Best Miter Gauge 2018 Steam,Kreg Drill Guide Block Free,Building Projects From Wood Equipment - Tips For You

Concrete shall be allowed to slide or flow or shoveled by any mean if segregation of constituents is not occurring. Concrete dropped into place shall be dropped vertically. It shall not strike the formwork between the point of its discharge and its final place in the work, and except by approval of the Engineer, it shall not be dropped freely through a height greater than 1.
In wet weather, the concrete shall be adequately protected as soon as it is placed. No concrete shall be placed in conditions of heavy rains if the total concreting process is not covered. No concrete in periods of dust storms. Special care required against drying winds. Records of delay due to dust storms to be prepared. Before continuing concreting the exposed concrete face shall be thoroughly wetted at constructions joints. Level pads with cement mortar top levels of the concrete will be established prior to the inspection.
Records showing date, time, temperature and weather conditions will be established for each concreting. Where permanent formwork is incorporated in the structure, extra care is required, as full compaction of the concrete cannot be checked after the formwork is removed.
Where concrete is to be placed on the rock, loose, shattered or unsound rock fragments shall be removed. Immediately before placing the blinding concrete the rock surfaces shall be thoroughly wetted so that water is not absorbed from the blinding concrete. Vertical faces of strip footings, bases and slabs may be cast against the faces of excavation provided: a.
Prior approval is obtained b. The faces are sufficiently accurate and stable c. Support to faces is withdrawn progressively as concrete is placed d. Adequate measures are taken to prevent contamination of concrete e.
Faces of the wall must be cast against formwork 3. No concrete shall be placed in a foundation until the extent of excavation and the character of bearing material have been approved and no concrete shall be placed in any structure until the placement of reinforcing steel and the adequacy of the forms and falsework has been approved.
Unless otherwise shown in the drawings or specified elsewhere, all concrete placed below ground level shall have a minimum protection to its outside faces as follows: a. Underside — Protected by the laying of a grade approved polyethylene sheeting on the blinding concrete. The sheeting shall be returned up the outside faces of the concrete and suitably sealed.
Sides — Coated with 3 coats of an approved bitumen rubber latex emulsion flexible damp and vapor-proof liquid membrane conforming to BRE Digest No. Arrangements for premature stoppage of a pour shall be agreed and in place before work starts.
Should premature stoppage of a pour occur, the Contractor shall notify the Engineer and agree with him the extent and timing of any necessary remedial work before the resumption of placing. Coring tests or Non-destructive testing may be required as directed by the Engineer, to verify the quality of the concrete bonding interface. After reaching the formation level, the final level will be controlled and monitored by the Surveyor.
The final level of excavation will be trimmed, cleaned, thoroughly compacted and consolidated. Rollers and plate compactors will be deployed at the formation level to carry out compaction works, as necessary. Any loose, improperly compacted, soft or other unsuitable material which is encountered below or adjacent to structural foundation levels will be completely removed, backfilled with a Class C25 Concrete.
After preparation of the surface, installation of earthing shall be done prior to cast blinding concrete. The Surveyor shall be responsible for the control and monitoring of the final levels of blinding concrete.
After curing and obtaining approval of the blinding concrete, a surface preparation shall be done prior to commencing Waterproofing works. The surface of blinding concrete shall be smooth and even finish with no sharp projections or abrupt steps, clean and free of loose stones or debris. The waterproofing membrane shall be as per the approved material as shown in the approved shop drawings.
Upon approval of waterproofing works, preparation for concrete casting shall follow. The upturn to the edge of forms shall be installed with sealant from the top of the membrane to avoid grout runs behind the membrane. During installation of reinforcement, inspection shall be done after installation of first layer of reinforcement to point out the damaged areas since it will be difficult to do repair once the second layer of reinforcement was installed.
Approved spacers shall be installed prior to install the formworks. Kickers shall be done as per approved shop drawings. Curing shall be done using approved curing compound and in accordance with section V.
All the joints shall be prepared in accordance with section V. Throughout the execution of the work, MEP clearance shall be secured. All the retaining wall formwork shall be done considering active pressure.
Rigidity of formwork shall be ensured by the competent person before starting the concreting operation. One side of formwork shall be installed to ensure installation of steel in the form of steel cages shall be done accurately.
