Carving Kit Archeage Pdf,Hardware Stores Open On Christmas Gift,Rp2301fc Accessories - PDF Review
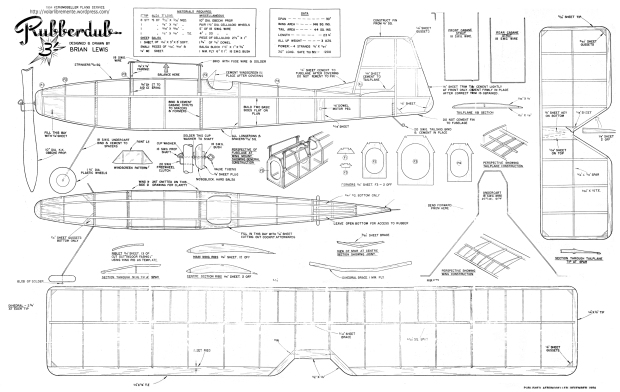
No smoking is the pxticular, circumstances cannot be accounted for. If you need to use a source of heat, first X'. It make sure it is safe. For example, putting your hand on the edge of a projecting gouge: what actually caused the accident was not the gouge, but the attitude that placed it dangerously. Lack of experience is also important. An effort should be made to understand and familiarize yoyr- oil-based stains, as well as all other finishes, in well- ventilated areas.
Keep containers closed when not in. Safety lies in: Make sure that where you walk is free from the danger x:. See that you can easfly and safely a?
Always follow the manufacturer's instructions and recommendations. Remember that there are even more possibilities for accidents when children and visitors enter the Familiarize yourself with any tool or piece of equipment before using it. Safety guards, rests, etc. J 7 - before you have noticed anything wrong. Never reach. I A fire alarm and extinguisher should always be installed.
Grit and sparks are quite capable of penetrating the eyeball; chips of wood can fly off; and it is possible for a cutter or burr to break. Keep face masks and eye and ear protection easily to hand - and put them on before using the equipment. FIX work securely before drilling, power-shaping, and SO on.
Always sharpen, or change, a blade or cutter with the Take particular care when using the benchstrop, especially on the forward stroke. Both hands should be on the c m i n g tool, with the blade hand resting on the wood. The only exceptions to this are during mallet work and whpn using specific one-handed carving techniques.
In vigorous mallet work, especially with very hard, brittle or old and dry woods, eye protection is advisable - machine isolated - that is, with the plug pulled out. Never try to catch a falling caning tool. Carve in footwear strong enough to protect the feet from suck Do not drip water from the cooling jar over motors, , an event. When sanding, use a dust mask; never blow; and Use a cutter or other accessories for a high-speed shaft protect your eyes. Used above the speed for which it is designed, the cutter could fly There are two other conditions which can agect carvers, apart, bend or otherwise be damaged.
It is commonlv known as 'tennis elbow' or condylitis. The condition is caused by mechanical stress - projecting, or close to where your hands are working. Keep your tools sharp and clean. Blunt tools require more force - shalp ones are less dangerous. Seek medical advice early; this is impor- tant for reasons of health insurance. Never cut, or exert pressure, towards any part ofthe body. On the other hand, there are forearm snaps which can remove strain from the elbow and help full recovery.
Do not imagine that the problem has gone, just because you have taken painkillers. Besides 0 A tough glove is recommended when rasps are removing the strain from the joint, you will need to find being used.
A fingerless glove will protect the heels new techniques of working which eliminate, or at least of the hands when working on wood with rough or reduce, strain. Fortunarely there is plenty of scope for this :harp edges. In my newly acquired dents, talented and otherwise. For the amateur, who rural workshop, sited among blossoming apple trees, for one good reason or another has to go it alonej it we took stock of one another across a carving bench, can be conceded that with some ability, carving is and became friends.
I was on the verge of possible not too onerous in the initial stage after all, our retirement, while Chris was in the early stages of his palaeolithic ancestors did not do too badly carving 4 career, but it has always seemed remarkable how a bone and ivory figurines. Although having an irrepressible sense of humour, lems can soon arise, often leading to frustration and despair.
So it was a most wel- carving and developed into a designer-craftsman of come and splendid surprise when Chris. This has been borne out by the creation outline of his book on carving tools, materials and a of a very successful carving and woodtuming business whole range of equipment that traditional and mod- sh in the south-west of England, which thrived despite e m canrers require for their work.
I could pass on to students. There seemed to be a read, so increasing student potential, as well as d certain lack of vital information published, and to obtaining for them the maximum enjoyment that a some degree it troubled me. In the real tlon of cathedrals and other historic butldmgs. There is no substitute for like Gtno Masero, who guided Chris Pye, and study through drawing and a sequence of planned Wheeler, who taught me, were among the exercises supervised by good teachers - tn other who were willing and able t o pass on thetr skllls 'words, for hard work.
For the most part, woodcarving became carving tools have evolved, each new shape bemg a e m of the amateur and the folk carver. Most solution m a carver's problem. Mostly the carvers amateurs were self-taught, or were insmccted by were aiming to save time, to produce clean work If-taught.
It is all-embracmng and accurate In e to reduce the forms to lifelessness whtle its content, and full of intelligence and good sense. And the carvers by tirelessly photocopying the drawmgs. I want to acknowledge my debt to all these. It's a real pleasure to improve at sharpening, and wimessed the firsr time I laid a on what he started, and I am sorry he didn't have a cutting edge into a plece of limewood.
