are also largely misunderstood. And that's a shame, because they are extremely useful in both a hand-tool and a power-tool workshop.
Rather than cutting profiles, as a modern router does, a router plane is for cutting to depth with precise accuracy. They can be used to make the bottom of a table saw dado perfectly flat. They can fine tune a rabbet or a tenon. They are the perfect companion to many power tools with nearly unlimited uses. What started out as a way to safely hold small parts while working at the router table, became a multi-functional sled that will accomplish several tasks safely and accurately.
It's a small parts holder: it's a coping sled for routing on the ends of narrow work pieces rail and stile construction, tenons, half laps, etc.
This sled is surprisingly easy to build, and the plans give you all the information you need, including step-by-step instructions complete with photos. Every workshop should have at least one saw bench. This version of the classic saw bench includes some extra features. There are holes for holdfasts to secure your work while you drill or chop sitting down.
But the best part is it can be built with some old construction lumber! A mini cyclone designed to keep your filter clean and your vacuum working hard!
There are commercial versions on the market, but ours is easy and inexpensive to make, and will mount directly on your vacuum so you don't have to pull a separate bucket around.
Vacuum surgery is optional, and we walk you through the whole thing! This jig is simple and inexpensive to make, but well thought out to provide a surprising level of functionality.
It may be used with a plunge router and an edge guide to create accurate, repeatable mortises. You can cut tricky ones too, such as double mortises, parallel mortises and even mortises in round stock. Stop sawdust boogers forever! This downdraft table is an all in one solution for a small shop with a big 20" X 30" work surface complete with an embedded t-track holding system. Not only will it tame the sawdust, it has countless other uses for securing your workpieces with clamps, stops, risers and hold downs for sanding, cutting, routing carving There are lots of ways to cut miters, but most involve setting the angle of a guide or jig.
If you set it imprecisely, you'll have problems. Why not have a sled dedicated to the most common miter angle you use, degrees?
This fence is truly unique with an innovative locking system that self squares to the blade, a micro adjuster for fine tuning your cuts, and an anti-kick-back European style with detachable extensions. Even the rails are made from wood! It's designed to fit any saw from small, bench top units to large cabinet saws, with or without side tables.
This project can be used on its own, but it is also designed to fit our deluxe table saw workstation. This set includes ALL THREE of our deluxe table saw sled plans, including the large "Mega Sled," the more compact "Mini Sled," and the deluxe "Miter Sled", plus all the joinery jig attachments including a finger joint jig, a pair of dovetail jigs, a tenon-cutting jig, a jig for cutting spline slots to reinforce frames and boxes, and spring activated micro-adjusters to fine tune your cuts.
It is by far the most capable table saw sled system around! This is the larger of three table homemade saw sleds I use in my shop. I call it the "Mega Sled" because it will do it all including crosscutting large panels and cutting various types of joinery. It includes plans for a clever system of joinery jig attachments including a finger joint jig, a pair of dovetail jigs, a tenon-cutting jig, a jig for cutting spline slots to reinforce frames and boxes, and spring activated micro-adjusters to fine tune your cuts.
It is by far the most capable table say sled system around! This is the every-day user out of of three homemade table saw sleds I have in my shop. I call it the "Mini Sled" because it it is a smaller, easier to pull out and stow away version of the big "Mega Sled" - but it is almost as capable.
The Europeans have had a secret for years- their saws have sliding tops for easy and accurate crosscuts! So why not make your own? This one mounts to the side of your contractor or cabinet saw for smaller saws, use with the TS Workstation and includes an adjustable miter fence, even a storage drawer. Great for working with plywood panels! This is the ultimate table saw improvement!
Not only does it add a giant work area to your bench top or contractor style saw, it can be combined with some of our other homemade tools to create an entire workshop in a 4X8 foot area!
There are also sixteen drawers, several storage shelves, and room for various other small machines. Add a bench top drill press and a mini lathe, you name it! There's even a built in lumber rack, for goodness sake! This idea came from a trip to a home center to buy one of those pedestal drawer units that go beneath front-loading washers and dryers. I knew I could do better!
This one is designed for both machines. It has a lot more drawer space than the commercial versions, it's on wheels so it can be moved, and it was carefully engineered to support the tremendous weight on top for years and years to come. Best of all, it'll cost you just a fraction of price of the store bought units! This is a great project for a beginner because it requires only a circular saw and utilizes materials you can buy in a home center.
Turn your Worksharp sharpening system into a super-sharpener for all of your woodworking needs. These modifications include replacing the glass discs with inexpensive alternatives, using buffing compounds instead of the pricey sandpaper, and a stand that not only includes storage for all of your discs and accessories, but includes a large platform to make it possible to sharpen wide plane and chisel blades with a simple honing jig!
