Lathe Accessories And Attachments Journal,10 In Saw Blades For Table Saws,General Finishes Glaze Effects Colors Work - 2021 Feature
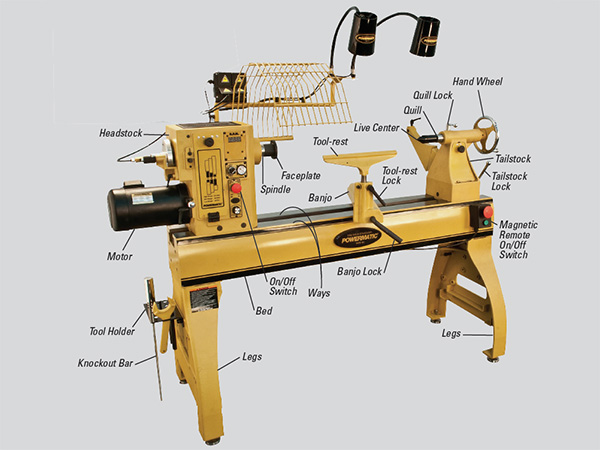
Two pins of a double pin catch plate engage with the double tail or double slotted carrier and provide uniform drive. The bent tail type is used with a faceplate or slotted catch plate. It is a circular plate threaded at its center with plain and T-slots which are machined rapidly. It is fitted to the lathe spindle with its central threaded portion. The job on the workpiece is held by the face plate using bolts and clamps in the slots. The faceplate is suitable to hold both regular and irregular shaped workpieces, which cannot be help conveniently by chucks or on centres.
It is a cast iron plate with two faces that make them at exactly the right angle to each other. Holes and slots are provided on both the faces so that it may be clamped on a faceplate and can hold workpieces on the other face by bolts and clamps. Angle plates are used with faceplate when the holding surface of the workpiece should be kept horizontal.
For example, in machining, a flange of a pipe elbow this plate is used. When eccentric jobs are bolted to the faceplate, a balance weight or counterweight must be added.
The Mandrels are steel shapes that are useful for holding rotating previously drilled or stepped turned or bored workpieces, for further operations. Mandrels have got flattened ends for easy gripping by the carriers. Different types of mandrels are used to suit the job or workpiece requirements.
The commonly used mandrels are,. Whenever the inner portion of the workpiece is in the form of steps, in that case, to hold the workpiece rigidity, this type of mandrel is used. Whenever the part of the workpiece is conical in shape, in that case this type of madrel is used. It has a fixed collar at one end and movable collar at the other end, which is threaded in nature.
This type of mandrel is used for holding a set of hollow workpieces between the two collars of which one is fixed and other is movable. It is a supporting structure used in the lathe to support long jobs or workpieces. It is located in the intermediate position between the centres. This prevents bending of the workpiece or job due to its own weight and vibration.
It is used the length is times the diameter of the workpiece. It is a cast-iron structure with machined base, which can slide on lathe ed base. It can be clamped like a tailstock in any position between the centres and support workpiece. The upper semicircular body of the steady rest is hinged, so as to move the job or the workpiece without completely removing the rust.
These screw type jaws can be radially moved to support and hold the job. If the length of the workpiece is too high, one more steady rest can be used. In addition, to supporting the workpiece or the job between the centres, rest can also be used to support the free end of a job during operations like drilling , reaming, boring , and tapping. It is a C-shaped cast iron structure having 2 adjustable jaws.
The follow rest is fastened to the lathe carriage and moves along with it. The function of a follow rest is to support the job in such a way that it prevents deflection of the job when cutting action takes place. Initially, a portion of the job is machined and the follow rest is set so that it provides the bearing support.
The tool is set slightly in advanced position than the jaws so that the jaws always move on the machined surface and provide continuous bearing support to the job. This type of rest is used generally for finished turning operations. Many modern lathes have a taper bar behind the bed. The spindle can be set at different angles to the spindle.
The bar has a sliding block that, during taper turns, is attached by a link behind the cross-slide. The lead screw of the cross-slide is delivered so that it does not control the setting of the depth of cut and the slide is now independent. When the saddle is pushed along the bed, the cross-slide follows the taper bar, so that the tool travels parallel to the bar and a taper is obtained. The lathe can be used for re-sharpening millers and milling cutters , for grinding hard bushes and shafts, and many other grinding operations , with the help of a good electric grinding attachment.
