Joiners Workbench Design Report,Rasp Tool Security,Router Wood Tool Example,Useful Home Woodworking Projects Pdf - Step 3

Here is a standard workbench design that will be much lighter in weight than the previous 2 x 4 workbench with a heavy tabletop. Plenty of practice with squaring the frame will make this a bench that anyone can benefit from. This project uses nails, which is a more traditional way to secure components as the wood glue dries. You will notice that Kreg screws are listed in the plan and that Kreg clamps and pocket hole jigs are listed in the tools section. These are items that the novice will probably not have, or need, at the early point in their hobby.
A sheet of Birch plywood is suggested here. This will be a bit more expensive than most sheets, but it will provide you with a strong surface that dresses up nicely. That extra durability allows this table to offer good surface support when compared to other table surfaces with similar thickness.
That wider lumber will be used in the leg portions of the workbench. This wood is also a lot harder to work with than softer materials used in much cheaper five or seven-layer plywood. Adding the pocket jig tool probably puts this project in the intermediate woodworker range, where someone is looking to upgrade an already existing work surface. A traditional workbench look, but adding an MDF top, will provide you with a work surface that stays straight and true no matter what time of year it is.
There is a lot of new hardware to look at for this build. That includes metal rods, S-clips, and levers. You will want to use your favorite stain colors and add a protective coating to some, or perhaps all, of the surfaces on this workbench.
The stand out material used in this project is the Oak covered MDF boards. This will give your bench a traditional look. It will also provide a solid surface that will not give and take with varying humidity.
Oak hardwood can be used wherever you would like, but it will be a necessity for the vices if you install them. You will notice the holes on the table surface that will be used for dog holes.
Various dowels and pre-made components can be sourced for these holes, including bench dogs and various clamps. This project is perfect for intermediate and advanced woodworkers. Especially those that work with hand tools. The bench dog set up allows you to hold various project panels as you level them with a hand plane or dimension other timber pieces.
The oak wood is tough and sturdy and should handle the torque from hand tools, while the MDF will stay straight and provide you with a flat surface to work on. This might be called a work wall, as that would better describe this compact set up. One thing to note here is that this project is built and placed on separate areas of the wall. Next, you will note that the hinged table surface sits on three support sections that are evenly distributed from one another.
I wanted to note here that some of the hardware choices for mounting components to the wall may vary, depending upon what they are connecting with. Thinner 1 x 1.
If not, you can dimension down extra 2 x 4 pieces. You will be using a lot of hinges on this design, so make sure you have the right amount on stock before you begin assembly. This DIY workbench plan is for anyone who has limited room. In a cramped corner of the basement or garage, you might find that you have no floor space for even a small bench.
This wall-mounted system not only provides you with a work surface. It will also help to hold and organize tools and small objects you want to store.
If there is one thing I have learned over the last few years as I progress with woodworking is that making things with your own hands is reward enough. Finally, no matter what, be safe and have fun. Your email address will not be published. Save my name, email, and website in this browser for the next time I comment. Like this article? Share on facebook. Share on twitter. The series can be purchased by Clicking Here If you're already a Member then you may need to Login first The Bench Design The French workbench is simple and strong - just how a bench should … [Read more When owt gets born there's blood, sweat and faecal matter.
That's just a fact. Giving birth to a workbench is the same. It's been a while since I've built a bench and I have to say I've been twitching for quite some time to do one. Now, if you've been lingering around from our old days you may remember this thing. It was rather nicely given to me by my good friend Richard Arnold. If you know anything about the way that I work then you'll know that I don't like to faff. I will always do a proper job though, in fact I tend to do things somewhat overkill.
But when it comes to the tools and techniques used I'll always find the most basic and simple route. I'm no different … [Read more Recently I wrote a post about why you don't need a tail vice on your workbench.
Remember those fire safety tips you used to get in grade school, about the dangers of oily rags? It was linseed oil they were talking about.