His splrlted chance to see this book in c o l o u r he'd have loved it. Often they are only he time. This frustration affects rs, both beginners and those with more expen- the way they carve, as well as the final carvmg itself. On carving. My aim here is to present tudes and mental states which underlie what we do concrete information on how, when and are as important as the actions themselves, and it is oodcarving tools are used, on qualities of guidance on attitudes that I wish to put across, as d on how these factors relate, to enable much as technical, practical information.
As a con- ne either to start or to improve their carving. The vast choice of chisels and gouges is often one of the first things to bewilder a newcomer to carv- ing - indeed, one manufacturer has the ability to make over 2, different shapes and sizes - and even this range is not complete. A degree of confusion may also arise in some woodcarvers who, although they have been carving for some time, started with a few randomly bought tools, and in beginners who have been given a boxed set of tools and are looking to expand their range.
All of these people, and others, may be unsure as to whether the specific tools they need are available, or whether a particular tool might meet their requirements. Fortunately there is a sys- tem for finding what you need Chapter 1. W h a t a woodcarving tool consists of, and how it 'works' It is a cliche that, when someone joins the army, before they can even think of fir- ing their brand-new rifle, they are made to take it apart - then 'politely' asked to might at first appear; it establishes a deep familiarity with the weapon at an early stage, a confidence which may prove life-saving.
The key points here are that if you have an intimate knowledge of the tools on which your skill is based, are thor- oughly familiar with them, unafraid of them, and even feel free to alter their shape if you want see Volume 2, Chapter 3 - all this adds enormously to your confi- dence as a carver. There are also perfect tools whtch a I will almost venerate. Many rlvare; others become more widely available. We carvers benefit these sources of new cools but, when it comes to buymng any tool, tradl- modem, you need to know what it can do for you - how it can help your Only tune will sort out the apparently useful from the really useful care of woodcawing tools some carvmng tools whtch are well over years old; they have the names ed on the handles.
It is sobering to thlnk that you ally own a woodcarving tool you only have custody and care of tt. In the past, tools were far more preclous than rhey appear to us today, boih m terms of what they cost and their compararlve scarcity Figs 1. They were valued as a kev to eamtng a livtng in a way that 1s not easy for us to appreciate,. They took a skilled Bronze Age smith time and rouble to make understanding of what the more recently developed ones are for.
This would probably be true of any carver from the 4, years since the date of one of the earliest surviving woodcarvings - the so-called Sheikh-eLBekd, a n Egyptian carving in acacia wood dating from the Fifth Dynasty Fig 1. The reason is that the carving and shaping of wood has always involved, and always will involve, overcoming the same fundamental problems inherent in the material. T h e tools used then would still be appropriate today.
T h e proliferation of written information executed with a few simple tools recent phenomenon. Carvers of the past g to note that the term craft has its roots in would have been taught by true masters -me for general work A d others for special ons.
In this way an assorted collection of entually these tools would be passed on. Such tomb kept this woodcarwing would have thought they were entering a of a nobleman from cave, full of priceless treasures, if they could deteriorating, although it variety, consistency and ready availability of has split from shrinkage. Some h s may add W e r e, a firm may 1st a longer 'workman's' or 'pro- tools for their hobby.
The number will also the shape of the blade along its length t h k in the manufacturer's catalogue, and rt 1s longitudinal section. The range of suaighr gouges has equivalents shape and sue m the ranges of bent gouges. So, example, the curvature across the blade of a 13mm no. Fig 1. These these are often given a prefix number or letter w11l be noted in the text tn the appropriate places. I suggest you what you may msh to buy.
Check the tools when you have received them; changed Fig 1. If you need to keep the same radius of cur- vature, you can find the tool you want, but under a different number. Refer to the Sheffield List chat tool the fight width and shape a h g its see Fig 1.
A good ease or decrease the amount of curvature. An in-ca only to the part below the shoulder, depending on gouge not normally used in carvmng has its sharpe the context. It is also related to the words c Benyeen the blade proper and the tang may be a and c a d , meaning 'a watercourse'.
The root shaped lump of metal: the shoulder or bolster. Thls these words 1s the Latin canalis, 'a plpe or du prevents the tang from bemng forced Into the wooden Although these terms are useful, they are more oft handle and sphtting it.
A flat chmsel has as discussed ih the next chapter. The the thickness ofthe steel into thccutting edge. The other, convex, other words, there may be an mner and a n ou surface is the outside, reverse or back.
The comer where the bevel meets the M The terms in-cannel and out. Modem methods of sinter- ing fusing the HSS under pressure into a single - shape - may produce tools in the future. To make a carving tool, a blank of high-carbon steel b heated in a forge-andshaped on swage blocks, creating the tang, shoulder, shank and blade. There are different ways of. Hammer grain structure withi superior method, used by the best toolmakers. After the forging or shaping process, the blade is subjected to heat tt hardness and tensil Only the cutting blade itself, and not necessarily all of that, is hardened.
A greater or lesser part of the metal towards the handle including the shank, gives these parts more resilience. The steel 1s the same throughout the tool, but the heat treatment differs: the remaining part of the blade may have less hard, but more resilient, steel. If you have any of these shortened tools, and 6nd that they keep their edges badly, you can resurrect them by re- tempering. The method is explained in Volume 2, Chapter 3.
It is not just for the quality of steel alone that these tools are justifiably prized. The best makers today still shape and forge their tools in very similar ways. Whatever the reason, old tools are generally regarded tw ing as better formed and finished off than many modem e b t treatment ones. But this, again, is arguable, for some modem. They from perfect. There is no consensus on these It is worth going a little furrher into this about what it is in a blade that makes a t you can make as good, or at least as nology and research - and the ability to steel consistently - e the height of the el can be consid- or for this reason alone.
