Preparing Wood For Turning Edge,Decorative Cabinet Door Locks,Woodwork Store Nz,Bench Dog Cast Iron Router Table Top Model - And More
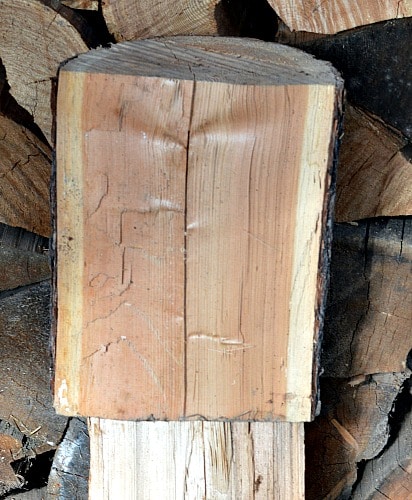
As I cut the bowl from the face plate this will keep me from making the parting cut too shallow or too deep. Here I am making a cut to the final uniform thickness of the bowl wall from the inside. The outside was already set before we began to turn the inside. It is very important to have the bowl wall thickness uniform in order to avoid checking of the wood when it dries. Some will check no matter what you do but if the bowl wall is thin and uniform, very few will check has been my experience.
Every time I am too lazy to use the calipers, I regret it. Here the calipers are set at a known width and slid down the bowl wall, with the lathe off. When it begins to hang you know that more wood needs to be removed at that area.
Trimming cuts like this need to be done gently. You cannot replace wood you have turned away. Measuring of the bowl wall thickness is now complete. Notice that in some areas of the rim the bark has come off. When this happens I remove all the bark. If it all stays on I leave it on. Some people love the bark left on for the added contrast.
Others feel it is too impractical to use around food. The bark edge is somewhat delicate and can chip off. However, it is not too delicate or it would not have survived being cut to a narrow width with a gouge while spinning at rpm.
In this picture I am removing some waste wood about the base and getting ready to use a parting tool. Here I am using a thin parting tool to remove the bowl from some of the waste wood into which the face plate screws are lodged.
This is a trick I learned from a master bowl turner named Fred Williamson. I will not complete this cut for several days. However, I cut in deeply enough to leave only 1 Dry Wood For Turning Edge to 2 inches of wood of the base of the bowl still connected with the waste wood with the screws attached. How deep the cut depends on the size of the bowl and the size of the faceplate being used.
What this step accomplishes is to separate the bowl base from most of the still wet wood in the waste attached to the faceplate. I will leave the bowl just as you see it now. In one to two days it is dry enough on the surface to begin sanding. I use my Souix drill with sanding pads to do the rough sanding. If you have ever tried to hold a large curved bowl in your lap to try to do this sanding you appreciate how nice it is to have the bowl still rigidly attached Preparing Green Wood For Turning Item to the lathe so both hands can be used on the sander.
Working near the base, the lathe can even be spinning slowly to speed up the sanding process. So the one or two inch plug at the bottom is enough to hold the bowl on the lathe but still most of the wet waste wood has been separated from the bowl so that the bowl base can dry evenly.
I am very grateful to Fred for sharing this technique with me. If you have several faceplates then you can have multiple bowls drying for several days while you continue to turn more bowls from wet wood. When you have completed the sanding of the bowl on the lathe then just cut through the plug that holds the base to the faceplate with a hand saw. This is safer for me than parting off a large bowl with the lathe spinning. If you use a saw, be careful how you angle the cut so that the saw teeth do not cut into the base of your bowl.
Sanding will finish the base so that it looks professionally done. Here is the finished bowl. To finish my bowls I sand through grits 80, , and Then I spray with dewaxed shellac I use Bullseye brand in an aerosol can available from Klingspor to seal the grain. Since the shellac has been dewaxed it is compatible with any other kind of finish including oil finishes. Sealing with shellac keeps the oil stain from soaking in the end grain and oozing out later to spoil the surface.
I sand all the shellac off starting with grit and then progress with , and grit. At this point I apply tung oil. I get a food-safe grade and dilute it with mineral spirits so it will penetrate. I use anywhere from one to four coats of tung oil waiting 24 hours between coats. More coats give a deeper looking finish. Then I like the bowl to dry for a month or more and then use the Beale buffing system I have described in earlier blog posts.
This starts with a coarse abrasive and ends with carnauba wax all applied with a buffing wheel. This is a real labor saver and results in a low gloss sheen. I am not in favor of shiny plastic appearing finishes.
Everything is easy when you know how. With the ability to show text and graphics, it puts the skill of wooden bowl making within the reach of anyone who has the proper equipment. Woodworkers have been generous to share their skills with me and I am pleased to be able to pass them on to you. Edwards, have enjoyed your expert tuition! As you know there are many ways to skin a cat. I am having trouble with natural edge projects in that the high points usually end up thicker than the low points.
