Metal Projects To Build Guide,Verizon Fios Router Login 94,Workshop Woodworking Projects 2020,Wood Workshop Philippines 2019 - Review
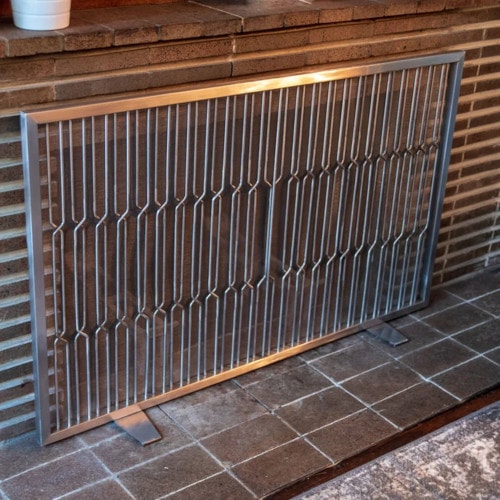
Worldwide Steel Buildings has more than 30 years of experience in the custom metal building manufacturing business. Open since , Worldwide Steel Buildings has been helping homeowners plan, design, and build custom homes made out of steel and metal. With building sizes ranging from square feet to more than 6, square feet , Worldwide Steel Buildings can help you create just about any metal building home that you can dream up. Our metal home kits come with everything needed to erect and build the structure, including trusses, studs, nuts and bolts, and everything in between to build your new home.
We can help you design your custom exterior to incorporate any finish you want, as well as add porches, overhangs, garages, or even an airplane hangar. You can use building materials such as stucco, brick, wainscot, and many other options. We supply the sheet metal, and you can supply your other building materials. Worldwide Steel Buildings produces the strongest, most versatile metal home building kits that the home construction industry has to offer. We are also experts in building codes , clear span requirements and all the other nitty-gritty details that sometimes deter first-timers from metal home kits.
Worldwide has supplied steel building kits in all 50 states and several other countries. Metal building homes are designed and manufactured to meet specific local building codes. This makes Worldwide Steel Buildings a cost-effective solution for home construction. This number would not include things like driveways and sidewalks. Worldwide supplies the structure only. New Century understands the steel home market and is able to assist our customers with their metal house financing needs.
Still have more questions? Check our Frequently Asked Questions page to get more answers, or download our informational guide. Informational Guide. We know you have options. Let our team of steel homes specialists help you plan and design your next dream home or barndominium from scratch. For example, this one has flats on the handle.
To mill the flats, I wait until the hammer is finished and assembled. Then I stick it in a milling vise, dial in the hammer head, and mill one side and add the chamfer. Then I flip it, using the underside as a register for the second flat and chamfer. I also drilled a hole in the bottom of the handle. I use it to fit allen keys, so I can use the hammer as a small cheater bar.
You can make it shallower or deeper to get a hammer balance that suits you. I adjusted the balance between the head Metal Projects To Build 500 and the handle to something I find more comfortable for the light tapping that this type of hammer is more typically used for.
And, since brass is significantly heavier than aluminum, I find that it feels better. This is a good project to get familiar with taper cutting on the lathe. For cutting the self-holding tapers for the inserts, I usually lock the compound rest at the angle and use a single setup to cut both the male and female tapers. If you get a smooth surface, that taper will hold forever.
Either the taper attachment or the offset tailstock method can be used for the handle. This one is good for more advanced students. Traditionally, this has been a project for tool and die makers. The skills that are targeted are job planning with grind allowance and order of operations. Machines used are mills, heat treating ovens, grinders, and lathes. For an extra challenge, try CNC engraving the name of the student in the vise body prior to heat treat and try to make the letters appear even after grinding.
Some schools choose to use , but it can be pretty demotivating when a student rough machines the part, and then has to do it again because it cracked in the oil quench. I went light on this drawing. Personally, I love it, since it helps ensure a working part at the end of the day. Use your discretion with what your students can reasonably measure. Plus I always like how the combination of brass and steel look.