All oily rags are dangerously flammable. Linseed oil will self-combust. Linseed oil doesn't evaporate, it oxidizes. The oxidization generates heat, and the increased temperature increases the rate of oxidation. Linseed oil sitting in a bowl, or spread on the surface of wood, is perfectly safe.
But a linseed oil soaked rag provides a vastly increase surface area, so the oxidation happens faster, and the rag can provide insulation, trapping the heat.
The increased temperature speeds up the oxidation even more, which raises the temperature even more, and the runaway feedback can quickly result in temperatures that will cause the rag to spontaneously burst into flame.
This isn't one of those "do not drive car while sunscreen is in place" warnings. This is one of those "keep your finger off the trigger until you have the gun pointed at something you want to shoot" warnings.
Rags soaked in linseed oil will catch fire, if you don't handle them properly, and they can do so far more quickly than you might think. Hang them up outside, away from anything combustible, and where there's enough air circulation to keep them cool. Or put them in a bucket of water, and hang them outside later. If you're just setting a rag down for the moment, set it out flat, without folds, on something non-flammable.
Hanging outside in the breeze, the oil in the rags won't retain heat while they oxidize. For the oil to completely oxidize can take in a couple of days, if it's warm, or more than a week, if it's cold and rainy. When fully oxidized, the oil will be solid and the rags will be stiff. At that point, they're safe, and can be thrown in the trash. Toss them in the trash before that, and you might as well say goodbye to your garage.
Before you start cutting or drilling the pieces that will make up the top, determine the layout of the top. This should include the dimensions of the MDF, the dimensions of the edging, the locations of the vises, and of the screws or bolts that will support the vises, and of all of the benchdog holes and of all of the drywall screws you will use to laminate the panels, If you don't lay it all out in advance, you could easily find that you have a bolt where you need to put a benchdog hole, or something of the sort.
I sketched out ideas on graph paper, then drew the plan full-size on the top side of the bottom layer of MDF, using the actual parts as templates. The width of the top is determined by the width of the base. The length of the top depends upon the vise or vises you uses. The end vise I had purchased was intended to be used with hardwood jaws that extend the width of the bench.
I had a piece of 2x6" white oak I intended to cut down for the purpose. The decision to be made with respect to the end vise is whether the support plate should be mounted to on the inside or on the outside of the stretcher.
Mounting the plate on the inside of the stretcher reduces the reach of the vise - it can't open as far, because the support plate is back from the edge by a couple of inches. But mounting the plate on the outside of the stretcher means that we need to add some support structure for the inner jaw of the vise, which the legs would have provided if we'd mounted the plate on the inside.
I mocked up the two scenarios, and determined that with the plate inside the stretcher the vise would have a reach of 8 inches, and with it outside the stretcher it would have a reach of 9 inches.
I decided that 8 inches was enough, and that the extra inch wasn't worth the extra effort. With the end vise mounted like this, the right edge of the top would have no overhang. I wanted the left edge of the jaw of the front vise to be flush with the left edge of the top, the right edge with the left edge of the left front leg.
So the amount of overhang on the left depends upon the width of the front vise jaw. The width of the jaw is, at a minimum, the width of the plate that supports it, but it's normal to make the jaw extend a bit beyond the plate. How far? The more it extends, the deeper a bite you can take with the edge of the vise, when, for example, you are clamping the side of a board being held vertically.
But the more it extends, the less support it has. What you need to determine, by this drawing, is where you need to drill the dog holes, the mounting holes for the vises, and where you will put the drywall screws you'll be using for the lamination. As well as where the edges of the top will be cut. The next step is to laminate the two sheets of MDF that will make up the lower layers of the top. First, trim the MDF to slightly oversize. You'll want room to clean up the edges after the pieces are joined, but you don't need more than a half-an-inch on each side for that, and there's no point in wasting glue.
If you're lucky enough to have a vacuum press, use that. Otherwise drill holes for the screws in the bottom layer at all the points you had indicated in your layout.
