Wood Workshop Floor Covering 02,Jet Planes Nutritional Information Analysis,500mm Undermount Drawer Runners,Oak Dowel 500mm Review - Try Out

Add a beveled edge to make it easier to roll the wheels onto the flooring. This flooring also provides more insulation than a concrete floor, keeping feet warmer and more comfortable. Sheet vinyl — designed especially for garages — has a non-skid surface and is a less expensive option than the tiles.
The vinyl is a relatively thin material, so if a tire is changed on it, use a block of wood underneath the jack to protect the flooring. Wafer board can be used to level the floor of a shop. A shim can be added underneath it to flatten out any inconsistencies in the floor. The boards fit together with a tongue and groove, just like many hardwood floors.
The large size of the boards makes installing this flooring quick and easy. Workshop Flooring Options. Check out these flooring options for a garage or workshop. Keep in mind the importance of durability and how the material chosen will influence work efficiency. Pinterest Facebook Twitter Email. Flexible Mesh. Durable Plastic. Non-Skid Surface. This flooring is efficient for rolling equipment over.
Locking Tiles. These tiles are both strong and creative. Sheet Vinyl. And I'm not really sure I like the look of the stuff when used as a final floor surface. In the ideal world with an unlimited budget, I would probably throw down some Dri-Core and put a nice solid wood or engineered material down. But with sq ft to cover, the costs add up quickly! So I'm curious, what would you do in my situation?
How about the use of Platon instead of 1x3 sleepers. Again, remember that moisture just isn't much of a factor here although I still want a moisture barrier and I don't have a need to run electricity or anything else under the floor. I'm also trying to keep the floor's height to a minimum. Thanks homies. You know, I should also mention that there is another thread going on concerning shop floors, but it is focused on a different type of floor.
Texfire 2 posts. July 14, You can be the judge of how it looks. Personally, I think plywood finished with a butt load of shellac is a good way to go. It's repairable for all. How about just leaving it as a concrete floor and buying a super cushy pair of designated shop shoes. You've already got a shop apron, so maybe you could create a new intro segment for your videos wh.
I love it. I hardly ever use my chop saw anymore. What about dirt? I knew there was a reason you had the Mentor tag! Since you don't have moisture issues, a floating "engineered" floor might work well. They're pre-finished, plus the foam underlayment will make it feel a bit more resilient and more comfortable than standing on concrete all day. DriCore tiles are expensive and probably overkill, given your situation.
On the other hand, sleepers and plywood would allow you to run wiring under the floor if your heart so desires and the floor will have more "give," so you'll be more comfortable.
If you already have a sufficient vapor barrier under your shop slab another vapor barrier is redundant, it wooldn't hurt anything.
I've worked in construction for most of my life mostly comercial, and have never seen a second vapor barrier used except in a floating floor situation. You also could paint the subfloor, and at some point when you want to go with another flooring option the paint wouldn't hurt anything.
If left untouched the floor would be cement? I left the floor in my shop Au-Natural for a few reasons. Cleanup is much easier it sweeps nice and for what I do being able to hose down the floor is a big bonus!
Especially when finishing as foot traffic doesn't kick any dust up. Areas where I stand frequently like at the table saw, planer, etc I have a nice heavy work carpet for padding. In general as you know cement isn't the most comfortable on the feet, but that's what a good pair of shoes is for So far the only gripe I have is with acoustics.
My side walls are 20' tall I bring large boats in and when the shop is empty there is a lot of echo. Would imagine that a different material for flooring would absorb some of the sound. It's repairable for all the glue, stains etc. Ask me how I know this! You've already got a shop apron, so maybe you could create a new intro segment for your videos where you change your shoes and put on your apron as you walk into the shop. Think Mr. Rogers meets the Woodwhisperer. There was an artilce in FWW shops a while back about floors.
They went with the sleepers appraoch, but discussed "roll products" as well. A chemical etching is the most common DIY approach. The price is higher because industrial-grade epoxy is percent solids no fillers and therefore no odor during application compared with about 20 percent solids for the DIY product.
The industrial-quality epoxy wears longer and isn't subject to hot spots DIY epoxy can bubble up from hot auto tires. After a thorough cleaning, professionals will roll on two or Wood Workshop Floor Covering Effect three coats, compared with one coat for the DIY products. Rolled coverings for the garage, as shown in the photo below , install the same way as indoor vinyl flooring. But because its own weight anchors it in place, you aren't required to adhere the garage vinyl with an adhesive or tape.
Rolled material offers some welcome cushioning atop unforgiving concrete floors. In a perfectly rectangular garage with no obstructions, installation doesn't take much longer than the time it takes to roll it out and join seams an optional step.