Any tips on how to remedy this? Regards Alan. The first hundred thousand of these are the hardest. They say you have to make several hundred ugly bowls until you can make a beautiful one. Well, enough of the silly comments although they do contain an element of truth. Let me share what I have learned. The higher rim gets thicker than the lower rim of the bowl from repeated cuts. You should strive to reduce the overall thickness of the side of the bowl to below the lowest part of the rim to perhaps an eighth or sixteenth of an inch from where you want the final thickness of the wall.
Then sharpen your gouge carefully. Now the aim is to hold your head so that you sight right down the inner rim of the turning bowl. Now take one continuous gouge cut to the final thickness of the rim all the way down keeping the cut parallel to the outer curve of the bowl. That means that waste wood needs to have been already removed from the area of what will be the lower rim and a bit below.
Otherwise you will not be able to make a cut from the upper area of the rim to the lower area of the rim in just one pass. When you try to remove too much wood you just get a catch or the lathe stalls. It is the repeated cuts entered lower down from the highest part of the rim that tend to go too deep. You end up with an acceptable rim thickness at the hight point of the rim but it becomes paper thin at the lower area of the rim. Ask me how I know this.
I have done it hundreds of times. So the key is to get to approximate thickness all the way down to below the lower rim. Then sight very carefully and run your very sharp gouge on a course that is exactly parallel to the curvature you established on the outside of the bowl and try to run that cut continuously all the way down to below the lower rim.
The more times you have to go back and recut below the higher rim the more risk you have in making the cut too deep. Your eye is focusing below the upper rim and you lose perspective of the outside curvature you are trying to match. It just comes with practice. The more bowls you do the more even you will get your wall thickness. I have learned that an expert tends to be very critical of his work.
He knows where the defects are and tends to point them out to others. It is really not necessary. What I have learned in giving my bowls as gifts and selling them at shows is that what you see as a glaring defect is not even noticed by others.
So just do the best you can and strive to do better with the next one. In time you will even be able to satisfy your harshest critic, which is yourself. Hope this helps a little. The side opposite the high side is the next higher side and then the other two are opposite each other and perpendicular to the two high sides.
I jsut do not want to screw it Preparing Wood For Turning 80 up. Any and all suggestions will be greatfully accepted. Our first instinct would be to saw a log in half and then screw the face plate to the flat sawn surface of the bowl blank. Here is how I have been taught to do it. Put your bowl blank between centers before worrying about the face plate attachment. With a spur center in the head stock at the exact center of the blank bring up the tailstock and screw the ram against the other side of the bowl blank.
The curved part of the blank the natural edge will be facing the head stock and the flat sawn side of the blank faces the tail stock. By hand slowly rotate the blank between the centers. Note if the high sides of the natural edge pass past the same fixed point.
You can use the tool rest and your finger resting on it as a reference point. Odds are they are off. It is highly advised not to use the rip fence as a guide when cutting, as it is hazardous and result in uneven cuts. After sawing the edges, smoothen it using the jointer to eliminate all the saw marks. The added inches are the allowance for the final removal of the saw marks after running it on the jointer.
Using the table saw, or miter saw, you can now cut the end at 90 degrees angle. Using miter saw can give you accurate angle cuts because it is adjustable to Preparing Wood For Turning Style your desired measurement. It is usually set to a default 90 degrees, so that will not be very tricky for you to set it up. As the final step of this process of preparing wood for your woodworking project, cut the remaining end to final length using either the table saw, or miter saw, as well.
When done, you are now all set and ready to start working on your project. Preparing the wood, you will use as important as acing your woodworking project because it will command the durability and quality of your final output. While going over each item on the list, did you find it helpful in your preparation for your woodworking project? How did you find the whole process? The stores can probably offer us ready-made wood pieces and hassle free work, but for me preparing it yourself gives you the assurance that the wood is cut perfectly to meet your needs.
You can also bet on the exact measurement and durability and at the same time control the sizes and dimension. Hence I find having lists like this useful and important especially for those doing some woodworking projects. You may have your own designed steps and techniques in preparing a wood or have other ideas regarding this list, which you can write in the comment section below. And if you find this interesting, hope you can share it with others too.
Step 1: Cut rough wood to size. Step 2: Flatten the best side of the wood using a jointer. Step 3: Flatten one edge using the jointer. Step 4: Plane the other side of the board. Can You Burn Treated Wood? Can You Sand Wet Wood? Can You Sandblast Wood? Can You Spray Paint Wood?
Can You Stain Wet Wood? How is Nail Set Used in Woodworking? Step 5: Cut the other edge using a table saw. Step 6: Run the sawed edge on the jointer. Step 7: Cut the best end of the square. How Long To Season Wood? Is a Router Necessary in Woodworking? What Does a Wood Jointer Do? What is Wood Alcohol? What is Wood Ash Good For? What is Wood Conditioner? What is Wood Pulp?



Rogers Router Login Hitron Install Center Mount Drawer Slides File Jet Planes Stormzy V2 |
princessa757
04.12.2020 at 20:19:16
Sibelka_tatarchonok
04.12.2020 at 17:11:57
Alisina
04.12.2020 at 10:39:12