Lathe Turning Tools Explained Gas,Dining Room Table Legs Wood Repair,Wood Furniture Plans Free 00,Pantry Drawer Slides Home Depot Gate - Test Out

Accommodation of Standard Technical Measures Lathe Turning Tools Explained 12 It is Company policy to accommodate, and not interfere with, standard technical measures it determines are reasonable under the circumstances, i. Click here - to use the wp menu builder Click here - to use the wp menu builder. Where Are They Now? Want More? Sign Up for Our Newsletter!
Follow hollywood. Patrick's Day movies to watch today plus drinking game ideas 46 thoughts I had while watching The Bachelor finale as a superfan 46 thoughts I had while watching The Bachelor finale as a non-fan. Copyright Issues Hollywood. Troubleshooting brake problems helps you to determine the faulty component, the type of problem, and other aspects.
Brake rotors are simple components. Not even power cables. Which makes them easy to troubleshoot. The components are also easy to access. All these attributes make the procedures to check a brake rotor for issues quick and less challenging. If you notice any symptoms to indicate a bad rotor such as a pulsating brake pedal, you may need to carry out inspections to confirm the problem. Here is the procedure to do so. Grooves appear as ridges on the frictional surface of the Lathe Turning Tools Explained 65 rotor.
They are an indication of excessive wear. In most cases, these mean a rotor that needs to be changed. These can be seen on the rotor surface without any difficulty.
They can be as tiny as hairlines to wide openings. Wide cracks should be a cause for worry and an indicator of a rotor that needs to be replaced. Hairline cracks, on the other hand, may not be a major issue. This is noticeably by looking closely at the edge of the rotor. It mostly happens when the rotor has worn to reach the allowable thickness.
Should you find rust on the rotor, determine its severity first. Should you notice corrosive rust on the rotor, the only option is replacement. Heat spots result from brake pad material that accumulates on the rotor surface and turns into cementite. This is a very tough substance causes localised heating on the rotor surface.
This leads to heat spots which are raised areas that cause vibrations during braking and a weak rotor structurally. If the heat spots on the rotor surface are extensive, a replacement becomes necessary. You cannot determine the level of rotor warping simply by looking at the surface. You need to use an instrument and a dial indicator is the right tool for that. You can also use a simple method to find out if the brake rotor is warped.
This may come in useful if a dial indicator is not immediately available. A gap indicates warping. Do this on both sides of the brake disc. Usually, brake rotors will have the values for thickness specs indicated by the manufacturer. The rotor must within those specs for it to function properly and safely.
To confirm brake disc thickness, you need a micrometer. Take measurements from different spots and compare the readings. The least value should be above the minimum thickness recommended by the manufacturer. If lower than that, the rotor needs to be discarded and a new one installed. However, the micrometer is more accurate and the most recommended. After you have found out about the problem with the rotor, the next step is determining whether to replace it or correct the imperfection.
If you decide to replace it by yourself, you may want to know the process to carry out brake rotor replacement. Not every damaged brake rotor has to be replaced. Sometimes, the problem is only superficial and can be corrected easily. A few raised spots, for example, can be cleared and a flat braking surface created. Some brake rotors are expensive components, and the cost to buy a new one may exceed the cost to fix it. In such situations, it would make economic sense to opt for repair rather than replacement.
Brake rotor repair is called resurfacing, machining or rotor turning. Resurfacing corrects a vibrating brake system, pulsating brake pedal, and many other problems that result from an improperly worn or damaged brake disc.
Brake rotors may develop uneven surfaces for various reason. This is not desirable as it causes unwanted vibrations and reduced braking efficiency.
Unless the rotors have reached the minimum allowed thickness, the surface can be put in a machine that removes the raised parts to create a perfectly smooth surface. The procedure creates a new surface, much like that of a new rotor. Brake disc resurfacing involves removing some material off the surface, at the frictional surface. The idea behind it is to clear imperfections to make the surface uniformly even. This procedure is best done by a qualified person on a lathe.
