Pocket Hole Jig Vs Biscuit Joiner Watch,Restaurant Food Supply Tucson,Make A Frame In Canva Review,Best Rap Remixes Edm Iphone - Try Out

This year's Dezeen Awards features media categories for the first time, with awards for architecture photography, video and visualisations plus websites for studios and brands. Introducing new Dezeen Awards prizes for sustainable architecture, interiors and design!
Our three categories celebrating projects that make positive environmental and social contributions are now open for entries. Dezeen Awards is now accepting entries! They will protect your billiard table and can serve as a buffet at your next party. How to Build a Home Theater Want a movie-theater experience in your home? Learn how to build a home theater with step by step instructions from the pros at HGTV.
How to Build an Occasional Table Make a cube-shaped coffee table that doubles as a storage piece in four simple steps. How to Build a Herringbone Privacy Screen Use basic home improvement store materials to add designer-grade privacy and graphic impact to an outdoor space. Magnetic Game Board Turn a magnetic message board into a fun game board.
How to Build a Convertible-Top Coffee Table Learn how to build a coffee table with hidden storage and a four seperate tabletops that flip from flat to cushioned. Miss Your Favorite Hotel? Load More. Rehab Addict Rescue 7am 6c. Rehab Addict Rescue 8am 7c. Rehab Addict Rescue 9am 8c. Rehab Addict Rescue 10am 9c. Rehab Addict Rescue 11am 10c. Rehab Addict Rescue 12pm 11c. Love It or List It 1pm 12c. Love It or List It 2pm 1c.
Love It or List It 3pm 2c. Love It or List It 4pm 3c. Love It or List It 5pm 4c. Home Town 6pm 5c. Home Town 7pm 6c. Home Town 9pm 8c. Home Town 10pm 9c. Home Town 11pm 10c. Home Town 12am 11c. Home Town 1am 12c. Home Town 2am 1c. Home Town 3am 2c. Home Town 4am 3c. Home Town 5am 4c. To sign up, please enable JavaScript. Privacy Policy Sign Up.
Sign Up for More No Thanks. The Wogdon is beginning to look like a pistol at last. Anyway I have to find a way of making them! I also need to make the cup for the head of the side nail in silver — I might try a cuttlefish casting for that, and then glue it onto a rod and turn it to shape:? Its really difficult to re-make holes that are almost right as it involves drilling into the edge of the old hole — in practice it is not even worth trying!
In this case I was able to put a 5 mm end mill through the lock plate in the correct position for the new frizzen screw hole and take out the old 3. I then hammered a slightly tapered 1 degree peg into the hole and fused it very lightly on the inside with the welder. I was then able to put the new hole through the centre of the plug. The early Wogdon frizzens had a very small roller in the lobe that runs on the spring — it works without the roller, but I will probably fit one for authenticity!
As far as the locks are concerned that leaves me with a top jaw and top jaw screw to make, and the cock to bend a little to clear the flash guard. At some point I need to make the ramrod fittings, but I guess that can wait till the pipes are installed. I waited ages before I began to shape the stock, now I have to wait ages before I can start to apply finish…….. Today I made the barrel bolts to hold the barrel through the loops I put in under the barrel.
There are at least three ways to make barrel bolts — you can heat up a suitable strip of metal and hammer a head on it, you can build up a large blob of weld on the end of the strip, or you can take a sheet of thicker metal and mill either side to leave the head at the end. All ways end up filing it to shape.
If not, or for larger barrel bolts I machine down a strip and file up the heads. Any way you then have to cut a fine slot down the middle, which I do by drilling a few small holes of 1. My thinnest files are about 0.
Depending on the slope of the stock the head will be filed at an angle — the one near the muzzle has a distinct slope, the rear one is pretty straight. Anyway that is another job done. The ones I made need a bit more tidying up, and the heads are probably a bit on the bold side, but they can always be filed down.