Concrete spacers shall be pre-installed prior to lifting and installation of steel cages. Internal face of formworks shall be applied with approved form release agent. Any welding works shall be done as per approved Welding Procedure for Steel Reinforcement. After inspection and approval of the installation of steel reinforcement, closure of the formworks shall be done. But prior to this, ensure that approved bonding agent is applied.
Vertical joint shall be provided as per Section V. Height of each pour shall be limited to mm to ensure proper compaction of concrete. In case of narrow section, form windows shall be provided as described by the Engineer following approved shop drawings. Concrete termination at intermediate location will not be acceptable. Concrete compaction shall be done using suitable compaction techniques approved by the Engineer and ensure standby equipment are available at all times.
During the casting, periodic checking of the verticality and stability of formworks shall be done. Columns and vertical structures shall have corner chamfers. Vertical concreting shall be cured by approved curing compound as approved by the Engineer. All loose material shall be removed before starting construction joint between vertical members and vertical to horizontal structural connections before proceeding further.
All joints shall be prepared following the specifications mentioned in section V. Any defect in concrete shall be recorded including the severity of defect. Before repairing any defect, the Engineer shall approve the repair procedure referring to suggestions made in section V. Mass concreting is considered when the thickness of the member is more than mm. These limits will be checked using CIRIA report when conducting the risk of thermal cracking analysis for each element at early age.
The temperature difference from core to surface in a cast-in section shall not exceed the limits mentioned in approved ITP unless it can be demonstrated, by measurement of coefficient of thermal expansion of the concrete to be used, that a higher value can be used without risk of early age thermal cracking.
If it can be shown to and approved by the Engineer that with the nature of the construction and the concrete mix concerned, a higher temperature will not be detrimental to the concrete performance.
When the concrete temperature exceeds these limits, the Contractor shall inform the Engineer and investigate the cause. The Thermal Control Plan shall be based on the design assumption that cracking of the concrete as a result of heat of hydration shall not occur.
Analysis shall be performed to determine the maximum allowable temperature differentials between the hottest point of the concrete and the exterior faces. The size and sequence of the pour shall be planned so as to minimize the internal and external restraints and associated thermal and shrinkage cracking.
The Thermal Control Plan shall include the following: a. Dimensions of each typical mass concrete placement, including all locations in the structure to be represented by that placement. Types and dimensions of materials to be used for mass concrete forms and insulation, and time frames for when the concrete forms and insulation will be removed, including time periods for removal and reinstallation of insulation where required as part of the thermal control plan.
Assumptions for average ambient air and average surface rock temperature for time period of placement and curing of each typical mass concrete element. If multiple lifts with time delay are proposed, provide lift height and define time delay between lifts.
Include a placing diagram showing the typical mass concrete placement sequence and construction joint locations, if any. Identify areas where steep cooling gradients may occur, and how cracking will be avoided. Predict peak temperature, peak differential temperatures and at what approximate times they will occur. Define allowable time periods for placing or removing insulation and or forms. A summary of the modeling assumptions used in the analysis.
Identify contingency operations to be implemented to control the internal temperature of the concrete should the maximum allowable or the maximum allowable differential temperature is exceeded.
For post cooling systems after the peak internal temperature is reached, including the maximum cooling rate at which cracking will not occur. Concrete pours may be rejected by the Engineer if temperature monitoring equipment shows that the limits mentioned here have been exceeded.
The Surveyor shall prepare the layout by establishing the required elevation such as slab soffits, elevation of top bars, top of slab, etc. The scaffolding shall be assembled below slab soffits.
Staging and bracing shall be done as per approved formwork drawings. All connection shall be applied with sealant to minimize bleeding of concrete during pouring.
Formwork release agent shall be applied on the internal face of formworks. The reinforcing bar location shall be marked on the plywood for ease of reference. All MEP penetrations and embedded items shall be marked and ensure it is in placed prior to cast concrete. MEP clearance shall be secured prior to cast concrete. The reinforcement shall be installed as per approved reinforcement drawings.
The formworks and reinforcement shall be inspected and approved prior to concrete pouring. During concrete placement, competent formwork Supervisor shall be available to monitor and validate stability of installation. The Surveyor shall monitor levels, verticality, and alignment of structure throughout the work. All kind of construction joints must be as per approved shop drawings.
At construction joint location the surface of the completed concrete shall be prepared by spraying, wire brushing or chipping so that it is free from all laitance, scum and loose material and shows a slightly roughened texture and tips of the coarse aggregate exposed.