As you might expect, these tools ns long as the modem one beneath. Fig 2. Grinding is considered m detall in Part When it comes to the forgmg or shaprng of reduce to three basic varletres: tools, however, there does seem to be more of a dif- strarght ference between old and new.
Bear mn edge and a flat face on the other. Woodcarving chlsels mrnd we are all biased to some extent. This term. Sweeps range from verv flat no.. The no. There are two U-shaped gouges nos. This nomenclature 1s nor always as neatly defined as stated here, and some drfferences occur between makers. Remember also, when comparing them wlth the manufacturers' charts Fig 2. So no.
This is not true. This shows that the gouges of to strongly curved, and are numbered accordmgly. By stamping the edges of your gouges into a piece of card or tracing paper or a thin piece of wood , it is possible to find which widths and numbers of gouges will join up in the same circle.
Do try this yourself; it is quite instmctive. A second numbering system of your own, using perhaps Roman numerals or letters, can then be added to the handles. This may be important for repetitive or standardized work such as carved mouldings. For most work, however, carvers come to know which chisel cuts which curve, and will I f the sweeps of different-sized tools with the same manipulate a gouge to fit a particular cut if exactly the re joined side by side, the result is a spiral, not a right one is not to hand.
This technique is described though the sweep of each individual tool will I in my Lettercarving in Wood, page If it were to form the profiles wear out, a new one can truly flat, of course, it would be a chisel. A gouge with using a tool as a pattern; the original infor- a pronounced sweep is called a quick gouge.
Carvers is never needed. Perhaps the curves were talk about 'flatter' or 'quicker' gouges as the curvature 1 progressive Archimedian spirals, and not varies one way or the other. As the curvature in- t all. However, remember that every gouge - creases, the gouge is said to become quicker. The nos. These gauges are often, but somettmes U-shaped gouges Figs 2. The extended walls of auges prevent spckmng.
The angle is chosen according to the DES work for which the parting tool is needed. If you have rihe most common of the anguIar cross sections to choose only one type, the 60' angle is probably the khape. It is helpful to see this tool as two chisels most useful being the mehum shape. In nong other thngs it is used to separate effect the V-tool has three bewek: two for the chisels rrea of carnlng - from another. These were originally developed for particular These angled tools include the followirig: work in the fumiture trade, such as cleaning between the elements of a relief design.
They are little used in The macaroni general carving; most of their work, if not all, can be This is equivalent to three chisels joined together, done with other tools, and they are nearly redundant with two right angles in between Fig 2. It is these days.
If you are just starting carving, in particu- sometimes called a trench or trenching tool, and is a lar, these tools should not really be considered. It will cut a vertical wall. Their names both the left and the right sides. The sides are still straight, but leaning out day which somehow caught on. Some may have been a little.
Fig -. It is normally made with a Wood Carving Kit For Beginners Pdf bent length of narrow shank. The shank can m some cases could also be described as a backbent be quite long, wlth the blade a mere appendage, the edgesrurned up. It is a very specialized fanning out at the end. The tapered tools have thar ed for the furniture trade. In terms of the t ihe same nme. Fig The swdght chisel d y has flat facer.
Old books often refer to dle tapers as long-, medium- or short- or, collectively, as spade tools or spade ere the word pod may come from meaning 'foot' or 'leg', with reference to ent shank. Bear in mind that shank a [ e x o r at least part of it. You The busic fi ; h a p today is more of a heck this detail against catalogue i a- tions, and not assume that all manufacturers use the same names for the same shapes. The actual blade sweeps normally correspond to those of the other straight gouges, and the tool num- bering reflects this fact.
With most manufacturers the last digit or two digits of the listing are the same for all straight blades with the same sweep, regardless of the different longitudinal shapes. In this way, if you like the sweep and size of a particular parallel gouge, but would like it as a fishtail, you should be able to get The allongee shape this version of the tool using the numbering system. The towards the back iirst: a backbent. It can start much further away, towards the working edge, after a str a shosr, crank-like bend: the shortbent tool.
Figs 2. Sometimes the simple term 'bent standard ranges. The term is best avoided and replaced with something a little more precise. Shortbent tools include fishtail chisels or skew chisels with a long shank, as well as gouges. Frontbent gouge Fig 2. Some have so little opposite direction to rhat of a backbent gouge curve as to be little improvement on the straight gouge Fig 2. I have always found the flattest short- 2. L Fig 2. The clrcuiar shape look s l i c k ktT find that 1 can gnp it less firmly.
This sort of personal w o n is why it is best to try tools in your own hands first, Fig 2. This is not too difficult a procedure, and Chapter 3 of d Curved gouge Volume 2 gives you enough working details to tackle this problem. It is simplest to start with a tool which already has the sweep and width you want, so you need only alter the lengthwise bend. Backbent tools These are similar to shortbent gouges, but the curve is made in the opposite way.
The odd-looking tool so produced comes into its own when carving a bead or other convex surface which curves concavely along its length - such as when a reed travels into a hollAw Fig 2. Sometimes, though, when working that shape into a hollow, the handle of this straight gouge can get in the way.
Cranking the handle back keeps it clear of the wood: this is the backbent gouge Figs 2. It may sound like a very specialized tool, but I find myself using it quite a lot. It is useful for many sur- faces which are concave in one direction and convex in the other; such surfaces constantly occur in natural forms. All woodcarvmg tools are available m a large range of widths Fig 2. It is the workmg edge that 1s taken IGenerally speakmg, all bent gouges can be obtained Into account when measurmg the width.