I made a list of all the jobs still to be done apart from finishing the stock and engraving the lock, barrel, false breech and trigger guard I have to sort out the ramrod, pipes and ends etc. It is thought that Wogdon and most London Gunmakers bought their locks in, probably from Birmingham, and that probably included the set triggers see the Wogdon book for this opinion They may Pocket Hole Jig Joinery Ltd well have bought in the steel furniture.
He also put his engraving out to an engraver — at some point to William Palmer. I discovered today that the person I had been sitting next to last March at interviews for a new head teacher developed Covid 19 at about the same time as I did — I wonder who gave it to who?
More remedial work — the AGA oil fired cooker died, or at least was in its death throws. It happens from time to time as its a very primitive machine. The filter clogs up every time the tank is refilled as it stirs up sediment, but I did that last week. The other regular problem is the burner which needs de-coking to get rid of a buildup of carbon and gunk.
It is just an open wick system so it just needs the burner taken out one union and a long drill rod put up the oil pipe and the carbon chipped out of the oil reservoir — takes about 45 minutes but the AGA needs to cool down first, and then get up to temperature again.
All done by lunchtime. I made a test barrel bolt yesterday and got both slots working, so I felt entitled to get on with shaping the stock at last. Anyway I got all the preliminary shaping done so most of the excess wood is removed and the shape is basically defined.
I then sanded with and so that I could see any faults and also run my fingers over the surface — touch is much better at exploring the shape than sight on wood where the surface has grain and is matte.
The Wogdon duelling pistols were unusual in the shape of the butt — the book helpfully gives the dimensions of each pistol — the one I am working from has a very wide end to the butt — I have made it a bit smaller than the width given but its still a lot bigger than most of the duelling pistols of that era — the Hutchinson is very slim by comparison. Then I have to make a vacuum chamber and get or make some form of vacuum pump and get my furnace going and find a decent gas torch.
Had a chance to minister to my ailing desktop PC in its agony. Turned out to be not so bad, although rather long winded. My only problem was finding an empty USB stick with enough space on it. But it all worked, and to my surprise there was no requirement to show that the computer had a legitimate copy of Windows It seems as if Microsoft has such a big and solid chunk of the market that they have dropped the paranoia over licenses, thank goodness.
I am homing in on shaping the stock, and finishing off a number of small jobs that need to be done before then, including fixing the false breech with a screw I have already made No 8 UNC and making and fitting the barrel bolts.
I guess I ought to pin the trigger guard in place, but I may leave that as I might want to inlet it a bit more when the shaping is finished. Idly reading the Wogdon book after dinner, as one does, I spotted that most of the duelling pistols actually pin the trigger guard tang through the butt, as I was expecting.
Oh, and I checked in Kaye and Laby — the physicists bible — and discovered that silver is the most thermally conductive metal bar none — I had a feeling it might be…. Unfortunately my desktop computer is terminally ill and will need some serious attention when I get time. Has fun getting the hook made for the tang of the trigger guard, and then getting it to work properly.
Then the real fun was silver soldering the parts of the trigger guard together. Holding them in place while I soldered them required a jig, so I used the original trial stock I had made and cut slots for the tang tab and the finial tab and wired both to the stock after cutting out a piece in the middle around where I had to solder. There were three little problems in soldering!
Anyway I managed it, only the tang and finial ended up about 3 mm too close to fit the stock, so I had to resolder the tang joint. Altogether a major trauma! But its done and after a whole lot of cleaning up of oxide and flux etc it looks good. I have been looking up details of getting it hallmarked — a legal requirement if you want to describe it as silver.
Next job is probably shape the tang when the stock is shaped, then polish and send for hallmarking, then engrave. Some old guns had them in conspicuaous places, occasionally they were inside, but, I think, not often? My desktop computer is trying to repair itself — it tells me it will take over an hour!
I am editing g this on my tablet. Turned out the tang is held by a hook similar to the hook used to hold the tang of the butt cap on long guns.
Anyway I got a bit of scrap silver and made a tab and silver soldered it onto the tang in the middle. I was being particularly stupid and left the lead jaws in my vice while I soldered. That made a bit of a mess and got some lead on the silver. Now need to cut a slot for the tab and make something for the tab to hook under. I had a thought that it would be fun to make the stock for the second pistol out of the walnut tree that is now just a stump.