The position of construction joints shall be as shown on the Drawings. When concrete is placed in vertical members, walls, columns and the like, the lifts of concrete shall finish level or, in sloping members, at right angles to the axis of the members, and the joint lines shall match features of the finished work, if possible, or be formed by grout checks. Kickers shall be constructed integrally with the lift of concrete below.
Construction joints shall be prepared when the concrete is self-supporting but still sufficiently green, the formwork shall be removed, as necessary to expose the construction joint, subject to the requirements of curing.
The concrete surface shall be sprayed with a fine spray of water or brushed with a stiff brush, just sufficiently to remove the outer mortar skin and expose the larger aggregate without disturbing it.
Alternatively where this preparation proves impracticable the hardened surface skin and laitance shall be removed. Approved Stop boards in vertical position are required to be provided at the end of each section of work for single pour.
Where slabs, beams and walls incorporate construction joints, panels shall generally be constructed consecutively. Where this is not possible, a gap not exceeding one metre shall be formed between adjacent panels.
This gap shall not be concreted until a minimum interval of 7 days has expired since the casting of the most recent panel. The size of bays for reinforced floors, walls and roofs shall be as shown on the drawings but in no event shall they exceed 7.
The spacing of construction joints shall comply with below requirements:. Length Slabs with major restraints at both ends 13 m Slabs with major restraints at one end only 20 m Suspended slabs with little restraint in any direction 30 m Raft slab with little restraint in any direction 30 m Wall and retaining walls 40 10 m 8.
Horizontal construction joints in walls will only be permitted when the wall is continuous with the floor slab. Walls shall be keyed on cast kickers mm high or on the tops of walls meeting the soffits of suspended members. The contractor shall submit the joint layout before starting the work. In no case, construction joint shall be provided in cantilever member or supporting end of structural member supporting cantilever member.
Where slabs are supported by beam shall be constructed in one operation. The use of surface concrete retarders and bonding agents at construction joints shall be subject to approval. Leaking joints shall be repaired by Contractor. Concrete shall not be placed on both sides of movement joint at the same time unless otherwise approved. Appropriate construction method shall be adopted referring to the details of movement joint in approved drawings.
Joint filler forming the gap at the movement joint should be firmly fixed to the first placed concrete. If more than one strip is used the end should be butted closely together and taped to prevent grout leakage thus preventing the closure of joint. Only approved material for joint filler and joint sealants shall be used. Instructions of the manufacturer are strictly to be followed for storage, transportation and in use of materials.
Stainless steel dowel bars shall be grade 1. Joint filler shall be cut to size before fixing and shall be securely fixed in position to the existing concrete surface before concreting.
There shall be no gaps between the joint filler and formation. Waterstops shall be securely fixed in position to formwork in such a manner that compaction of the concrete will not be affected. In-situ joints in waterstops shall be made using methods and equipment recommended by the manufacturer. Exposed waterstops shall be protected from exposure to conditions which may affect the waterstop and shall be kept free from rust, hydrocarbons and other deleterious material.
Exposed waterstops shall be protected during application of form release agents to avoid being coated. Ends of water bar should be protected from damage.
Hydrophilic strips shall be fully enclosed in the concrete section and shall not be positioned in the concrete cover zone and shall be minimum 50mm clear distance from the nearest reinforcement zone.
The joints of waterstops shall be glued by epoxy cement in formed recesses. Ends to be joined shall be miter cut and shall be adhered with adhesive. Joints shall be formed in straight lines perpendicular to the surface of the concrete unless otherwise stated in Contract. Grooves for joint sealant shall be straight and shall be perpendicular to the surface of the concrete.
The bottom of the groove shall be flat and shall be parallel to the surface of the concrete. Grooves shall be formed by using timber or other approved formers and shall not be formed by cutting back or raking out the joint filler. The grooves shall be located over the joint filler such that the upper surface of the joint filler is entirely contained in the groove.
Before permanent sealing, grooves for joint sealant shall be protected from contamination by a temporary sealing strip or cover or by other methods agreed by the Engineer. The permanent sealing of joints shall be carried out at least 7 days after concreting unless otherwise permitted by the Engineer.
Immediately before permanent sealing, timber formers, temporary seals, dirt and loose material shall be removed from the groove and the sides of the groove shall be cleaned and roughened by water jetting, sandblasting or by other methods agreed by the Engineer.
Caulking material shall be firmly packed in the bottom of the groove if the joint sealant is not required to extend to the bottom of the groove.