Overall this project will help the beginner learn basic things like slotting on a mill and threading on a lathe. There are lots of non-critical features that are purely cosmetic, but there are a handful that just need to be done right for this thing to work smoothly. A great attachment for making a simple dial indicator even more useful. This is a really good way of checking the depth of shallow steps or seeing how deep a damaged area on a part is. This is the simpler of the two depth attachments.
You can also use it as an opportunity to grind some HSS cutting tools for threading and undercutting. The milling portion is very simple. A simple, handly little attachment for your calipers, this will fit Mitutoyo 6 and 8 inch models. This project gives you a bit of experience on both a mill and a lathe. The project could also be modified to allow for some practice with heat treating and grinding if you want a hardened steel body.
This would have been difficult to accomplish without the equipment. Using a Gradeall to hold truss while bolting in place. Next I placed the permanent purlins. The moveable scaffolding was handy during this step of the metal building construction. The only quality control issue that I found in this steel building package was with the wind bracing rods. The threads were poorly cut poorly leaving gaps on the rods.
However, the way the rods are installed allowed me to position the nuts on the good portion of the threads. It would be nice to have clean threads and minimum torque specs. Constructing this steel building solo, most purlins were not a problem because they sat At Home Building Projects Guide on the trusses and the anchor plates and were held in place by gravity while being bolted down. However, the bottom outboard purlin has nothing to sit on while it is being bolted in place.
So I temporarily screwed notched 2x4s on the ends to hook on the anchor plates while bolting the bottom purlin. After the girts and purlins were in place, it became apparent that our hot Idaho sun during a record heat wave was not being nice to the exposed wood. A downside to constructing my steel building solo is that it took longer, giving the wood more time to twist and bow in the heat. It was so bad that gang drilling the panels would have been impractical.
So I ended up placing blocking at the midpoint of all girts and purlins to straighten them out. Blocking in place on the girts and purlins. The end columns were too heavy for me to lift into place, so I used a forklift and chain hoist. Instead, I should have used a plumb bob.
Forks and chain hoist used to lift door headers. Once the overhead door headers and the overhead doors were installed, I was ready to install the siding. As recommended in the construction plans, it is best to pre-drill the panels.
For this project, I made a jig to hold the bit. That prevented me from having to mark each line while also holding the bit nice and straight. Limit gang drilling to six sheets, but doing so is a major time saver. I framed the windows and man doors to match the spacing of the 3-foot wide panels. That made cutting the panels around those openings easier and saved a significant amount of panel material that I will repurpose later on another project.
The polycarbonate panels on the south wall will allow natural light inside an otherwise dark man cave. The only material shortage I experienced with this order was a foot poly panel, but The Home Depot has similar panels that match the rib pattern on the 3-foot-wide siding.
One glitch I experienced as I started to install the panels was that I placed the closure strips against the trim without measuring. Being offset, they were useless at best. I learned to pre-mark the rib locations and then force the foam strips to match the marks.
Once the wall panels were up, it was time for roofing. The biggest challenge in roofing this metal workshop was how to get foot-long metal panels into place without bending or damaging them. I built a sloped rack for the tractor with a pitch to match the roof and then lifted them high enough to slide into place.
Although it was not included in the design plans, I chose to place a layer of EcoFoil bubble insulation between the purlins and the roofing to minimize and hopefully prevent condensation from collecting on the metal panels and dripping onto equipment below. It was not difficult to add the insulation, but it did add significant time to the roofing placement.
Plus, the reflective insulation wanted to flop around in even the slightest breeze, so at times I had to temporarily hold it down with 2x2s until the roofing was slid into place. The foil side should face the metal. And finally the ridge cap — the last component — is installed. I deviated from the plans and omitted the closure strip between the ridge cap and roofing to provide a continuous open ridge vent.

Cheap Table Saws For Sale Uk Uk Custom Brand Clothing |
Aysel
23.05.2021 at 21:46:10
T_U_R_K_A_N_E
23.05.2021 at 18:53:26