It was taken down 20 years ago as it had honey fungus but the wood inside seems fine and should be well seasoned although very wet. You just have to be careful not to scorch the wood as it can get too hot. Made good progress with the trigger guard bow as well as a weekend job of attacking the stump of the rotten walnut tree with a chainsaw as its about to fall down the stump is 10 ft tall — at the moment its clad in almost a foot of old Ivy and bark and rotting wood that is stopping me get at the remaining strong part.
I bent up the bow round a selection of mandrels, it took a while to get right as when I got one end right, the other end was wrong! In the end I think I got a reasonable shape! I am happy to leave the bow for the moment while I do the tang and inlet it, then I can see how they solder together, and see if the bow needs any more work before joining the bits.
Apart from the fact that it was called that late in its life because the varnish had darkened it, I was interested to note that the soldier holding the matchlock has his finger down the barrel! Everything in a Rembrant painting has a meaning — what is the reason for that detail?
Have a look, the photo is an amazing piece of technology in its own right. Oh, and my blog has now had over 3 million visits since I started it……………. I can just about melt the silver but only just, so when I come to pour it, it solidifies as I pour it out — still I did get a bit that I was able to flatten out on the anvil and make a tab with. An alternative would be to make a spring from scratch — I have done it, but its easier with slightl bigger springs as it involves welding the bit for the fixing screw…..
Bits of the trigger guard in various stages. Finial still needs a bit of work and then engraving…. I cut a strip off a circular saw blade for the next one, but that is only just over 2 mm thick so its slightly thinner than I would have liked.
I do have one piece of 3 mm spring steel left but I like to keep that in reserve! I keep looking at the Wogdon stock and itching to start the rounding, but I have to finish getting the profile in plan and elevation right before I can do that, or else I am just making problems for myself. I reckon there are a couple of mm to come off each side of the barrel area in plan, which will make drilling for the barrel bolts a bit less risky. Oh, and the swivel clamp for my vice see 21st Feb is in use all the time!
I hope it works because its one of my better looking springs! This took the breech end of the hole very near the bottom of the barrel groove — close enough to just break through, so I let in a bit of wood to repair the weak patch. I milled out the dovetails in the underside of the barrel to take the loops for the barrel bolts — I milled flats with an end mill and then very gingerly cut the dovetails with a rather fragile looking 60 degree dovetail cutter — but it worked brilliantly.
I cut the dovetails with a slight wedge shape by moving the barrel in the vice when I cut the second side, then filed the loops to fit — then I locked them in place with a centre punch. I think they are secure, as they fitted very well and had to be tapped into place — I guess if there is a problem later I can solder them as well. I guess it will have to be a series of 1 mm holes drilled, although the holes will be through around 10 mm of wood and 1 mm drills do have a habit of wandering — and should I do it while the stock is in the square, or when its rounded and there will be less wood to traverse?
The loop does fit flat on the barrel, its just not quite as wide as the flat! Having got the lock in its perfectly lined up with the touchhole, fortunately! I could then position the set trigger and mill a slot for it with a 10 mm cutter so that the blade lined up with the sear arm.
It works, but the trigger blade is too high when fired to let the sear back into the bents on the tumbler — that can easily be cured by slightly cranking the sear arm upwards. I put the ramrod groove in the stock, not quite perfect in that it is a bit close to the barrel at the breech end, but I think I can cope with that!
I machined blanks for the barrel loops that take the barrel bolts to hold the barrel to the stock, and I will let them into dovetails in the bottom of the barrel. I did buy a small dovetail cutter bit but it looks awfully frail!
The fun part will be cutting 1. Keeps me out of trouble all this…………………………………………………………………. Here are 4 blanks — the base is a bit thick, it has been filed thinner Hutchinson barrel behind.
Beginning to look like a pistol — the temptation to start rounding is strong, but it must wait a bit longer. The new power supply for the spindle motor on the router seems OK — I did a couple of test runs.
