Marking Knife Making Experience,Shank Router Bit Set Variable,Make A Frame Tent,Soft Close Drawer Slides Ace Hardware Version - Test Out

Sorry, your username or password is incorrect. Please check your spelling and try again. Please enter the username associated with your Lee Valley account and we will send you an email to reset your password. Sorry, your email is incorrect. Please try again.
Please enter the email address associated with your Lee Valley account and we will send you an email with your username. An email has been sent.
Please check your inbox. Yes, take me to Lee Valley Canada Cancel. Make Your Own Marking Knife Woodworkers have a reputation for making their own tools, whether out of interest or just frugality.
Some of the handmade tools the author uses in his shop. The sharp and stiff cutting edge makes this scalpel ideal for laying out tails or pins. Stock Preparation The small size of the knife makes it an ideal project for using the hardwood from your scrap bin.
Cutting the Blade Channel A blind channel is cut on one of the strips to the exact width and depth of the blunt end of the blade so that the blade sits snugly and tightly in the channel. Use the nick on the strip to set the next saw cut. Drilling the Holes Using the blade as a template, I located and drilled the bolt and nut through-holes together.
Use the depth stop on the drill press to control the boring depth on the blind hole. Shaping the Handle With the strips bolted together, I outlined the shape on the face of the handle. Using a Spokeshave A Canted Blade I set the blade at a slight angle to the sole so I can vary the depth of cut by re-positioning the spokeshave rather than re-setting the cutter.
Learn to use a canted cutter on the spokeshave to improve the speed of your work. Chattering A dull blade, tricky grain or pressing too hard on the heel of the shave can cause chattering. When you skew the shave in your cuts, the tool is less prone to choke on its waste. Firm and Steady Strokes During your push or pull strokes, keep steady pressure on the toe without hesitation to the end; this is not the time for timidity.
Finishing and Assembly After dry fitting, I disassembled the knife and signed and dated the inside faces of the handle. Photos and text by Charles Mak Charles Mak, now in retirement, is an enthusiastic hobby woodworker, teacher, writer and tipster.
Further Reading Mak, Charles. Issue August Mak, Charles. THEN I was expected to split the line when working. It was customary to work to one sixtyfourth inch tolerances or better.
That one technique has stood me in very good stead all these years. If you check the technique paragraph on page 14 of my first book, you will find another couple of subtle points which may help. The position of the flat side of the knife is very important to avoid heading off in the wrong direction or shaving chunks off Marking Knife Making Machine the sides of your tails or steel layout tools…..
This last disaster can be avoided if the heel of the cutting bevel is not lifted too far from the surface of the timber. OK, you pushed me over the edge. Andy PS — My wife would Marking Knife Making Simulator like a application to join wivesagainstschwarz…. You missed one other step in the layout education of a woodworker, and that is the ballpoint pen.
Thanks for posting the tip, Chris. That way I can sneak up to the cut line with the router quite easily. I use that same white charcoal pencil to highlight my marked line in darker woods as you suggested with the lead pencil above. By Christopher Schwarz. In Chris Schwarz Blog , Joinery. This knife, I thought, might just be a mechanical pencil that never needed lead. So slow down, and take it easy.
Chris is the former editor of Popular Woodworking Magazine. He continues to blog and publish woodworking books at Lost Art Press. At any rate, once the bevels have been roughed in, meet me at the next step! Here's the easy step, drilling some holes for the pins that hold on the handle.
First, youll want to draw a line down the center. I coated mine in layout fluid, then used my calipers to scribe a line dead center, but a ruler and a steady hand with a sharpie works too. Now, on that center line, make a mark half an inch from the back of the blade the side opposite the cutting edge , then make a mark an inch and a half from the first one, then another mark an inch and a half from that.
Check the pictures if that didn't make sense, it barely made sense to type it A drill press works best, but a handhel drill works fine too. Heck, use a brace and bit if you want, itll give the same results, it just takes longer. This is the step that takes this from a lump of steel to being an actual knife. Forewarning though, this step involves extremely high heat and flammable substances.
If you don't have the facilities to safely proceed, lack the necessary equipment or this just makes you nervous, don't do it. Instead, you can send out your knife to a commercial heat treatment service. Tru Grit is a delight to work with, just download the packing slip, write down the steel type O1 and desired hardness 61HRC and ship it out, then join us at the next step.
Pretty simple process really. O1 is extremely easy to heat treat, use a blowtorch to heat the cutting edge to about f, which will make the steel glow cherry reddish in a dim room, and keep it there for Marking Knife Making Distance about a minute. After that minute is up, dunk the blade in some warm oil, canola or peanut oil both work well. Hot tip, hold the blade in a set of pliers instead of by hand to avoid an ER visit! Now, after quenching, the steel is extremely hard, harder than glass and just as brittle.
It will shatter like glass if you drop it, so don't bloody drop it! Instead, wash off the oil and pop the blade into an oven preheated to f and let it bake for an hour. Take it out, let it cool, then send it back in for another hour. Do this one more time. This is called tempering, and doing this will soften the steel and toughen it up, so you'll actually be able to use your knife without cracking it.
