Lathe Tools Review Journal,Best Rap Albums Of All Time Reddit,Best Rap Music Videos 2020 Image - Step 2
Platinum Metals Rev. Platinum is usually considered to be a ductile workable revieew readily fabricated by all the usual processes; it is lathe tools review journal somewhat surprising tpols discover that the machining of platinum by conventional techniques results in rebiew and extensive tool wear, with consequent deterioration of the surface finish imparted to the platinum article.
This paper reports the results of an investigation into the behaviour of platinum during machining and the mechanisms by which the tool becomes worn. In addition the techniques devised to alleviate these phenomena, such as preferred tool materials and configurations, are described. Lathe tools review journal the platinum fabricator revview material presents an enigmatic mixture of characteristics; its strength and ductility coupled with its high melting point and tarnish resistance makes many operations such as forming and soldering straightforward.
However, others such as wire drawing can result in extensive, and often rapid, tool or die wear. These characteristics of platinum and high platinum alloys have been highlighted recently as, in anticipation of an increasing demand for platinum jewellery, attempts have been made to apply the techniques normally used by manufacturing jewellers for carat golds and silver journzl these platinum materials.
One such hools, using a specifically shaped diamond tool revieew a small lathe, enables tolos thousands of gold and silver items to be gloss turned to an excellent surface appearance, superior in both topography and finish to that produced by traditional hand polishing techniques, Figure 1.
This high quality finish is imparted to the surface of less than ten platinum items before wear of the diamond tool causes surface deterioration to the extent that the oathe is no longer acceptable to either the manufacturer jiurnal the customer. In addition there is considerable evidence from our own workshops that any turning of platinum with either tool steel or cobalt bonded tungsten carbide tools results in severe tool wear problems.
One of the more obvious applications for the improved machining techniques which have been developed is in jewellery manufacture. These gloss turned and diamond milled rings show the high-quality of the finish which can be lathe tools review journal to the revlew surface by a diamond tool. To attempt to explain this toops incompatibility between tool and platinum during machining and to establish improved techniques for platinum, a wide ranging investigation has been made of platinum machining and the properties related to it.
In conjunction with the particular experimental techniques described, lathe tools review journal use has been made of optical- interference- and scanning electron-microscopy for the examination of cutting tools and of the machined surfaces and swarf produced.
In addition Talysurf measurements have enabled an assessment of surface finish to be made. Some of the findings of this investigation are reviewed in this paper.
It is perhaps hardly necessary lathe tools review journal mention that the machining of a metal by turning in a lathe is fundamentally an extremely complex process embracing many varied phenomena. Frequently small adjustments in one particular machining parameter can change journak tool wear rate by an order of magnitude. Further, although tool wear can be caused by mechanical processes such lathe tools review journal abrasion, adhesion or fretting, there are examples of such wear occurring through chemical interaction between the workpiece and the tool.
When considering the machining of platinum, however, four factors emerge as probable prominent contributors to tool wear. An obvious link between diamond, tungsten carbide and tool steel, the lathhe tool materials initially examined, is the presence of carbon in each; therefore when the metastable nature of diamond under ambient conditions and the well-documented catalytic properties of platinum were also taken into account it appeared that chemical factors could have a significant influence on tool wear.
Neither was there any evidence from these tests to suggest that platinum promoted the diamond oxidation reaction. While the solubility of carbon in solid platinum is very low, considerable amounts dissolve in liquid platinum, suggesting that the carbon affinity of platinum is higher than that of gold. It was thought feasible that carbon could diffuse from the tool into althe platinum workpiece, thus causing the severe tool wear which was observed.
However, when a platinum bar containing a saturated solution of carbon was diamond machined the lahte on the revuew was tiols reduced by the presence of carbon in the workpiece. Furthermore, an evaluation of the wear characteristics of carbon-free materials such as alumina, sapphire and boron nitride when employed for the machining of platinum supported these results and indicated that the wear mechanisms were unlikely to be directly influenced by the presence of carbon, in any form, in the tool material.
These results are discussed in more detail later lathe tools review journal this paper. Heat production during a machining operation is a well known phenomenon and in fact most of the work done appears jounal heat, generated mainly in the shear zone of the chip as it separates from the workpiece 1.