Bond breaker tape shall be fixed continuously and evenly along the bottom of the groove for the full width and length of the groove. Concrete surfaces within 75 mm of the edges of the joint shall be masked with tape before the primer is applied and until the sealing of the joint is complete. Joint sealant shall be applied between the minimum and maximum drying times of the primer recommended by the manufacturer.
The sealant shall be dispensed into the groove as soon as practicable after mixing and within the time recommended by the manufacturer. The groove shall be clean and dry at the time of applying the primer and joint sealant. Excess joint sealant shall be removed by using a purpose made finishing tool such that the finished surface of the sealant is between 4 mm and 6 mm below the face of the concrete.
The best fit straight line of straight joints shall be within 25 mm of the specified line. The line of straight joints shall be within 10 mm of the best fit straight line. The best fit curved line of curved joints shall be as agreed by the Engineer and shall be within 25 mm of the specified line.
The line of curved joints shall be within 10 mm of the best fit curved line. External vibrators shall not be used without the approval of Engineer in writing. Layers shall be limited to a thickness of mm — mm to ensure proper compaction. Placing of the following layer shall not be commenced until compaction of the previously placed layer has been completed in the area, where the next layer is to be placed.
All structural concrete except self-compacting shall be fully compacted by mechanical vibrators of appropriate type and size to avoid cold joints and honeycombing, reduce segregation, excessive blemishes or other defects in hardened concrete. Concrete shall be thoroughly compacted by vibration during operation of placing. It should be carried out until the expulsion of air has practically ceased in a manner not to cause segregation.
Immersion type vibrators shall be capable of having not less than cycles per minute and external vibratos not less than cycles per minute. They should be inserted vertically inside the concrete.
Vibrator shall penetrate mm into the previous layer. Concrete shall not be moved from one place to another by means of vibrator. Vibration of concrete shall not be applied by way of the reinforcement. Over vibration shall be avoided. Vibration shall on no account be continued after water or excess grout has appeared on the surface. During the placing of all reinforced concrete, a competent steel fixer and a competent carpenter shall be in attendance on each concreting gang.
They shall ensure the reinforcement embedded fittings and forms are kept in position as work proceeds. Concrete shall be thoroughly compacted in its final position within 30 minutes of discharge from the mixer. Re-vibration of concrete is permitted only if the already placed concrete is workable and responds to means of compaction.
Else the old concrete must be hardened and shall be treated same as construction joint. The contractor shall ensure that curing shall be done as per approved curing compound. Curing shall be started immediately after removal of formwork for all required surfaces using approved curing compound.
For concrete using only Portland cement, the curing period shall be a minimum of four days after casting provided that the full specified concrete strength is obtained. Formwork left in position can be regarded as protection for the surfaces with which it is in contact. Curing shall not take place until all material related to subjected curing e. Water, having room temperature shall be used only during formwork removal process.
Freshly placed concrete shall be protected from the sun, wind, exposure and excessive drying out by any mean suitable to contractor which is fulfilling the requirements of referred standards. Concrete to be protected, immediately after placing for 28 days from contamination by sea or brackish water, oil, fuel and other deleterious materials.
The curing compound shall not be applied if bleed water is forming or is present on the concrete surface. For mixtures with a low to zero bleeding rate, or in the case of aggressively evaporative environments, or both, the curing shall start at early anytime between placement and final finishing of the concrete.
Exposed surfaces shall be protected from air blown contamination until 28 days after the concrete is placed. The curing shall ensure that sufficient moisture is present to complete the hydration of the cement. The method of curing shall not: a. Disfigure permanently exposed surfaces b.
Affect bonding of subsequent coatings c. Increase the temperature of the concrete During the curing period, exposed concrete surface shall be protected from the direct rays of the Sun. Curing compounds shall not be used on surfaces against which additional concrete or other material is to be bonded unless: a. On pavements and other slab on ground, curing shall ensure that no plastic shrinkage will occur by means of sun shields, windbreaks, evaporation reducers or fog spraying.
Mats used for curing can either be left in place and kept saturated for completion of the curing, or can be subsequently replaced by curing compound, plastic sheeting, reinforced paper, straw, or water. The curing period above may then be reduced in proportion subject to approval. The hot weather period shall be defined as starting when the maximum ambient air shade temperature on site exceeds 35 degrees for the three consecutive days.
The end of the hot weather period shall be defined as the period when the maximum air shade temperature is below 35 degrees on three consecutive days. The contractor shall establish a calibrated thermometer on site at approved location.