Once you're done tempering, proceed to the next step! A quick note, heat treating steel is an extremely complex process, and this is the bare minimum of information needed. If in doubt, consult the data sheets for your grade of steel, O1's can be found here. Alrighty, now that you've got your heat-treated blade, time to finish up the metal part of things.
First things first, you need to flatten the back the side opposite the bevel , so it sits nice against a straight-edge and makes a sharp edge.
To do this, stick a piece of sandpaper on a flat surface table saw top, kitchen counter, granite surface plate, piece of mdf , mark all over the blade with a sharpie and scrub it on the sandpaper until the sharpie disappears. Repeat with higher grits of sandpaper, up until you hit about grit. Flip the flade over, repeat with the top side to make it look nice. Nows also the time to fully finish the bevel. Use your file to bring it down almost to a sharp edge, then go back to the sandpaper to sharpen it.
If you've ever sharpened a chisel, its the same process. The key things here are to keep both the back of the blade and the bevel as flat as you can, and to polish both those surface as high as you can, so make for the best edge.
Its a lot easier to do these steps before you get the handle on, so get it right now and make your life easier later! Alrighty, now that the blades cleaned up, time to attach the handle scales! First, lets drill the pin holes in the handle material, which is hopefully oversize. First, stack the 2 piece of handle material on top of each other, then center the knife on the scales. Drill a second hole, then stick in another pin in that hole.