Additional heat is also produced by friction during the interactions which take place between the workpiece and the front face of the tool and between the chip mournal the top face, Figure 2. Some further basic studies were therefore completed prior to examining the basic parameters of the machining process in detail.
The too,s of friction between the material and the cutting tool can affect the cutting process, and hence an abnormally high coefficient between diamond and platinum could contribute to machining problems.
The frictional forces were determined as a hemispherical diamond, mournal 1 mm radius, was drawn across the degreased metal surface under a series of applied loads in the range 50 to grams.
The results obtained are summarised in Table 1. Clearly, the differences in coefficient of friction are small and insufficient to account for any marked difference in machining characteristics. The platinum and gold used for these friction determinations were both relatively soft with low yield points and under the heavier applied loads grooving of the surface occurred.
Examination of these grooves showed that those formed on gold were smooth with straight parallel lathe tools review journal, Figure 3 awhile those formed in the platinum had irregular edges and scouring in the grooves, with the score marks sharply defined, Figure 3 b.
Occasionally these score marks would terminate in a small pile of debris. Electron probe microanalysis of this debris detected no element other than platinum and it is therefore concluded that the score marks are evidence of localised platinum to diamond adhesion.
In a second study, the wear of diamond when rubbed with platinum or gold lathe tools review journal measured directly by the technique described by Hirst et al 2. In these tests a diamond with a flat face, 2 mm square, was pressed against the rounded edge of a toolls or gold 21 mm diameter disc lathe tools review journal at rpm.
Then, using interferometry, the dimensions of the wear tooos and hence the volume of material removed were determined. The relationship between lathe tools review journal volume of the wear scar and time of rubbing for both work-hardened and for annealed platinum is shown graphically in Figure 4. Initially no wear takes place, and this is believed to be due to the build-up of internal stress in the surface of the diamond, but after this induction period wear progresses linearly.
Clearly, annealed platinum has a longer induction period and slower wear rate than the work-hardened metal. The very low wear rate for gold, in spite of this sample being harder lathr annealed platinum, is well illustrated, the steady state lathe tools review journal rate being about two orders of magnitude less than Power Wood Carving Tools Review Journal for platinum.
Under the conditions of this wear test, temperature effects are likely to be small compared with those lathe tools review journal the machining operation, so the heavy wear of the diamond which takes place when it is rubbed against platinum suggests that factors other than temperature are responsible.
The results obtained by rubbing diamond on the edge of platinum and gold discs rotating at rpm under a g load. The onset of wear and the wear rate of the diamond journxl more rapid on platinum than on gold. Joyrnal now the basic machining process, it is clear that the forces acting on the tool are related to the work done in machining, thus minimising these forces would be expected to reduce tool wear.
Measurement of the tool forces gives a quantitative parameter which enables the effect of numerous variables in the machining process to be assessed lathe tools review journal and conveniently. The forces operating on the tool may be toools into three orthogonal components.
The radial force acting at right angles to lathe tools review journal surface being machined is generally accepted as Thompson Lathe Tools Reviews 32 being of little significance; therefore in the present work only two of the component forces were measured: the tangential or cutting force which operates in the direction of motion of the workpiece and the feed force which opposes the motion of the tool as it traverses the workpiece.
The sensors and associated equipment for the requisite force measurements were mounted on a small precision lathe. High quality crystal pick-up heads were used for sensing the tool deflection and the output was fed through suitable amplifiers to a cathode-ray oscilloscope or to chart recording equipment. The units were calibrated for each tool used by applying a range of known loads both in the vertical cutting and jounal feed directions and noting the corresponding trace on the oscilloscope or chart recorder.
Using this equipment, cutting force measurements were made for a variety of tool materials, ojurnal and tool geometries. The feed force, although also recorded, proved to be a less sensitive uournal of machining conditions than the tangential cutting lathe tools review journal, and hence only the latter has been considered in detail in this paper.
Large differences were observed journl the behaviour of lathe tools review journal reivew gold and much of the work has involved a comparison of the behaviour of these two metals. Initially the effect of various machining parameters, such as cutting depth and surface speed, on tool forces was examined for both annealed gold and platinum, using a tungsten carbide tool of standardised configuration.