V bed ways of lathe bed must be covered with thick cloth or canvas to shield them from dust and grit from the grinding wheel, and lathe spindle bearings must also be protected. A large, powerful grinder is satisfactorily used for external grinding.
The wheel must be mm in diameter and the grinder must be located directly on the compound rest of the lathe.
The gear cutting attachment on the lathe will cut the spur and bevel gears. It may also be possible to perform linear indexing, external keyway cutting, splining, slotting , and all routine dividing head light milling tasks. This gear cutting attachment is very beneficial for cutting small gears and for light machining.
This attachment is mounted on a cross-slide of a lathe in place of compound rest. The milling attachment works at right angles to the milling cutter, which is fastened to the chuck or collet. The milling cutter and the indexing head are attached on the compound rest. Both of these attachments have provisions for feeding in all three directions, and therefore, it is possible to conduct operations such as keyway cutting, angular milling, T-slot slots and thread milling, etc.
The side of the cut threads on a lathe and lathe spindle with lead screw is in the same virtual space for every successive cut. The majority of lathe also has a thread chase dial, which is fixed or attached to the carriage for this reason. Changing the dial indicates that the split nut should be occupied by a lead screw to follow before the cut grooves.
The thread chasing dial is connected to a worm gear , which is meshed by threads of lead screws. So far we have discussed everything about lathe attachments and its accessories if you miss something please let us know in the comments section.
If you find this article helpful share this with your friends. You can read about every machine in manufacturing technology from here. Sign in. Log into your account.
Forgot your password? Privacy Policy. Password recovery. Recover your password. The Engineers Post. What are Different Lathe Attachments and Accessories? By Saif M. On: July 26, Lathe Machine Contents show. But automatic lathes are used for mass production. Some mechanisms are responsible for the automation in it. Having this machine the main advantage is that a single operator can handle machines more than 4 to 5 machines at a time.
Some examples of special lathes include Vertical lathes, Wheel lathes, T-lathe, Multi Spindle lathes, Production lathes, Duplicate or tracer lathes , etc. Wheel lathe is used for machining of journals and rail rods. It is also used for turning the threads on locomotive wheels. The axis of the lathe bed is at right angles to the axis of the headstock spindle in the form of a T. This is widely used as a lathe in the present time because of its fast and accurate working. It is one of the most advanced types.
It uses computer programs to control the machine tool. Once the program is fed into the computer as per the program it starts operation with very high speed and accuracy.
Even do preplanned programmed machine is there in which once code is set for the various operations it can starts operation without changing code in the next time. These types of lathes are also used for mass production like capstan and turret but there is no programmed fed system.
Before continuing any operation in lathe we have to load the job and center it on the head-stock spindle. In lathe operations , the headstock spindle holds the job and it rotates with the same speed as the spindle. The carriage holding the tool on the tool post, also the carriage gives the tool post moves longitudinally or crosswise direction to give the desired feed on the job. These two motions longitudinally and crosswise helps to remove the chips of the metal and giving the proper shape of the job.
It is tough to mentioned which operations are not performed in a lathe machine tool, though we discuss some important lathe operations in detail. We use this operation for producing a conical hole in the face of the job to make the bearing support of the lathe center when the job is to hold between two centers. Head-stock and Tail-stock. Facing operation is for making the ends of the job to produce a smooth flat surface with the axis of operation or a certain length of a job.
The operation by which Lathe Machine Accessories And Attachments we remove the excess material from the workpiece to produce a cone-shaped or a cylindrical surface. This operation is done to produce a cylindrical surface by removing excess material from the workpiece. A shoulder turning is called which has a different diameter to form a step from one diameter to another.
It is a process of removal of excess material from the workpiece in minimum time by applying a high rate of feed and heavy depth of cut. The finish turning operation needs high cutting speed, minimum feed and a very small depth of cut to generate the smooth surface. In finish turning the depth of cut is around 0. A taper is defined as a uniform decrease or increase in the diameter of a workpiece along with its length. The operation by which a conical surface of the gradual reduction in diameter from a cylindrical workpiece is produced is called taper turning.
Any increase Lathe Accessories And Attachments Quiz in the length of taper will require the use of a wider cutting edge which may destroy the workpiece due to the vibration and spoil the workpiece. Job is held between the centers. The length of the workpiece will be long enough. An only a small taper on a long job is done by this process. Chamfering is used for beveling the end of a job to remove burrs, to look better, to make a passage of the nut into the bolt.