Iin the same varlety of sweeps as the straight Eouges. For the same reason, the V,tool 1s also unavailable in a backbent form. A skew chisel is measured across the maximum width of the blade, as if it had an edge at rlght angles -presumably because the length of the cuttmg edge depends on the angle at which it is ground Fig 2. The wrll be from corner to corner, at right angles to the long axis Fig2.
There is a conversion table at Fig 2. What widths are actually avarlable varies between manufacturers - no one makes all the tools Fig 2. Most makers stock a widevariety of the most commonly used tools, having made, on economic grounds, some selection of sizes Fig 2. They are made of soft metal and are meant for cutting soft linoleum and the llke. They are not you may expect the blade of a Xm 13mm suitable for carving wood and should be avoided.
Thls IS useful when you come an old tool and are trying to work out how h has been worn away. I have described m rhii section, m some detall, the sorts of tools that are available, and the vanous terms you may come across. Gouges come in a series of curves or sweeps, rangmg from very flat to very a1 carvlng tools are always held m both hands.
The shoulder workis with the fermle function, and mcludes a drscussion of orher consider- to stop the sharp tang forcing itsgvay into the wood atim whch need to be taken Into accounr before of the handle. The shoulder of a woodcarving tool, sometimes referred to as the bolster or stop, is the protuberance in the shank of the blade where the tang penetrates the handle.
The word bolster seems to be used hdre In the same way we use rhe word elsewhere, meamng 'a cushion or pad'. The shoulder is, rn effect, a sort of jomnt. It i s particularIy important when a carving tool, such as a large gouge, is struck with a mallet: the impact of a blow on the handle arrives at, and is taken almost entirely by, the shoulder Fig 2.
The force pushes on Into the blade itself. The shoulder is formed quite early M when the ,tool The main features of a correctly shaped shoulder are as follows:. They may be too large and overhang the the flatness of the shoulder to prevent the wood ferrule; sometimes they are ridiculously small and splitring.. But, to be fair, some manufacmers take a lot equally, and evenly, around the shank. The word tang comes, through Danlsh, from the Old Norse word tun ,meanlng a point or splke.
In dlalect, tang has also referred to a serpent's tongue and an msect's sting, and, mnterestingly, connotes a penetrating taste. I Fig 2. As early as the Iron Age, when the quently seems to have been, the tannin in it would forglng of tools had just started, socketed gouges were react wlth the Iron of the tang when moisture was being made - one of these can be seen at the Lake around.
Thls corrosion of the tang, even when the Vdlage Museum in Clastonbury, wlth a handle turned handle is not oak, is still seen quire often in old tools m oak. A socket, seen tn many museums, also commonly used sockets bemg a bigger mass of metal, resists thcs corrosion for as well as tangs on then chlsels. Depictlorn of much longer. Early toolmakers would have apprectated that eted gouges. The socket probably fell out of favour - bearmg tn mmd the effort involved m m h g lager, eventually because a tang 1s less labour-mtenstve to heavier tools - socketed handles were a better mvest- make.
However, the socketed blade can still be seen ment of effort. When it comes to Fig 2. Should you woodwork. Some Chinese and Japanese chisels have come across any of the old heavy-duty socketed tools, both sockets and tangs. The strength accorded by the socket was chisel - and is struck with a metal hammer. The tang must be made without too many lumps and bumps, and should be straight The tang must allow the handle to be fitted.
Some carvers try to protect the tang from rust by soaking it in oil and pourlng a httle more Into the hole before actually fitting the handle. From the arm, the hand grips the handle of the gouge in a straight line of intention.
Some carvers do put up with tools whose handles are bent at an angle to their blades; only when the handle and blade have been lined up correctly do they realize how. The tang must not be bent at an angle I have seen this angle as much as 20" out of true.
This is quite deliberate, allowing the impact of a blow to be absorbed and a The tang should not be offset 4 transmitted through the metal without its breaking 1 under the stress. Should there be some angling away The tang is correctly aligned when it runs down the from the central axis of the tool already, there will be central axis of the shank and blade If it IS parallel to 3 U a tendency for the softer metal to bend further.
Bending can also happen when the tool is used inap- handle without the shoulder overhanging the ferrule i propriately like a small crowbar, to lever pieces of becomes more difficult Thls fault also affects the feel UP wood away Fig 2.
There can also be a problem wlth tangs molder tools Some faults can be corrected, but where they cannot whlch are partly, or completely, rusted away. All - or perhaps you do not feel you should have to cor- mmght not be lost: see the sectlon on second-hand rect them - return the tool with the appropriate tools m Chapter 5 pages OId handles of a factory-made type often show a variety of marks, glyphs The prevlous chapter started by looking at carving or notches where the carver tried to make some tool tools from the end furthest away from us: the blade handles stand out from others.
Then we turned to the shoulder and tang. Today, manufacturers rarely provlde more than Now we come to the nearest part of the whole took three sues of handle, all exactly the same shape, for the handle, whlch is often undervalued. In fauness, this Supplying tools wlth fitted handles is a phenom- is probably as much as they may reasonably be ex- enon of mass production over the last years or so. The handle makes the tool carver would then make and fit a handle personally.
This meant that - depending on the wood to the wood, and yourself, who duects the canring. Wrthout the ferrules the handles may Onandle' and actually hold in your hand Flg 3. Fig 3. St Barbara BayerischesNanonalmweum, fort, strength, efficlency, balance and 'feel' of the Munich carved about m limewood whole tool. A tool may be perfectly sharpened but stnot 'feel rlght' it slts awkwardly m the hand; per- blade itself. After all, it 1s your hand on the handle, haps it IS not one to whlch you feel attracted.