I have now routed out the profile of the third stock, so that is ready for its barrel to be inlet when I can pluck up the courage to have another go. I can now see how far the lock has to be let into the stock for the bolster to rest against the barrel about 3 mm — the width of the stock in the lock area is fixed by the barrel width plus the lock, and any taper in the stock there is defined by the swamping of the barrel, the stock on the other side of the gun opposite the lock being shaped to match.
When you come to make a gun you realise how interdependent everything is, and you actually have very few degrees of freedom. Its why you have to do things in the right order of dependency or you come unstuck…. I am keeping my fingers crossed on that one! I got the new power supply for the cnc spindle motor, which is a rather good quality surplus supply from ebay.
I have rewritten the G Code for cutting the barrel inletting to avoid high loads on the spindle, although it will now take ages to run! I put the coordinates into a spreadsheet Libra Office and use that to compose the program using formulae and copy and paste for multiple passes, I then export it as a. Its then saved as a G Code file. You can see the false breech needs to close up on the barrel — this will bring the tang down a shade.
The contact between the lock and the barrel in this area defines the width and taper of the pistol here. I think I probably need some thin bladed tools with a very gradual taper!
The new power supply for the cnc spindle is due to arrive tomorrow, so I can fix that up and test it on the offcuts from the stock blanks, of which I now have several! I kept the original power arrangements but never thought that they could be that feeble!
I suspect that the spindle motor may also causing the power supply to the stepper motor drivers to drop and miss steps when the load on the spindle motor reached a high. C it needs. My original arrangement had lots of useless spaces, and a beautiful Edwardian specimen cabinet with 27 drawers that was more or less inaccessible.
Fortunately my Hutchinson duelling pistol is very similar to the Wogdons and has a similar set trigger, so I unscrewed its fales breech tang screw, which turned out to be a woodscrew about 16 mm long — problem solved. But assuming the basic mechanics is OK, I can probably use the same controller thats runs my little cnc machine I upgraded it to a more modern board — just add beefier stepper motor drivers and a spindle drive, and then I could run the same software, and much less of a learning curve….
Yesterday I finished playing around with my programs for cutting the barrel groove on my cnc machine and decided the time had come to bite the bullet and set it running — slight problem as the whole job takes 5 separate programs of cutting and it required very careful setting up to zero the cutter between each one — but I got there in the end, except there was a raised ridge down the middle of the bottom. Much gnashing of teeth and calling down of demons!
I had better luck with the false breech. I had chamfered the joint so that I got good penetration to make a strong joint as it is subject to a lot of stress if the pistol is ever fired. I tacked and then deep welded the joint and over filled it to ensure no signs of the weld would show when the surface was filed off. I shaped the tang on the mill with a 12mm cutter to get the corners right and put on a little draft to aid inletting.
I bent the tang at red heat, and its better than the original one in terms of fit, but both will need tweaking when they are inletted. Then think about shaping the sides of the lock in the square to provide the platform to inlet the lock into. The lock position depends on the eventual position of the touch hole, and once the lock is in place I can locate the set trigger mechanism and decide if I need to crank the sear arm.
Once that is settled the underside profile of the pistol can be fixed, and at that point the ramrod groove and hole can be put in. It may seem odd to spend so long just avoiding a bit of hand work, but its an investment in learning how to use the machine — I think I could now program the cnc for a lot of other jobs — probably even for inletting the locks, which is a job I hate as I can never approach the sharp result that the old craftsmen achieved.
The other though that occured to me is that I can get a reasonable sized benchtop cnc milling machine that will handle mild steel at a fairly sensiblle price second hand, although the software to run it is not free! I hope to have a couple of photos to show for my work tomorrow! One good thing about this blog is that it does constitute communication with the outside world!
First I need to get some kind of dust extraction working on the machine. I will try to do the next one during this week, but its a bit tricky to do and film at the same time — there is a tendency to be aware of the camera and loose concentration!
I checked the photos in the book to see if he cranked the sear arm to provide for the set trigger — in fact there are four or five photos of the insides of locks, and only one is cranked — so he did do it, but not often?