Although not advisable, there are vehicle owners who prefer the DIY way by purchasing a brake disc resurfacing tool. This is a simple machine that can be used to machine a rotor.
A better option would be to remove your brake disc, take it to a shop that turns rotors, have it turned to the right levels and specs then re-install it. Brake rotor machining comes with benefits and disadvantages. Often, the type and level of damage determine whether to resurface or replace a brake rotor.
But there are times where you can be in a dilemma as to which option is the best for your situation. Here, let us take a look at the pros and cons of both rotor resurfacing and replacement. Resurfacing a brake rotor is significantly cheaper. If you have several bad rotors to repair at the same time, rotor turning can be a financially sound option.
But then, machining removes material off the rotor surface and could reduce the thickness considerably. Such a rotor would also be liable to cracking and breakage.
Replacing a rotor may cost a lot, but suitable if you have the budget for that. New rotors conform to all the manufacturer specifications, which means they offer better performance and for long. Rotor replacement is also more convenient when compared to the hassles of machining, plus it gives you the option to upgrade to a better type of brake rotor.
Learn about how to do that in the next chapter. Replacing a brake rotor gives new life to the brakes. In most cases of brake disc damage such as warping, replacement offers a longterm solution. Generally, you know that a brake rotor requires replacing if you notice excessive wear or damage. Damage could be in the form of deep scoring or raised areas that are too pronounced. Also, if the wear has reduced the brake disc thickness so much that machining it risks exceeding the discard thickness specification.
Unlike brake rotor resurfacing, replacing a brake rotor is a simple process that can even be a DIY task. You do not need any special skills, and neither do you require many tools. Here is how to do it. What is the average lifetime of a brake rotor? The average marriage is usually 30, to 70, miles but which can vary due to the factors mentioned. Can you change brake pads without changing the rotor? Brake pads are made from a softer material than brake discs.
As a result, they wear at a faster rate and require frequent replacements. Often, many vehicles owners find they have to replace the pads as many as three times before they need to change the rotor. What is the average rotor replacement cost? Expect to pay a few hundred dollars to have a rotor replaced but which can be higher if the rotor model is high-end. Carrying out the replacement yourself can save you more than a hundred dollars.
Is brake rotor resurfacing better than installing a new one? Resurfacing only prolongs the rotor lifespan for a limited amount of time. How long do brake rotors last after resurfacing? It also depends on the wear or level of damage before the rotor was turned. Brake rotor machining exposes the surface to warping risk due to the reduced ability to handle extreme temperatures.
The rotor cannot, therefore, be expected to last for long. Do new rotors need to be resurfaced? Some manufacturers advise against machining new rotors, saying the components are ready to be used in the condition they come in. Others recommend that vehicle owners turn the rotors before installation. But then, there are rotors that do not come with ready frictional surfaces and if not machined, do not break-in properly.
That can result in problems with brake pad materials and cause raised spots that lead to vibrations and weak braking. If the new rotor comes with a smooth surface, you may not need to turn it before installation. What is the idea behind sanding rotors for new pads? Basically, sanding helps to remove raised spots and improve the surface finish. The result is fast seating of the pads and a better feel at the pedal when braking.
Removing raised spots also helps prevent rapid or uneven wear of the pads. Replacing a brake disc offers many benefits. You can do it yourself or, if unsure, seek the help of a mechanic. Brake rotors are simple components yet among the most essential in the brakes of modern automobiles. Proper maintenance of the brake rotor is, therefore, paramount. It ensures the braking system performs at an optimum and consistently. Taking care of this component requires that you have adequate knowledge about it, and we hope that this brake rotor guide provided you with that.
You now know what function the brake rotor serves and the different designs that you will find on the market. You also understand what braking problems are caused by a bad rotor and how to go about correcting them. Furthermore, you can now make a wise decision when choosing between resurfacing and replacing a failing brake disc. And if you have to install a new one, what rotor type suits your vehicle application and driving conditions. Your email address will not be published. Save my name, email, and website in this browser for the next time I comment.
Your Name. Your Email. Your Message. Source : YouTube. Submit a Comment Cancel reply Your email address will not be published.