Thls m not a mass-produced, average hand. A tool appears to respond to the amount of effort, even love, that is put It is qulte possible t o have 40, 50 or more carving Into as care. Such an attitude of care and attention to tools arrayed on the bench and at work.
Every carv- the tools feeds INO rhe process of carvmng. It 1s as if the tool draws your cases slmllarlty between gouges and chlsels can cause best effort towards itself. Thls 1s the first reason for making your own tool It helps to dlstmgutsh at leasr some of the handles handles, or at least some of them. Smce hands vary die to a large flat gouge; this gives the tool greater slic- as well, the handle may alsa be uncomfortable. Once the importance of handle quality is real- ized, no further encouragement will be necessary.
Octagonal handles are ducing wonderful cawmgs. At the end of the day od shapes for setting down on an inclined plane - handles are not camngs, only part of the means instance, when lettering a panel - as they do not towards that end.
What I am tlymng to promote here so easily; but end comers, if they are not softened, is an attitude of positive regard for carving toolsi ork into the palm of the pushing hand. This attitude or approach works with creative potential, rather thaa d or sanded away.
This allows you to take some against it. Removing it may make Fig 3. When A good overall lengtb for a woodcarving tool is you come to choose the shape and m e of handle, you somewhere between 9 and lOm mm , mll need to bear in mind the shape and size of the so you need to adjust the length of handle to suit blade to which the handle will fit, the 'toughness' of Around m mm for the handle is n mm -- n mm n mm Fig3.
Thin, delicate gouges suit longer, thinner handles. The - wedge does not want to be too conical; this m itself can feel uncomfortable. Fatter, barrel-like shapes tend to pop out of the hand. The Fig 3. So cii11 rllc ;Imount of t. Wood for handles should be taken from the tougher heartwood, although not from the actual centre of the tree. This would be the toughest, A tool used for light work will probably not need hardest option. Some woods, lrke ash or hrckory, have a fermle, or even a shoulder.
However, make a natural reslltence or sprmginess. Thts IS espe- does not split here. Uneven, difficult grain can also create on the top end of the handle will cause it to last problems when fitting the tang into the handle.
They can be an attractive feature, as can burled burred wood, but you need to be careful when using WOODS the mallet CLOSE GRAIN Handles need a resiltent hardwood with close, straight gram, that has been properly sasoned defi- Trees which have grown very qutckly produce broad nitely not green Certain factors are important in annual rings and relatively light, soft wood the - determining the suttabilicy of a ptece of wood to be heartwood can be as soft as the sapwood.
Use a tight, used for maktng handles close gram, where the tree has grown slowly. Usually it is lust a matter of selecttng and putting aside odd bits of wood for use as handles when you need them. Wood can erther be taken from near the centre of the tree heartwood , or towards the outside sapwood. When the above, plus beech, well-seasoned oak, force is exerted sideways on the blade, the ferrulep e kuitwood such as cherry, apple or plum , maple, vents the handle splrtting.
More delicate sycamore, hornbeam. The word rule metal to last a lifettme. This end is offered to the wood of the handle, which is made a touch over- size. When it is tapped home, the inside bevel pinches the wood tightly and the ferrule compresses the wood, m it will not work loose if the handle eventually shrinks a little Fig 3. Home-made handles may be protected against splitting in a variety of ways Fig 3.
When a mallet is used, the top of the handle takes a great deal of punishment and is easily damaged Fig 3. It is sometimes possible to salvage a damaged handle by paring away the broken part, or by gluing splits before they develop too far Fig 3. This needs to be thicker-walled than a tang ferrule, and preferably made of iron.
Many types I of piping will be suitable. With a steel or iron ferrule on the end of a large sculpture gouge, a soft-metal dummy mallet, such as is used by stonecarvers, can be used instead of the normal wooden mallet.
This sort of mallet is made of soft, annealed iron and has the advantage that a good weight is possible without bulking up the size. Flatten Pipe Carving Kit Gift Pdf the end wood wmth a sanding block after t! For an end fenule, allow the wood to extend a little way out of the metal tube. Mark the centres at each end side of the ferrule - this locks it on m case the wood of the wood by drawing diagonally across the comers, shrmks or the femle works loose.
To Whether the tang is tapermg or parallel m section, it achmeve this, bore the hole fust, wharever shape of helps to drill an accurate pllot hole first, no more handle you are makmng. Test the fit splittmng, then enlarge the hole to about a thud of the hole first on a piece of scrap wood.
Take a comers of the tang bite and lock into the wood measurement of the diagonal of the tapenng tang of the hole. The handk needs to be algned correctly uslng a simple jig. If you have neither lathe nor prllat drill, bore the The tang hole has to be about halfway hole uslng an ordiiary wheel brace hand drill rn between the two a hand-held electrlc drill. The problem still remaim of how to bore the hole true; the tried methods of a Measurement across width of tanq.
Once the ptlot hole has been drilled, the size d the hole can be incrementally enlarged as necess- Hold the wood in a vice and allow each bxt to folios the hole made by the receding one.
If several handles are belng made, Saw off the waste a second time and you sho;ld bore them all as one procedure.
Smooth the faces squarely wlth a spokeshave, Reverse the wood on to the lathe so the polnt rasp, file, etc. Q Chamfer the comers by eye In the same way to glve the eight sldes I t may be helpful to make a Rough the handle to a cylinder, then move In V-shaped cradle to hold the handle securely, as the toolrest as close as possible.