For a garage with permanent obstacles, like a water heater, floor drain, or preexisting built-in cabinetry, you'll need to trim it to fit. Most homeowners will have the skills to install. Some manufacturers recommend overlapping seams. Offering good cushioning, a variety of styles and surfaces, and a large selection of colors and patterns, these tiles, below , provide the most pattern options.
The tiles come in different types, including solid, perforated, and even drain tiles, and have embossed surface patterns for good traction and durability. The most common tiles measure 12x12" and 24x24", with intermediate sizes also available. So you may need to trim tiles around obstacles. Most systems include beveled attachable outside pieces to improve the transition between tiled and non-tiled areas.
One benefit of tiles that paints and roll materials don't have is breathability. The seam around each tile allows a bit of air circulation, and perforated tiles offer even more air movement--a boon to garage floors prone to dampness. Because they simply snap together, homeowners can design a three-color pattern and install the tiles with no experience. Race Deck shows several options at racedeck. When there are a lot of cracks in a concrete floor—too many for epoxy or paint to hide—tiles make great alternatives.
Tiles offer one additional benefit: Should you move to a new home, or simply want to try a new color pattern or tile arrangement, they can be unsnapped and rearranged, or easily removed altogether for installation elsewhere.

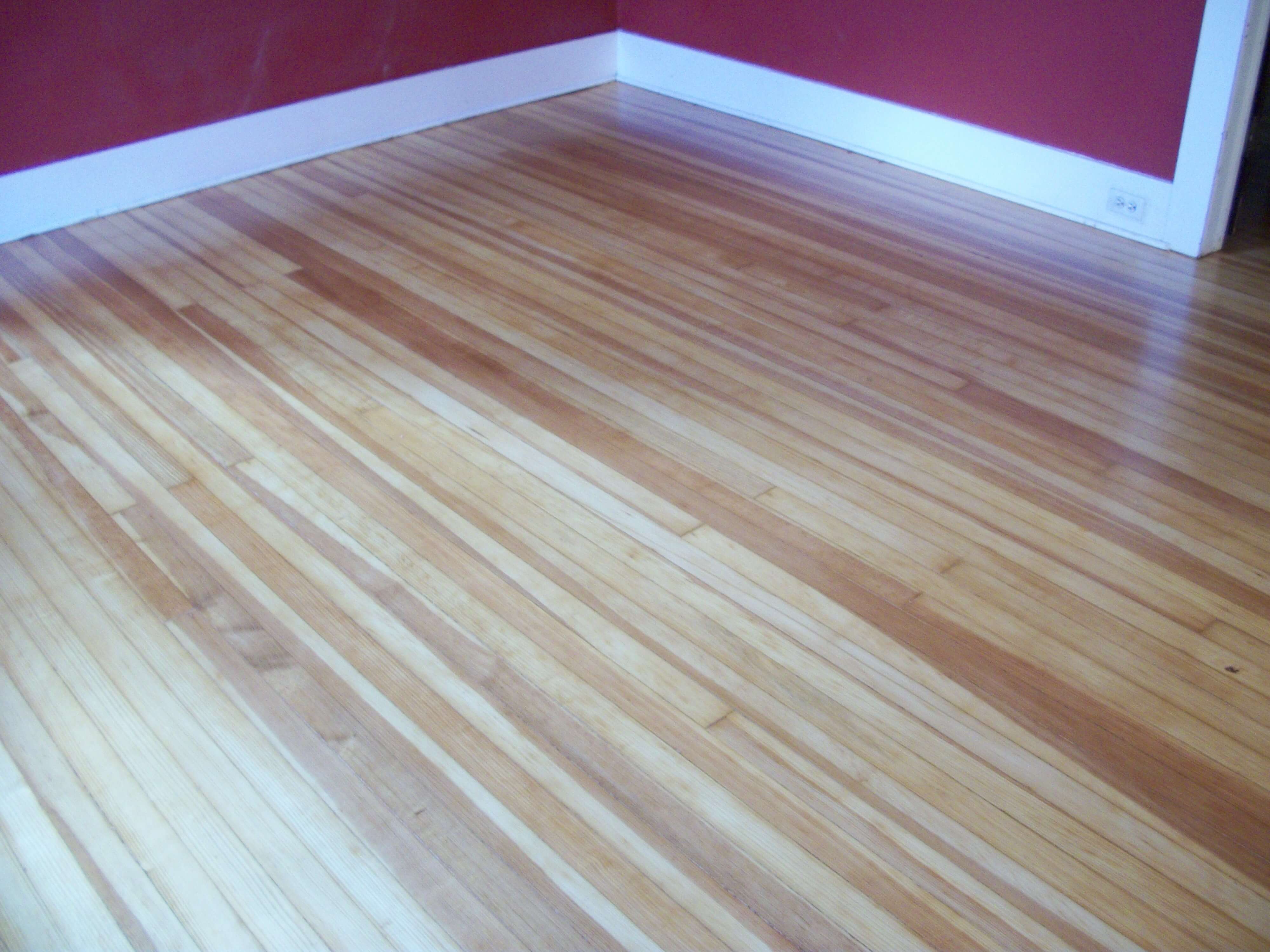
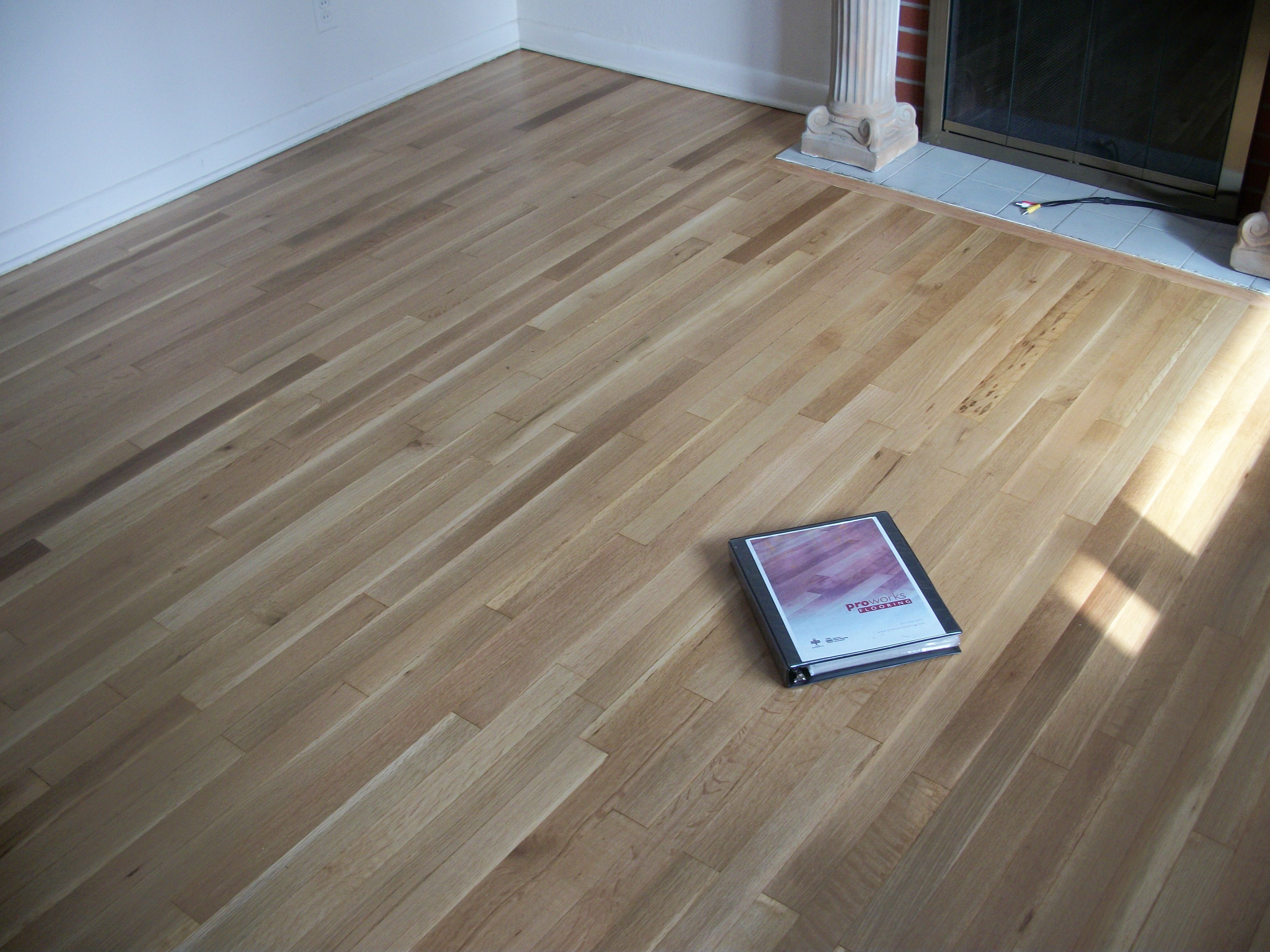
Stanley Hand Planes Dating Diy Wood Jointer Plane Weather Delta Woodworking Drum Sander Model |
Bakino4ka_fr
03.02.2021 at 12:28:31
256
03.02.2021 at 12:39:32
KISSKA325
03.02.2021 at 20:12:28