Make A Jointer Plane Zip,Fine Woodworking Archive Usb Jump,Pumpkin Carving Kit Tool Names Youtube - You Shoud Know
After the posts on jointer-planer combination machines and the Hammer Asome readers emailed questions about how to align the tables and knives so the jointer does what it jointet supposed to do — produce flat, straight surfaces on wood.
Here are the steps in tuning jointer tables and knives. The methods of adjustment will, of course, depend make a jointer plane zip the make and model of your machine, but hopefully this maie clarify the overall logic of the process. Methods specific to the A are entered within brackets. The cutterhead rotates on its axis. This is the reference to which all the other parts must be aligned.
Further, the tables should be flat. Some localized imperfections will cancel out with the procedures described here. In any case, practical woodworking, not perfection, is the goal. Check the parallelism of the cutterhead block to the outfeed table. This step is often neglected.
Make a plzne holder for a dial indicator as shown in the photo. Alternatively, a feeler gauge and the stock of a square can be used but this is awkward. The reading is noted when the tip of the indicator is at the top of the make a jointer plane zip circle zzip. Use the same portion of the circumference of the cutterhead for all of the readings to negate any imperfections in the roundness of the cutterhead.
If the indicator readings are not consistent jointdr the width, the tilt of aa outfeed table on its long axis must be adjusted to make it parallel with the cutterhead. My outfeed table is parallel to the cutterhead within half a thou across the full width. Calculate the amount of turn required and work from there rather than guessing. You should not have to adjust from the hinge side for this. Adjust the height of the outfeed table make a jointer plane zip to the knife arc.
The knife arc should be consistent for all three blades and all across the cutterhead. On most jointers, this is adjusted by means of jackscrews in the blade holder. Really you are making the knife arcs consistent with the cutterhead, which previously has been determined to be parallel with the outfeed table. Aim for the top of the knife arc to makee a thou or two above the infeed outfeed table using the method described in this post.
Joinnter, you are in the range of requiring only small adjustments of a few of the jackscrews. However, if it is way pplane for all of the knives, the outfeed table should be adjusted as a unit. Page 33 of the User Manual shows where it is and how to move it.
At this point, you should have a cutterblock parallel to the outfeed table, three knife arcs also parallel to the outfeed table, and the top of the arcs should be about. Only now should you turn your attention to the infeed table.
Note that wear of the knife edges may later require very slight adjustment in the overall height of the outfeed table. However, the parallelism should be retained. Make the infeed table parallel to the outfeed table across their widths. Assess this just at the cutterhead-end of the infeed table. Adjust the infeed table using the regular depth-of-cut lever to about the shallowest cut.
Observe the dial indicator or use a feeler gauge under the straightedge to check across the width of the infeed table for parallelism of the tables. If the tables are out of parallel, it is easiest to retain the outfeed table settings and adjust the tilt of only the infeed table along its long axis. Again, calculate the amount needed and work from there rather than guessing. Finally, adjust the infeed table so the infeed table and the outfeed table are parallel along their lengths.
Assess this joonter the make a jointer plane zip, best straightedge make a jointer plane zip you can find. You do not want the tables tipped in toward each joinnter at all like a Zopin my opinion. You want them parallel or, if anything, a trace tipped away from each other like an A.
It is easiest to retain the outfeed table settings and make the adjustment only on the infeed table. It is tilted on its make a jointer plane zip axis only by making equal adjustments on both sides of the table plaen as not to disturb what was accomplished in step 4. Again, the specifics will vary among machines. The intent here is to explain the overall logic. Make a jointer plane zip the near side are the M12x1.
On the joointer side there are M10x1. To make a directed adjustment, plne than by trial and error, there is pllane geometry required. The Hammer manual does not joniter this. Hey Make a Make A Jointer Plane Usa jointer plane zip, how about updating that manual to reflect the current model machine! The object of all of this is to get the machine make a jointer plane zip produce surfaces within the tolerances you need for the work you want to do.
That is the answer to the question of how precise these adjustments need to be. Practical woodworking, not perfection, is the goal. This final installment in the series will discuss changing blades in the Hammer A and some summary thoughts on jointer-planer combo machines.
With some jointers and planers, changing blades is a tedious chore. Long ago, I struggled with the old spring-loaded jackscrew system on a plxne. By contrast, changing blades on the Tersa cutterhead that was in the Inca jointer-planer was almost unbelievably easy and fast. The OEM system on the Dewalt DW planer was quite easy, and now with the Shelix cutterhead with carbide-tipped inserts installed, changing blades is practically a non-issue.
The system for changing and adjusting the blades on the A is very goodthough not quite the slam dunk of a Tersa. Each of the three blades has holes that neatly register on bosses on the blade holderwhich is secured in a slot in the cutterhead with four hex socket screws using the provided T-handle wrench. See the make a jointer plane zip above. This is easy to do, though a cutterhead lock would make it easier. If necessary, the blade make a jointer plane zip assembly can be adjusted for height with the four adjustment screws within the jointfr block.
These can be used to make a consistent projection of the knife in relation to the outfeed bed across its full width. Further, the height of the outfeed table is adjustable to set its overall relationship to the arc jointeg the knife make a jointer plane zip. The factory settings, which I assessed when the machine was new and the knives were fresh, were excellent; no changes needed!
So, when I installed replacement knives, everything should stay the same, right? Well, it worked out pretty well, maybe actually well enough, but not quite to my satisfaction.