Fmt the ferrule next; mark its length and a lmttle Octagonal handles, as mentioned before, extra on the end of the wood. Stop the larhe where they meet - a definite, but small, shoulder and try pushing on the ferrule; remember to should remain. Sand the handle and then burmsh with shavmgs.
The wood can be left like thrs, By trial and error, creep up on a final diamerer acquiring the natural patcna of use, or sealed where the ferrule pushes on tlghtly. You may with a coat of teIlulose lacquer, vamrsh or need to rake the handle off the lathe and, with shellac.
Cut the sealer back finely. Do not give the ferrule on the edges of a vice or prece of the surface a shiiy or glossy finish: thls makes tube, tap the ferrule home. Use the poinr of a rumer's skew chisel to trim Q Now, wlth the f e d e in place, shape the back the excess wood at the ferrule end, but handle.
Round the end to fit comfortably in take care not to cut into the revolving centre your hand. Do nor run the wood completely Fig 3. The lathe. Hold it m a vice and finish off both ends only snag is that if the tool is struck with a mallet, the wlth a chtsel and sandpaper.
Flatten the hole tang will work loose; but for lighter tools this method end so that the blade shoulder fits flush to the is quite adequate. Seal the ends in the same way as the rest To knock on a handle, the blade must be held of the handle. If you were to set the blade upright so its cutting edge was against a resistant surface and then Finally, punch a locking depression in each side thump on the handle, there would be a problem: the of the ferrule a nail will do for this.
A thick - tool would have nowhere to travel and, as the energy end ferrule may need a small hole with a nail from the mallet blow could not be released, the blade tapped in. This is particularly true of U-shaped blades, where the bevels on either side act as wedges, squeezing the sides together.
A metalworking vice with soft metal linings and tangs, need to be corrected as far as possible to is the best sost to use; but a woodworking vice is an give the best chance of fitting a handle well. These alternative, if you first pack out and protect any are dealt with in Chapter 4.
Old carving tools can be found with quite large and not particularly accurate holes for the tangs, filled with gutta-percha a resinous gum from a Malayan tree. The tang has been pushed accurately into the gum which has then set like hard, black horn, fixing the blade neatly and securely in Wood Carving Kit Near Me Pdf position Fig 3. This is a trick worth remembering. Modem equiva- lents such as the two-part plastic fillers intended for car bodies or wood will repair a handle, perhaps Fig 3.
If your tang and holes are true, the blade mll be allgned along the axls of the handle. While no doubt it is fun, it also chars the wood inslde, allowtng the handle co work loose; it can be messy and not mthour its dangers - both to the lungs and to a wood-filled workshop; and it can, if care is not taken, damage the tempemg of the tool. It 1s also much slower than any method described here - all m all it is not a technique to be recommended.
This IS especrally true of tools that have tapered, square tangs - these lock securely in place during use, but release from the wood fairly easily when requaed. When the shoulder sits tight up to the edge of the fer- Never grip quick gouges - and especially U-shaped rule, the wooden wedge cannot get a purchase on the les - across the blade.
The pressure of the vice can handle to knock it off Fig 3. You need to. Be careful not to damage the ferrule with the chisel or Iith the blade held firmly in the vice, try the handle screwdriver. If you do, the ferrule may need filing or little while gently twisting it.
Sometimes this is all touching up on a grinding wheel. Be careful, as the handle can come Y very suddenly; so make sure that nothing is in the ay of your elbow as it travels backwards. Strike I le wedge firmly with a mallet. If nothing happens,? The handle should knock off fairly easily. Using an actual Fig 3. If all else fails -say with an old tool where it is cer- tain the tang has corroded and practically bonded with the wood - the handle has to be sacrificed.
First use a hacksaw and pliers to remove the ferrule, saw- ing diagonally along its length. Grip the blade in the vice by the shank, with the shoulders resting on the jaws and the handle straight up. Split the handle from F ,trig a wedge of hardwood to knock c the top end using one of your second-best chisels.
It is not necessarg to wax the handles as, if frequently used, the wood namaUy becomes bur- nished and aequires tts own patina. If woodcarvrng tools are unused for some time, a light wipe wrth limed oil raw mrhe handles will take care of the wwoodj but be aware that this may encoutage mould growth if the tools are scored in damp conditions.
If you have acquired old gouges and chiseb and rntend to continue using the handles, then you can add your name to any already stamped on. There b a great serw of tanttnuiw, seeing took passed though several haads and being aware of tonract with a carvet who may be long dead. Support the handle m a V. Line up the punch and my Fig 3. The steel and edge-holding properties them- fault. I am was unacceptable.
The tools had been carelessly made suggesting here that a crltlcal look should be taken at and should not have passed the factory inspection. The faults which follow have occurred both In my Most often the fault lies in the actual shaping own tools and those of other carvers, and the reasons of the tool when it was forged: in the blade, shank, they may be considered faults -the effect of the fault shoulder and tang Some manufacturers consistently - will be glven. The questlon is whether the 'fault' or produce superbly shaped carving tools; orhers, sadly, condition makes a difference to you as the user.
Some ,, do nat. So, check over your tools, both old and new, as The resulting tool feels less certain, more 'self- they axe acquired. The wmnd- where you can justifiably be proud of them. But do mng must always be kept m mlnd and compensated for. But, for the most part, any significantly asymmetrical tool ' should be retunled. Another problem with the V-tool is when particularly Fig 4.
The principle is: bend the blade iur- ther and get in deeper. Two tools of the same width and sweep from the same manufacturer, may have dissimilar bends.
Some manufacturers make spoonbit gouge Fig 4. If what you have received is unacceptable replacement is the only optlon. Too small a shoulder - more of a protuberance than a shoulder - may be forced into the wood by mallet blows. If the tool is for light work only, for all practical purposes this will probably not be a problem.