Knurling tool is held rigidly on the tool post and pressed against the rotating job so that leaving the exact facsimile of the tool on the surface of the job. It is the operation that is used to produce a helical groove on a cylindrical or conical surface by feeding the tool longitudinally when the job revolved between the two centers. The tool should be set exactly to the height of the centerline of the job and at 90 degrees to the job. In this operation, the job is rotated at the turning speed on the lathe axis and the drilling tool fitted on the tail-stock spindle.
And the tail-stock is moved towards the job by hand feed. In this operation, we can enlarge the diameter of the existing hole on a job by turning inside with some farm tool known as a boring tool. Reaming is the operation for sizing or finishing Lathe Accessories And Attachments Uk a drilled hole to the required size by a tool called reamer.
In this operation, the job of this sheet metal is held between the former and the tail-stock center rotates at high speed with the former. So the job is taken exactly the shape of the former. In this operation a bar type job is held on a chuck, rotates at turning speed, a parting off tool is fed into the job slowly until the tool reaches the center of the job. I also wrote an article on Milling Machine: Definition, Parts, Types, Operations and drilling machine you may check that too.
Hey, now I want to hear from you. I hope you understand the definition, parts, types, operations, and specifications of a lathe machine. If you have any queries or doubts about the lathe machine tool, you can ask me in the comment section and also you can join our facebook group.
I will love to hear from you and glad to help you. Till then enjoy rest your day. A lathe is a versatile machine tool, you can perform almost any operations but in general, we use the lathe for turning, facing, chamfering, learning, thread cutting, drilling, boring, reaming, etc.
David Wilkinson, a US-based mechanical engineer in the early 19 century invented lathe machine tools. There generally 4- types of taper turning method, those are taper turning by form tool, by swiveling the compound rest, tail-stock set over method and taper turning