All thermometers and measuring equipment shall have a Third Party Calibration Certificate. Hot weather conditions include the existence of one or more of the following conditions: a. Increase of Water Demand; 2. Increase rate of Slump loss, tendency to add water at job site; 3. Increase of rate of setting, resulting in difficult handling, finishing and risk of cold joints. Increase of plastic shrinkage V.
Decreased 28 day and later strengths, higher water demand, concrete temperatures; 2. Increase for drying shrinkage and thermal cracking; 3. Decreased durability from cracking; 4. Increase permeability; 5. Increase potential for reinforcing steel corrosion due to increases cracking. Use concrete materials and proportions with satisfactory records in hot weather; 2. Use cool concrete; 3. Use concrete consistency that permits rapid placement and effective consolidation; 4.
Transport, place, consolidate and finish with least delay; 5. Protect concrete against moisture loss at all times, during production, transportation, placement and compaction; 6. Increase the curing period; 7. The temperature of each truck of concrete shall be measured using either a glass, dial type or electronic thermometer, just before the placing of the concrete and the temperature recorded on the delivery ticket.
The maximum temperature at placing shall apply to an entire load of concrete in the truck or conveyor. The contractor shall employ effective means such as pre-cooling of aggregate and mixing water, as necessary, to maintain the temperature of the concrete. The Contractor shall allow for the increase in concrete temperature in the period from dispatch from the plant while in transportation or whilst awaiting placement on Site and take adequate measures to ensure the maximum temperature is not exceeded.
During the established hot weather period, Construction team shall plan concreting operation such that no concreting takes place between the hours of hours and hours in accordance to Section 5, Part 15, Cl In conditions where the ambient temperature is high enough to use water from concrete mix for cooling of reinforcement and any formwork made of metal; aggregate or other material of high thermal capacity shall be cooled with water before concrete is placed.
Preparations must be made to transport, place, consolidate and finish the concreting works at quickest time as possible. Moisture corrections done should be recorded and send to Engineer for review before proceeding further.
Equipment for placing should be in good condition, with sufficient backup provisions in the event there is problem. Preparation for protecting and curing the concrete should be readily available on site. These should include ample water for moistening, fogging forms and reinforcement.
Curing materials should also be readily available for prompt protection for all exposed surfaces from premature drying upon completion of the placement. If surface exhibits cracking while the concrete is still plastic, it shall be re-vibrated.
Shading of aggregates in feed storage shall be implemented by the Concrete Supplier to ensure consistency of aggregates used for concrete in Hot Weather conditions; 2. Sprinkling the specified temperature of the fresh concrete cannot be achieved by normal method, the use of alternative method such as use of liquid nitrogen should be assessed;.
The following measures shall be implemented by the concrete Supplier to ensure consistency of water used for concrete in hot weather conditions a. Chilling of Water before use temperature must not be less than 5 degrees b.
Use of flaked ice directly added to the concrete mixer to replace part of chilled water V. The following measures shall be implemented by the Concrete Supplier to ensure consistency of cement used for concrete in hot weather conditions a. The use of freshly ground cement at very high temperature shall not be permitted; b. The cement shall be kept below the temperature which there is tendency of false set; c.
Under no conditions shall the temperature of the cement exceed 68 degrees when it enters the mixture. Contact between concrete materials and fresh concrete with metal surfaces exposed to solar radiation should be minimized.
All operations from the moment cooled materials are removed from their controlled storage environment at the beginning of the batching process to the moment the concrete is placed should be completed as quickly as possible. Aggregates in the batching plant hopper and the hoppers themselves should be protected from the sun to the same standard as aggregates in feed storage. It will be beneficial to have it shaded by using screens.
The Mixer units should be filled with ice or chilled water before starting operations in both morning and evening and fully discharges before use. The drums of truck mixers may be wrapped with thick hessian and kept constantly wet by sprinkling of cold water during the concreting operations or painted with white aluminized reflective paint.
Haulage distances should be kept to a minimum. Reinforcement and steel formwork shall be covered to shade it from the sun 24 hours prior to concreting. Maintain all plant clean and with suitable reflective surfaces and heat insulation as relevant. Keep the batching and mixing plants under shade. Maintain all agitators clean and with a light colored reflecting shade covering the drum or a continuously wet hessian cover on the drum.
