Jig Tool Harbor Freight 80,Oneida 15 Hp Cyclone Dust Collector Not,Miter Gauge Uses Questions - Good Point
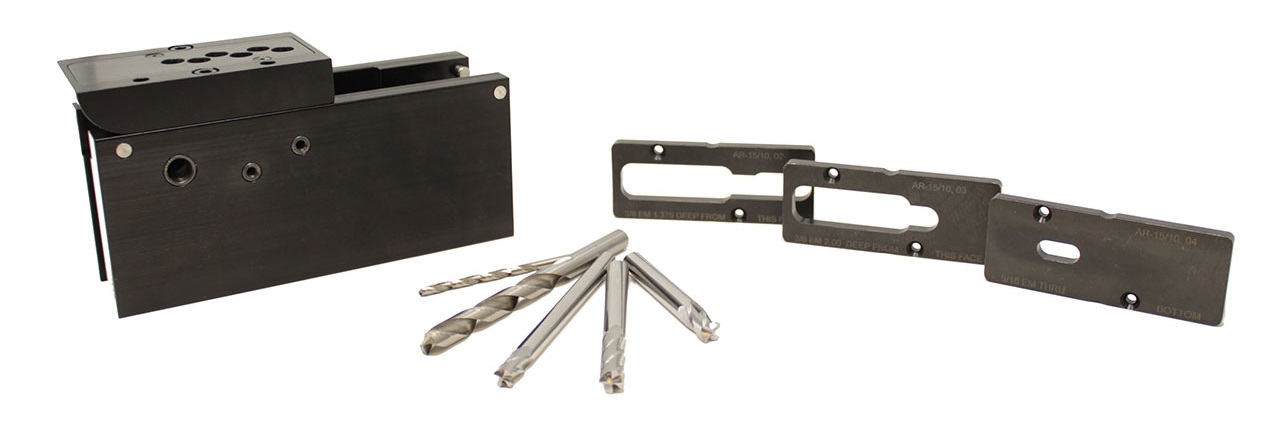
NOTE: As with all router jigs on the market the hash marks are a bit too aggressive in my opinion. There is less chance of your end mill biting and jumping with these reduced depth millings. It does add some time but the finished product will be worth it. Rotate the top template back down and reinstall the two rear support and four side plate screws. Connect the two holes by routing the material between them and then continue working outwards until you have milled the entire area at the first cutting depth.
Repeat the process until you have completely milled out the trigger slot. Use caution when milling because the top template of the Modulus Arms jig is fairly narrow and your router could want to tip over the edge if you aren't careful. I really wish it was a wider top plate. Now set the depth of cut on the end mill to the first hash mark on the "B" slot in the depth guide. Mill as before working your way up to the final cutting depth. Remove the two screws from the rear support, two screws from the front support and the four screws from the top of the side plates.
Turn the top template degrees so the trigger pocket portion of the template is now towards the rear with the recessed holes still facing up. Attach the drilling guide to the top template under the trigger pocket template. Reattach the two rear support, two front support and four side plate screws to the top template. You can now install the large rear screw between the two side plates and through the rear takedown holes of the lower receiver.
This will give added support throughout the remainder of the machining. I usually set my maximum depth to just slightly less than the maximum. This helps prevent dimpling on the bottom of the trigger pocket after final machining. Drill out the three large holes in the fire control group pocket template. As before, remove the two screws from the rear support, two screws from the front support and the four screws from the top of the side plates.
Pick up the top template and then remove the drilling guide with the four screws. Now set the depth of cut on the end mill to the first hash mark on the "C" slot in the depth guide. As you approach the final pass make sure you are starting your end mill over the trigger slot which has been completely milled through. This is much easier and safer and makes for a cleaner final cut. Now it's time to drill the holes for the trigger pin, hammer pin and safety selector. Because of the non-flat nature of the sides of the jig you will need to rig something up to keep the jig flat when drilling with the drill press.