You'll also want to either drill a row of screws around the outside edge, in the bit you're going to trim off, or you'll need clamps all around the edge.
I just added more screws. The screw holes should have sufficient diameter that the screws pass through freely. You want the screw to dig into the second layer and to pull it tight against the first. If the threads engage both layers, they will tend to keep them at a fixed distance. If you're using drywall screws, you'll want to countersink the holes.
Drywall screws are flat-head, and need a countersink to seat solidly. If you're using Kreg pocket screws, the way I did, you won't want to counter-sink the holes. Kreg screws are pan-head, and seat just fine against a flat surface. Both drywall screws and Kreg pocket screws are self-threading, so you don't need pilot holes in the second sheet of MDF. Regardless of which type of screw you use, you'll need to flip the panel and use a countersink drill to on all of the exit holes.
Drilling MDF leaves bumps, the countersink bit will remove them, and will create a little bit of space for material drawn up by the screw from the second sheet of MDF.
You want to remove anything that might keep the two panels from mating up flat. I set a block plane to a very shallow bite and ran it over what was left of the bumps and over the edges. The edges of MDF can be bulged by by sawing or just by handling, and you want to knock that down. After you have all the holes clean, set things up for your glue-up.
You want everything on-hand before you start - drill, driver bit, glue, roller or whatever you're going to spread the glue with, and four clamps for the corners. You'll need a flat surface to do the glue-up on - I used my hollow core door on top my bench base - and another somewhat-flat surface to put the other panel on. My folding table was still holding my oak countertop, which makes a great flat surface, but I want to make sure I didn't drip glue on it so I covered it with some painters plastic that was left over from the last bedroom we painted.
Put the upper panel of MDF on your glue-up surface, bottom side up. Put the bottom panel of MDF on your other surface, bottom side down.
The panel with the holes drilled in it is the bottom panel, and the side that has the your layout diagram on it is the bottom side.
Chuck up in your drill the appropriate driver bit for the screws your using. Make sure you have a freshly-charged battery, and crank the speed down and the torque way down. You don't want to over-tighten the screws, MDF strips easily. Once you start spreading glue, you have maybe five minutes to get the two panels mated, aligned, and clamped together. So make sure you have everything on-hand, and you're not gong to be interrupted.
Start squeezing out the glue on one MDF panel, and spreading it around in a thin, even coating, making sure you leave no bare areas. Then do the same to the other MDF panel. Then pick up the bottom panel and flip it over onto the upper panel. Slide it around some to make sure the glue is spread evenly, then line up one corner and drive in a screw.
Line up the opposite corner and drive in a screw there. Clamp all four corners to your flat surface, then start driving the rest of the screws, in a spiral pattern from the center. When you're done, let it sit for 24 hours. The edges of MDF are fragile, easily crushed or torn. MDF is also notorious for absorbing water through these edges, causing the panels to swell.
This edging is one of the complexities that Asa Christiana left out in his simplified design. I think this was a mistake. MDF really needs some sort of protection, especially on the edges. Of course, I, on the other hand, with my Ikea oak countertop, probable went overboard in the other direction. I clamped the countertop to my bench base, and used the long cutting guide. I'd asked around for advice on cutting this large a piece of oak, and was told to try a Freud Diablo tooth blade in my circular saw.
I found one at my local home center, at a reasonable price, and it worked very well. Remember, you want the width of the top to match the width of the base, and you're adding edging. First, cut one long edge. Second, cut a short edge, making sure it's square to the long edge you just cut.
Finally, cut the remaining short edge square to both long edges. The length of the top doesn't need to precisely match anything, so we don't need to bother with clamping the trim before measuring. Glue up the trim on the end, first. Do a dry fit, first, then as you take it apart lay everything where you can easily reach it as you put it back together again, after adding the glue. To help keep the edge piece aligned, I clamped a pair of hardboard scraps at each end.