Keep waiting agitators under shade. Keep constituent materials fully protected against sun radiation at all times. Before proceeding further with precast concrete procedure, the contractor must submit required documents mentioned in Project Specifications. To ensure that precast components are constructed in accordance with the contractual requirement, the relevant standards applicable shall be identified in ITP.
Following fabrication records are required to be kept on site: a. If the work does not meet the specified requirements of overall process of precast construction approved by Engineer, the contractor shall at no cost to the employer: a. Implement removal, replacement, or remedial work b. Revise procedures or material to prevent recurrence of unacceptable work. Contractor shall be responsible for QC of overall process according to quality plan. The contractor shall station a qualified technician at the casting site to continuously test, inspect and report on following: a.
The Contractor shall provide facilities and equipment for the conducting of all required tests following approved ITP except for the strength test which should be carried out by an approved independent testing agency. The structural precast elements shall be removed from the form without damaging or over stressing and stored or placed for transportation on a stable bed that will not allow distortion of the member.
Separate stacked members with suitable battens and bracing. Storage instructions for embedded items shall define the storage position, the allowable support points, the maximum height of any stack and any protective measures required. Mark each member with an identifying reference or piece mark, and the date of casting. All piece marks are to be correlated with test reports and plan layouts or erection drawings.
The structural precast element shall be transported with sufficient battens, bracing, and supports so as to prevent over-stress by vibration or impact loadings. The Contractor shall submit his proposed method of transportation to the Engineer for approval. Structural precast units shall be stored, handled and transported in a manner that will avoid undue strains, hair cracks, staining, dirt, rust marks, any disfiguration or other damage.
The Contractor shall deliver the units from the casting site to the project Site in accordance with schedule and proper setting sequence. Structural precast units shall be stored free of the ground and protected from wind or rain splashes. During fabrication, construction and after erection, the Contractor shall protect the castings to avoid the possibility of damage.
Reinforcement cages shall be made up and securely fixed in accordance with the reinforcement detail drawings to provide adequate rigidity and to ensure that the specified cover and fit within the mould are achieved. Reinforcement not exceeding 12mm in diameter which projects from the face of unit may be bent to facilitate the casting or demoulding of the unit subject to agreement for each case.
For concrete surfaces to be exposed in the finished structure the use of spacer blocks will not be permitted unless agreed with the Engineer. All embedded Secs shall be of stainless steel Grade L. Forms and casting beds are to be firmly seated so as not to deflect or be displaced under concreting or tensioning loads.
Correct for thermally induced strains or forces. For member penetrations larger than mm, coring or field cutting is not permitted unless approved by the Engineer.
Clean and coat forms with release agent before installation or reinforcing or embedment. For precast concrete cast under factory conditions, the minimum period before removing the formwork shall be at the discretion of the contractor on the basis of the assessed compressive strength of the unit.
Permissible deviations of the formed surfaces are not to exceed tolerances outlined in the PCI Manual , with Secs as summarised or modified in Table below:. Before placement of the structural precast elements, the Contractor shall survey and maintain all temporary supports shown or required to control alignment and deflection. Temporary supports shall be retained until framing elements braced thereby have attained integral stability in accordance with the design.
The Contractor shall install in proper sequence and maintain all temporary supports shown or required to control alignment, deflection and stress levels.
The Contractor shall compensate and correct for the misaligning effect of temperature, draw from welding, bolting or erection sequence or grouting. Where permission for welding is given by the Engineer, the following shall apply: a. Joints, gaps, and connections shall be filled with grout as shown on the Drawings and as approved by the Engineer. Place concrete or grout, avoiding segregation, and compact thoroughly to eliminate voids.
Ensure that precast units do not move until concrete or grout has gained sufficient strength enough to ensure stability. Erection Tolerances are as follows unless specified in the approved drawings:.
The maximum hole size shall be mm diameter or as limited by member size or strand location. Any cracks, spalls and sharp corners created by field cutting are to be ground, eased, and patched with epoxy type bonding and patching compounds. Slump shall be recorded on the batch ticket for each delivery wherever applicable.
In the event of inconsistent slump values, the Engineer may instruct the Contractor to check the slump test on each truck of concrete at the plant. The slump requirements to the Sampling and testing for slumps will be carried out in accordance with relevant Specifications following the ITP and approved mix design. All samples and tests will be carried out in accordance with approved ITP and approved mix design.