Alternatively you can clamp the jig in a vise and use a hand drill to complete these holes. Do not try to go through both sides of the receiver at once. You can now disassemble the jig and remove the lower.
In theory the buffer insert in conjunction with the front support should center the jig. The side plates also have some mobility and can accomodate odd shaped lowers and avoid the problems with the magwell all together.
The problem I ran into with the buffer support was remedied with the latest iteration of the buffer support so that takes care of the problems I had with universality of the jig. Here is a summary of the other issues I have with this jig. First, the requirement to install the front pivot pin in order to machine the lower.
As discussed previously it is a pain and I don't always want to assemble the lower right away or might need to anodize or paint the lower after machining. There should be another solution that comes with the jig. Easy in, easy out. Plus the clevis pin can be used as an improvised tool to install the front pivot pin spring, detent and pin.
Value added! The cotterless hitch pin also works well and is easy to insert and remove. Second, the sheer number of screws required to assemble, change and reassemble is high. I also wish the screws were black oxide instead of stainless so they wouldn't want to slip off my magnetic tipped screwdriver as easily. Dealing with sixteen screws is bad enough but when they are small and don't want to stay put this is an extra aggravation.
With the Easy Jig there are four main bolts to assemble the jig and four smaller bolts to change the drilling and milling plates. With the Modulus Arms jig you not only must remove and install at least six screws every time you need to change from the drilling guide to the milling plate but you must also realign all of the plates with the top template.
Flipping the template around requires the removal, installation and alignment of eight screws. Third, the top plate is too narrow. The Easy Jig gives you a nice wide base to use with your router and you never feel like it wants to tip over.
With this jig I had to be very conscious of the edges and not allow the router to tip over the side as I moved the router about.
It seems like this Harbor Freight Truck Lumber Rack is a change that could be made to the jig without otherwise modifying the design. Fourth, the jig is tall for how narrow it is. Using it on the drill press was tedious because I had to make sure the jig was secure and wouldn't tip over. It was also too tall to be used solely with my 8" drill press table. Then after I had started these holes I could stop the drill press, place the bit into the partially drilled hole, swing the table back under the jig and finish drilling the hole with a more secure base under it.
This is a limitation of my drill press but it wasn't an issue with the Easy Jig and I know a lot of users only have a small drill press as I do. The only reason I can see that the jig is so tall is because the side plates are identical and therefore longer than they need to be. Modulus Arms has informed me this is done for two reasons. Technically four times as many as you need since you only drill through one plate at a time.
If you should wear one set out due to user error or very high usage you can just flip the jig plates over and you have a fresh set. Second, the taller plates allow you to clamp the jig in a vise more easily than if they were shorter. The long screws keep the plates from pushing towards each other when clamped in the vise.
Finally, someone really needs to overhaul that manual. It is not clear at all and jumps around too much. Ideally they should bring in an English major and have them proof the manual as they are also trying to follow the steps. Local college Woodturning Tools At Harbor Freight Zip students often work cheap and if they have an interest in firearms or machining all the better. That being said I don't know how narrow the intersection of English major college students and firearm manufacturing enthusiasts is on the Venn diagram.
I found the jig more tedious to use because of the number of screws, small top work surface and the "height vs my equipment" problems. But my first time using the jig, albeit as an experienced builder, did not pose any problems that affected the final product.
This jig Harbor Freight Lathe Tool Post is the only router based design that will handle some of the wilder lower designs out there. Specifically the New Frontier Armory lower comes to mind. This just won't fit in the Easy Jig even with the universal side plates. There's only so much universality you can build into a product that uses full side plates and this jig gets around that by only having partial length side plates. This pocket hole jig kit mounts securely to your workbench or can be used as a portable unit from job to job.
This pocket hole jig lets you drill pocket holes with maximum precision Due to popular demand this product is currently out of stock and will not be back in stock until Mar Compare to.