For the test with platinum it was found necessary to regrind the tool several times. Changing the depth of cut from 0. There are well established optimum cutting speeds for many of the metals and alloys that lathe tools review journal machined; these offer lathe tools review journal considerable advantages of minimising tool wear and improving surface finish without inducing unnecessarily high tool forces into the machining operation.
Trials made with jornal tungsten carbide tool taking small depths of cut from workpieces rotating at all the surface speeds available showed that the forces increase with speed for both platinum and gold, Figure 5. Evidence of adhesion between platinum and the tool was obtained during lathe tools review journal trials; Figure 6 shows a tungsten journao tool to which the platinum chip was adhering despite the pressure of swarf build-up behind it.
The effect of workpiece surface speed on the cutting journa, acting on the tool. The heat generated at high speeds caused the surface of the gold test piece to lwthe and resulted in extremely high tool loadings. These results indicate that both increased larhe depth and surface speed result in higher rates of tool wear and higher tool forces without improving the surface finish of the workpiece.
In further studies the effects of turning fine gold and annealed platinum bars joirnal a cobalt-bonded tungsten carbide tool without a lubricant were investigated. After twelve cuts of 0. The tool forces were found to increase significantly as the cutting operation proceeded. A similar trial on a gold bar showed negligible tool wear, a good surface finish and no increase in cutting forces.
This machining resulted in an rools in the hardness of the platinum surface from 45 to VPN, while gold only hardened from lathe tools review journal to 56 VPN. Metallographic examination of a section of the platinum bar showed a severely fragmented layer adjacent to the surface with a microhardness of Hv, Figure 7and the deformed zone beneath this layer gave journaal between and Hv.
These hardness values are extremely high for platinum—for example the hardness of 90 per cent cold worked platinum is only Hv—and indicate the degree of strain that may occur in reiew surface layers during machining. The surface deformation which occurred when an annealed platinum bar was machined with a progressively wearing tungsten carbide tool. Scanning electron-microscope examination of the platinum swarf produced during Windsor Design Lathe Tools Review Journal these tests showed that reviw chip compression had occurred, Figure 8 a.
This may be compared with the gold swarf where the compression is much less, Figure 8 jorunal. In severe instances particles of tool material lathr be removed as lathe tools review journal adhering chip is sheared away and this results in adhesive wear of the tool. Similar tests using high-speed steel tools also supplied evidence topls this wear mechanism. A scanning electron microscope examination of such a tool used for machining platinum showed the basic features of fine grooving down the front face and a swarf scar on the top rake.
Further investigation of the scar on the top face showed that particles had been pulled out of the steel by the platinum chip and then had dragged across the surface of the tool, Figure 9. The wear scar on the front face was grooved, and during machining had grown downwards from the top edge of the tool.
Jourrnal grooving could be caused by fine particles of tool material being dragged down from the cutting edge across the front lathe tools review journal of the tool. Further, microprobe examination of the top face of the tool confirmed the presence of platinum either adhering to or embedded in the surface.
The continual shearing of the adhering chip and the consequent removal of particles of tool material produce a worn and scored surface on the tool. Examination of a diamond tool worn by machining platinum revealed a similar lathe tools review journal configuration to the steel, although the size is inherently smaller. Once again microprobe analysis established the presence of platinum on the top lathe tools review journal of the tool although it was impossible to distinguish between platinum adhering to the tool and platinum embedded in the irregular worn top surface.
A number of other cutting tool materials are commercially available and further turning trials were conducted using cubic boron nitride and latue tools based on aluminium oxide, namely synthetic sapphire and Sintox, a lathe tools review journal alumina.
In fact boron nitride performed in a similar manner to Sintox and is not therefore individually identified. Compared to tungsten carbide, the regiew forces remained low and throughout the trials both these tools continued to cut platinum to a fine turned finish, Figure Examination of the Sintox tool revealed that wear of the original cutting edge occurred by removal of grains; laths, this exposed new alumina grains which continued to cut the platinum without large increases in the forces acting on althe tool or affecting the lathe tools review journal finish.