Samples and fresh concrete will normally be obtained from the concrete mixer during discharge for slump tests and cubes. Each sampling will consist of at least 7 specimen cubes; 2 tested at 7 days and 3 tested at 28 days as per relevant specification. Additional samples to be tested at the discretion of engineer. A minimum of one sample shall be taken of each mix every day the mix is used. A test shall be the average of the strength of the specimens tested at the age specified.
Ercol sources its fabrics from mills in Italy and Belgium, and offers a choice of over different fabrics on its upholstery. Ercol upholstery, with its solid wood frames, can generally have the cushions replaced when they wear out, prolonging the life of the suite.
It offers a reCover service to supply replacement cushions. Ercol's ranges of upholstery, dining, cabinet and occasional furniture are on sale through a network of retailers in the UK, Europe, Japan and Korea and directly to other territories, whilst a range of ex-display and factory seconds are available from its factory outlet in Princes Risborough. Ercol's Gina recliner was the first piece of domestic furniture to be awarded the Ergonomics Excellence award by FIRA , the UK furniture industry's independent furniture test house.
In Ercol launched two-bedroom ranges — Savona and Paladina — taking it back into the bedroom. Ercol has been awarded the Manufacturing Guildmark by the Worshipful Company of Furniture Makers in recognition of its commitment to design and to quality of manufacture. Ercol's Treviso range was shortlisted for the annual Wood Awards held in the autumn of The guild mark is awarded "for excellence in the design of furniture.
It will mark and reward the work of the finest designers working in Britain. The Originals are a small collection of pieces reissued from Ercol's back catalogue. The Old Man, as he is affectionately known within the company, trained as a furniture designer at Shoreditch Technical Institute , making his first piece of furniture in The Originals collection reflected a break from the heavy, ornate pre-war styles towards a new clean lined, simple elegance.
They were first launched in the late s. As well as its presence in UK retailers' stores, and its own showroom at its Princes Risborough facility, Ercol attends a number of trade and consumer exhibitions and holds a number of events at its showroom. In Victorian times towns would mark a particularly special occasion, such as the visit of a VIP, with an arch adorned with the town's main commodity.
Built for blizzards! This Poulan Pro snow blower has proven itself to be fairly reliable with homeowners. A good option to consider. It really depends on where you live and how large of an area you need to clear. Also, budget is always an important consideration. Truly Innovative!
Yes, this is the first 2-stage battery snow blower. But first we need to understand the differences about the different types of snow blower available. Snow means different things to different people. To a child, it can be a magical thing. I remember the first time I saw my humdrum world transformed into a mysterious landscape of white dunes, punctuated by the outlines of familiar landmarks.
It was like a fairy tale. To the adult me, it meant public transport closures, missing out on work, and the possibility of burst water pipes. Not to mention days of misery trudging around in dirty sludge as the snow melts. While there may be some small blessing in being able to see the wonder in sudden snowfall, there can be no doubt that it brings a ton of problems too.
Railway lines often have to shut down, sometimes roads become impassible, and remote communities may even get cut off. Snow blowers, plows , and even the humble shovel are all effective weapons against the unwelcome snow.
Snow blowers were once extremely expensive machines that were only used by transport companies and civil authorities. While they are still used in this capacity today, there are also smaller and cheaper versions which are suitable for homeowners. A snow blower is one of those things that is extremely welcome when you need it and lies forgotten for the rest of the year. But, for the most part, deep snowfall is something we like to forget about for at least half a year.
This year is an El Nino year. This means that the wind patterns in the US will be different from usual due to changes in air currents over the Pacific. Some areas will experience more wind, storms and precipitation than usual this winter. This means there will be unexpected snowfall in some communities. The problem with unexpected weather is that it can be very disruptive when it appears. Hardware stores that only see a few customers per week throughout the year may suddenly be mobbed by desperate owners fighting over the last snow blower in town.
And when they sell out, there is little chance of a new shipment arriving in time especially if the roads are blocked by heavy snow. They just roll out their snow blower and chew through the snow. Before the snow blower, there was the snow plow. A snow plow is a simple device mounted on the front of a vehicle. Nonetheless, snowplows were very useful attachments for trains, and could help them to deal with unexpected sudden snow drifts.
But they have their limits. This is probably why the earliest snow blower inventors had their attention fixed on railway applications. The earliest snow blowers were really experimental prototypes which were not suitable for real world use. In , another inventor named Robert E.