Product Overview This pocket hole jig kit creates pocket holes at variable center distances for a range of material thicknesses. Variable center distances for a range of material thicknesses Fixed toggle clamp with position adjustments Hardened steel drill guides for maximum precision Use as a portable unit or mount to bench Anodized aluminum jig body. Shipping Weight 4. Warranty Warranty We guarantee this product to be free from defects in materials and workmanship 90 days from the date of purchase.
Limitations apply.


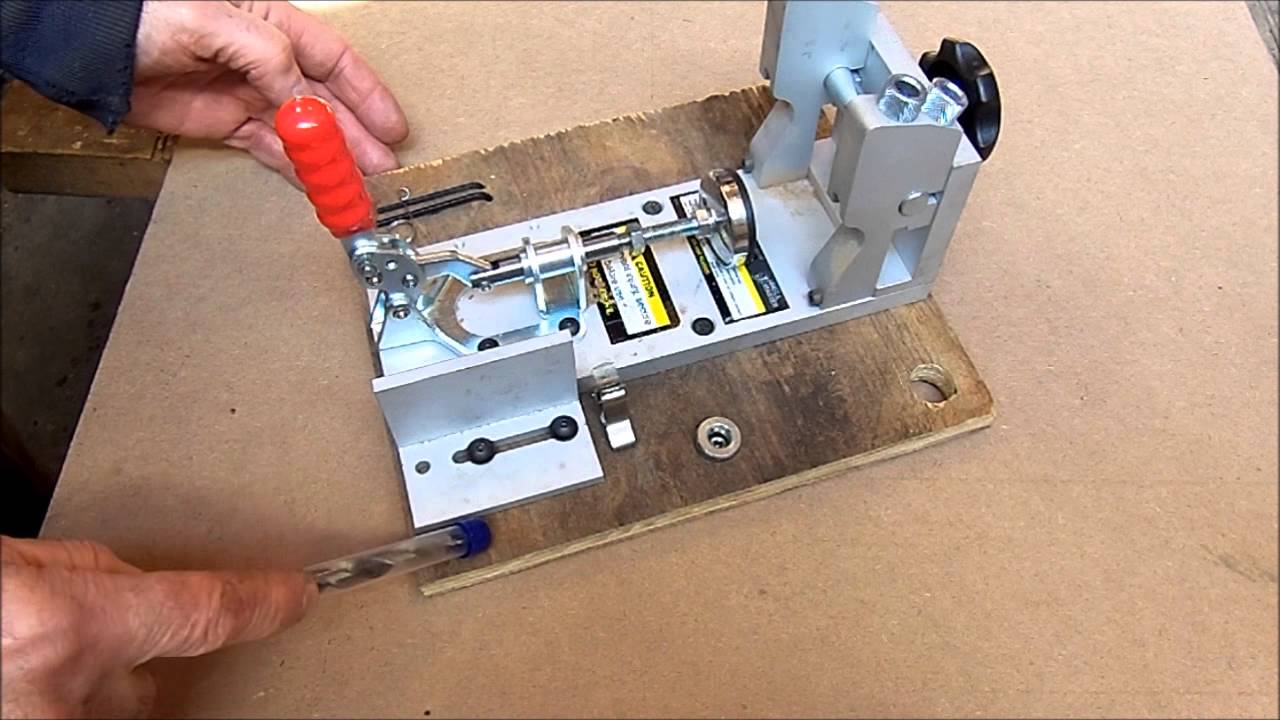
Wood Carving Starter Set 9002 Best Rap Editing Software Windows Tools Used In Woodwork Queen |
EKULYA
10.08.2020 at 17:45:52
aci_hayat
10.08.2020 at 19:23:39
S_k_E_l_i_T_o_N
10.08.2020 at 15:33:34
8
10.08.2020 at 19:47:20
Seytan_666
10.08.2020 at 15:59:52