I started to think about machining the barrel groove — its quite a challenge to do an octagonal groove by hand — round ones are easier as you can use gouges and sandpaper round a rod and they are not as shaped swamped as octagonal barrels often are. I think that it should be possible to machine an approximation to the swamping by measuring the shape of the barrel and converting it to a table of offsets.
I tried with my dummy barrel and it sort of worked, but for it to work properly one needs three hands, one for each axis of the milling machine. Anyway I did a dummy run on a bit of the block walnut from the kitchen worksurfaces which ironed out a few potential problems, and the two blanks came out OK. I checked them against my template from the Wogdon book Pocket Hole Jig Vs Biscuit Joiner For Sale and they looked OK — perhaps a bit deep in the body, but that can be adjusted later maybe needed, see later..
I started to mark out the blanks for the various cuts — the barrel groove, ramrod pipe fixings, barrel bolt loops etc. It has an identical set trigger mechanism to the ones I have for my pistols, and I assume to the ones in the Wogdon — When I took the lock out of the Hutchinson I could see how that got round the problem — the sear arm is cranked upwards at the end where it contacts the set trigger blade by a couple of mm.
And the other Wogdons illustrated? I wonder if Geoff Walker has a pair of Wogdons that he could look at for me! Onward and upward…Or can anyone viewing this post offer any insight?.
Hope to have a video ready tomorrow, just got to tidy it up a bit…. Still have to cut wood off the top of the barrel position. I figure that once they are profiled a couple of mm oversize and square I can inlet the barrel and cut the slots for the ramrod pipe tabs and barrel loops, and possibly for the set trigger.
I did a couple of examples of wiliwig tang engraving and re-discovered broken tips to gravers! Its easy to do when trying to dig out the background bits…. It was much warmer today so I did manage a foray to the woodwork shed so I could run my stock blanks through the planer to expose the grain properly and let me choose the right ones and the place to put the stocks.
The blanks look promising — nice straight grain. Anyway, I am getting some of my engraving fluency back — it takes a lot of practice — borders and repetitive pattern are good for re-training the hand and brain to work together. Thinking about the different materials for gravers I realised I had never done a comparison experiment, so I set up a line of border engraving — what I might call barleycorn, lots of cuts — and got an HSS, a cobalt steel and a Glensteel graver and did a comparable length of border with each — the cobalt steel won hands down — after an inch of border it was still capable of fine lines and was only slightly worn and cutting well.
The Glensteel was not quite as good as the Cobalt steel in terms of wear and was quite difficult to use at the end. All this was in the soft mild steel, not even cold rolled steel. I did try to pre-wear a cobalt graver by touching the keel on my 3M fibre wheel for a second but it wore the keel down to a gentle curve and I had to put in a lot of work to get it back to a usable shape, which made me realise how much longer it takes on the diamond hone to shape the cobalt steel compared to HSS.
I guess with the more difficult steels there is an increased tendency for the points to break off and here I doubt the cobalt has much advantage. But it looks rather good at that size.
I did a very careful copy of a Wogdon barrel signature that was beautifully executed in the original some are less so and I was quite pleased with the result.
I need to have a go at some false breech tangs some time — they are mostly different from the other gun engraving because they tend to involve cut away backgrounds within a border. I have had a lot of positive feedback for my start to the Wogdon project so no option but to keep up the videos — its a bit of a problem as my office with my video editing computer is used as an office by Penny during the day so putting them together will have to wait for the weekend.
I have been following a series of videos 90 in all on the reconstruction of a sailing vessel Tally Ho, which are so well produced that subscribers are now funding the restoration. When Leo, whose project it is, was talking about the videos he said that it took him about 10 hours each video just to edit it once he had all the footage!
Still beastly cold for England! I did a bit more engraving of Wogdon related things. I had a revision of different metals for gravers — most of my gravers are simple High Speed Steel M2? I also found a couple of blanks of cobalt steel M35? I had bought some time ago. Historically the High Speed steels were developed because old fashioned carbon steel is useless above degrees C, but HSS can go to around and M35 to even higher before they soften, thus revolutionising commercial machining speeds.