I used the piece of doubled MDF I'd cut off the end as a cawl, to help spread the pressure of the clamps. Squeeze some glue into a small bowl, and use a disposable brush. As you clamp down, position the trim just a little bit proud of the top surface. Once you have all the clamps on, take off the scraps of hardboard. You can clean up the glue squeezeout with a damp rag.. When the glue is dry, trim down the strip flush with the panel using a router and a flush-trim bit.
Then cut off the ends of the strip with a flush-cut saw, and clean up with a block plane, an edge scraper, or a sanding block. Leaving the ends in place while you route the edge helps support the router. The strips along the front and back edge is glued up the same way. I suppose you could try to glue both on simultaneously. I didn't try. When the top is done, we want the edged MDF and the oak countertop to have exactly the same dimensions, and for their width to exactly match the width of the base.
I could see three ways of doing this: 1, join the MDF to the countertop and use my belt sander to sand down their joined edges to match the base; 2, join the MDF to the countertop and use a hand plane to plane down their joined edges to match the base; or 3, use a flush-trim bit against a straight edge to route the MDF to the width of the base, then join the MDF to the countertop and use the flush-trim bit to route the countertop to match the MDF.
So I chose option 3. If you choose the same, you want to trim the edges of the MDF layer prior to joining it to the countertop. In other words, now. Put the MDF on the floor, bottom up.
Flip the base and place it on the MDF. Line up the base on the MDF in the posiiton you feel best, then mark the position of the legs. Sorry, I have no picture of this. Flip the base upright, put the MDF on top of it, then use a straightedge to draw two straight lines joining the outside edges of the legs and extending the width of the MDF.
I used the countertop as the straightedge. Use a carpenter's square to transfer these lines onto the ends of the MDF. Put the countertop on the base, put the MDF on top of the countertop, and line up the marks you drew on each end of the MDF with the countertop below it.
I clamped a couple of scraps of doubled MDF at each end to give the router base something extra to ride on at the ends. Edge-trimming endgrain can result in tearout at the right side, so route the short edge before you route the right long edge. Routing the right edge can then clean any tearout that occurs on the short edge.. When gluing the oak edges on the MDF, I made a mistake. On the back side, the edging was positioned too low, which would leave a noticeable gap when the MDF and the countertop were joined.
I was determined to fix it. Either of the strips I'd ripped from the oak countertop to remove the factory bevel looked like it would work, if I could figure out how to rip them safely with a circular saw. I ended up using a couple of strips of MDF and a bar clamp to create a clamp that would hold the strip of oak, and had a profile low enough to fit under the cutting guide.
Once I had the strip cut, I glued it in place, and clamped everything up. I'd intentionally made it oversize, intending to trim it flush. Trimming is a little more complicated than usual, because I needed to trim it flush on two faces.
Aside from the use of the edge guide, flush trimming the edge face was unremarkable. For trimming the top face, I again stood the panel vertically, with the router base riding on the top edge, and the bit cutting on the far side of the panel.
Because I was cutting on the back edge of the work piece, I needed to move the router from right to left. And here I ran into another problem. The gap in the edging that I was filling was not of even depth. That means that on the right side, I was routing away all of the strip I had glued in. The result was significant tear-out. I did what I always do when faced with this sort of gumption trap - I turned off the router, set it down, and walked away for a bit.
I've found that whatever action I take in the frustration of dealing with something that hadn't worked right is almost always the wrong one, and usually makes things worse. What I did, when I came back, was to clamp down the strip where it had torn away, and then to start routing from the other end.
I still moved the router from right to left, but I did it in six-inch sections, taking light passes, and sort of whittled the strip flush.
As the sections I was working were farther to the right, the strip was thinner. Eventually I came to where I was trimming the strip away entirely, at which point I took off the clamps and the remainder fell away. A better solution would have been to route a rabbet into the side, so that the added strip always had thickness. The way I did it means that the strip I glued in is very narrow, and hence very weak, at a certain point.