Search for:. I first encountered a decompression valve on a Sears moped I bought when I was 14, so there is nothing new about this idea. They definitely make starting easier because you are not coming up against TDC at the beginning of the recoil rope pull.
You get the cylinder moving and have inertia working for you before you hit resistance. The decompression valve on the Magnum is a dandy. It is easy to get to, but is not hit accidentally and does its job handily.
You push it, and it does its job, closing at the first cough of the engine. Before you push the decompression valve and pull the recoil handle, the Master Control Lever needs to be set.
This takes a bit of getting used to. For a cold start you must first set the choke, and this involves pushing the throttle lock with your right thumb and then triggering the throttle with your index finger while pushing the Master Control further down.
It will only move to this starting position with the throttle advanced. The throttle trigger must be released before releasing the Master Control Lever for everything to stay set correctly. It sounds a lot more complex than it really is. I employ a ground start for a cold engine, but after pushing the decompression valve, it generally takes no more than two pulls for a good start.
Not needing a small screwdriver to tweak carburetor idle and richness is a bit unnerving at first, but you soon revel in being unburdened. M-Tronic even stores your starting parameters for a variety of situations and rolls them out as needed.
You grow to love the Wagnerian Nibelung under the hood constantly tweaking better than you could do it yourself. A third leg of the starting tripod is the Pre-Separation Air Filtration System which keeps the paper air filter noticeably cleaner. It works much the same as a two stage dust blower by creating a vortex. The heavy dust and chips end up in the center of this cyclone and drop out because of the lower pressure there.
This means that the paper filter has to do much less work and need less cleaning. Pre-separation is not a new idea, Jonsered introduced the feature the year after I bought mine. I have to clean it a couple of times a day. The has a robust paper unit with much more surface area to ensure good engine aspiration. The photo above shows its pristine condition after a couple of days of sawing for this article. In many years of chain sawing with a cavalcade of saws I have never had the pleasure of tripping a safety brake due to an accident.
However, I have demonstrated the feature to my students a multitude of times. In a kickback the handlebar rotates in your left hand as the bar nose rises. No saw is sold without a chain brake today, and that is very good. Statistics show that they work.
They trip because of violent movement alone, as in a kickback. No such test is mentioned in the Stihl instruction manual; however, I tried this same experiment with the and I am happy to report it tripped just fine. The manual suggest setting the brake for starting, and this brings further safety to start ups. A feature I really appreciated is having the chain tension adjustment screw located on the right side of the saw between the bar nuts. This really beats digging oil soaked shavings from the area between the bucking spike and the bar to find the adjusting nut which is the scheme on every other saw I have operated.
Some engineer had the good thought to make them the same size as the spark plug so the same tool removes the plug or adjusts the bar. Simply loosen the two nuts and turn the screw in the recess between the two nuts clockwise with the straight screwdriver end of the tool while lifting the nose of the bar to tighten the chain.
The tool rides nicely in the pocket of my chaps. Like the ES series it has a narrow nose to reduce kickbacks. The most frequent cause of a kickback is the upper quadrant of the bar nose touching a limb or another log adjacent to what is being cut.
By reducing the nose radius a kickback has less leverage and distance to kick the saw up and back. I find this very chincy for a saw of this price and quality. Because of all the ripping I do, having bucking spikes on both sides of the bar is almost a necessity. If nothing else, one spike makes it much harder to keep the cut square whether you are bucking or ripping! However, it also gives a lack of support and leverage for rips on the left side of a log. I ordered an outboard comrade to keep the inboard spike company straightaway.