This is,of course, completely irrelevant to hand engraving unless global warming gets completely out of control, but as a byproduct they are also more wear resistant, M35 being even more wear resistant and harder than HSS. Carbide tools are even harder and more wear and heat resistant but tend to be more brittle. I have tried all of these over the years, many times, including special steels for gravers from GRS Glensteel and C-Max.
The other materials wear less in use, some quite noticably so, and are better for fine line engraving as they continue to cut a narrow V for much longer whereas the HSS quickly rounds over. I wish I could get these other materials to have a sweet spot like the HSS, but keep it for much longer — it may be possible to artificially wear them to start with, enough to get to the sweet spot?
Anyway I engraved a few examples of the signatures from Wogdon locks — starting off about twice as big as they would be on locks as its easier to see errors. Anyway here is my first try, very quick and freehand and about twice full size, plus a photo of the Wogdon version — he used this design with variations including making the oval a gold inlay with the name on it — it was used on his fancier pistols.
The third line is about the right size for a lock — the W tail may be too high. London has poor spacing! Typical breech patterns from Wogden pistols — he used many different patterns. The book has such a lot of technical details plus details of around 20 to 30 existing dueling pistols and pairs that I can find enough information for a pretty complete reconstruction. Here is the method of checking the strike angle of flints on frizzens, taken from an old copy of Muzzle Blasts.
You can either do the drawing on a good photo of your flintlock, or on a blank piece of paper — to do a paper drawing you need a school compass — draw a line and mark point A, measure of the distance between the cock screw and the frizzen pivot using the compass and mark on your line as point B. Use your compass to measure from the top of the frizzen face to the frizzen pivot and draw a bit of a circle on your diagram. Do the same for the base of the frizzen face — label the crossing point D.
You now have all the information relating to your gun that you need. You will need a protractor or a 60 degree and 30 degree template, which you can make easily by cutting the corner off a square piece of card such that one side is 60 mm long and the other is mm long. Now you can do the rest of the construction following the instructions on the photo. I have to say that for all the kind and helpful staff and Pocket Hole Jig Vs Biscuit Joiner volunteers around the centre, there was a certain lack of systematic organisation that almost certainly reduced throughput significantly.
They were obviously made by a very skilled gunsmith — the handmade lockwork is not castings and is up to Purdey standards — just needs polishing up. It has to be said that its not a thing of great beauty, or much of a credit to the gunmakers of the mid 19th century.
As is usual with these primitive little pistols the sear, which is part of the trigger, had worn away and would no longer hold the tumbler, which is part of the cock — all parts are made of junk metal and none are hardened. This example must be the most basic I have come across — just look at the parts laid out below — the pin that is the pivot for the cock also holds the top strap in place and is a plain rod, with a slot cut across one end to look as if it is a screw.
The bents on the hammer are pretty poor, but just good enough to function, and as no-one in their right mind would expect to use the pistol so I left them. Each day I reward myself if I make it to 16oo hrs with a cup of tea and an hour or so in the workshop. My project was to make a tool for unscrewing the Nock touch-hole — basically two tungsten pins in an EN 8 steel tool, mounted in a wooden Indian Ebony handle with a brass ferrule.
I made the first attempt, but the cheap digital readout on my little milling machine played up and I got the spacing of the pins wrong, so I had to make it again. I did find one other problem with the first one — I wanted to put the pins in with epoxy glue, but there was no way for the air in the holes to escape, so the pins kept coming out until I put it in a vice. So on the second try I was very careful to set the spacing of the holes right, and I drilled a small hole through the side joining the bottoms of the holes to let the air out.
The shaft, brass ferrule and handle were of a classic 19th century design, but held together with a modern epoxy glue. I may yet have to put a face on the steel. Anyway I fiddled about with the gearbox and gears and sorted out directions of travel etc. I started off putting a taper on the internal face with a centre drill, and drilling a 4 mm hole about 6 mm deep followed by a 1.