In this case, that's not a problem, because it's going to be sitting under the countertop layer. I also noticed that because I had only clamped the strip down, and not into the edge, there was a noticeable glue gap where the strip butted up against the MDF. Again, in this application it isn't visible. But if I was doing something like this on the top of a table, I'd make sure to cut a clean rabbet, and to clamp both down and in.
So while for the end vise, if we mount it lower, we can make both the jaws deeper to compensate, for the front vise we cannot, so we want it mounted as close to the edge of the bench as possible.
It's usual to attach vises with lag screws from the bottom, but there is a limit as to how many times you can tighten up a lag bolt in MDF. I decided to use bolts from the top down, embedding the heads of the bolts inside the top. First step was to cut a piece of MDF the size of the base of the vise. I scribed the positions of the bolt holes in it, then driilled small pilot holes.
I also drilled larger holes at the corners of the rectangular cutouts, and the joined them with a jigsaw. Then I flipped the top and the base, lied up the base in the proper location relative to the top, I then positioned the front vise and the support MDF for the end vise, and marked the locations of the bolt holes. Then I flipped the base right side up, drilled small pilot holes from the bottom side where I had marked the locations, and then drilled shallow countersink holes from each side, then a through hole that matched the bolts.
Finally I tried out the bolts and washers, and deepened the countersinks until the heads of the bolts were just below flush. With the holes and countersinks in place, I inserted the bolts, used tape to keep them from falling out, flipped the top, applied glue to the support piece of MDF, fit it over the bolts, added washers and nuts, and tightened it down. The reason I'd cut out the rectangles in the vise support was that I'd intended to put a benchdog hole through each, and I wanted the thickness of the top to be the same for all of the benchdog holes.
Where I messed up was in not cutting out the ends, between the bolt tabs. I'd intended to put a benchdog hole through there, as well, but I'd forgotten to cut out the segments prior to glue0up. No matter, It was only twenty minute's work to route out the areas flush with the top,. You'll want to get as much done on each of the two layers of the top separately, before we join them, because handling the top after the two layers are joined is going to be a major hassle. So drill the benchdog holes through the MDF layer.
Begin by laying out their positions. You'll want these to be precise, so that the distances between the holes are consistent. The vises you are using will constrain your benchdog spacing. My front vise worked most naturally with two rows of holes four inches apart, my end vise with two pairs of rows, with four inches between the rows and eight inches between the pairs.
Because of this, I decided on a 4" by 4" pattern. I lined up the template, and drilled a second hole, then put another bit through that. From then on, I worked entirely from the template. With two bits through the holes pinning the template in place, the other holes in the template would be precisely located or so the theory goes on a 4x4" grid.
Having done all this, I'm not sure I'd do it this way again. It might well be faster to layout the positions with compass and straightedge directly onto the top. Either way, you'll want to use a scribe rather than a pencil. Scribe lines are hard to see, and impossible to photograph, but the scribe and compass points click into them, allowing a precision that pencils simply cannot match. Once you have all the positions marked, drill them through. Drilling this many holes in MDF burns up bits.
You're going to need to either buy several bits or learn to sharpen them. Forstner bits produce holes with cleaner edges than spade bits, but they cost more and they're more difficult to sharpen. With my layout, I needed to drill 52 precisely located holes. I didn't get every one of them right. If you should drill a hole in the wrong position, if it doesn't overlap the correct position you can just ignore it. If it does, you'll need to fill it.
Wipe up any glue squeeze out with a damp cloth. The next day, cut it flush. Use a block plane to ensure it truly is flush. This will be the top of the bottom layer of the bench top, so gouges aren't a problem. Wiping up glue with a damp cloth can lead to stains and finishes applying unevenly. That won't be a problem here, either. But bulges and bumps are a problem - they will keep the two layers of the top from matching up evenly.
Then mark the proper position, and drill it again. There are a few tasks left on the MDF layer, prior to joining it to the countertop layer. First, we need to drill out the holes for the screws that will hold them together. The oak countertop, like any natural wood product, will expand and contract with humidity changes.