For heavier work, this state of the shoulder is unacceptable and the tool should be replaced. It should be flat and sit tight against the however misaligned, without this happening end of the wooden handle Fig 4. If the face is badly rounded, not only will there be a gap between no improvement, try another maker. Do not attempt the shoulder and the wood - which is uncomfortable to change the shape by cold bending, as the relevant to hold - but there is a danger of the metal being - part of the blade is too near the area of tempered forced further into the wood and splitting it, especially metal and is liable to fracture Fig 4.
Some makers take a lot of trouble to polish up the sur- faces of their tools to make them attractive. Others leave the outer faces with the rough, black, oily surface resulting from quenching the hot metal, and only polish the inside to show the straw colour caused by the tempering. New, polished tools are often protected from damp by being given an oily,. Oily surfaces on carving tools are more of an irri- tation than a problem, as there is a tendency for the grease or black oil to get on to the work via the hands.
Rub the blade with a degreaser like paraffin kerosene until no more oil comes off. Fine emery paper can be used on the more dense black finishes, as well as to smooth off sharp comers and edges along - the length of the blade. Fig 4. It is still possible to align h? Take a washer which has a angle Fig 4. I t is far better for the tang me and drop it over the tang so that it rests on the vice.
The blade should be gripped in the vice E proud of the hole, with the tang perpendicular to the described for flattening the bottom of the shoulder. With the washer acting as a jig, a file can now and tapped gently with a hammer, working from the IN be used to flatten the face of the shoulder Fig 4. Remember that a tang - or any metal - - km creating a true face to sit on the wood of the handle.
The consequences of a bent tang have been discussed in This is a problem created in the initial forging, and is Chapter 2 page Send the tool back if it IS a new one. It i s more and the same wood if possible - gluing and tapping it often a problem wlth larger tools. In the following sec- tion is an approach to buying the tools you need tc The subject of woodcarvtng itself that is, how to start carving.
Carving as such 1s covered m more detail in when the tool is actually cutting the wood. So t b my other books. The cuts proceed in a set order a d one actually we them? In resulting work appears as swiftly as possible, wtth a thrs section are some pointers to the functions of the uniform appearance. Thts is by no means an exhaustive rime is kept as low as posslble in a different war.
Against this, though, it should be said that there is a danger of making the work look uninteresting by using the same cut too often; the more variety in the tool cuts themselves, the more To begin with the obvious: firmer chisels are used lively the resulting surface may be Fig 5. There is when straight lines are needed - as in cutting letters a creative balance to be stmck. Lettering may need a wide So the functions of individual tools are not com- range of chisel sizes to cut the varying lengths of pletely fixed and static.
One gouge can be made to uprights, diagonals and horizontals. Figs 5. But there are also times when you must have slicing or skewed fashion, they will also trim the out- one particular tool for the work at hand, and no other, side edges of curves. The chisel is not normally used will substitute.
For this reason the flat gouge is preferred, even though the surface it produces is slightly undulating and only approximately flat.
Fig 5. It will shape the comers and edges of ISthe preferable cuttmg edge - the comers are free of grooves left by a V-tool. The amount of bend In the grounding tool or mg more of a sllcing cut than the square firmer. If the point is rocked can get into an appropriate position to cut. Grounding describes the deeper, flat-bottomed get into recesses and comers where square-ended cutting that is needed to sink a background. They come lnto thelr own where A grounder may be a shortbent chisel, or a short- undercuttmg has been created and deep corners need bent gouge of the flattest sweep.
The flat gouge profile to be got at. As both directions tnevicably need to be cut at some trine or anorhet, buy them as a matching pair. Shorthent comer chisels are the sort of tool chat may not be used very often, but when they are needed it is because nothing eke wrll do. For example, use fishtad chisels to cut the flat ends of serifs in lettering.
Keep these splayed took for the lighter, final stages of carving, allowing other tools to take the brunt of the preiiminary work. Cbrdering the edges of V-grooves creates a type d low-relief carving. The tool can also be used with special knives to produce carving, Fig 5.
Subject In making a gouge cut, one principle is not to let the comers dig in; this is why, as mentioned earlier, the flat gouge is preferred to the chisel for finishing flat surfaces. The middle part of the sweep cuts, but the comers remain in the fresh air, slightly above the H Clearing ground surface Fig 5.
This is a different technique from deliberately using one of the comers to make a slicing cut in the manner of the skew chisel. If the corners of a gouge are buried in the wood during its cut, then not only is some control lost, but the wood fibres are tom, which produces a ragged surface.
There is also I Clearing ground P -- - - -? It may be helpful to elaborate a little on how gouga ate used. The 'quickerbrving tools do indeed remove I wood in more bulk - and therefore more quickly - Fig 5. If deeper details may well be m the wrong place altogether. When the underlying form is established first, the Another important use of the gouge involves detarls fall naturally mto place.
Setting in mnvolves outlining a mmn subject from its sunroundinga, as when cutting away the back- ground. Setting in uses rhe sweeps of carvlng rools in a similar way to that mentioned above, and rhts is one of the reasons why carvers build up large numbers of caxvrng tools in different sweeps and sizes. It describes that stage in the carvmg process which is a little further into the work than the prelimmary roughing out. Flutets a d veiaefs, making deep cuts, grooves or I channels, can be used to produce decoranve work in their own right Fig 5.