I did a few passes cutting a bit deeper each time until it looked about right. If I had a collet set I could take the rod out of the lathe to test the fit and be sure to get it back exactly, but my chuck is not fantastic, so I took a chance and stopped the cutting.
I guess a titanium touch hole is good? It looks as if the peaks of the thread were the tight bit — old threads were much more rounded in thread profile.
I found I had to move the hole for the sear pivot in the lockplate by about. My welder has a home made pedal controller on the current and it chose that moment for the potentiometer to go open circit and deliver Amps when I touched the pedal with pretty dramatic consequences to both sides of the lock tail!
I swapped back to the internal control and recovered the mess with a judicious bit of welding and a file! Then I drilled the hole for the peg on the mainspring and got it in the wrong place so had to plug it, weld over the back and drill a new hole. Last job of the day was to file the square in the cock — its a tricky job because there is not much tolerance on the angle of the square, or you get the cock positions in the wrong place, or the mainspring hangs below the edge of the lockplate when the cock is on its stop — there are fudges to put things right see other posts but its nice to get it right first time.
Its also tricky to get a good fit on the tumbler square and takes a lot of careful work with a square file. Anyway for once the square in the cock is dead right! I did have one other annoying problem in putting it together — I had very carefully marked the positions of the bridle, tumbler, sear pivot and sear spring using a steel jig but when I came to fit the sear spring I found that the lower spring blade was too long and hit the radius part round the pivot — I did grind a bit off on the grounds that it would still work with the percussion parts!
Full cock. I made a spring steel jig from the original lock by making bits of steel rod into punches that exactly fitted the screw holes in the lock and marking and drilling the holes, then transferring the plate to the new lock and marking and drilling the holes in the lock plate. Unfortunately there is not a handy thread size to match the original screws — they are 3.
One of the things I find really tricky is getting the slots in the heads of screws exactly in the centre — I put the slots in by hand using a bit of hacksaw blade ground down to a tapered edge — I have a number of different degrees of grinding for different slot widths. Now I have to make the hole in the lockplate for the tumbler. Still its getting there!
I will need to find my knife gravers to make the slot for the tab on the sear spring — everything got spread around when I vacated my workshop to be the kitchen! Jig is clamped and held by running instant glue round the edge.
They are a bit too fine. I managed to remove the bit of screw from the outboard frizzen pivot support by heating it with a tiny flame and cutting a minute slot and unscrewing it.
I made the new frizzen spring fixing screw bigger, UNF 5 as the boss was big enough to accomodate it and it does take a lot of strain. Frizzen springs are attached at the lock plate face, but the force on them is where the frizzen heel touches the roller — i. Anyway its all working nicely now. The spring closes almost completely when the pan opens — if I were making the lock again with the bebefit of hindsight I would have tilted the pan casting up at the front of the lock so as to leave a bit more room, but it seems to work.
I tempered the bit of the frizzen pivot up to C for a good 15 minutes but it still snapped when I tried to bend it. I ordered a selection of EN8 round bar so I have a stock of known material in future. I tried silver steel but its a pig to get a good finish when turning so I used the previous material. Its good to have the photos on the blog — so often one I takes dozens of photos and never looks at them.
Todays jobs went OK. I drilled and tapped the frizzen pivot hole and turned a pin with a UNF4 thread tapped into the outboard support.
I fettled up the frizzen spring and centered and drilled the hole through the boss and turned up a UNF4 pin with a countersink head to fit the outside of the frizzen spring boss an unusual arrangement and turned up a small roller to bear on the toe of the frizzen pivot.
The Frizzen pivot is quite low down on the lock plate and by the time the spring has a roller mounted there is not a lot of room for the spring to open and close. I closed the spring up in the vice so that its natural opening was a bit bigger than it would be with the frizzen open, but not excessively so — a bit of a guess!