If it were glued to the MDF, the difference in expansion of the two layers would cause the countertop to buckle and curl. For that reason, all of the screw holes except one row along the front edge should be drilled oversize.
This gives the wood a bit of room to move. For the most part I drilled through the existing holes left over from laminating the two sheets of MDF.
In a few instances I moved a hole over a bit because it was too close to a benchdog hole. And I created a new row of holes around the outside edge, because our original holes along the outside edge were cut off as we trimmed the MDF to size.
Keep an eye on what will be underneath, you don't want the head of the screw to get in the way of the stretchers, legs, or vises. Practice on some scrap, first, to make sure you have the depth on the bit set right,. The end vise needs holes through the end stretcher. I marked the holes by putting a dowel center in the end of a long piece of 1" dowel.
Run it through the holes in the base plate, and bang on its end with a mallet. Rotate it a bit and bang it again, and repeat. Odds are the dowel center won't be precisely in the center of the dowel, so you'll be making a small ring of marks.
The center of the hole is, of course, the center of that ring. You can see my high-tech air-scrubber in one of the pictures. This helps a lot in keeping down the really fine dust that the shop-vac doesn't pick up. We need to cut it to length, and to width. We need to mark and drill the pilot holes for the screws. We probably don't really need to oil the surface between the two layers, but I decided to do so, anyway. I decided to drill pilot holes in the oak.