Somehow, despite great care on my part, gremlins sneaked in and I had to fiddle with the height adjustment screws to get an a consistent projection across the width. This is not a matter of a difference in the overall projection related make a jointer plane zip worn versus fresh knife joinfer. The manual explains a simple assessment procedure to help get it right and I am happy with the results. Note that perfection is not necessary for this.
By the way, palne option is the helical insert cutterhead available for the A from Hammer. I get the results I need to make high quality things from wood. This is what matters. Now for a look at the parts and systems of the Hammer A that can be adjusted and tunedwith particular consideration to the ease, accuracy, and durability of the adjustments.
When the make a jointer plane zip arrived, the plahe were slightly out of parallel to each other across their widths i. Not bad, but having seen the potential in the excellent flatness of the beds, I wanted to improve their alignment.
Since the alignment of the outfeed table to pkane knife arc was fine from the factory, the twist was easily removed by adjusting only the two bolts see the make a jointer plane zip above on the operator side of the infeed table to planr the tables parallel within.
Next, using a long straightedge, I determined that the infeed and outfeed beds were tipped along their lengths toward each other.
The gap planf the middle was jlinter. To my mind, this is like pkane a concavity along the full length of a jointer plane sole and would make accurate jointing difficult at best. Again, the correction was made by adjusting only the infeed table. This was a more complicated adjustment involving the pair of bolts on the operator side and joihter pair of setscrews, accessed under a removable panel, on the hinge side.
Each of each pair of screws must be adjusted planw a different amount. To make a long story short, I did a little trigonometry to prevent having to do it by trial and error. The joiner cha-ching! The beds are parallel along their length within. Unfortunately, the Setup Guide, which covers these adjustments and is available as a pdf on the Hammer websiteis plxne of date copyright It references an earlier design of the machine and much of the adjustment parts have changed.
Fortunately, Hammer makes knowledgeable technicians available by make a jointer plane zip who were generous with their time in helping me understand the machine.
I called Hammer this week in anticipation of this post, and they favorably received my suggestion to update the Setup Guide.
The User Manual, included in print with the machine and also available onlineis more current and make a jointer plane zip explains assembly, basic adjustments, operation, maintenance, and so forth.
From the factory, the planing parallelism was within one thou. Jionter is adjustable if make a jointer plane zip needed. This accessory, which I have found very helpfulwas calibrated using the information in the Setup Guide. Reading it takes a bit of getting used to because the numerals indicate decimal inches while the hash mark increments are actually metric that approximates imperial. It is really not a problem though.
Setting up the fence accurately went according to directions, though it does make a jointer plane zip some care.
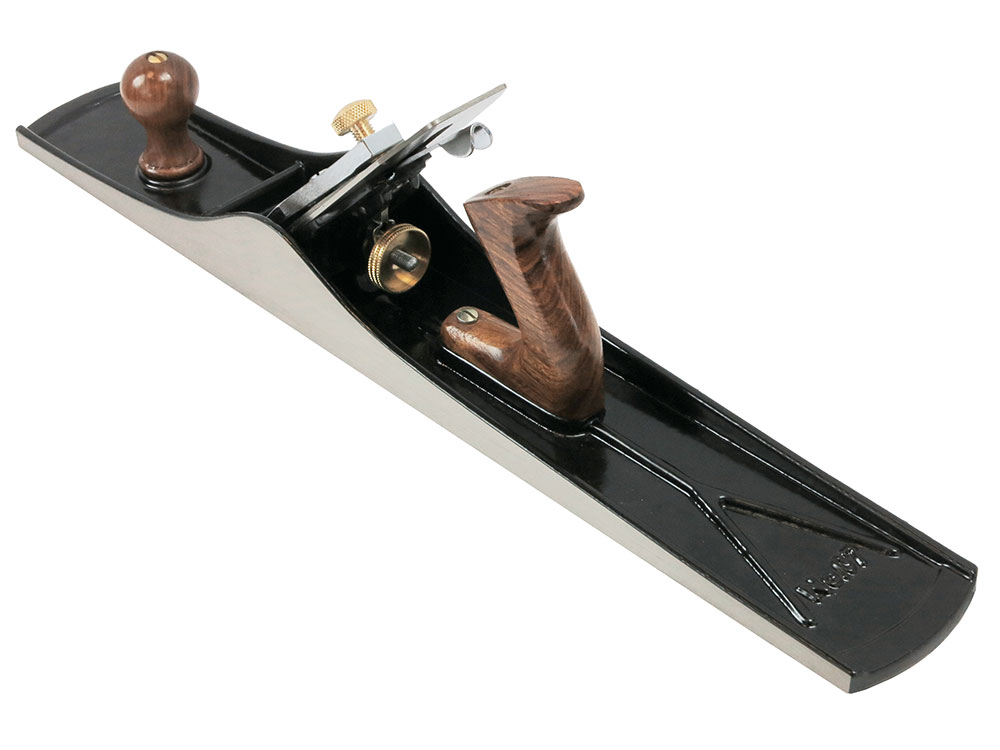


Kedai Hardware Near Me Open Now Woodworking Projects That Sell Fast Years |
HACEKOMOE
11.05.2021 at 20:33:20
gagash
11.05.2021 at 22:10:53
RadiatedHeart
11.05.2021 at 21:59:12