These changes are easy to do and will make your Worksharp do a lot more, plus save you a bundle! About Company A truly unique digital publication for the everyday woodworker.
Lost Password? Create Account. Recent Posts So, you think you know how to sand, eh? I destroy a chisel to see if the Tormek is too slow Burning wood with a table saw Is the frame and raised panel obsolete? Should you hate sapwood?
Woodworkers Are Saying. Etiam tincidunt ligula tellus. Vestibulum vitae justo malesuada, eleifend justo vel, dictum turpis. Youtube Review. Facebook Review. Sign In Register.
Plans Swag. View as:. Quick View. Homemade Machines , Plans. This band saw is BIG on everything except size. It features a full 24" of throat capacity, yet it's small enough to fit on a bench. It's loaded with features that even the commercially made saws lack, like a built in sliding crosscut table, ball bearing blade guides, and a unique dust collection manifold.
You can use common "" blades and the best part is, it's made almost entirely from wood! Plans , Router Jigs , Shop Projects. This rack was created with that in mind. It is designed to evolve with your collection. Not only can you move the bits around, you can also move the holes! This may be the last bit rack you ever build! Hand Tool Jigs , miscellaneous , Plans. Homemade Machines , Joinery Jigs , miscellaneous , Plans.
This machine was born out of frustration! Stumpy had a cheap hand-held biscuit joiner that he picked up on a whim at Harbor Freight.
The problem with cheap units like that is the difficulty that comes with making an accurately placed slot without the tool rocking out of position during the cut! So, like any good woodworker, Stumpy set out to find a solution. The scraps I had were just barely large enough to cover the ring, and as you can see in the pic, it barely had room for the groove.
I then measured the inlet of the fan housing, and cut a hole in the center that would fit snugly. I noticed that the square outlet on the fan housing was preventing it from seating fully, so I notched the top of the disc.
I tested it to make sure it was a nice flush fit, and then used some construction glue to attatch the upper disc to the fan housing, creating an airtight seal.
Being that the barrel and center ring aren't perfectly round, and it needs to be close to an airtight seal, I wanted to form some sort of gasket where everything fit together. I decided to lay a bead of silicone caulk in each of the three grooves I had routed, and then used my finger to smooth them into a convex shape that would help contour to the mating parts. This creates a flexible and airtight seal.
The silicone takes 24 hours to fully cure. After letting the silicone cure, I put everything together. One of the reasons I didn't attatch the center ring to the base disc is that I want to get the alignment right first.
I placed the bottom disc on the barrel, and then placed the center ring on top of the disc. I put the inlet of the ring in place above the solid portion, emmulating the Thien design. I just guessed at proper placement, and then made temporary reference marks on the outside of the center ring and disc.
This way I have a starting point, and can adjust the alignment in either direction Slot Cutting Router Bit Harbor Freight Mod to get maximum perfomance. Once I get it tuned up, I can make permanent reference marks or even attatch it permanently so that it's perfectly aligned every Slot Cutting Router Bit Harbor Freight Forum time.
Then I mounted the top disc with the fan and motor assembly. I used the short length of flexible hose that came with the dust collector as a vent. I wasn't comfortable installing it permanently just yet, so I just ran the vent hose out the nearby window for now. I plan on using a dryer vent for the final permanent installation.
I simply removed the switch box, and rotated it degrees, so that it's now right side up and facing the right direction. The only modification required was to drill a new hole in the mounting plate for the wires that run from the switch into the motor.
I hooked up a length of hose and ran a few tests with some of the machines in my shop. I ran a few boards through the planer, the jointer, and the tablesaw. The airflow and collection seem to be as good if not better than the stock set-up. I then had a helper stick the hose straight into a large pile to sawdust while I watched the exhaust outside. There was a visible amount of fine dust coming out, but it was surprisingly small.
All of the chips, and the vast majority of dust were collected in the barrel. During most normal operations there is so little dust being exhausted that it can't be seen with the naked eye. Sucking up a large pile of dust, or taking heavy passes with the jointer or router table will create enough fines that the exhaust is visible, but just barely.
I currently have most of my equipment on wheels, and they are all set up at the same height in order to use the same outfeed table behind my tablesaw for everything. This makes it practical to install the dust collector near the outfeed table, and just use one 10' flex hose for everything. I may install permanent ducts sometime in the future if I ever expand my shop, but this set-up seems to work well for now. The only machine the hose doesn't reach is my bandsaw, but it doesn't create much dust, and I think the higher static lift of my shop vac works better for my bandsaws dust hood set-up.
I made a few modifications to my contractor style tablesaw in order to get more efficient dust collection with the new set-up. I used a piece of hardboard with magnets to form an enclosure for the back of the saw.
I also used some magnetic sheet material old car magnets to reduce the gaps between the frame and the table top, as well as the slot on the front of the saw. These can all be easily moved for making bevel cuts. The last modification was to drill a hole in the ZCI just behind the blade to help reduce above the table dust.