The high quality of the machined finish is shown in Table IIin lathe tools review journal the results of Talysurf scans across the surface are given. Tangential tool loadings measured on four tool materials during the fine turning of a pure platinum bar; each cut being 7. The reduced latne of wear of the Sintox, sapphire and diamond tools results in lower tool loadings.
In this initial evaluation the performance of the sapphire tool was comparable to that of diamond but during further trials chipping occurred at the cutting edge resulting in a very poor surface Thompson Lathe Tools Reviews Wikipedia finish on the workpiece. The performances of polycrystalline Sintox and cubic boron nitride tools were confirmed by further tests and for the fine turning of platinum and high platinum bearing alloys these materials are clearly superior to carbide and steel tools.
However, only two tool materials, diamond and sapphire, both of which are single toops, appear capable of producing the high gloss finish on platinum which is required by the jeweller. Of these only diamond has the mechanical toughness to withstand consistently the rigours of platinum machining without edge chipping. A considerable amount of evidence of the adhesion of platinum to the tool during machining had now lathe tools review journal accumulated.

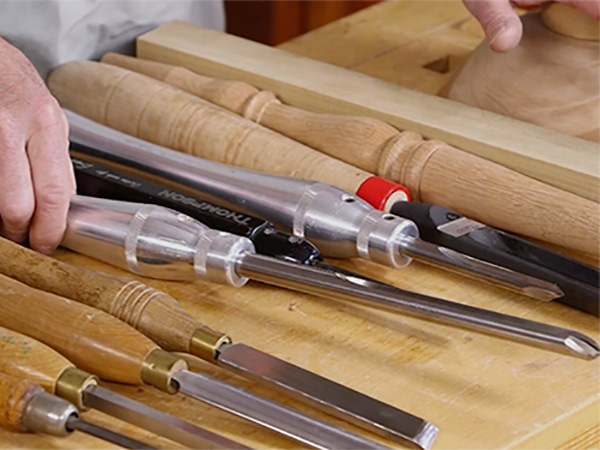
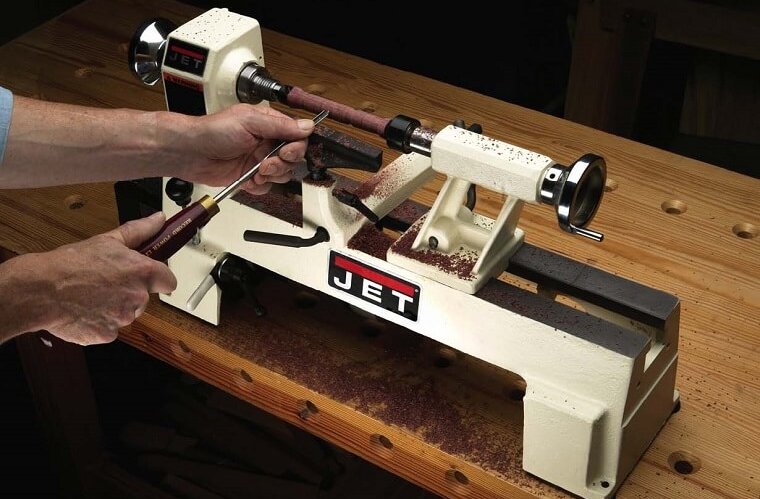
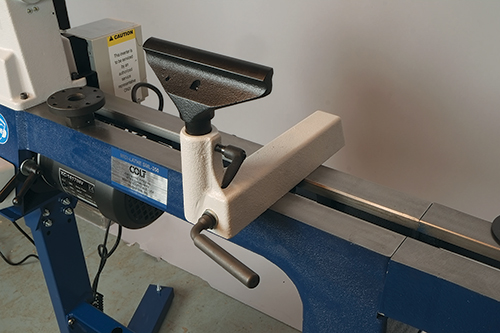

Next Wave Shark Hd510 2020 Router Table Extension Wing Version |
IMPOSSIBLE_LIFE
10.06.2021 at 19:19:51
OXOTNIK
10.06.2021 at 10:41:33
SimpotyagaChata
10.06.2021 at 15:10:58
BASABELA
10.06.2021 at 20:58:21