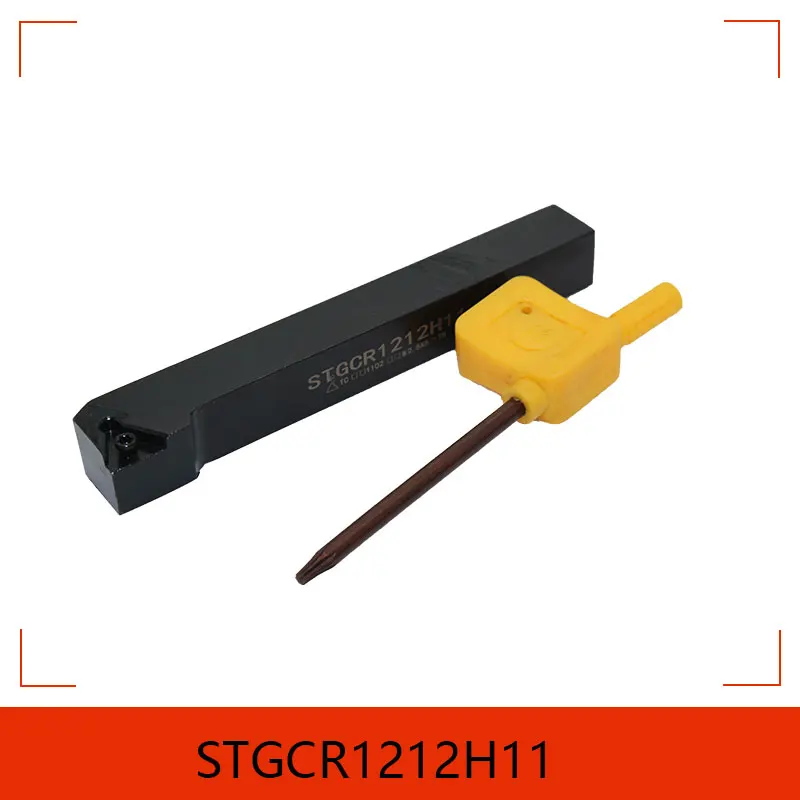
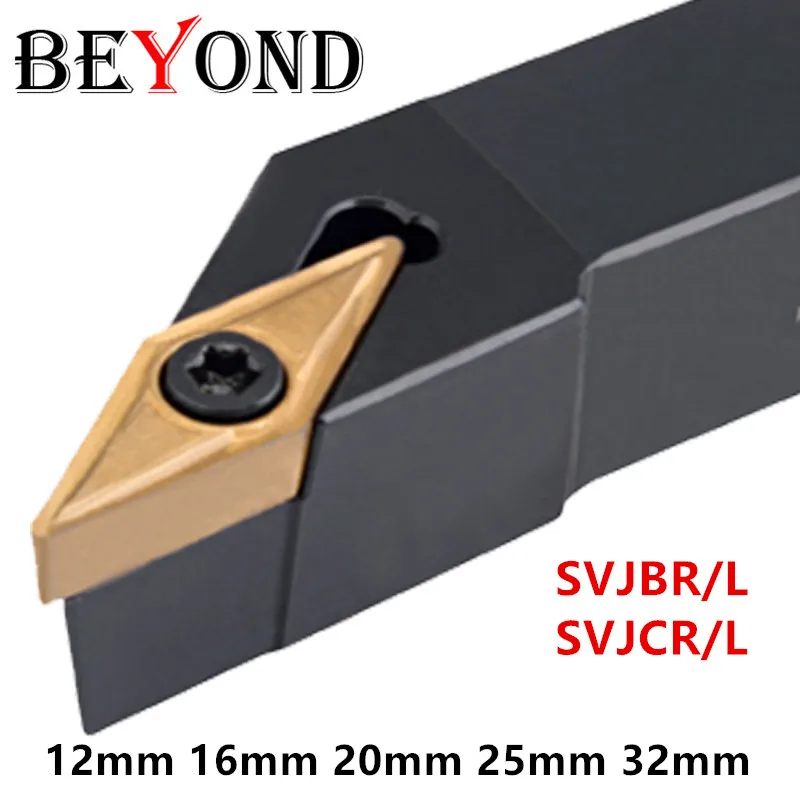
32 Inch Soft Close Drawer Slides Lathe Supplies 5g Palm Router Sign Making 2020 |
xXx
27.01.2021 at 17:55:58
PRIZROK
27.01.2021 at 18:13:30