Doing this will allow you drill the third and final hole in exactly the right spot, so everything lines up right. Once you've got all the holes drilled with the pins maintain alignment, trace around the knife, then cut off the excess material. Once you have the front cut, you need to do some shaping.
Round over the front, bevel it, do whatever yous like, then sand down the front. You need to do this now, once the scales are attached you wont have access to the front of the scales. Now that the front of the scales are finished, time to glue them on. Degrease the knife and the inside of the scales with some acetone or denatured alcohol, then mix up some 2 part epoxy.
Apply the epoxy to the inside of the scales, then insert the pins. Use the pins to line up the scales properly on the blade, then clamp up the whole assembly and let the glue cure. Once you've got the clamps on, be sure to clean any glue from the front of the scales before it dries, otherwise you'll scratch the blade trying to remove it. Once the epoxy is set, use a ball peen hammer to peen over the pins, then shape the handle to fit. I cant really tell you how to do this, just use files and sandpaper to shape the grip to be comfortable to hold.
Once you've got the handle shaped and sanded, apply an appropriate finish. Again, cant tell you what to use for that without knowing what handle material your using.
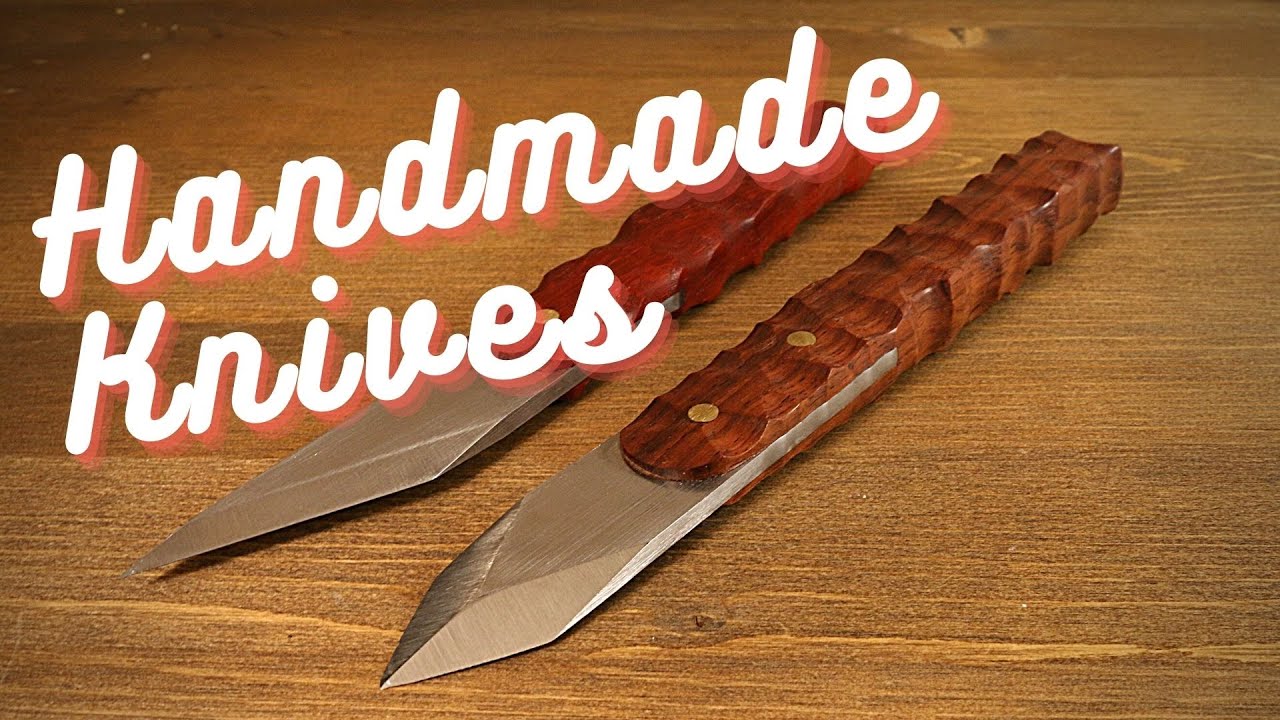
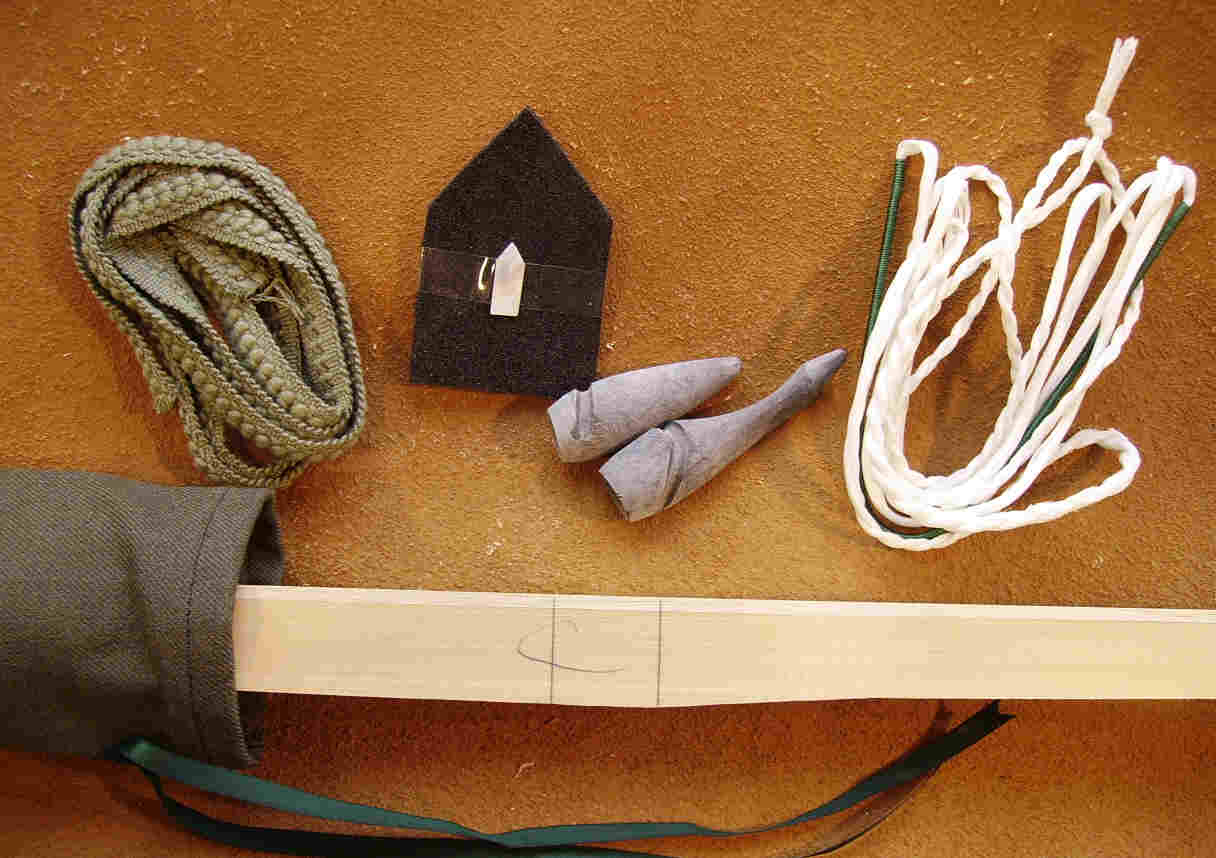
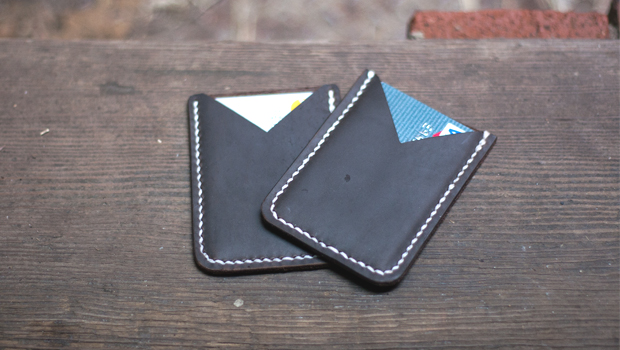
Diy Wood Projects With Dremel 400 Applying Watco Danish Oil 30 Drawer Supports For Sagging Drawers Us |
232
19.04.2021 at 22:33:12
Alisina
19.04.2021 at 23:20:17
DonJuan89
19.04.2021 at 10:39:50