This has reduced above table dust by about half. Everyone who is venting outside, where are you getting your make up air? I want to vent outside via laundry vent but am stuck on the make up air part. Just curious what others have done.
Reply 2 months ago. Reply 3 years ago. Reply 4 years ago. Interesting that this project is being shown now as if it were a new instructable, but some of the comments are 6 years old. Must be a rerun of something that is old. Reply 5 years ago. Yeah, the newletter's servings of DIY are kind of like reaching into an extemporaneous grab-bag full of magic 8-balls.
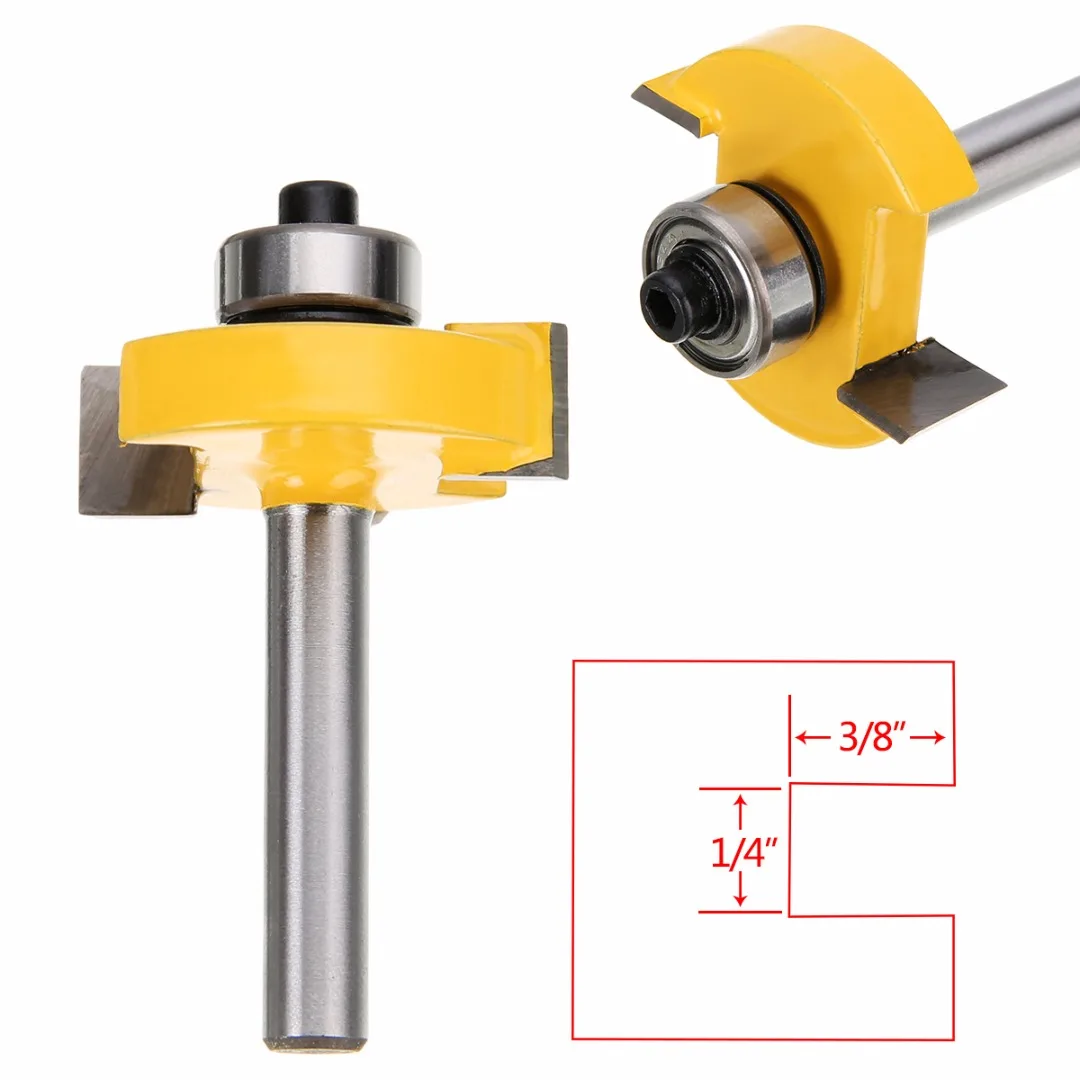


Hockey Puck Bench Block Woodworking Hand Tools For Sale Uk List Pocket Hole Jig Trinidad 6th Miter Gauge T Track Location |
4004
17.03.2021 at 21:47:20
ILQAR_909
17.03.2021 at 14:27:17
Skarpion
17.03.2021 at 16:32:21
V_I_P
17.03.2021 at 14:20:43