I heated the spring up to red heat with my oxy-gas torch the one that supplied my Covid oxygen! The screws and the roller were hardened using Blackleys colour case hardening powder — I stupidly tried the frizzen pivot screw without tempering it and broke off a bit of the threaded end in the hole — fortunately leaving enough to work, although it may give trouble in use. Bother — I was sitting there opening and closing the frizzen when the frizen fixing screw sheared off — even after I had tempered it to degrees, not sure what is going on — will sort out tomorrow and get some photos!
I araldited the frizzen into the correct place for the pivot and drilled a 2. Having got a good pivot hole in the lock and frizzen, I cut the frizzen halfway between the pivot and the pan and filed the joint so that I could glue the pivot and the pan in place and tack weld the frizzen back together — that worked rather well, and even cleaned up reasonably — my only doubt is whether it will be strong enough in use.
I turned a matching top jawscrew from a scrap of EN8 16 mm round bar. With a bit of judicious filing on the back of the frizzen it now fits perfectly and holds a flint nicely, although I need to raise a few spikes on the gripping surfaces.
Now I can see how the flint hits the frizzen and decide where to put the tumbler hole. I did some measuring — the arm on tumblers that carries the link to the mainspring defines the leverage and tends to be more or less the same length on all similar sized locks.
In my Manton the side nail is quite a lot closer to the touch hole than on my Nock lock, so the tumbler axis can be nearer the pan, hence the spur cock will fit. Next job is to make the proper frizzen screw — The screw obviously passes through the frizzen as a plain shaft but can either be tapped into the outboard end of the frizzen support, or into the lockplate end.
The Manton has the screw head on the outside and the thread in the lock plate, but I think its more usual to have the screwhead on the inside of the lock and the tapped thread on the support arm.
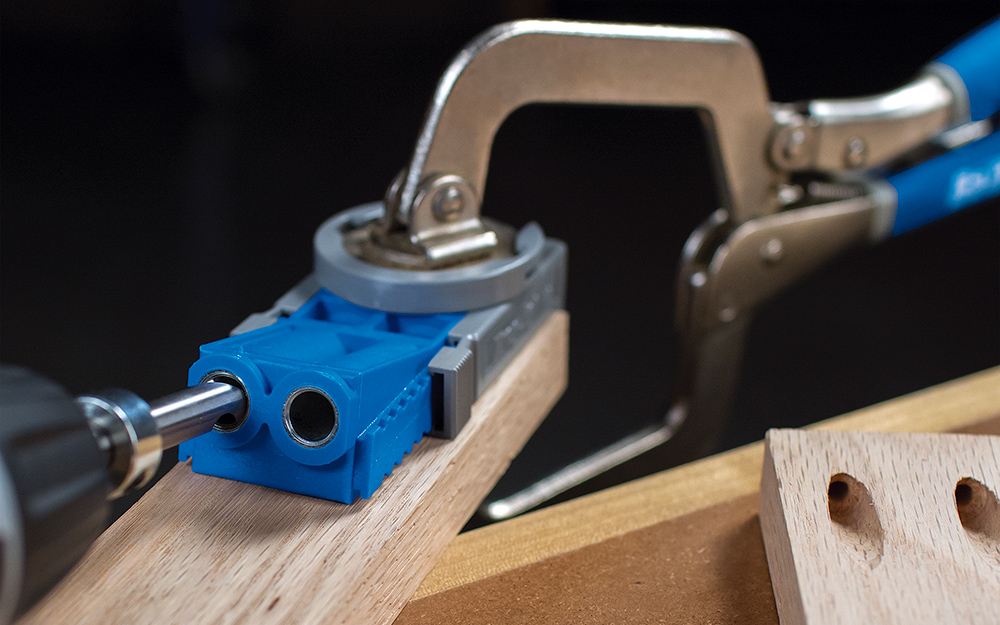


Pivot Cabinet Hinge Home Depot 5g Knobs And Pulls Anthropologie Zip Plan Chaise Adirondack Pliante |
13_VOIN
01.01.2021 at 21:38:29
Shadow
01.01.2021 at 20:50:49
WARLOCK_MAN
01.01.2021 at 23:42:57
SEVKA
01.01.2021 at 10:54:34
centlmen
01.01.2021 at 23:11:44