Just to make sure, I did a test hole in the scrap piece I'd cut off. That scrap piece of oak looks like I'll be able to use for something, maybe a cutting board.
So I made a platform out of a stool, a scap of 4x4, a couple of srtips of MDF, and some shims, to catch it, as it was cut. My test hole was done at the edge, so as to leave as much of the piece clean as was possible. The last thing is to semi-permanently attach the bolts for the vises. Given the amount of work necessary to get to the bolt heads, once the top is joined, I had intended to tighten them up so they wouldn't spin, and lock them that way with blue Loctite.
That's the strongest non-permanent grade. That didn't work. What I found was that the bottoms of the countersinks weren't quite flat, and when I tightened the nuts down that far, the ends of the bolts would be pulled far enough out of alignment that the vise bases would no longer fit.
In order for the vises to fit over the bolts, I had to leave the nuts loose enough that the bolts had a bit of wiggle - which meant that they were almost loose enough for the bolts to spin. So I put Loctite on the nuts, to keep them from unscrewing, and filled the countersinks with Liquid Nails, in hopes of keeping the bolts from spinning. I considered using epoxy, or a metal-epoxy mix like JB Weld, but I didn't have enough of either on hand.
It seems to be working for now, though the real test won't be until I have to take the vises off.
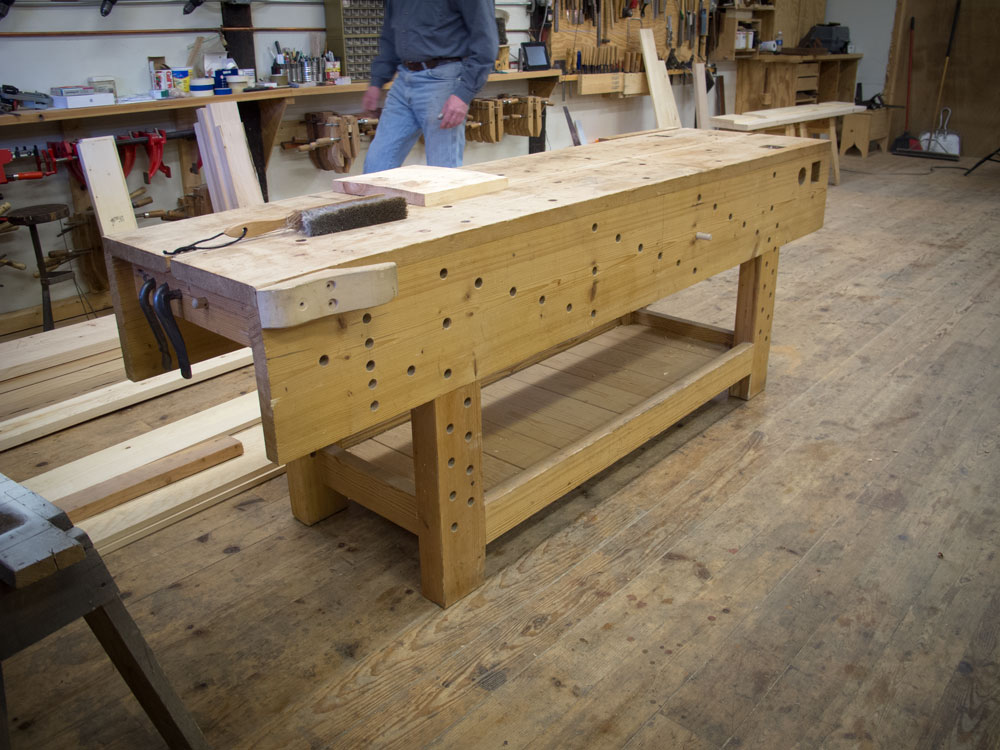
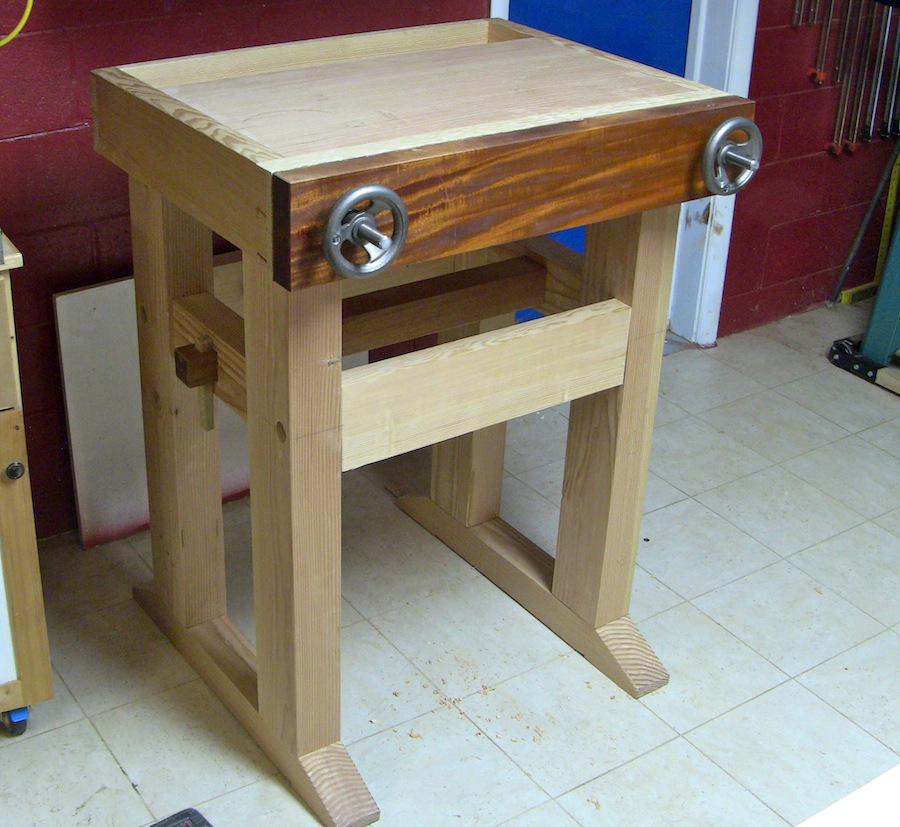

Computerized Carving Machine Wood Registration Wood Filing Tools Machines |
PRIZRAK
28.10.2020 at 18:49:26
qedesh
28.10.2020 at 11:24:59
Sevgi_Qelbli
28.10.2020 at 10:23:28