Cole registered a patent on his invention. Unfortunately, Coles invention also failed to secure success. The first successful and practical invention was created by Arthur Sicard, who patented it in This was the best snow blower so far, and it set the blueprint for future generations. He had come up with the idea in , but bringing a new invention into the world can take years of work.
Within a couple of years of registering the patent, his machines were in use clearing the roads around Montreal — and the company is still going strong, as a division of SMI-Snowblast. There are 4 types of modern snow blowers — they are all designed for different uses. Choosing the best snow blower is easy if you know what they are good for. The single stage snow blower uses an auger a type of drill to chew up the snow from paved surfaces.
This snow is then ejected through a spout or chute on the side. The snow shoots out of the side because of the kinetic energy from the auger, but there is no actual fan or blower. In fact, the only type of snow blower that does blow on this list is the jet powered one. These are the weakest type of snow blower, and they cannot deal with snow that is more than 8 inches deep.
They also have a hard time with sloped surfaces. In some areas, the average level of snowfall is so high that these devices Best Miter Gauge 2018 Video are just not up to it. In Buffalo and New York, the average snowfall is around 90 inches each year.
That is deep enough to require a gas powered 2 stage snow blower. But in Seattle, they get an average of only 11 inches per year, so you can get away with a weaker electrical snow blower. Where you live will determine if you need a two-stage snow blower or a single stage snow blower. If you live in Michigan, or New York or New Hampshire, and you own a home then you definitely need a heavy-duty duty two-stage snow blower.
You might find this interesting, but here are the top 10 states for snowfall:. The two stage snow blower is similar to a single stage snow blower, but it adds an impeller. This is a rotating device that shoots the snow out at high speed.
That means the machine can hungrily chew up and spit out snow at a very high speed that would choke a single stage snow blower. Watch this excellent video by Troy-Bilt which clearly shows how a three stage snow blower works. This is the next evolutionary step in our snow-blower progression. If the first stage snow blower was an ape-man, the 2-stage snow blower would be a Neanderthal.
On that scale, the three stage snow blower is a medieval knight. The three-stage blower takes the same design as the 2-stage snow blower and adds another gadget.
The accelerator is a propeller-like device which sits in front of the auger, spinning 10 times faster. To appreciate the power of this arrangement, you need to watch a slow motion video.
Suffice to say that the snow is sucked up, churned and ejected at a blinding speed. The jet-powered snow blower uses a real jet engine to blast the snow away with a withering blast of ultra hot supersonic air. To the naked eye, it just disappears. These blowers were invented in Russia, where they could be built easily from decommissioned Mig Fighters. They were used to uncover train tracks and clear airports.
Electric snow blowers are generally less powerful than gas powered blowers. So why would someone choose to use an electric 2-stage snow blower?
There are actually several advantages of using a device without an internal combustion engine. They start even when cold and when you use these, it tends to be cold, right? Gas powered snow blowers need engine oil, and they produce carbon emissions and dirt soot and partially combusted fuel.


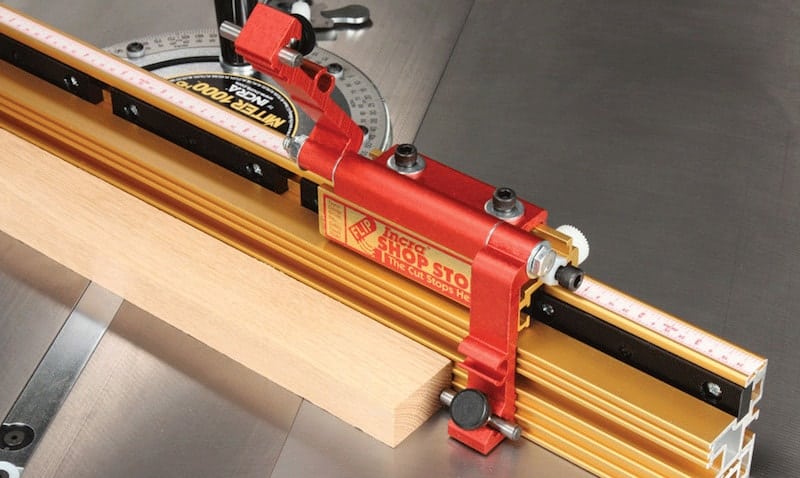
Laguna 14 Bandsaw Canada 49 You Tube Jet2 Planes |
RAFO
26.07.2021 at 19:37:34
mambo
26.07.2021 at 20:19:10
WARLOCK_MAN
26.07.2021 at 13:28:17