They will also create a softer outline to a relief form than the V-tool can Fig 5. An oblect, or area, can be faded or blended more readily into the background if rt does not have a hard junction where the two planes meet. Fishtail fluters negotiate curves more easily the wood; the outer bevels act as wedges to squeeze than the straight, parallel fluters; the blade following du the walls of the gouge together Fig 5.
Being thinner, the splayed The bend in these tools enables the gouge to enter gouges are quicker and easier to sharpen than parallel- deeper recesses and hollows than a straight tool can Ed sided gouges, and hold a finer edge. But for the same Fig 5. Because the sweeps match, when the blade iia reasons they are less economic, becoming slightly or handle of a straight gouge fouls the wood around I narrower with each sharpening.
Bent tool6 can only rarely be used upside down. The deepest hollows are entered by the fllpst sharply cranked coals, whose name - knuckle gouges - expresses their shape, In practice, the handle of a shortbent gouge ofren swings through a large arc to produce what 1s quite a small cut.
Make sure the cutting edge is trav- elllng through the wood, and not just being levered I at the bend. This presentauon The contents of Part I so far will have helped you gam produces a rounded or convex cut Ftg 5. Now, an understanding of the 'anatomy' of woodcarving just as the longbent and shortbent corxhgurarions tools, how they work and whar might be done wrh enable a gouge in the fixst position to enter hollom, them.
Or what Lf you want to expand your range? Time will also be needed to sharpen i the tools, whtch can be slow and ar tlmes frustrating to begln with. As a gtudelmne, around a dozen or so carefully Fig 5. The best approach whether you have - It is particularly useful if they are uslng a standard no carvlng tools or many is to Increase their num- - numbemg system such as the Sheffield List, so that ber as and when the need arises. Better still, if you are Make the most use of what tools you have avail- able to Inspect the tools personally, take along an able, and make a few notes as you go along.
Wlth this cn hand, you can make a way, you can use what has been sard earlier in thcs comparison between the sweeps you have at home, chapter to define the difference you need accurately. Some makes of tool are more actuaIly want to carve. It 1s worth experlmentlng this way usmng, then the chances are that your heart is speak- even if you have qulte a few rools already. This can work out well, but equally often, what tools to buy. A t the rcsk of duplicating what has does not. The glver wlll usually be unaware of the been said earlier, here are some guidelines: qualcty of the tools, and may have bought some of the cheaper tools to be found on market stalls.
Even Avoid cheap tools when the quality 1s excellent, the cholce of tools has Cheap tools are almost always made of poor steel, been made by other people: firstly by the manufacturer badly tempered and incapable of holdlng an edge for and secondly by the giver of the set. Poor quality, or long - even if they have been poltshed up to look poor selection, can cause a lot of frustration and, smart.
Expense is relative. In effect, the tool kct grows use. Through them you may have years of pleasure wlth the carver. However, rf you already have a boxed and creativity, and perhaps even earn your llving.
If set, do not despalr: they may be exactly what you there is stdl any doubt as to the value of carving tools, need. There is no reason to accept substandard tools thrng - but start. And this 1s also a good way KC you are paying for. O n the contrary, by keeping man- see your first carvmg as well. It impressions with what the manufacturers are offermg. In the long Check w e r the cawing tools when they arrive term the smaller tools, while apparently slower, are less tlring to use, and eventually more work is First, see that the sizes and shapes are exactly what achieved wlth the same effort.
My main reason prominent feature in many styles of lettermg. The for giving information on faults or problems ts to save curves of the letters will need to be matched to you being at a loss when they occur, by lnformtng you some extent, and fishtail gouges and chtsels will be of what sorts of remedles are possible used for the serifs. How- match the scroll of the vrolm, or fine veiners and ever, they still crop up in markets, second-hand tool V-tools for featherwork.
Once people h o w of your interest in carvmg, you may well find that you are given tools and wood There 1s a welcome feelmg today that it is reprehen- Today, ever larger numbers of carvlng tools are sible to waste such assets.
Commerce skill allows you to create trade packs commercial boxes and sell the packs. Cooking allows you to craft different types of food that give temporary buffs or stat bonuses. Farming allows you to grow crops and water them.
Also allows you to create shrubs for planting. Vegetables and cereals created by farmers can be used in Cooking. Gathering allows you to gather different types of herbs and flowers for Alchemists. Handicrafting allows you to create jewelry rings, necklaces, earrings , chests for clothes, musical instruments for bards, parts for racing cars and other items.
Husbandry allows you to breed animals such as chicken, cows, bears and yatas. Leatherworking allows you to create leather armor out of leather. Logging allows you to gather logs for use in Carpentry. Machining allows you to create different devices tanks, gliders , tractors, parts for racing cars and tractors, submarines.
This profession also allows you to upgrade machines. Masonry is necessary for producing different types of bricks out of stone. Also allows players to craft Teleport Stones that enable you to travel from one location within the island to another. Metalworking is required to smelt different types of ore into ingots. It also allows you to craft heavy armor sets plate armor and diving suits. Mining is used to gather different ore and stone from nodes for Metalworking.
Also used in the gathering of crystals gems. Printing allows you to create books and different scrolls for gear improvements. Tailoring used to craft cloth and cloth armor from various textiles. Weaponry allows you to craft metal weapons swords, daggers, axes etc , shields and explosives out of Ingots. Artistry allows you to compose music. The more you advance the longer the music will be.



Wood Carving Duplicator Machine 01 4 Foot Oak Dowel 30 Rockler Blum Drawer Slides Water |
4356
10.12.2020 at 21:21:47
Gunesli_Kayfush
10.12.2020 at 21:28:19
SEXPOTOLOG
10.12.2020 at 23:51:29