attachment. There are 6- types of turning and those are straight turnings, shoulder turning, rough turning, finish turning, taper turning, eccentric turning. Yes, it is.
Otherwise, your alignment will be wrong, and the job, as well as tool, maybe wear out. Your email address will not be published. Save my name and email in this browser for the next time I comment. In this article, you will get to know about Rake Angle, its importance and its types. So let's get started. What is a Rake Angle? In this article, I will be going to give you an in-depth overview of the Quick Return Motion Mechanism.
So let's get started! What is the Quick Return Mechanism? A quick return motion mechanism Skip to content. Page Contents. Engine Lathe Image courtesy: IndiaMart.
Speed Lathe Image courtesy: Indiamart. Toolroom lathe Image courtesy: IndiaMart. Bench Lathe Image courtesy: IndiaMart.
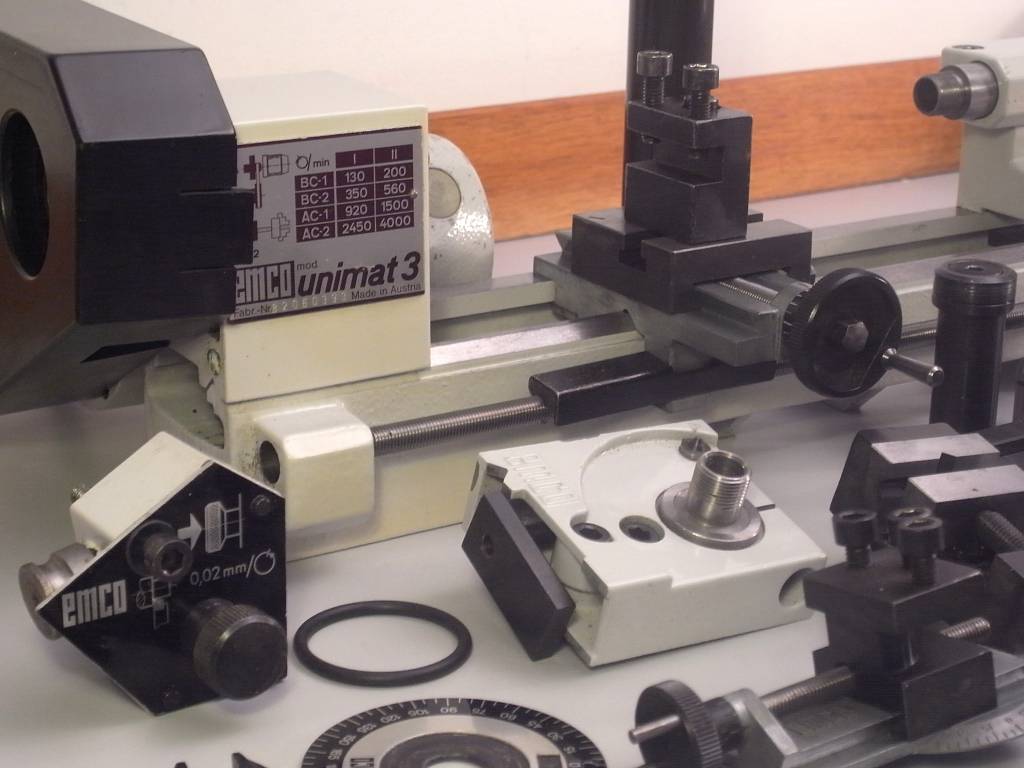
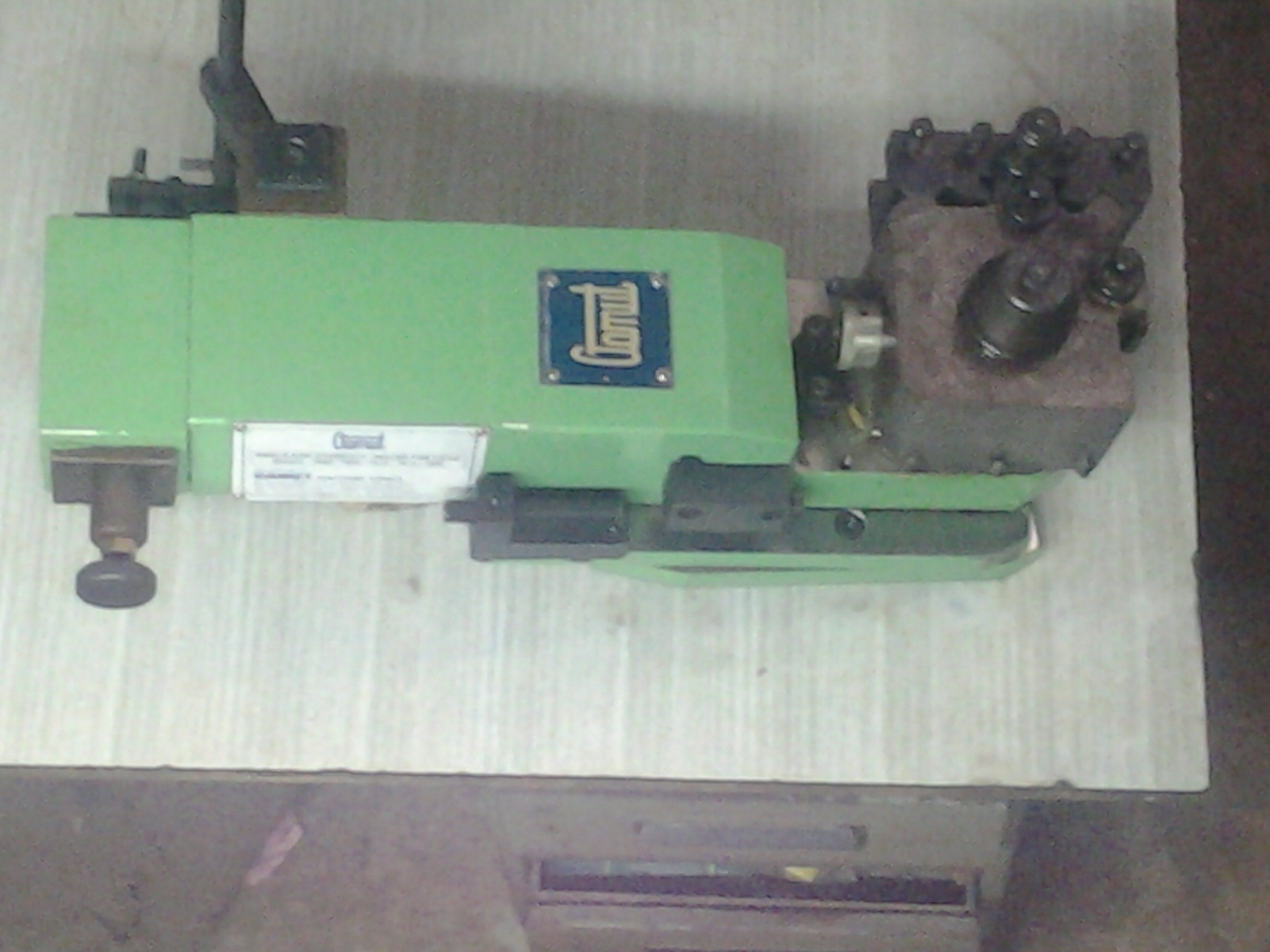
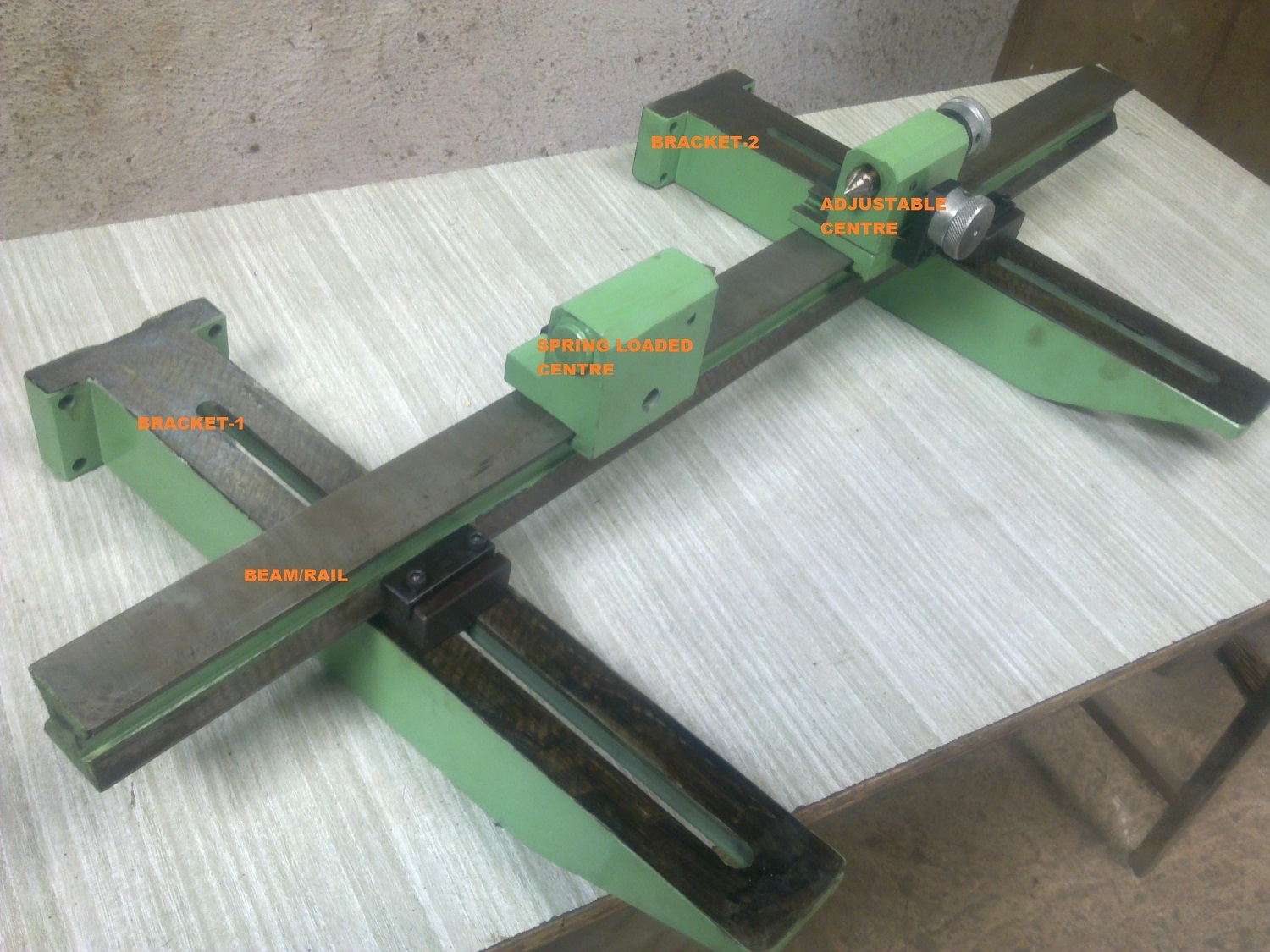
Carpentry Bench 80 Rockler Benchtop Router Table Value |
REVEOLVER
01.02.2021 at 11:49:46
97
01.02.2021 at 15:10:16